In the field of engineering, the utmost priority lies in ensuring safety and reliability. Among the array of tools and methodologies employed for safety, Failure Mode and Effects Analysis (FMEA) holds a significant position. FMEA serves as a robust instrument in Risk-Based Inspection (RBI) strategies, providing organizations with the means to identify and mitigate potential risks. In this article, we will dive deep into the fundamentals and the process of making FMEA analysis.
What Is Failure Modes and Effect Analysis?
Failure Modes and Effect Analysis (FMEA) is a systematic and proactive method, aiming to identify where and how it might fail and to assess the relative impact of different failures. Its primary goal is to identify areas within the process that require improvements and changes.
Failure modes refer to the different ways in which a system or component can fail or stop functioning as intended. One can categorize failure modes according to the type of failure, including physical failure (like structural damage), functional failure (such as the inability to perform a required function), or systemic failure (like the breakdown of an entire system).
Meanwhile, effect analysis refers to the process of examining the potential consequences or impacts of a particular action or event. Engineers usually perform an FMEA to identify potential failures by examining system or process components and determining failure modes, taking into account the severity, likelihood of occurrence, and detectability of each failure mode.
What Is An Example of A Failure Mode?
A well blowout is an example of a failure mode that can occur in the oil and gas industry. When the pressure in a well exceeds the strength of the equipment that contains it, oil, gas, and other fluids may escape uncontrollably.
The consequences of well blowouts can be severe in terms of environmental damage and safety hazards, such as oil spills, fires, and explosions. Oil and gas companies employ various safety measures, including blowout preventers, pressure control systems, and well-monitoring equipment to prevent well blowouts.
Corrosion of pipelines and other equipment is another failure mode that can occur in the oil and gas industry. This process can weaken the structural integrity of pipelines and other components, increasing the likelihood of leaks, spills, and other types of failures. Corrosion can be triggered by exposure to a range of factors, such as water, oxygen, and other corrosive substances.
To combat corrosion, oil and gas companies often utilize corrosion-resistant materials, protective coatings, and regular inspection and maintenance of equipment. Considering how deadly failure modes in the oil and gas industry can be, FMEA becomes a common utility to identify potential failure modes and to reduce or eliminate their negative effects, thereby preventing well blowouts, corrosion of the equipment, and any other accidents from occurring in the oil and gas industry.
What Are The 5 Steps of The FMEA Process?
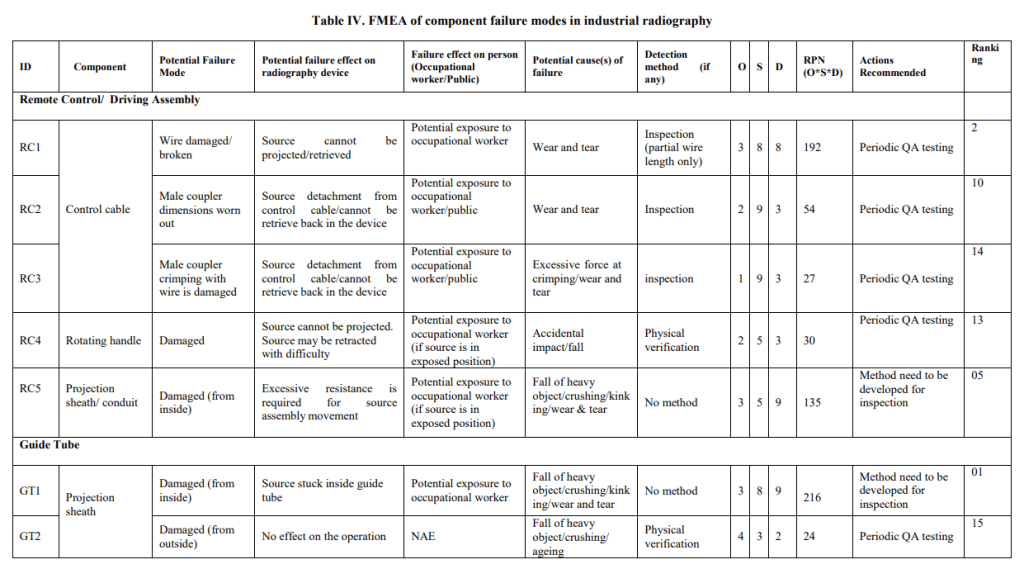
API 580 is a suggested procedure developed by the American Petroleum Institute (API) that offers direction on executing Risk Based Inspection (RBI) evaluations for equipment and pipelines in the oil and gas sector. To perform FMEA according to API 580, follow these steps:
1. Define The Scope of The Analysis
Identify the limits of the system being examined, comprising the machinery or conduit, and the projected operational circumstances. To begin the FMEA process, the identifying information should be filled out at the top of the FMEA form, as shown in Table IV. The remaining steps will require information that will be entered into the columns of the form.
2. Identify Failure Modes
Engage in a creative session and recognize all conceivable ways in which the system may fail. This can be accomplished by analyzing records, reviewing equipment manuals, and seeking advice from experts in the relevant field. To complete this step, fill out and evaluate the likelihood of failure and the severity of the consequences.
- Evaluate The Likelihood of Failure
Evaluate the likelihood of each potential failure mode by examining its frequency of occurrence and the probability of detecting it.
- Evaluate The Severity of The Consequences
Analyze the effects that result from every possible way in which something could fail, and assess how it would affect aspects such as safety, the environment, production, and cost
3. Assign a Risk Priority Number (RPN)
The Risk Priority Number (RPN) is obtained by multiplying the probability and severity ratings and is utilized to rank the failure modes in order to determine which ones require further examination. Assign an occurrence rating (O), for each cause, Evaluate each control by assigning a detection rating (D), and determine the severity level by assigning an (S).
4. Develop Mitigation Strategies
Create plans to reduce the most critical potential causes of failure, which could involve altering equipment design, carrying out proactive maintenance procedures, or enhancing methods for monitoring and inspecting.
5. Review and Update the FMEA
Regularly evaluate and revise the FMEA (Failure Mode and Effects Analysis) to guarantee that it stays up-to-date and appropriate, especially following any modifications made to the system or operational circumstances.
The process of FMEA is quite complex. It requires specialized knowledge and expertise in multiple areas. Those who want to conduct the FMEA approach can join API 580 and API 581 training and Reliability Centered Maintenance training course to acquire the necessary skills and understanding of the FMEA process thoroughly.
PetroSync crafts API 580 and 581 training with a comprehensive outline. Our training focuses on API 580 Risk-Based Inspection and API Publication 581 Base Resource Document as its foundation.
The initial focus of the course is to provide practical and effective approaches to implementing a successful RBI program, without causing unnecessary complexity. The training aims to explain the RBI framework and methodology in a straightforward way so that the company can execute a risk-based inspection program that aligns with its specific objectives.
You can also learn FMEA methodologies to implement effective controls to prevent failures. By attending this training, you can gain the knowledge and skills required to carry out successful FMEA analysis and perform a Risk Based Inspection with better decision-making and resource allocation. Join us and maximize the efficiency and effectiveness of your inspection techniques with PetroSync!
Credit header image: freepik.com
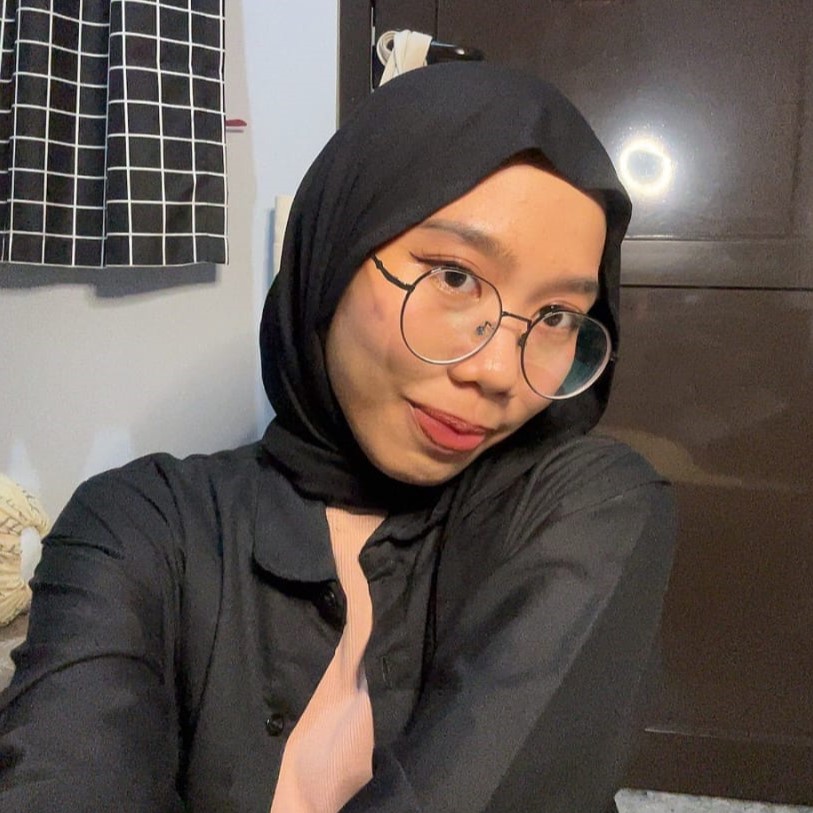
SEO specialist by day, fact-checker by night. An avid reader and content writer dedicated to delivering accurate and engaging articles through research and credible sources.