Are you in need of more information about power boilers? Let’s break down the critical parts of power boilers, which are essential for a solid and efficient system. Starting with the furnace and moving on to the steam drum, we’ll explore the fundamentals. Read on to learn about the components and some notable knowledge of power boilers.
What Is A Power Boiler?
A power boiler is a specialized equipment designed to generate steam by heating water. Its primary function is to convert water into steam, which can then be used for various purposes in industries and power plants.
The process begins by heating the water to produce steam under high pressure. This high-pressure steam is then utilized to turn turbines, generating mechanical energy that, in turn, produces electricity. In essence, a power boiler plays a crucial role in the production of steam, which becomes a valuable source of power for electricity generation and industrial processes.
It operates at pressures exceeding 15 psig for external use or at pressures over 160 psig and/or temperatures exceeding 250 degrees F for processes such as electricity generation, utilizing the direct application of energy from the combustion of fuels or electricity, solar, or nuclear energy.
What Is Combustion in Power Boilers?
In a power boiler, combustion is the ignition and burning of a fuel source. The burning fuel releases heat energy, which is harnessed to elevate the water temperature, transforming it into steam. This fundamental combustion process is vital for fueling boilers and effectively generating steam for diverse industrial and power plant uses.
What Is The Difference between Boilers and Power Boilers?
The primary difference between a boiler and a power boiler lies in their intended functions and capabilities. In essence, while both boiler and power boiler involve heating water to create steam, a power boiler is specialized for power generation, particularly in industrial and power plant settings.
It is commonly known that a boiler is a general term for a device that heats water to produce steam, which can be used for heating buildings, providing hot water, or generating power. While a power boiler specifically focuses on producing steam at high pressures and temperatures to generate electricity.
One significant application of a power boiler in a power plant is for converting thermal energy into electricity. It achieves this by burning a fuel source to produce high-temperature gases, generating heat energy. This heat is used to turn water into high-pressure steam.
The steam then powers a turbine connected to a generator, converting the mechanical energy into electricity. This process showcases the essential role of a power boiler in efficiently transforming fuel heat into electrical power within the power plant’s operations.
What Are The Types of Power Boilers?
Understanding the various types of power boilers is essential for individuals involved in the field of energy generation. Here are some key types of power boilers explained:
1. Fire-Tube Boilers
Fire-tube boilers are a common type of power boiler characterized by a cylindrical shell containing water, with hot gases passing through tubes immersed in the water. These boilers are known for their simplicity and easy maintenance.
The heat from fuel combustion is transferred through the tube walls to the water, generating steam. Fire-tube boilers find application in smaller industrial settings, heating buildings, and providing hot water for various purposes.
Water-Tube Boilers
In contrast to fire-tube boilers, water-tube boilers have water-filled tubes that carry heated gases. These boilers are often used in larger industrial and power plant settings, offering higher efficiency and the ability to handle higher pressures.
Water-tube boilers excel in applications requiring large steam outputs, making them prevalent in power generation facilities and industrial processes demanding substantial energy.
Electric Boilers
Electric boilers utilize electricity as the primary source of heat to generate steam. These boilers are characterized by simplicity, cleanliness, and precision in controlling the steam generation process. Electric boilers are commonly employed in diverse industries where electricity is readily available, offering an efficient and eco-friendly solution for steam production.
Circulating Fluidized Bed Boilers
Circulating Fluidized Bed (CFB) boilers feature a fluidized bed of material, usually sand, limestone, and ash, through which air is blown to facilitate combustion. CFB boilers are known for their fuel flexibility and the ability to capture pollutants during combustion. They find applications in power plants, particularly for burning low-grade fuels like coal and biomass, contributing to more sustainable and efficient energy production.
Once-Through Boilers
Once-through boilers, also known as monotube boilers, operate in a continuous flow, where water is fed in at one end and steam is extracted at the other. These boilers are characterized by rapid steam generation and response to changing loads.
Due to their efficiency and compact design, once-through boilers are often used in applications where quick steam production and precise control are crucial, such as in nuclear power plants and certain industrial processes.
What Are The Main Components of Power Boilers?
The three main components of a power boiler consist of a burner, combustion chamber, and heat exchanger.
1. Burner
The burner is a fundamental component of a power boiler responsible for initiating the combustion process. It introduces and mixes the fuel with air in precise proportions, creating an explosive mixture. This mixture is then ignited, producing a controlled flame that releases heat energy. The type and design of the burner significantly influence the efficiency and performance of the power boiler.
2. Combustion Chamber
The combustion chamber is the space within the power boiler where the actual combustion process takes place. It provides a controlled environment for the combustion of fuel, ensuring efficient and complete burning.
The design of the combustion chamber influences factors such as temperature, turbulence, and residence time, all crucial for optimal combustion. The combustion chamber plays a pivotal role in converting the chemical energy of the fuel into heat.
3. Heat Exchanger
The heat exchanger is a key component that transfers the heat generated during combustion to the water, producing steam. It consists of a network of tubes or passages through which hot gases from the combustion process flow. As these gases pass over the surface of the heat exchanger, heat is transferred to the water circulating the tubes, converting it into steam. The efficiency of the heat exchanger directly impacts the overall efficiency of the power boiler in harnessing thermal energy for various applications.
What Are The Other Components of Power Boilers?
Component |
Description |
Aquastats | Aquastats are devices that control the temperature of the water within the boiler, ensuring it stays within the desired range. |
Backflow Valve | A backflow valve prevents the reverse flow of water, maintaining the correct direction of water flow within the boiler system. |
Circulator Pumps | Circulator pumps facilitate the movement of water through the boiler and heating system, ensuring efficient heat distribution. |
Controls | Controls regulate various aspects of the boiler system, including temperature, pressure, and other critical operational parameters. |
Deaerators/Condensers | Deaerators remove dissolved gases from the water, preventing corrosion, while condensers enhance efficiency by recovering heat from exhaust gases. |
Economizer | An economizer preheats the water using waste heat from the flue gases, improving overall boiler efficiency. |
Exhaust Stack | The exhaust stack directs the flue gases produced during combustion safely out of the boiler system. |
Expansion Tank | An expansion tank accommodates the expansion and contraction of water within the boiler, preventing damage to the system. |
Supply Lines | Supply lines transport water into the boiler, providing a continuous flow for the heating process. |
Refractory | Refractory materials line the combustion chamber, protecting the boiler structure from extreme heat and ensuring durability. |
Return Lines | Return lines carry water back to the boiler after it has circulated through the heating system, completing the cycle. |
Superheater | The superheater further increases the temperature of steam generated, enhancing its energy-carrying capacity for specific applications. |
These components collectively contribute to the efficient and safe operation of a power boiler, ensuring the effective generation and distribution of steam for various industrial and heating applications.
In summary, it is crucial to excel in designing and inspecting power boilers, adhering to global standards like ASME Section I. Since power boilers play a vital role in various industries, proficiency in design and careful inspection is not just about operational efficiency—it is about ensuring safety and meeting regulations.
ASME Section I sets the international and widely accepted standard for building and inspecting power boilers, emphasizing precise design, top-notch materials, and rigorous testing. If you are an engineer or industry professional, a solid grasp of these standards is essential.
PetroSync, in the mission to empower you to contribute to the reliability, efficiency, and safety of power boilers, realizes the importance of this equipment as it becomes the backbone of many industrial processes. Join ASME Section I training by PetroSync and excel in power boiler design and inspection with us. Showcase your commitment to excellence, reliability, and the seamless integration of these critical components in industrial settings with PetroSync!
credit header image: iStock
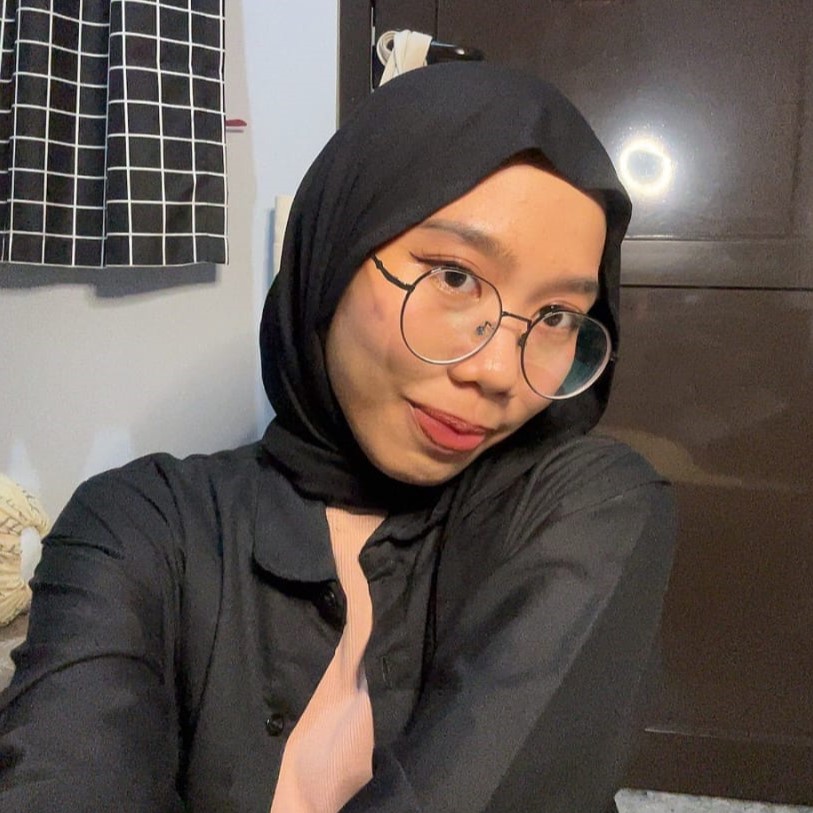
SEO specialist by day, fact-checker by night. An avid reader and content writer dedicated to delivering accurate and engaging articles through research and credible sources.