In the ever-changing world of industrial operations, the consistent performance of assets is vital for ongoing success. Reliability and asset management play essential roles, overseeing the careful control and improvement of valuable resources in an organization. Whether it’s machinery, equipment, or key infrastructure, the smooth operation of these assets is crucial for reducing downtime, boosting efficiency, and protecting against unexpected disruptions.
What Is Asset Management and Reliability?
Reliability asset management is a systematic and comprehensive approach that combines managerial art with engineering science to coordinate all asset management activity within a business enterprise.
It aims to ensure that equipment, machinery, and systems consistently perform their intended functions without unexpected breakdowns, strategically maintaining, monitoring, and optimizing these assets throughout their lifecycle.
The goal of reliability and asset management is to enhance operational efficiency, reduce downtime, and maximize the overall reliability and lifespan of the assets, contributing to the smooth functioning of the business. An asset management & reliability program is designed to realize maximum operational and financial value from the business’ critical physical assets.
What Is Reliability?
Reliability refers to the consistency and dependability of a system, process, or equipment, and it is the probability that a product, system, or service will perform its intended function adequately for a specified period. In simpler terms, it measures how well something works over time and how likely it is to keep working without unexpected interruptions. A high level of reliability indicates a more trustworthy and consistent performance, while low reliability suggests a higher likelihood of disruptions or failures.
How Do I Measure The Reliability of An Asset?
To measure the reliability of an asset, you can use a formula that considers three key factors: Quality Performance, Time Performance, and Speed Performance.
The formula is:
Reliability Index=MTBPL/MPL
Where:
- MTBPL stands for Mean Time Between Production Loss (Time running/number of production losses)
- MPL stands for Tons Lost/Number of Production Losses
To calculate the Reliability Index, you multiply the percentages of Quality Performance, Time Performance, and Speed Performance. For example, if each performance factor is 90%, the calculation would be:
Reliability Index=90%×90%×90%=72.9%
This index provides a numerical representation of the asset’s reliability. Additionally, when measuring time performance, it’s crucial to consider all available hours, such as 8,760 hours in a year, excluding market-related downtime and time for capital rebuilds. This comprehensive approach ensures a more accurate evaluation of the asset’s overall production reliability.
What Is Asset Management?
Asset management involves the organized and strategic control of valuable items or resources that a business owns, considering the entire lifecycle of plant assets, such as equipment, parts, production lines, and the plant buildings themselves. It includes planning, monitoring, and optimizing these resources to generate maximum value. In simpler terms, asset management is about efficiently handling and getting the most from the things a business owns to contribute to its success.
When To Perform Reliability and Asset Management?
Understanding when to perform reliability and asset management is crucial for ensuring the efficient and effective operation of a business or industrial facility.
Condition |
Checklist |
|
1. | Asset management processes do not cover critical assets’ lifecycles in their entirety. | Evaluate when there is an incomplete understanding or coverage of critical asset life cycles, ensuring comprehensive management from acquisition to retirement. |
2. | High, or increasing, estimated exposure to property damage or business interruption loss. | Conduct when there’s a significant risk of property damage or disruptions to business operations, emphasizing proactive measures for prevention and preparedness. |
3. | Absence of a comprehensive system of KPIs for asset performance, maintenance, and replacement. | Perform when key performance indicators (KPIs) are lacking, aiming to establish a systematic approach for measuring and improving asset performance and maintenance. |
4. | Long lead times for replacement of critical production and /or infrastructure equipment not identified. | Address when delays in replacing crucial equipment are not identified, emphasizing the importance of timely identification and planning for replacements. |
5. | Underutilization or overutilization of the company’s Computerized Maintenance Management System (CMMS). | Evaluate when the CMMS is not optimally utilized, focusing on streamlining its use for efficient maintenance planning, scheduling, and tracking. |
6. | Asset Management and Reliability Process Troubleshooting. | Engage in troubleshooting when there are issues or gaps in the asset management and reliability processes, ensuring continuous improvement and effectiveness. |
7. | Underdeveloped “change management” processes. | Examine when change management processes are underdeveloped, emphasizing the need for robust processes to handle changes affecting assets and reliability. |
8. | Poor asset performance, poor maintenance performance, or excessive or escalating costs of asset maintenance or operational downtime, as measured by established KPIs. | Investigate when there are indications of poor asset or maintenance performance, aiming to address issues and optimize costs based on established KPIs. |
9. | Inadequate tracking of, or insufficient attention to, asset performance, maintenance performance and costs, in comparison to established KPIs. | Assess when there is a lack of focus on tracking and analyzing asset and maintenance performance against established KPIs, emphasizing the need for attention and improvement. |
10. | Business interruption exposures are not adequately considered in asset contingency planning. | Review when there is insufficient consideration of business interruption risks in asset contingency planning, ensuring comprehensive planning to minimize disruptions. |
11. | “Maintenance planning” drives “operations planning,” rather than vice-versa. | Address when maintenance planning takes precedence over operational planning, emphasizing the need for a balanced approach that aligns both for overall efficiency. |
12. | Absence of a formal process for analysis and management of third-party recommendations. | Evaluate when there is no formal process for analyzing and managing recommendations from third parties, emphasizing the importance of a structured approach for effective integration. |
13. | Asset management strategies seem more “time and compliance” based, rather than “asset performance and conditions” based. | Examine when strategies are focused on time and compliance rather than asset performance, emphasizing the need to shift towards performance and condition-based strategies for improved outcomes. |
14. | Investment in hi-tech solutions to address asset management issues without collection and thorough analysis of applicable data. | Assess when there’s a focus on technology solutions without sufficient data collection and analysis, emphasizing the importance of informed decision-making based on relevant data. |
15. | High rates of turnover in company personnel and/or third-party contractors. | Consider when there is a high turnover of personnel or contractors, addressing the impact on continuity and knowledge transfer in asset management and reliability processes. |
What Is The Difference Between Asset and Reliability?
An asset refers to any valuable item or resource that a business owns and utilizes to generate value, while asset reliability measures how long equipment performs its intended function. This can include physical items like machinery, buildings, or vehicles, as well as intangible assets like patents or trademarks.
In the context of reliability asset management, reliability specifically involves ensuring that these assets consistently perform their intended functions without unexpected failures. It focuses on optimizing the performance and longevity of assets to enhance overall operational efficiency and minimize disruptions in business activities.
Taking steps to boost your expertise in reliability engineering can greatly advance your career in the oil and gas, petrochemical, and energy fields. PetroSync’s Certified Reliability Engineer training is tailored to provide you with the knowledge and skills needed to excel in this crucial area.
This program not only deepens your understanding of reliability principles but also offers practical insights you can apply directly to your work. By enrolling in this training, you’re not just getting a certification; you’re opening doors to new opportunities and positioning yourself as a valuable asset in your industry. Invest in your professional growth by joining PetroSync‘s Certified Reliability Engineer training and empower yourself to contribute to the success of your organization!
Credit: Freepik
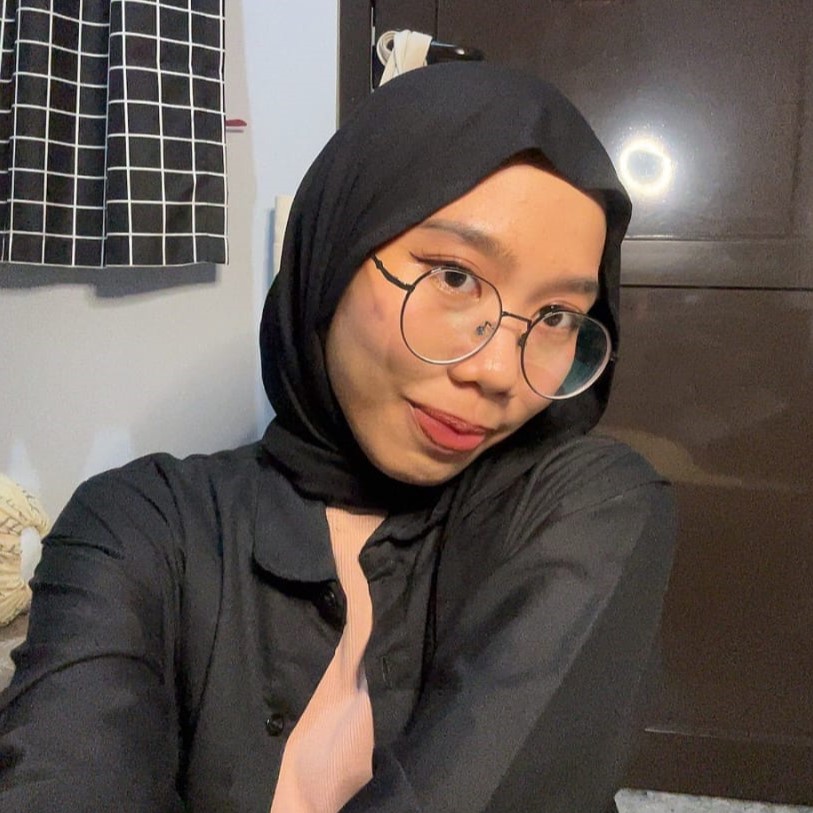
SEO specialist by day, fact-checker by night. An avid reader and content writer dedicated to delivering accurate and engaging articles through research and credible sources.