Discover the crucial aspects of shell and tube heat exchangers maintenance in this comprehensive guide. Delve into the essentials, from defining the structure of these heat exchangers to highlighting the importance of regular maintenance. Uncover common issues, visible signs, and proactive tasks to equip operators with actionable insights for optimal performance.
What Is Shell and Tube?
A shell and tube heat exchanger is a type of heat-exchanging device constructed using a large cylindrical enclosure, or shell, that has bundles of tubing compacted in its interior. This device facilitates the transfer of heat between two different fluids.
The shell contains numerous tubes, with one fluid flowing through them and the other flowing over the outside. The design enhances heat exchange efficiency, and baffles inside the shell increase turbulence, preventing stagnation and improving overall heat transfer rates. Shell and tube heat exchangers are widely utilized for both cooling and heating processes in various industrial applications.
What Is Shell and Tube Maintenance?
Shell and tube maintenance is the regular upkeep required for optimal performance of a shell and tube heat exchanger, which consists of a large outer shell with bundles of tubes. Key tasks include safe depressurization, cleaning headers and tube sheets, and clearing tube blockages. Visual inspections address potential leaks, and replacing worn gaskets is vital.
Verifying pressure gauges and thermometers ensures effective monitoring while cleaning strainers prevent efficiency-reducing clogs. Checking safety devices and routine cleaning of exterior surfaces maintain safe and efficient operation. Verifying a sump tank’s operation, if used, is crucial. Tightening mechanical connections is vital to avoid inefficiencies or failures.
When To Perform Shell and Tube Maintenance?
There are some conditions where performing shell and tube heat exchangers maintenance is necessary.
1. Visible Signs of Fouling
Fouling happens when unwanted deposits like scale, sediment, or biological growth build up on the heat exchanger surfaces. When you notice signs such as reduced efficiency, increased pressure drops, or weaker equipment performance, it means fouling might be occurring. If ignored, this can lower the efficiency of heat transfer, leading to more energy use and higher costs. Over time, it could cause permanent damage to the heat exchanger.
2. Tube Blockages and Reduced Efficiency
To keep a shell and tube heat exchanger working well, it’s important to regularly clean the tubes. How often you need to do this depends on the liquids involved. Maintenance becomes necessary when you see a clear drop in effectiveness, signaling potential tube blockages.
If you don’t deal with blockages, it could reduce how well heat transfers, putting a strain on the whole system. This may lead to more energy use, increased wear and tear, and could even shorten the life of the heat exchanger.
3. Presence of Slime or Algae Buildup
If you find slime or algae buildup, it’s time for maintenance. You can use high-pressure water for smaller deposits (called hydro blasting) and mechanical methods for larger sludge deposits. Ignoring this buildup could lead to clogged tubes, slowing down fluid flow and hindering heat transfer. This might cause overheating, reduce how well the system works, and could even lead to the equipment breaking down if you don’t fix it promptly.
4. Chemical Incompatibility or Stubborn Deposits
Maintenance is needed when using detergents or chemical cleaners to deal with stubborn deposits. It’s crucial to make sure these cleaning chemicals won’t damage the heat exchanger’s tubes. Ignoring this could result in corrosion or damage to the tubes, putting the heat exchanger’s integrity at risk. This might lead to leaks, reduced performance, and the need for expensive repairs or replacement.
5. After Visual Inspections and Cleaning
Checking the heat exchanger visually after cleaning is crucial to making sure it stays reliable. If you see signs of leaks, cracks, or corrosion during this check, it’s time for maintenance. Neglecting these checks might lead to unnoticed issues, causing leaks, fluid mix-ups, and even a potential breakdown. Dealing with problems as soon as you spot them is important to prevent more damage and keep the system working well.
6. Leak Repairs and Tube Damage
Fixing leaks quickly is important to stop fluids from mixing and to keep everything running smoothly. You might need to use methods like re-rolling, beading, welding, or temporarily plugging tubes for repairs. Ignoring leaks can lead to fluid mix-ups, affecting the quality of what the system produces or causing safety problems. Also, if you leave tube damage without fixing it, the problem might get worse, leading to more damage and higher repair costs.
7. Regular Maintenance Intervals
Setting a regular schedule for maintenance based on how the system works is key to preventing big problems and keeping things running smoothly. If maintenance happens irregularly or not often enough, there’s a risk of missing signs of fouling, blockages, or other issues. This could lead to unexpected downtime, higher costs for repairs, and a greater chance of the system breaking down. Regular maintenance is really important for making sure the system stays efficient and works well in the long run.
What Is The Checklist of Shell and Tube Maintenance?
Maintenance Task |
To Do |
Depressurize the unit | Before performing any maintenance, ensure the system is depressurized to guarantee the safety of personnel and prevent potential accidents during the maintenance process. |
Cleaning out the headers and scrape down tube sheets | Remove any debris or buildup in the headers and scrape down tube sheets to maintain optimal heat transfer efficiency. This helps prevent fouling and scaling issues. |
Clear tubes of any blockages | Ensure efficient operation by clearing tubes of blockages. Methods include using acids, high-pressure water, drill rods, scrapers, calcite cleaners, or scale remover. |
Visually check for leaks | Conduct a visual inspection to identify any leaks, cracks, or corrosion in the system. This step is crucial for maintaining the integrity and reliability of the heat exchanger. |
Replace gaskets | Replace worn or damaged gaskets to prevent fluid leakage and maintain the proper seal between the tubes and the shell. |
Verify pressure gauge and thermometer accuracy | Ensure the accuracy of pressure gauges and thermometers to obtain reliable readings, allowing for effective monitoring and control of the heat exchanger’s performance. |
Check and clean strainers if present | If strainers are present, check and clean them to prevent clogging. Clogged strainers can reduce flow rates and hinder the overall efficiency of the heat exchanger. |
Check operating safety devices | Verify the proper functioning of safety devices to ensure the heat exchanger operates within safe parameters. This includes pressure relief valves and temperature controls. |
Clean exterior surfaces as needed | Maintain the cleanliness of the exterior surfaces to prevent the accumulation of dirt and debris, which could impede heat dissipation and affect overall performance. |
Verify operation of Sump Tank | If a sump tank is part of the system, verify its operation to ensure proper drainage and collection of condensate or other fluids. |
Tighten all mechanical connections | Ensure all mechanical connections are tightened to recommended torques. Loose connections can lead to inefficiencies, leaks, or even equipment failure. |
This checklist outlines essential maintenance tasks for a shell and tube heat exchanger, covering safety precautions, cleanliness, and the inspection of critical components to ensure efficient and reliable operation.
Regular and smart maintenance of shell and tube heat exchangers is integral to ensuring your efficient and reliable operation. Ignoring the maintenance tasks could lead to decreased efficiency, increased energy consumption, and even permanent damage to the heat exchanger.
By adhering to a well-structured maintenance checklist, operators can enhance the longevity, safety, and effectiveness of shell and tube heat exchangers, ultimately contributing to the smooth operation of industrial processes.
Enhance your expertise in shell and tube heat exchangers training with Petrosync’s specialized training. Our courses, focusing on ASME and TEMA standards, provide practical insights for professionals in the oil and gas industry. Learn design principles, fabrication techniques, and effective maintenance strategies.
With hands-on experience and real-world applications, our training goes beyond theory. Invest in PetroSync‘s programs to align with industry standards, make informed decisions, and optimize the performance of these crucial components. Elevate your team’s capabilities and contribute to the success of your operations through our comprehensive and practical training of shell and tube heat exchangers.
Credit header image: iStock
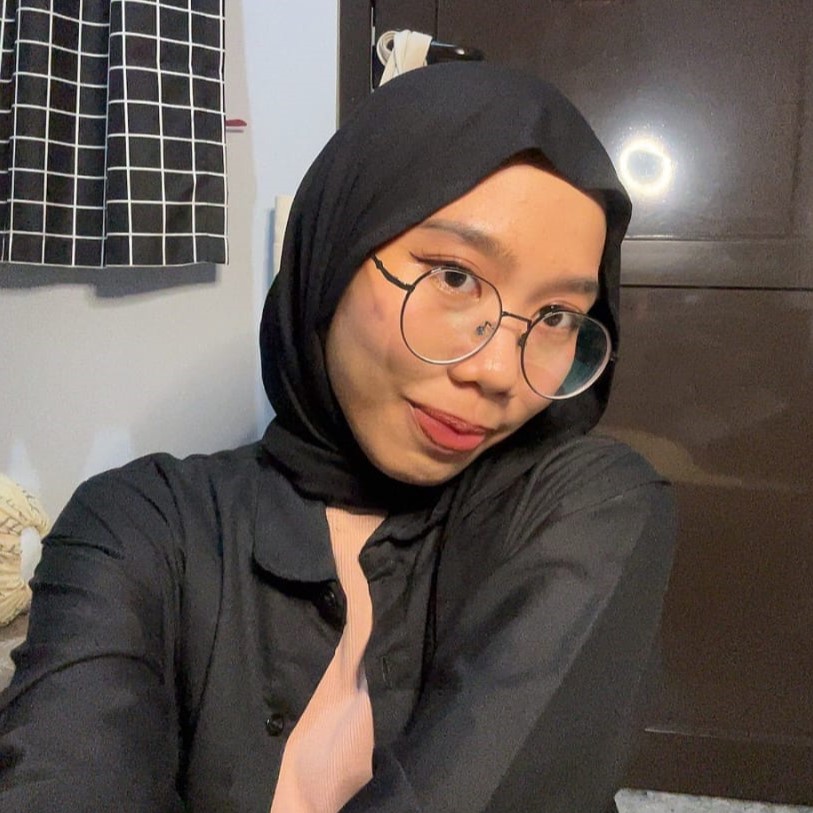
SEO specialist by day, fact-checker by night. An avid reader and content writer dedicated to delivering accurate and engaging articles through research and credible sources.