Industries that use heavy machinery and equipment often require post weld heat treatment (PWHT) to strengthen and improve the durability of welded components. In oil and gas where harsh environment is common, heat treatment can also enhance the corrosion resistance of weld joints. In this article, we will dig deeper into the fundamentals, some common PWHT techniques, disadvantages, and alternatives to heat treatment.
What Is Post-Weld Heat Treatment?
Post Weld Heat Treatment (PWHT) is a thermal process that is performed on welded materials after welding to reduce residual stresses and improve the welded joint’s mechanical properties. Residual stresses occur during welding due to heat input, leading to flaws such as distortion, cracking, and defects in the welded joint.
PWHT relieves these stresses and enhances the joint’s toughness, ductility, and strength. The process involves heating the welded material to specific temperatures for a defined period and controlled cooling.
PWHT parameters depend on the material, welding process, and desired joint properties. Industries such as oil and gas, petrochemical, and aerospace commonly use PWHT for welded joints exposed to high temperatures, pressure, and extreme conditions. Decisions to perform PWHT should be based on the specific application requirements since not all welded joints require PWHT.
What Is The Most Common Post Weld Heat Treatment?
Some of the most common post weld heat treatments are:
1.Post Heating
In post weld heat treatment (PWHT), post-heating involves heating the welded material to a specific temperature immediately after welding to prevent rapid cooling and avoid the formation of defects such as cracks or porosity.
The temperature and duration of post-heating depend on factors such as the material being welded, the welding process used, and the size of the joint.
2. Stress Relieving
In post weld heat treatment (PWHT), stress relieving is a process used to reduce residual stresses that may occur during welding, which can lead to defects in the welded joint.
During stress relieving, the material is heated to a specific temperature below its transformation temperature and held for a certain period of time to reduce these stresses and improve the mechanical properties of the joint.
What Are The Disadvantages of Post Weld Heat Treatment?
There are some of the disdavantegs of performing post weld heat treatment, such as:
1. Time and Cost
Performing PWHT on pressure equipment can be time-consuming and costly due to the need for specialized equipment and skilled personnel. The process can significantly increase the cost of equipment maintenance and repair, especially for large or complex pressure equipment.
2. Equipment Limitations
Certain types of pressure equipment may not be suitable for PWHT due to equipment limitations, such as size, geometry, or material type. In some cases, the treatment can cause cracking or other issues that make the process impractical or impossible.
3. Distortion and Warping
PWHT involves heating the welded joint to high temperatures and then cooling it down slowly. This can cause distortion and warping of the pressure equipment, which can compromise its dimensional accuracy and structural integrity.
4. Delayed Cracking
PWHT can delay the onset of cracking in welded joints, making it difficult to detect any issues during inspection. This can increase the risk of failures or leaks in the equipment, especially if the cracks are not detected promptly.
5. Environmental Concerns
The use of PWHT can consume significant amounts of energy, which can contribute to greenhouse gas emissions and other environmental concerns. Multiple PWHT cycles over the service life of the equipment can compound these environmental impacts.
Alternatives to Post weld Heat Treatment
Composite materials can provide an alternative to PWHT for the repair and reinforcement of pressure equipment. They can restore the equipment’s integrity by providing sufficient strength and stiffness. Unlike PWHT, which is a thermal process that can cause issues like warping and distortion, composite repairs can be designed and installed without the need for hot work or extensive welding.
What Are The Advantages of Using Composite Materials?
For the special case of pressure equipment like piping systems, composite repairs can also reinforce while improving their structural integrity and resistance to damage. This can extend their service life and reduce the risk of failures and leaks. The advantages of using composite materials for pressure vessels include:
1. High Strength-to-weight Ratio
Composite materials provide the necessary strength and stiffness without adding significant weight to the vessel.
2. Corrosion Resistance
Composite materials are highly resistant to corrosion, which can help extend the vessel’s service life and reduce maintenance costs.
3. Easy Installation
Composite repairs can be installed without the need for hot work or extensive welding, reducing downtime and minimizing risks.
4. Durability
Composite repairs can be designed to be highly durable, with long service life and resistance to damage, which can save time and money.
5. Versatility
Composite materials can be tailored to meet specific performance requirements, making them a versatile solution for a wide range of pressure vessel applications.
Heating the welded joint to high temperatures during PWHT can be risky for pressure vessel equipment since it can cause thermal distortion and weaken the strength and toughness of the metal. An improper implementation of the PWHT process can further result in defects like cracking or distortion, which can compromise the integrity of the pressure equipment.
Learning ASME PCC-2 for composite materials as an alternative to PWHT can be beneficial as it enables you to gain knowledge and understanding of the guidelines and standards for repairing and strengthening pressure equipment using composite materials. This helps you make informed decisions on when and how to use composite materials for pressure equipment repair to be in compliance with the required standards.
ASME PCC-2 has gained worldwide recognition for repairing pressure equipment and piping. Several large companies have incorporated these procedures in their company specifications.
PetroSync provides 3 days ASME PCC-2 Repair of Pressure Equipment training course covering ASME PCC-2 standards, the limitations, and advantages/disadvantages of all the procedures outlined. We believe that you can gain knowledge and understanding of the standard’s fundamental concepts, philosophy, and procedures for repairing pressure equipment and piping.
Our ASME PCC-2 course also offers comprehensive information on the advantages, limitations, and best practices for repairing and reinforcing pressure equipment, including alternatives to PWHT. Reserve your spot in ASME PCC-2 training and improve your understanding and proficiency in repairing pressure equipment with PetroSync!
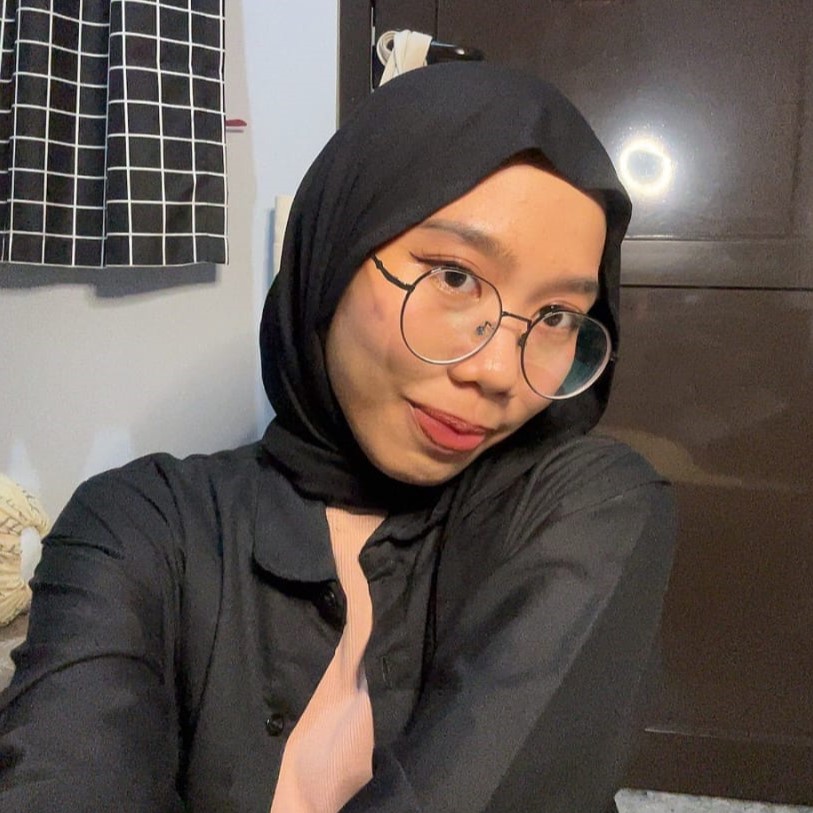
SEO specialist by day, fact-checker by night. An avid reader and content writer dedicated to delivering accurate and engaging articles through research and credible sources.