In the world of efficient asset management, understanding and using asset failure codes are essential. These codes provide a structured way of organizing and recording information about equipment issues. This article aims to clearly explain what asset failure codes are and guide readers on how to use them effectively in maintenance.
What Is Failure Codes?
Failure codes, a short sequence consisting of alphabetical, numeric, or alphanumeric characters that are used in maintenance and asset management, are systematic labels or identifiers used to categorize and describe the reasons behind equipment failures. These codes help organizations classify and understand the root causes of malfunctions, breakdowns, or inefficiencies in machinery or systems.
By assigning specific failure codes, businesses can establish a standardized way of recording and analyzing data related to equipment issues. This systematic approach aids in identifying recurring problems, implementing targeted solutions, and improving overall equipment reliability and performance. In essence, failure codes serve as a structured method for cataloging and comprehending the various factors contributing to equipment failures.
What Are Failure Codes Used in Asset Management?
Many experts recommend having 30 or fewer failure codes. This ensures a good variety without overwhelming technicians who deal with these codes daily. Since technicians are the ones interacting with these codes, minimizing confusion is crucial. When creating codes, consider the following:
- Organization: Arrange the codes in a structured manner.
- Logic: Ensure the codes make logical sense.
- Consistency: Maintain uniformity in code usage.
- Simplicity: Keep the codes straightforward and easy to understand.
Following these guidelines helps in creating an effective and user-friendly system for managing failure codes. However, here is a table with some common failure codes used in asset management along with their definitions
Code |
Definition |
Description |
AOL | Abnormal outlet low | Low output |
PLU | Plugged | Partial or full-flow restriction |
IHT | Insufficient heat transfer | Insufficient heating/cooling |
AIR | Abnormal instrument reading | False alarm or faulty reading |
SPS | Spurious stop | Unexpected shutdown |
REPAIR | Maintenance action to restore an item | Restore the item to the original state |
REPLACE | Replace the item with a new or refurbished item | Replace with a new or refurbished item |
MODIFY | Replace/renew/change an item | Change item type, make, design, or material |
SERVICE | Periodic servicing | Periodic maintenance with little dismantling |
TEST | Periodic test of function availability | Verify function availability |
CHECK | Investigate the issue | No action required or deferred action |
ADJUST | Bring out of tolerance condition | Adjust within tolerance |
ARLK | Air Leak | |
ALRM | Alarm or Problem Indicator | |
BRNG | Bearing Problem | |
CALB | Calibration Problem | |
DIRT | Dirt or Foreign Matter Problem | |
ADJS | Equipment Adjustment Required | |
CUTO | Equipment Cutting Out | |
JAMD | Equipment Jammed | |
HUNG | Equipment PC or Microprocessor Hung Up | |
XLUB | Excessive Lubrication | |
NOIS | Excessive Noise | |
VIBR | Excessive Vibration | |
LLUB | Lack of Lubrication | |
WIRE | Loose or Broken Connection or Wire | |
ALIN | Misalignment | |
NAIR | No Air | |
NPWR | No Power | |
OLLK | Oil Leak | |
OPER | Operator Error | |
XHOT | Overheating or Smoking | |
BROK | Part of Equipment Is Physically Broken | |
SHRT | Short Circuit | |
VNDL | Vandalism | |
WTLK | Water Leak | |
NOGO | Will Not Start |
These codes are commonly used to categorize and describe various issues encountered in asset management, providing a standardized way to record and communicate information about equipment failures and maintenance actions.
How To Implement Failure Codes?
Implementing failure codes involves selecting a method for code capture, often utilizing a Computerized Maintenance Management System (CMMS) for consistent and efficient data management. Read on to know the details on how to implement failure codes in your asset management activities.
1. Selecting the Method for Failure Code Recording
To implement failure codes, you can either handle it manually or, more commonly, use a Computerized Maintenance Management System (CMMS). CMMS allows for consistent data recording and easy retrieval. Most modern CMMS supports three or four-character codes, ensuring technicians cannot submit a defect report or complete a planned maintenance task without applying a relevant code.
2. Categorizing the Data
For effective failure coding, establish a comprehensive coding structure that aligns with your business needs. This structure should cover three main categories: Defects, Failures, and Interventions.
- Defects: Capture operational issues requiring maintenance intervention (leaks, noise, vibration, overheating, or unplanned stoppages).
- Failures: Identify the root cause of an issue once a technician investigates and resolves a task (failed bearing, worn seal, cooling fan failure, pump bypass).
- Interventions: Describe the maintenance technician’s action to resolve a defect (lubrication, repair, replacement, or overhaul).
These categories provide an instant overview of the problem, its cause, and the technician’s resolution. When aggregated, this data becomes a valuable resource for operational improvement.
3. Building a Code Library
Populate each category with specific codes related to your assets. Start with generic codes applicable to most equipment. Refer to the international standard ISO 14224 for examples. Pay attention to less obvious code groups such as calibration, electrical defects, human error, and normal wear and tear.
4. Employee Training in Code Application
Conduct training sessions to ensure employees understand why failure codes are implemented and the benefits they bring to both individuals and the business through a more efficient maintenance system. Make the code library easily accessible, especially on mobile devices technicians use. Mandate the use of codes for submitting work requests, closing work orders, or interacting with the store’s system. Using a CMMS ensures that entering failure codes is a mandatory step in the workflow.
What Are The Functions of Failure Codes?
The functions of failure codes encompass organizing data systematically, offering diagnostic insights into equipment issues, and facilitating reporting and analysis for proactive maintenance planning. Further, we explain the function in detail as follows.
1. Organized Data Capture
Failure codes help in systematically recording information about equipment issues, creating an organized database. This structured approach allows for efficient tracking and analysis.
2. Diagnostic Insights
By categorizing failures, these codes offer insights into the nature and causes of issues. This diagnostic information helps maintenance teams understand problems more quickly and accurately.
3. Reporting and Analysis
Failure codes facilitate the generation of detailed reports. Through analysis of these reports, organizations can identify patterns, trends, and recurring issues, enabling proactive maintenance planning.
4. Efficient Communication
Standardized failure codes provide a common language for communication among team members. This ensures clarity and precision when discussing equipment problems, reducing the chances of misunderstandings.
5. Streamlined Workflows
Integrating failure codes into maintenance processes streamlines workflows. They serve as mandatory steps, ensuring that necessary information is captured at each stage, from reporting an issue to resolving it.
6. Performance Measurement
By tracking the frequency and types of failures, organizations can assess the overall performance of equipment. This data helps in making informed decisions about maintenance strategies and resource allocation.
7. Training and Knowledge Transfer
Failure codes contribute to training programs by providing a structured framework for understanding equipment issues. New technicians can quickly learn and established codes, promoting knowledge transfer within the team.
8. Continuous Improvement
The aggregated data from failure codes becomes a valuable resource for continuous improvement. Organizations can learn from past failures, refine maintenance strategies, and enhance overall operational efficiency.
In essence, failure codes serve as a vital tool in the maintenance toolkit, contributing to better communication, informed decision-making, and the overall effectiveness of asset management processes.
In conclusion, failure codes prove to be indispensable in the realm of asset management and maintenance planning. By providing a structured system for capturing and categorizing information about equipment issues, these codes facilitate efficient communication and analysis.
The relevancy of failure codes becomes evident in their role in diagnostic insights, streamlined workflows, and the continuous improvement of maintenance practices. A well-implemented failure code system enables organizations to identify patterns, make informed decisions, and allocate resources effectively.
As a result, maintenance planning and scheduling become more proactive, minimizing downtime, reducing costs, and enhancing overall operational efficiency. Embracing and leveraging the power of failure codes is a strategic approach toward achieving optimal asset performance and maximizing the lifespan of equipment.
We encourage you to consider taking Maintenance Planning and Scheduling training with PetroSync. Our training program not only covers essential aspects of maintenance but also includes comprehensive insights into failure modes, aligning with the crucial role of failure codes in asset management.
Our Maintenance Planning and Scheduling training will equip you with valuable knowledge and skills to effectively plan and schedule maintenance activities, minimizing downtime and optimizing asset performance. PetroSync‘s structured approach ensures that you gain a clear understanding of maintenance best practices, including the strategic use of failure codes for improved diagnostic insights and continuous improvement.
Credit: Vecteezy
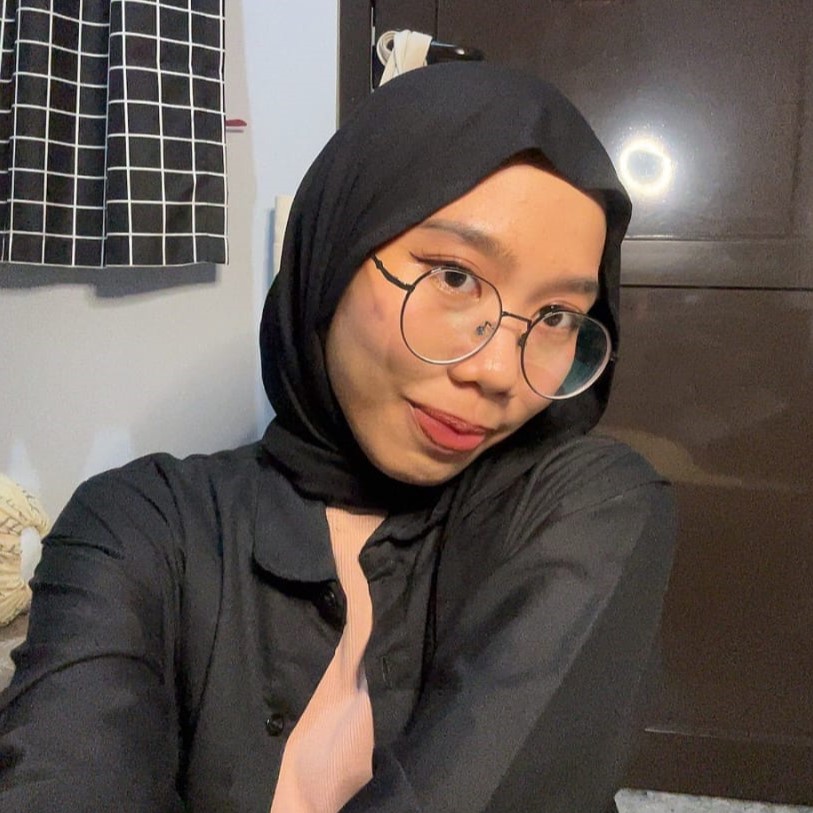
SEO specialist by day, fact-checker by night. An avid reader and content writer dedicated to delivering accurate and engaging articles through research and credible sources.