In the competitive oil and gas business, quality control in refractory installations is not an option; it is required. API 936 is a crucial certification that demonstrates a professional’s competence to properly manage and oversee refractory operations. With rising expectations for safety and efficiency.
The API 936 course provides a complete approach to learning refractory quality control requirements, giving professionals a competitive advantage in this specialized industry.
What Is API 936?
API 936 is developed by the American Petroleum Institute (API), is the industry standard for quality control of refractory systems. Refractory materials are important in constructing long-lasting linings for equipment that operates at high temperatures, such as furnaces, reactors, and kilns.
These materials are critical to the stability and efficiency of operations in the oil, gas, petrochemical, and energy industries. The API 936 standard provides recommendations for installing, inspecting, and testing refractory linings, with a focus on material properties, installation procedures, and quality assurance techniques.
Adhering to these standards helps to reduce hazards like equipment failure and costly downtime, which can have an impact on both safety and profitability. Certified API 936 professionals have the knowledge to ensure that refractory installations satisfy the strict standards for optimal operational performance.
What Is API 936 Course?
PetroSync’s API 936 course is a training program designed specifically for professionals seeking certification in refractory quality control. It provides a thorough overview of the materials, procedures, and inspection protocols defined in the API 936 specification. The training is aimed for people who want to expand their knowledge of refractory installation and quality management.
Giving them the tools they need to ensure that installations fulfill safety and effectiveness standards. PetroSync’s API 936 training provides participants with a curriculum that covers all aspects of refractory quality control. The training covers everything from material selection and handling to hands-on inspection procedures, providing a balanced approach to academic knowledge and practical abilities.
How to Get API 936?
Obtaining API 936 certification requires multiple processes, beginning with achieving qualifying conditions. Candidates are normally expected to have prior expertise in refractory installations, quality control, or a related subject. This experience helps students grasp the course content and prepares them for the certification exam.
The next step is to enroll in an approved API 936 training course. The training covers all exam topics, including refractory materials, installation techniques, and quality control protocols. Training normally consists of lectures, hands-on workshops, and practice examinations, all geared to provide applicants with the information and abilities required to pass the API 936 exam.
Following completion of the course, students must register for and pass the certification exam at an authorized testing facility.
What Is API 936 Course Objective?
Upon the successful completion of this course, each participant will be able to:
- Design, apply, install and inspect refractory materials in a professional manner
- Describe the refractory types and classification, test procedures, effects of additives and explain why chemistry alone is not a critical factor
- Emphasize the refractory phase relationships and fracture mechanics
- Inspect and quality control the refractory that includes acceptance/rejection criteria, sampling and testing as well as material and installer certification
- Discuss monolithic refractories including castable and plastic refractories, compositions and properties, anchorage, design and installation and the effects of firing on strength and thermal properties
- Employ the refractory installation techniques including modern refractory state of the art, precast modules, storage & handling, failure analyses, etc.
- Carryout refractory repairs and design various refractory linings
- Employ and apply the refractory selection guidelines from data sheet interpretation and product choice for designed exposure
- Determine and practice the refinery application of refractories including FFCU applications, effects of coking, reformers, transfer lines, Sulphur plants as well as the stacks, creep tests and hot spot detection
What Is API 936 Course Outlines?
Day 1
- Registration and Coffee
- Welcome and Introduction
- Pre – Test
- Introduction of Refractories:
– Types and Classifications
– Test Procedures
– Effects of Additives
– Why Chemistry alone is not a Critical Factor
– Phase Relationships
– Fracture Mechanics - Refractory Inspection and Quality Control:
– Acceptance / Rejection Criteria
– Sampling and Testing
– Records and Reports
– Refractory Quality Control
– Material and Installer
– Certification - Case Study:
- Brick Failure
- Cracking in Monolithic Lining
Day 2
- Monolithics:
– Casable and Plastic Refractories
– Compositions and Properties
– Anchorage
– Design and Installation
– Effects of Firing on Strength and Thermal Properties - Case Study:
- SRU Brick Lining
- Acid Gas Incinerator Refractory Damage
Day 3
- Refractory Installation Techniques:
– Modern Refractory State-of-the-Art
– Self-Flow, Vibe/Pump Cast, Gunite/Shotcrete,
– Rammed Plastics
– Precast Modules
– Storage & Handling
– Joints
– Maintenance Practice - Refractory Repairs:
– Failure Analyses
– Structural (Anchors, Erosion)
– Chemical (Proces Reactions, Slag Attack)
– Thermal (Impingement, Spalling, Fusion) - Case Study:
- Study Exposure to Thermal Cycle in FCCU
- Fibber Modules fallen from the Roof
Day 4
- Furnace Linings:
– Design of Various Refractory Lining Types
– Thermal Curing and Drying
– Explosive Spalling
– Effects of Aggressive Atmospheres - Refractory Selection Guidelines:
– Data Sheet Interpretation
– Product Choices for Design Exposures
– Castable, Plastic, Fiber and Brick Selection-
– Criteria for FCB and MSW
– Boilers, Incinerators, Gasifiers and Heaters - Case Study:
- Failing Brick Walls Deformations or Collapse Castable Cracking
Day 5
- Refinery Application Refractories:
– FCCU Applications
– Effects of Coking
– Reformers
– Transfer Lines
– Sulfur Plants
– Stacks
– Creep Tests
– Hot Spot Detection - Case Study:
- Flare Brick Failure
- Regeneration Heater H 1301 Accident Result
- Course Conclusion
- POST-TEST
Who Should Attend API 936 Course?
This course provide an overview of all significant aspect and considerations of refractory for those who are responsible for refractory design, application, installation, and inspection.
Master API 936 Certification With PetroSync’s Expert Training
Achieving API 936 certification can be a career-defining milestone, especially in the oil and gas sector. PetroSync’s training programs are designed to offer a blend of theoretical knowledge and hands-on experience, preparing you thoroughly for the API 936 exam. Join PetroSync today and gain the skills and credentials you need to stand out as an expert in refractory quality control.
Take the first step towards mastering the essentials of refractory installation and ensuring operational safety with API 936 certification.
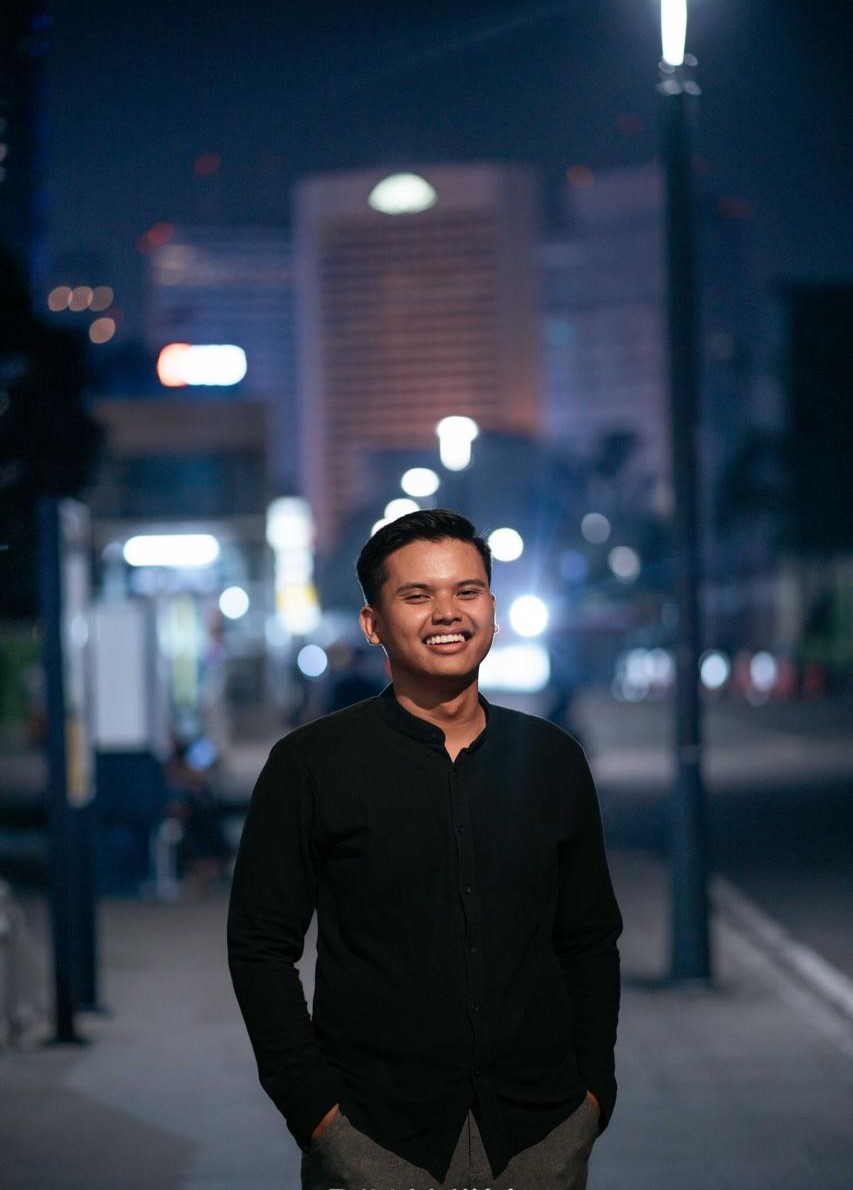
Results-oriented and thorough SEO specialist with extensive experience in conducting keyword research, developing and implementing digital website promotion strategies and plans, managing campaigns to develop company websites in the digital world, excellent knowledge of marketing techniques and principles, and attentive strong attention to detail.