Discover the details of pressure vessel fabrication in this extensive guide. Delve into the complexities, advantages, and expert perspectives of the pressure vessel manufacturing world.
What Is A Pressure Vessel Fabrication?
Pressure vessel fabrication is a meticulous process encompassing precise cutting, molding, welding, and assembling of metals for creating vessels designed to contain gases or liquids at different pressures. In simpler terms, it involves the construction of specialized containers, ensuring they are built with accuracy to hold substances under varying pressure conditions safely.
What Is The Sequence of Fabrication of Pressure Vessels?
Pressure vessel fabrication is a meticulous process involving precise cutting, molding, welding, and assembling of metals to create containers for gases or liquids under different pressures. Before starting, crucial design steps are essential:
1. Design Concept
When concepting the pressure vessel design, engineers must clearly define the project scope and technical specifications. Specify the vessel’s shape, size, and dimensions. Fabricators choose materials based on the intended purpose. The pressuer
2. Stress & Strain Analysis
Perform mechanical calculations to determine the strength of the chosen materials for fabrication.
3. Fabrication Drawings
Create detailed drawings specifying material parts, manufacturing standards, viewing sections, and welding/bolting information. These drawings guide the flawless execution of the fabrication process.
The materials used in fabrication include plates, pipes, forgings, structural shapes, welding rods, or wire. These components are molded and forged according to vessel specifications, followed by machining if necessary. The welded parts are assembled, undergo cooling and sandblasting, and finally, primer and paint are applied.
What Are The Steps in The Manufacturing of Pressure Vessels?
1. Raw Material Preparation
Steps |
Checklist |
1.1 Material Selection | Choose appropriate materials based on requirements |
1.2 Material Inspection | Ensure materials meet quality standards |
1.3 Material Cutting | Cut materials into manageable pieces |
2. Scribing
Steps | Checklist |
2.1 Marking Guidelines | Mark guidelines for cutting |
2.2 Inspection of Marks | Ensure accurate markings for precision |
2.3 Verification | Double-check markings before cutting |
3. Blanking
Steps | Checklist |
3.1 Cutting According to Marks | Cut materials along marked guidelines |
3.2 Quality Inspection | Inspect cut pieces for accuracy and consistency |
3.3 Waste Management | Properly manage and dispose of excess material |
4. Bending
Steps | Checklist |
4.1 Shaping the Pieces | Bend materials into desired shapes |
4.2 Measurement Check | Ensure dimensions align with specifications |
4.3 Quality Assurance | Inspect bends for any deformities or flaws |
5. Forming
Steps | Checklist |
5.1 Giving Final Shape | Form the pieces into the intended structure |
5.2 Precision Check | Verify that the final form meets standards |
5.3 Consistency Inspection | Ensure uniformity across all components |
6. Edge Processing
Steps | Checklist |
6.1 Smoothing Edges | Refine edges for safety and aesthetic purposes |
6.2 Deburring | Remove any burrs or sharp edges |
6.3 Quality Check | Inspect edges to meet quality standards |
7. Assembly
Steps | Checklist |
7.1 Fitting Components Together | Assemble various parts into the vessel |
7.2 Alignment Check | Ensure proper alignment of assembled parts |
7.3 Pre-Welding Inspection | Inspect assembly before welding begins |
8. Welding
Steps | Checklist |
8.1 Secure Welding | Weld components securely according to standards |
8.2 Inspection During Welding | Monitor welding process for any irregularities |
8.3 Post-Welding Inspection | Inspect welded joints for quality and strength |
9. Inspection
Steps | Checklist |
9.1 Visual Inspection | Visually inspect the entire vessel for any issues |
9.2 Non-Destructive Testing | Conduct tests without affecting the vessel’s integrity |
9.3 Dimensional Inspection | Verify vessel dimensions meet specifications |
10. Additional Steps (if required)
Steps | Checklist |
10.1 Testing | Perform necessary tests for pressure and integrity |
10.2 Finishing Touches | Apply protective coatings or finishes as required |
10.3 Final Inspection | Conduct a thorough final inspection before delivery |
By following these detailed steps and checklists, the pressure vessel manufacturing process ensures precision, quality, and safety in producing these critical components.
Which Material Is Most Suitable for Fabrication of Pressure Vessels?
Creating pressure vessels involves choosing materials carefully to make sure they are safe, durable, and perform well in tough industrial conditions.
1. Stainless Steel
Stainless steel is a popular choice due to its excellent corrosion resistance and durability. It is particularly suitable for applications where exposure to harsh environments or corrosive substances is a concern. While it might be heavier compared to some alternatives, its robustness makes it ideal for industries such as chemical processing and pharmaceuticals.
2. Titanium
Titanium is known for its exceptional strength-to-weight ratio, making it a preferred choice for applications requiring lightweight yet durable vessels. It offers superb corrosion resistance, especially in environments with strong acids.
However, the cost of titanium can be higher than other materials, limiting its use to industries like aerospace and certain chemical processes where its unique properties are indispensable.
3. Aluminium
Aluminium is valued for its lightweight nature, making it suitable for applications where weight is a crucial factor. While it may not possess the same corrosion resistance as stainless steel or titanium, its affordability and malleability make it an excellent choice for certain low-pressure applications, like in the manufacturing of food and beverage containers.
4. Nickel Alloy
Nickel alloys provide a combination of high strength and excellent corrosion resistance, making them suitable for demanding environments. Industries such as petrochemicals and oil and gas often utilize nickel alloys in pressure vessels where resistance to extreme temperatures and corrosive substances is paramount. However, the cost of nickel alloys can be relatively high.
What Are Some FAQs About Pressure Vessel Fabrications?
Below are 6 of the most frequently asked question about pressure vessel fabrication:
1. What materials are commonly used in pressure vessel fabrications?
Pressure vessels often utilize high-strength alloys such as stainless steel and carbon steel to withstand extreme conditions.
2. How is the structural integrity of pressure vessels ensured?
Quality control measures, including non-destructive testing, are rigorously implemented to guarantee the structural soundness of pressure vessels.
3. Are there specific design considerations for pressure vessels in different industries?
Yes, each industry may have unique design requirements, and pressure vessels are engineered to meet these specific needs.
4. What challenges do welders face in pressure vessel fabrications?
Welders often encounter challenges related to material compatibility and achieving precise welds, which require skill and experience.
5. Can pressure vessel fabrications be customized for specialized applications?
Absolutely. The flexibility of design and material selection allows for the customization of pressure vessels to suit various industrial requirements.
6. How have technological advancements impacted the field of pressure vessel fabrications?
Technological innovations, such as automated welding processes and advanced materials, have significantly improved the efficiency and reliability of pressure vessel fabrications.
In summary, creating pressure vessel fabrications showcases human creativity and engineering skill. As industries progress, the techniques and technologies for making these essential components also advance. Whether overcoming challenges or adopting new ideas, the field of pressure vessel fabrications constantly explores the limits of what can be achieved.
PetroSync is dedicated to aiding you in comprehending pressure vessel intricacies through specialized courses like API 510, ASME B31.3, ASME Section VIII, and ASME Section I training.
We recognize the challenges in staying current with evolving regulations and technologies in the realm of pressure vessels. Our commitment to education promotes professional growth, offering valuable insights and hands-on experience.
In a complex industry, PetroSync’s ASME training can be your partner in enhancing your skills while contributing to overall industry progress.
credit header image: iStock
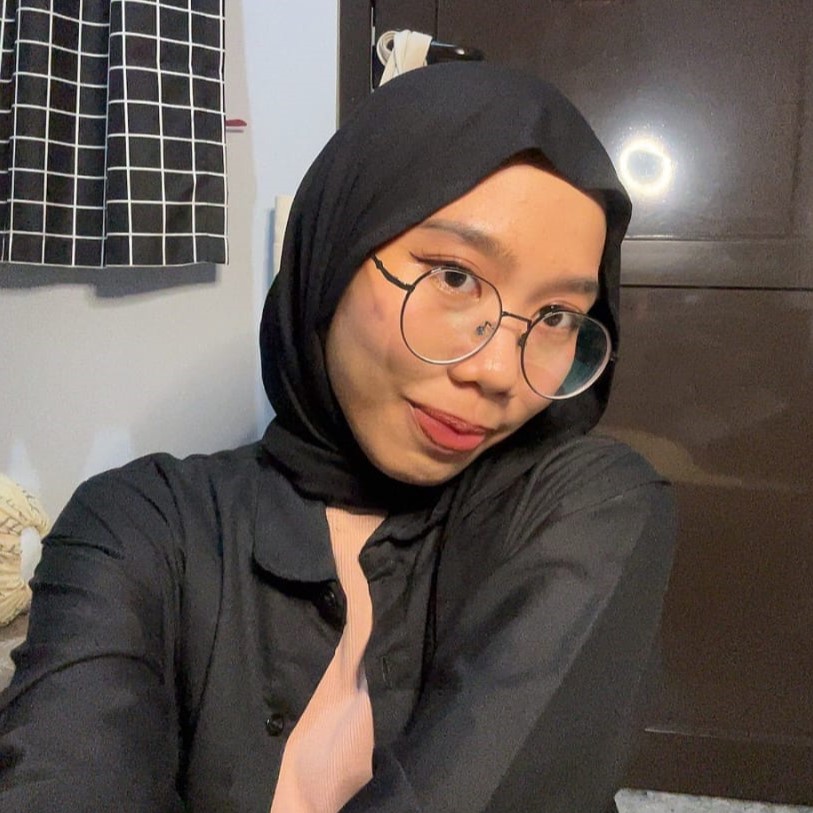
SEO specialist by day, fact-checker by night. An avid reader and content writer dedicated to delivering accurate and engaging articles through research and credible sources.