Trying to decide between vertical and horizontal pressure vessels? This detailed guide covers everything you need to know to make an informed choice. Selecting the correct pressure vessel is crucial for industries that work with fluids and gases. In this article, we will explore their differences, providing valuable insights to help you make the right decision.
What Is a Vertical Pressure Vessel?
Vertical pressure vessels are specially-made containers that hold gases or liquids at pressures different from the air around them. This type of vessel is the preferred choice when space on the floor is limited, and the vessel does not need to hold much material.
Vertical pressure vessels are commonly used in mixing tanks where the mixing action is important, and they often feature a high amount of gas compared to liquid. Due to its shape, vertical pressure vessels often have several layers or flat pieces inside. These are meant to make sure that gas or vapor moving upwards mixes properly with the liquid flowing down.
What Are The Advantages of Vertical Pressure Vessels?
1. Space Efficiency
Vertical pressure vessels save space because they stand upright. This is great when you don’t have a lot of room to spare in your facility.
2. Good for Mixing
They’re perfect for processes where you need to mix things like gases or vapors with liquids. The vertical design helps these elements blend effectively.
3. Natural Separation
In vertical vessels, gases rise upward and separate from the liquid. This is handy in many applications where you need these two components to stay apart.
4. Easy to Maintain
Maintaining vertical vessels is straightforward. You can easily access and service them due to their upright design, which is a plus for maintenance teams.
5. Variety of Uses
Vertical vessels are versatile. They find applications in many different industries and processes, making them a reliable choice for a wide range of needs.
What Is a Horizontal Pressure Vessel?
Horizontal pressure vessels are widely employed across various industries used for specific situations. They come in different sizes and serve multiple purposes. Typically, these vessels function as storage containers, separation tanks, or settling drums, where solid particles settle at the bottom of the liquid.
The horizontal vessel is the go-to choice for heat exchangers, where heat transfer between fluids is critical. Additionally, you will find it used in flash drums, which are crucial in separating components in a mixture. Settling drums, as mentioned earlier, where solid particles settle from liquids, also benefit from the horizontal orientation.
What Are The Advantages of Horizontal Pressure Vessels?
Horizontal pressure vessels lay on their sides and offer their unique benefits:
1. Even Stress Distribution
Horizontal pressure vessels, lying on their sides, have the advantage of distributing stress more evenly. This even stress distribution can increase the vessel’s lifespan, as it reduces the risk of wear and tear by spreading the load across a broader surface area, especially in their cylindrical shape, which minimizes areas of concentrated stress.
2. Accessibility
These vessels are a smart choice when you require easy access to tasks like loading and unloading materials or conducting maintenance. Their horizontal orientation makes it convenient to reach and work on various vessel parts, simplifying operational processes and reducing downtime.
3. Natural Drainage
Horizontal pressure vessels are efficient for drainage, allowing for the effective removal of liquids. This feature makes them particularly suitable for applications where complete drainage is necessary, ensuring that no residual liquid remains inside, contributing to process efficiency and cleanliness.
4. Versatility
Their horizontal layout also makes them versatile, and suitable for various industries and applications, where even stress distribution, accessibility, and natural drainage are valued. Whether for storage, separation, or drainage, these vessels offer flexibility, making them a valuable asset in different industrial settings.
Which One Is The Right Pressure Vessel: Vertical vs. Horizontal?
Your choice between vertical and horizontal pressure vessels depends on specific factors:
1. How much space do you have?
Your choice should primarily depend on the space you have. If your facility has limited floor space but more vertical room, consider vertical vessels. For instance, in a small chemical plant with a compact layout, vertical vessels can efficiently use the available height while taking up less floor space. In contrast, if you have ample ground space but lower ceiling clearance, horizontal vessels are the better choice.
2. Do you have specific operational needs?
Think about your day-to-day operations. If you need frequent access to the vessel for tasks like loading, unloading, or regular maintenance, opt for horizontal vessels. For example, in a food processing facility, horizontal vessels are often preferred for easy ingredient loading and cleaning.
3. What materials do you process?
The materials you handle matter. Some substances, like corrosive chemicals or abrasive materials, may have unique requirements. In such cases, the choice of vessel orientation might depend on the compatibility of materials and the vessel’s resistance to corrosion. Always consider material compatibility when deciding.
4. What are the safety regulations in your region?
Safety is paramount. Ensure that your chosen pressure vessel complies with industry-specific safety standards and regulations. For instance, in the petrochemical sector, vessels must adhere to stringent safety guidelines to prevent accidents and protect the environment.
5. How much budget do you allocate for each vessel?
Compare the total costs, including purchase, installation, and maintenance, for both vertical and horizontal vessels. Make a decision based on your budget and long-term expenses. For instance, while horizontal vessels might have higher installation costs due to the need for a larger foundation, they could be more cost-effective in the long run if they reduce maintenance and operational costs.
6. How is your company’s future projection?
Consider your future production needs. If you anticipate an increase in production, choose a vessel that can accommodate this growth. For example, in a brewery, where production volumes may expand over time, opting for vessels with larger capacity ensures that your equipment can meet future demand without costly replacements or additions.
Choosing the right pressure vessel is vital for the safety and efficiency of your industrial processes. Vertical and horizontal pressure vessels each have their strengths. Your decision should align with your specific needs, budget, and plans. Take the time to assess your situation, consult experts, and ensure your choice complies with safety and industry standards.
One excellent step towards ensuring the integrity of your pressure vessels is to consider taking the API 510 Pressure Vessel Inspection course offered by PetroSync. This comprehensive training program equips you with the knowledge and skills needed to excel in the inspection process of pressure vessels. Proper inspection is key to maintaining these vessels’ structural soundness and safety, safeguarding your operations, workforce, and environment.
By enrolling in the API 510 Pressure Vessel Inspection course, you’ll gain valuable insights into best practices, industry standards, and safety protocols. It’s an investment not only in your professional development but also in the overall reliability and security of your industrial processes.
Don’t leave the safety and efficiency of your operations to chance. Take control of your pressure vessel management and inspection with the right training and expertise. PetroSync’s API 510 course is your gateway to a more secure and successful industrial future.
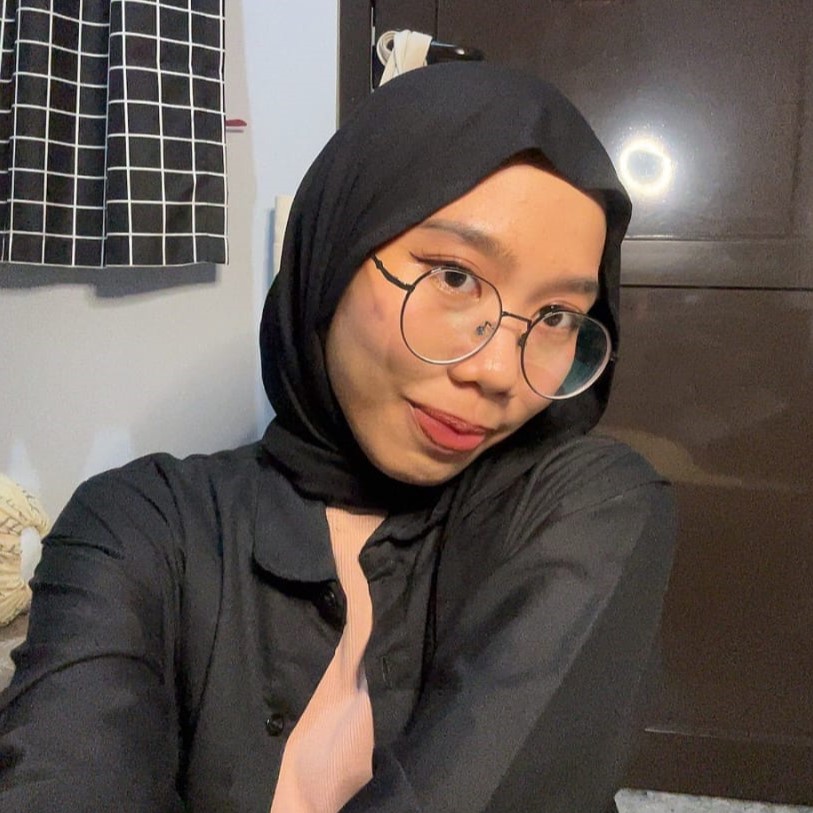
SEO specialist by day, fact-checker by night. An avid reader and content writer dedicated to delivering accurate and engaging articles through research and credible sources.