In fast-paced and asset-intensive industries such as oil and gas, the potential to keep dependable tools operations is now not a luxurious – it’s a necessity. Equipment failure can motive tens of millions in unplanned downtime, pose protection hazards, and severely have an effect on manufacturing schedules.
This is why forward-thinking companies are adopting a greater strategic method to renovation – Reliability Centered Maintenance (RCM). RCM goes past actually fixing machines. It represents a cultural and procedural shift that focuses on grasp asset functionality, failure patterns, and preservation movements that forestall these failures.
When true implemented, RCM can substantially extend uptime, minimize renovation costs, and prolong asset existence cycles.
What is Reliability Centered Maintenance?
Reliability Centered Maintenance is a structured framework used to determine the most effective maintenance strategies for critical assets. It aims to ensure that systems continue to perform their intended functions reliably, efficiently, and safely within a defined operating context.
RCM differs from traditional approaches by focusing not just on the likelihood of failure, but more importantly on the consequences of failure. This approach allows maintenance resources to be prioritized based on asset criticality and failure impact, ensuring that companies avoid wasting time on over-maintaining non-essential equipment.
A typical RCM process includes:
- Identifying the functions of the asset
- Determining potential failure modes
- Analyzing the impact of failures
- Selecting the most appropriate maintenance tactics (e.g., predictive, preventive, or redesign)
What is the RCM Theory of Maintenance?
The theory behind RCM is rooted in a major insight: not all failures can or should be prevented through scheduled maintenance. This idea challenged decades of conventional wisdom which assumed that equipment should be maintained at regular intervals to prevent breakdowns.
RCM theory, first formalized in the aviation sector during the 1960s, and later documented in the SAE JA1011 standard, proposes seven core questions that guide the maintenance strategy:
1. What are the asset’s functions?
2. How can it fail to perform those functions?
3. What causes each failure?
4. What happens when the failure occurs?
5. What are the consequences of the failure?
6. What proactive tasks can prevent or detect the failure?
7. What should be done if a suitable proactive task cannot be found?
This logical structure ensures that maintenance decisions are function-focused, failure-driven, and risk-informed. The goal is not simply to prevent failures, but to manage the risks and consequences of those failures in the most cost-effective way.
What is an Example of RCM Maintenance?
Imagine a centrifugal pump in an offshore oil platform responsible for circulating cooling water through critical systems. A failure in this pump could overheat vital equipment, leading to production shutdowns or even safety incidents.
Through RCM analysis, the maintenance team may identify the following failure modes:
- Bearing wear due to improper lubrication
- Seal leakage leading to corrosion
- Impeller erosion from abrasive particles
Each of these has different consequences. RCM might prescribe:
- Installing vibration sensors for early detection of bearing wear
- Weekly visual inspection of seals
- Fluid analysis every month to monitor particle contamination
This tailored maintenance plan addresses real-world conditions and focuses on early detection and prevention, which is far more efficient than waiting for a failure to happen.
What is the Difference Between Reliability Centered Maintenance and TPM?
While each RCM and TPM (Total Productive Maintenance) goal to enhance gear reliability, they fluctuate drastically in focal point and methodology. RCM is especially treasured for high-risk, high-cost assets, the place failure can have serious protection or manufacturing consequences.
TPM, on the different hand, encourages a company-wide effort to enhance daily performance, frequently via things to do like self sustaining upkeep and non-stop improvement. Some leading companies integrate both: RCM for strategic planning and TPM for operational execution.
PetroSync Training: Join the Path to Professional Growth
Implementing Reliability Centered Maintenance (RCM) efficiently doesn’t manifest overnight. It needs greater than technical knowledge—it requires strategic insight, sensible tools, and hands-on ride tailor-made to your industry. That’s precisely what PetroSync offers.
We design our specialised coaching programs in Reliability and Maintenance to meet the needs of senior professionals, from engineers and planners to asset managers and decision-makers. With our expert-led courses, you’ll no longer solely analyze the principle in the back of RCM but additionally how to follow it correctly in complex, real-world operations.
At PetroSync, we go past traditional training. You’ll achieve get right of entry to to worldwide instructors, sensible case studies, and established frameworks that raise your protection strategy. Whether your purpose is to minimize downtime, increase asset performance, or lead a high-performing renovation team, our education offers you the aspect to make it happen.
Ready to release new fee from your belongings and develop your career?
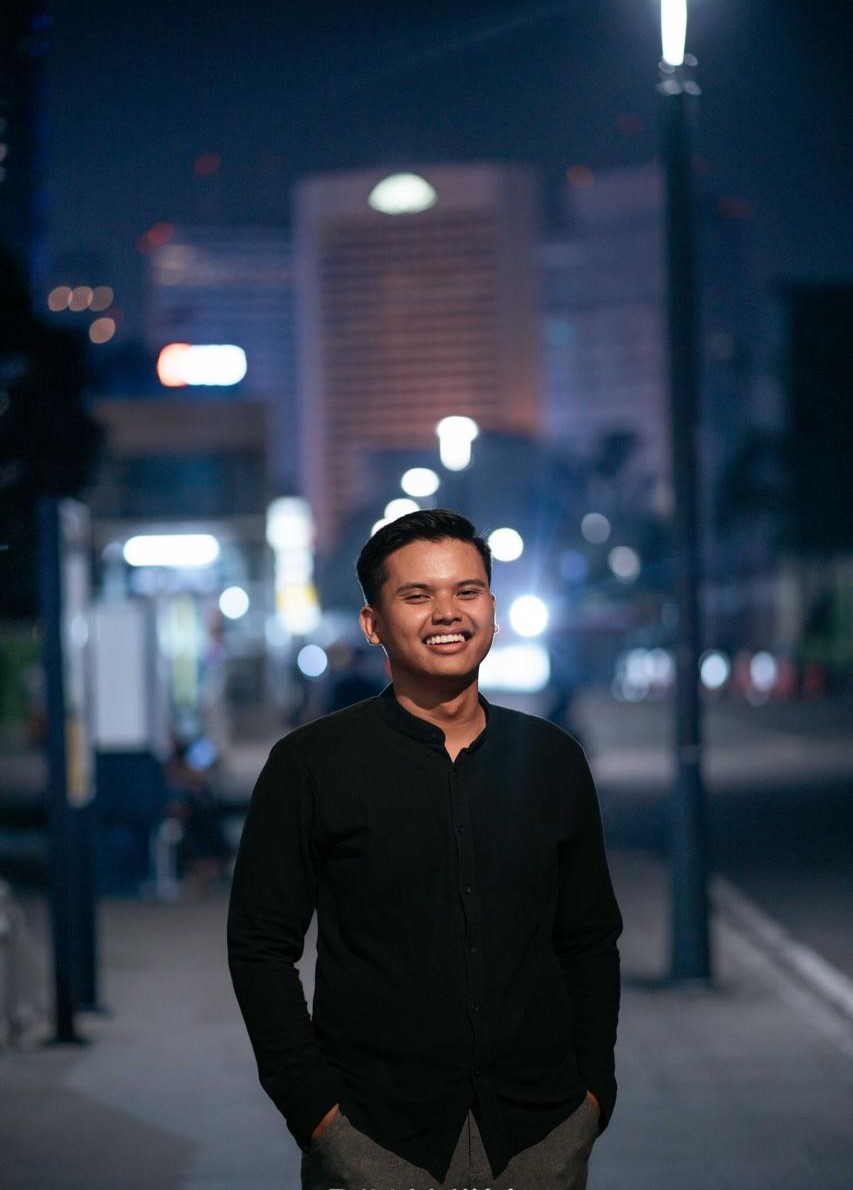
Results-oriented and thorough SEO specialist with extensive experience in conducting keyword research, developing and implementing digital website promotion strategies and plans, managing campaigns to develop company websites in the digital world, excellent knowledge of marketing techniques and principles, and attentive strong attention to detail.