In the realm of monolithic refractories, extreme heat and harsh conditions are everyday challenges. In this detailed guide, we will delve into the fascinating world of monolithic refractories, providing a clear understanding of their types, applications, and the numerous advantages they offer.
What Is Monolithic Refractory?
Monolithic refractory products are significant in various industries and processes due to their flexibility and special characteristics. In essence, they are refractory materials that can be molded into any needed shape, providing several benefits over conventional choices.
The word “monolithic” comes from “monolith,” which means a large stone. These materials are mixed into a kind of mixture that eventually solidifies into a hard, compact mass. Because of its versatility, the proportion of monolithic refractories within the refractories industry has grown in the past two decades and is expected to keep increasing. Economic factors and the presence of skilled individuals in the industry primarily drive this shift.
What Are The Types of Monolithic Refractories?
1. Castables
Castables are a type of monolithic refractory material that is highly versatile. They resemble a thick, heat-resistant paste. What makes castables unique is their ability to be molded into various forms to suit specific requirements. This adaptability is especially valuable in industries where they are used to line structures such as furnaces or kilns.
Castables can be shaped like clay to precisely match the needed structure. Once they dry and harden, they become incredibly sturdy and can endure high temperatures. In essence, castables are like the versatile chameleons of the refractory world, capable of taking on different shapes and fulfilling various purposes.
2. Plastic Refractories
Plastic refractories are a type of monolithic refractory material known for their malleability. These materials have a soft, clay-like texture. They are used in situations where existing refractory linings need repair or patching. Think of them as the “fix-it” materials for high-temperature environments.
Plastic refractories are easy to work with, just like modeling clay, making them ideal for quickly repairing or maintaining refractory linings. Once they are applied and dried, they become solid and provide heat resistance, ensuring the structure’s integrity in demanding conditions. In a way, they are like the handy repair tools in the world of refractories, ensuring everything stays in good shape.
3. Ramming Mixes
Ramming Mixes are a type of monolithic refractory material with a dense and sturdy texture. They are used in situations where it’s crucial to create solid and durable linings for high-temperature environments. The name “ramming” comes from the method used to install these mixes. They are packed or “rammed” into place to form a hard and compact lining.
When it comes to ramming mixes, you can think of it like building a strong wall with bricks; the ramming process ensures that the mix becomes tightly packed, creating a robust barrier that can withstand the heat and abrasion typical of these environments. Ramming Mixes are like the builders of heat-resistant fortresses, creating strong defenses against extreme conditions.
4. Gunning Mixes
Gunning Mixes are a type of monolithic refractory material with a unique application method. These mixes are designed to be sprayed or “gunned” onto surfaces. They are typically used to repair or maintain refractory linings, especially in areas that are difficult to reach.
The “gunning” process involves using specialized equipment to spray the mix onto the surface, much like painting a wall. This makes it ideal for patching up and keeping refractory linings in good condition, even in tight or challenging spots. Once applied and allowed to dry, Gunning Mixes become strong and heat-resistant, ensuring the continued integrity of the lining.
In essence, Gunning Mixes are like skilled craftsmen who can reach and repair the most inaccessible areas in the world of refractories, keeping everything in top shape.
5. Special Refractories
Special Refractories are a distinct type of monolithic refractory material. These refractories are tailored to withstand very specific and challenging conditions, like extremely high temperatures or harsh chemical environments. They are like the problem-solvers of the refractory world.
In many industries, the usual refractory materials might not be able to handle the extreme conditions, and that’s where Special Refractories come in. They are specially designed to cope with these tough situations.
Think of them as the “special forces” in the world of refractories – they are equipped to tackle the most demanding and unique challenges that standard refractories can not handle.
6. Coating Refractories
Coating refractories are a type of monolithic refractory material that serves a unique purpose. Instead of being a solid, shaped material like bricks, they are more like a paint or a layer that’s applied to the surface of other refractory materials.
These coatings act as protective shields. They are used to cover the surface of refractory linings, adding an extra layer of heat resistance and protection. Think of it like applying sunscreen to shield your skin from the sun’s rays.
Coating refractories are like the protective armor for other refractory materials, enhancing their ability to withstand high temperatures and harsh conditions, making them last longer and perform better.
Where Are Monolithic Refractories Used?
Monolithic refractories are versatile and widely used in industries to support their manufacturing process.
1. Steel Industry
Refractories in the steel industry are special materials used to line the inside of equipment like furnaces and ladles that are exposed to extremely high temperatures. These materials act as a protective shield, ensuring that the intense heat involved in making steel doesn’t damage or melt the equipment. In other words, they play a crucial role in preserving the integrity of the equipment and, by extension, the steel-making process.
2. Cement Production
In cement production, refractories are essential materials used to line the inside of rotary kilns. These kilns are like giant ovens that heat raw materials to create cement. The refractories protect the kiln’s inner walls from the extremely high temperatures.
Think of refractories as the sturdy armor that prevents the kiln from getting damaged by the intense heat. This protection ensures that the cement production process runs smoothly and that the kiln can withstand the demanding job of turning raw materials into cement.
3. Petrochemical Plants
In petrochemical plants, refractories are specialized materials used to line high-temperature equipment like cracking furnaces and reactors. These materials are like the protective shell that these equipment need to endure the extreme heat and harsh chemical substances they encounter during the petrochemical processes.
Refractories play a crucial role in maintaining the integrity and safety of these equipment, ensuring they can withstand the demanding conditions of the petrochemical industry. They are the heat-resistant guardians of the petrochemical plants, safeguarding the essential equipment and ensuring the smooth operation of the processes.
4. Foundries
In foundries, refractories are special materials used to line the furnaces where metals are melted and cast. These materials act like a shield, protecting the furnaces from the incredibly high temperatures and the wear and tear caused by the metal-making process.
Think of refractories as the sturdy armor that keeps the furnaces from getting damaged by the intense heat and the molten metal. They ensure that the foundries can operate efficiently, melting and shaping metals for various purposes, from car parts to machinery. So, they are like the protectors of the foundry, making sure everything stays in working order.
5. Glass Manufacturing
In the glass manufacturing industry, refractories are special materials used to line the equipment, such as melting tanks and high-temperature ovens, where raw materials are turned into glass. These materials act as a shield, safeguarding the equipment from the extremely high temperatures involved in making glass.
Think of refractories as the protective layer that ensures the equipment doesn’t get damaged by the intense heat. They play a vital role in keeping the glass manufacturing process running smoothly, helping to create all sorts of glass products we use every day, from windows to glassware. In essence, they’re the guardians of glass manufacturing, ensuring the equipment’s durability and performance.
What Are The Properties of Monolithic Refractories?
Monolithic refractories have specific qualities that make them excellent for various industrial uses. These qualities include:
- Chemical Inertness: They don’t react with corrosive or reactive substances.
- High-Temperature Resistance: They can handle temperatures as high as 1800°C (3272°F).
- Thermal Shock Resistance: Sudden temperature changes won’t harm these materials.
These characteristics make monolithic refractories highly durable and dependable, especially in demanding environments with high heat or harsh chemicals. They can withstand wear and tear, resist corrosion when exposed to chemicals, and perform well under different pressures and vacuums.
What Are The Advantages of Monolithic Refractories?
Since monolithic refractories are efficient and cost-effective solutions, many organizations use monolithic refractories due to their numerous advantages.
1. Reduced Downtime
Monolithic refractories are known for their ease of installation and maintenance, which leads to reduced downtime in industrial operations. Quick repairs and replacements mean less disruption to production.
2. Enhanced Energy Efficiency
Monolithic refractories offer superior thermal insulation properties, leading to improved energy efficiency in high-temperature processes. This translates to cost savings and reduced environmental impact.
3. Extended Service Life
Monolithic refractories exhibit exceptional durability, resulting in an extended service life for equipment and reduced replacement costs, a significant benefit in any industry.
4. Versatility
Their ability to be shaped to fit specific needs, whether for lining or repairing, makes monolithic refractories highly versatile, adapting to various industrial requirements.
What Are Some Frequently Asked Questions (FAQs) About Monolithic Refractories?
We summarize 6 frequently asked questions about monolithic refractories in the industry mentioned as follows.
1. What Are Monolithic Refractories?
Monolithic refractories are a type of heat-resistant material used in various industries. They come in different forms, such as castables, plastic refractories, and ramming mixes, each with specific applications.
2. Where Are Monolithic Refractories Commonly Used?
These refractories find extensive use in industries like steel, cement, petrochemicals, foundries, and glass manufacturing, where high temperatures and harsh conditions are prevalent.
3. What Advantages Do Monolithic Refractories Offer?
Monolithic refractories offer advantages such as reduced downtime, improved energy efficiency, and extended service life. Their versatility makes them adaptable to various industrial needs.
4. Are Monolithic Refractories Easy To Install?
Yes, monolithic refractories are known for their ease of installation and maintenance, making them a practical choice for industries.
5. How Do Monolithic Refractories Contribute to Energy Efficiency?
Their superior thermal insulation properties lead to enhanced energy efficiency, resulting in cost savings and reduced environmental impact.
6. Can Monolithic Refractories Withstand Extreme Temperatures?
Yes, these refractories are designed to withstand extreme heat and harsh chemical environments, making them ideal for high-temperature applications.
Monolithic refractories are the backbone of industries where heat and harsh conditions are a constant challenge. Their ability to withstand extreme temperatures, adapt to various needs, and offer significant advantages in terms of efficiency and cost savings makes them indispensable
If you’re looking to enhance your expertise in the realm of monolithic refractories and other crucial aspects of the industry, PetroSync offers specialized API 936 training programs designed to empower personnel like you with valuable knowledge and skills. These training sessions are crafted to ensure you stay at the forefront of industry practices and contribute effectively to your workplace’s success.
Credit header image: steemit.com
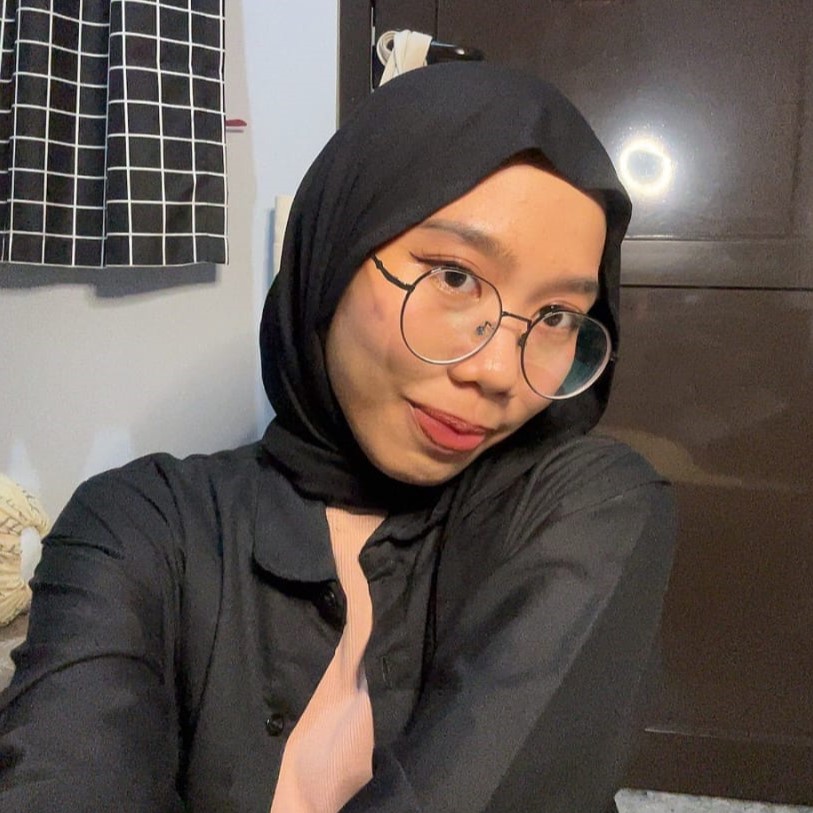
SEO specialist by day, fact-checker by night. An avid reader and content writer dedicated to delivering accurate and engaging articles through research and credible sources.