In the high-stakes world of oil and gas, the place of downtime can imply hundreds of thousands in losses and security incidents can raise catastrophic consequences, preservation is no longer simply a department – it’s a strategic imperative. Maintenance planning and scheduling are no longer considered as back-office duties however are now diagnosed as central pillars of operational excellence.
Companies that excel in this location persistently outperform rivals in uptime, protection compliance, and price control. Yet, many organizations still struggle to move beyond reactive maintenance or find themselves overwhelmed by unplanned downtime, equipment failure, or inefficient workforce utilization.
In this article, we delve into best practices that can revolutionize your maintenance program and position your business for long-term operational success.
What is Maintenance Planning and Scheduling?
Maintenance planning and scheduling is the method of identifying and organizing all the resources, tools, parts, and directions wanted to function to protect things to do efficiently. It solves the “what,” “how,” and “with what resources” questions. Scheduling, on the other hand, solves the “when” and “by whom” – it is the time-based agency of deliberate things to do to limit conflicts and manufacturing disruptions.
Proper planning ensures that work can be performed safely and effectively, while proper scheduling ensures minimal downtime and optimal resource use. When integrated, planning and scheduling can increase technician productivity by up to 50% and reduce emergency work dramatically, according to the Marshall Institute.
A worthwhile safety technique entails every role working together. Planning besides scheduling penalties in neglected chances and chaos, while scheduling barring planning many times leads to delays and rework.
What is the Best Practice for Maintenance?
To be effective, preservation practices should be proactive, data-driven, and aligned with enterprise goals. Below are key best practices adopted by leading organizations:
1. Digital Integration with CMMS:
A Computerized Maintenance Management System (CMMS) approves real-time monitoring of work orders, asset history, inventory levels, and labor availability.
2. Standard Job Plans (SJPs):
Create templates for activities preservation duties that encompass all tools, protection requirements, and estimated times. This reduces planning time, improves consistency, and minimizes errors.
3. Maintenance KPIs and Analytics:
Regularly track Key Performance Indicators such as Mean Time to Repair (MTTR), Mean Time Between Failures (MTBF), and Schedule Compliance. These metrics allow you to measure progress and identify areas needing improvement.
4. Preventive and Predictive Maintenance (PM & PdM):
Moving from reactive to proactive safety exceedingly enhances reliability. Preventive renovation is time or usage-based, at the same time as predictive makes use of sensors and AI to comprehend feasible failures.
5. Collaborative Workflows:
Coordination amongst operations, procurement, and engineering ensures that renovation things to do do no longer disrupt manufacturing and that components and equipment are on hand in time.
6. Root Cause Analysis (RCA):
Every failure ought to be investigated utterly to decide its root cause. A sturdy RCA system reduces recurrence and leads to smarter planning.
Implementing these best practices doesn’t just improve maintenance—it transforms the entire production ecosystem.
How to Schedule a Maintenance Plan?
Effective scheduling ensures the right work is done at the right time with the right resources. Here’s how to do it:
1. Prioritize Based on Criticality:
Not all properties are equal. Use techniques like Failure Mode and Effects Analysis (FMEA) or Reliability Centered Maintenance (RCM) to rank property by way of ability of value to safety, production, and cost.
2. Create a Maintenance Calendar:
Develop weekly, monthly, and annual calendars that align with manufacturing cycles, shutdowns, and labor availability. Rolling schedules permit flexibility whilst retaining structure.
3. Coordinate Resources and Materials:
Ensure that spare parts, permits, and gear are reachable in the past when the job starts. This reduces downtime and improves wrench time.
4. Use Look-Ahead Schedules:
Plan at least 2-4 weeks in advance to permit ample time for procurement and useful resource allocation. This proactive step ensures seamless execution.
5. Daily and Weekly Review Meetings:
Maintenance planners and supervisors ought to meet many situations to alter schedules, cope with emergencies, and reallocate property as needed.
6. Track Compliance and Backlog:
Monitor scheduled vs. performed work. A wholesome backlog (2-4 weeks of deliberate work) shows advantageous planning.
What are the 4 Types of Maintenance Strategy?
Understanding the suitable protection approach for each asset can drastically beautify ordinary overall performance and minimize costs. Here are the four most regularly occurring types:
1. Corrective Maintenance (CM):
Also known as reactive maintenance, this is carried out after equipment fails. It may additionally be appropriate for non-critical assets, however conventional use leads to greater expenses and security risks.
2. Preventive Maintenance (PM):
Scheduled primarily based on time or utilization intervals, PM reduces the possibility of surprising breakdowns. It is reasonably-priced for most properties and improves tools lifespan.
3. Predictive Maintenance (PdM):
Uses real-time records from sensors and IoT devices to predict screw ups beforehand then they occur. Though preliminary funding is high, PdM provides the best possible ROI in the lengthy term.
4. Reliability-Centered Maintenance (RCM):
A complete method that evaluates the features of an asset and develops a custom-made renovation design targeted on safety, operations, and cost-effectiveness.
According to the International Journal of Engineering Research & Technology (IJERT), integrating PdM and RCM can enlarge asset availability to over 90% whilst slicing renovation fees by means of 25-30%.
Join PetroSync for Specialized Technical Training
If you are a senior engineer, upkeep manager, or operational chief searching to sharpen your team’s abilities and enhance upkeep performance, PetroSync gives technical education tailor-made to your enterprise needs.
Our specialised Maintenance and Reliability courses are designed with real-world case studies, hands-on exercises, and professional instructors who apprehend the unique challenges of the oil and gasoline sector.
Whether you are looking out to restrict downtime, adorn safety, or put in pressure predictive maintenance, our applications equip your crew with the gear and information to electricity measurable impact.
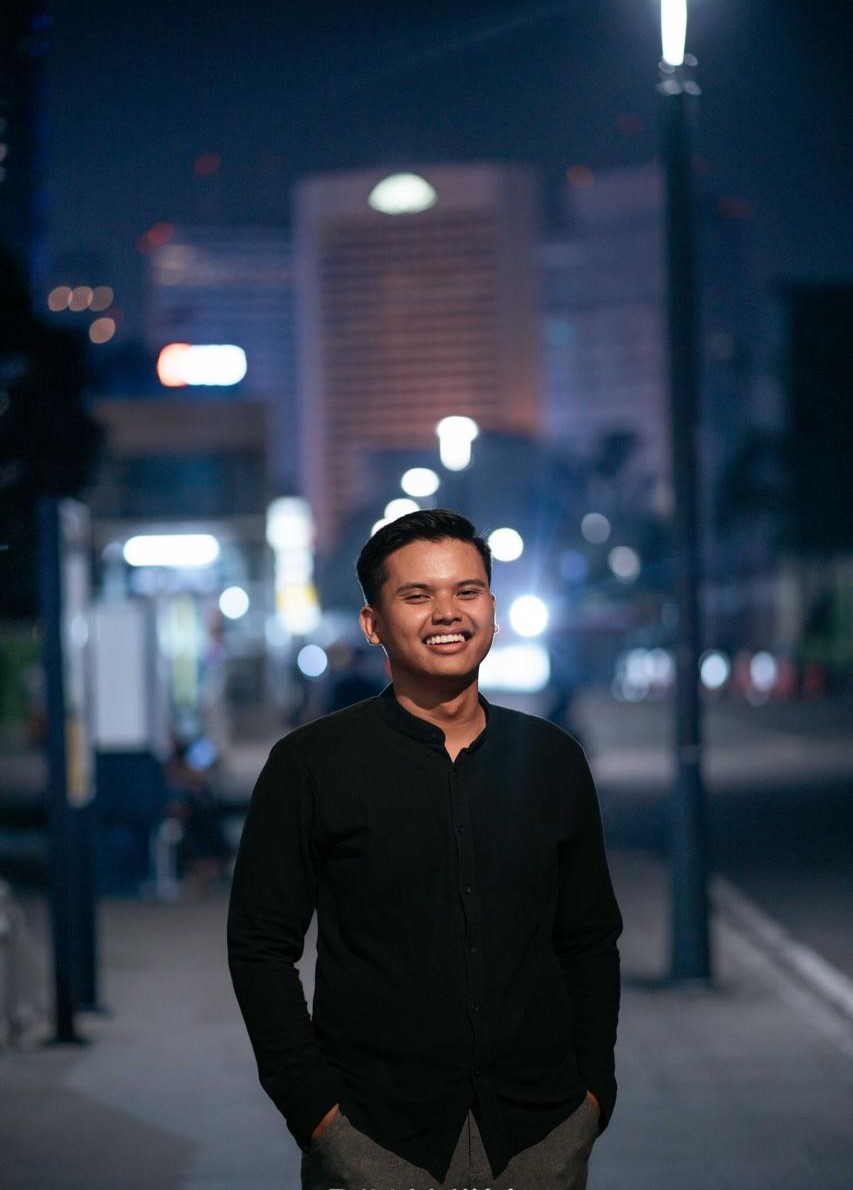
Results-oriented and thorough SEO specialist with extensive experience in conducting keyword research, developing and implementing digital website promotion strategies and plans, managing campaigns to develop company websites in the digital world, excellent knowledge of marketing techniques and principles, and attentive strong attention to detail.