As competition in the industrial world heats up, the dependability sector has emerged as a critical aspect in assuring performance and equipment life for optimal systems. Today, the Certified Reliability Engineer (CRE) plays a critical role in reducing failures, boosting productivity, and lowering costs.
The Certified Reliability Engineer (CRE) training will cover the most significant components of a comprehensive guide for professionals looking to participate and advance their careers.
What Is Certified Reliability Engineer Training Course Overview?
PetroSync creates Certified Dependability Engineer (CRE) training for experienced professionals who want to improve their knowledge, insights, and skills in product, system, and process dependability. This training curriculum includes a range of topics, including:
– Reliability Management
– Probability and Statistics for Reliability
– Reliability in Design and Development
– Reliability Modeling and Predictions
– Reliability Testing
– Maintainability and Availability
– Data Collection and Use
Participants in this course will get valuable knowledge about implementing effective dependability techniques in the real world through a combination of theoretical and practical teaching.
What Is the Certified Reliability Engineer Training Course Objective?
The primary goal of Certified Reliability Engineer (CRE) training is to provide participants with the skills necessary to comprehend reliability concepts and practices. At the end of this course, participants will be adept in the use of statistical tools, reliability modeling, and risk management techniques to improve the dependability and performance of engineering systems.
We intend to develop this course for professionals preparing to take the Certified Reliability Engineer (CRE) certification exam and who wish to improve their skills and dedication to excellence in the sector.
What Is Certified Reliability Engineer Training Course Outline?
We provide this training for five days. Each day will focus on a unique element of reliability engineering. To learn more about what the Certified Reliability Engineer (CRE) course includes, please refer to the information below:
Day 1: Reliability Management
- Strategic management
- Benefits of reliability engineering
- Describe how reliability engineering techniques and methods improve programs, processes, products, systems, and services. (Understand)
- Interrelationship of safety, quality, and reliability
- Define and describe the relationships among safety, reliability, and quality. (Understand)
- Role of the reliability function in the organization
- Describe how reliability techniques can be applied in other functional areas of the organization, such as marketing, engineering, customer /product support, safety and product liability, etc. (Apply)
- Reliability in product and process development
- Integrate reliability engineering techniques with other development activities, concurrent engineering, corporate improvement initiatives such as lean and six sigma methodologies, and emerging technologies. (Apply)
- Failure consequence and liability management
- Describe the importance of these concepts in determining reliability acceptance criteria. (Understand)
- Warranty management
- Define and describe warranty terms and conditions, including warranty period, conditions of use, failure criteria, etc., and identify the uses and limitations of warranty data. (Understand)
- Customer needs assessment
- Use various feedback methods (e.g., quality function deployment (QFD), prototyping, beta testing) to determine customer needs in relation to reliability requirements for products and services. (Apply)
- Supplier reliability
- Define and describe supplier reliability assessments that can be monitored in support of the overall reliability program. (Understand)
- Reliability program management
- Terminology
- Explain basic reliability terms (e.g., MTTF, MTBF, MTTR, availability, failure rate, reliability, maintainability). (Understand)
- Elements of a reliability program
- Explain how planning, testing, tracking, and using customer needs and requirements are used to develop a reliability program, and identify various drivers of reliability requirements, including market expectations and standards, as well as safety, liability, and regulatory concerns. (Understand)
- Types of risk
- Describe the relationship between reliability and various types of risk, including technical, scheduling, safety, financial, etc. (Understand)
- Product lifecycle engineering
- Describe the impact various lifecycle stages (concept/design, introduction, growth, maturity, decline) have on reliability, and the cost issues (product maintenance, life expectation, software defect phase containment, etc.) associated with those stages. (Understand)
- Design evaluation
- Use validation, verification, and other review techniques to assess the reliability of a product’s design at various lifecycle stages. (Analyze)
- Systems engineering and integration
- Describe how these processes are used to create requirements and prioritize design and development activities. (Understand)
- Ethics, safety, and liability
- Ethical issues
- Identify appropriate ethical behaviors for a reliability engineer in various situations. (Evaluate)
- Roles and responsibilities
- Describe the roles and responsibilities of a reliability engineer in relation to product safety and liability. (Understand)
- System safety
- Identify safety-related issues by analyzing customer feedback, design data, field data, and other information. (Analyze)
- Case Study/Exercise: Performing FMEA studies as well as RCA (5 methods)
Day 2: Probability and Statistics for Reliability
- Basic concepts
- Statistical terms
- Define and use terms such as population, parameter, statistic, sample, the central limit theorem, etc., and compute their values. (Apply)
- Basic probability concepts
- Use basic probability concepts (e.g., independence, mutually exclusive, conditional probability) and compute expected values. (Apply)
- Discrete and continuous probability distributions
- Compare and contrast various distributions (binomial, Poisson, exponential, Weibull, normal, log-normal, etc.) and their functions (e.g., cumulative distribution functions (CDFs), probability density functions (PDFs), hazard functions), and relate them to the bathtub curve. (Analyze)
- Poisson process models
- Define and describe homogeneous and non-homogeneous Poisson process models (HPP and NHPP). (Understand)
- Non-parametric statistical methods
- Apply non-parametric statistical methods, including median, Kaplan-Meier, Mann-Whitney, etc., in various situations. (Apply)
- Sample size determination
- Use various theories, tables, and formulas to determine appropriate sample sizes for statistical and reliability testing. (Apply)
- Statistical process control (SPC) and process capability
- Define and describe SPC and process capability studies (Cp, Cpk, etc.), their control charts, and how they are all related to reliability. (Understand)
- Statistical inference
- Point estimates of parameters
- Obtain point estimates of model parameters using probability plots, maximum likelihood methods, etc. Analyze the efficiency and bias of the estimators. (Evaluate)
- Statistical interval estimates
- Compute confidence intervals, tolerance intervals, etc., and draw conclusions from the results. (Evaluate)
- Hypothesis testing (parametric and non-parametric)
- Apply hypothesis testing for parameters such as means, variance, proportions, and distribution parameters.
- Interpret significance levels and Type I and Type II errors for accepting/rejecting the null hypothesis. (Evaluate)
Day 3: Reliability in Design and Development
- Reliability design techniques
- Environmental and use factors
- Identify environmental and use factors (e.g., temperature, humidity, vibration) and stresses (e.g., severity of service, electrostatic discharge (ESD), throughput) to which a product may be subjected. (Apply)
- Stress-strength analysis
- Apply stress-strength analysis method of computing probability of failure, and interpret the results. (Evaluate)
- FMEA and FMECA
- Define and distinguish between failure mode and effects analysis and failure mode, effects, and criticality analysis and apply these techniques in products, processes, and designs. (Analyze)
- Common mode failure analysis
- Describe this type of failure (also known as common cause mode failure) and how it affects design for reliability. (Understand)
- Fault tree analysis (FTA) and success tree analysis (STA)
- Apply these techniques to develop models that can be used to evaluate undesirable (FTA) and desirable (STA) events. (Analyze)
- Tolerance and worst-case analyses
- Describe how tolerance and worst-case analyses (e.g., root of sum of squares, extreme value) can be used to characterize variation that affects reliability. (Understand)
- Design of experiments
- Plan and conduct standard design of experiments (DOE) (e.g., full-factorial, fractional factorial, Latin square design). Implement robust-design approaches (e.g., Taguchi design, parametric design, DOE incorporating noise factors) to improve or optimize design. (Analyze)
- Fault tolerance
- Define and describe fault tolerance and the reliability methods used to maintain system functionality. (Understand)
- Reliability optimization
- Use various approaches, including redundancy, derating, trade studies, etc., to optimize reliability within the constraints of cost, schedule, weight, design requirements, etc. (Apply)
- Human factors
- Describe the relationship between human factors and reliability engineering. (Understand)
- Design for X (DFX)
- Apply DFX techniques such as design for assembly, testability, maintainability environment (recycling and disposal), etc., to enhance a product’s producibility and serviceability. (Apply)
- Reliability apportionment (allocation) techniques
- Use these techniques to specify subsystem and component reliability requirements. (Analyze)
- Parts and systems management
- Selection, standardization, and reuse
- Apply techniques for materials selection, parts standardization and reduction, parallel modeling, software reuse, including commercial off-the-shelf (COTS) software, etc. (Apply)
- Derating methods and principles
- Use methods such as S-N diagram, stress-life relationship, etc., to determine the relationship between applied stress and rated value, and to improve design. (Analyze)
- Parts obsolescence management
- Explain the implications of parts obsolescence and requirements for parts or system requalification. Develop risk mitigation plans such as lifetime buy, backwards compatibility, etc. (Apply)
- Establishing specifications
- Develop metrics for reliability, maintainability, and serviceability (e.g., MTBF, MTBR, MTBUMA, service interval) for product specifications. (Create)
Day 3/Day 4: Reliability Modeling and Predictions
- Reliability modeling
- Sources and uses of reliability data
- Describe sources of reliability data (prototype, development, test, field, warranty, published, etc.), their advantages and limitations, and how the data can be used to measure and enhance product reliability. (Apply)
- Reliability block diagrams and models
- Generate and analyze various types of block diagrams and models, including series, parallel, partial redundancy, time-dependent, etc. (Create)
- Physics of failure models
- Identify various failure mechanisms (e.g., fracture, corrosion, memory corruption) and select appropriate theoretical models (e.g., Arrhenius, S-N curve) to assess their impact. (Apply)
- Simulation techniques
- Describe the advantages and limitations of the Monte Carlo and Markov models. (Apply)
- Dynamic reliability
- Describe dynamic reliability as it relates to failure criteria that change over time or under different conditions. (Understand)
- Reliability predictions
- Part count predictions and part stress analysis
- Use parts failure rate data to estimate system- and subsystem-level reliability. (Apply)
- Reliability prediction methods
- Use various reliability prediction methods for both repairable and non-repairable components and systems, incorporating test and field reliability data when available (Apply)
- Case Study/Exercise: Data analytics and advanced topics (Markov chains and Monte Carlo simulation)
Day 4: Reliability Testing
- Reliability test planning
- Reliability test strategies
- Create and apply the appropriate test strategies (e.g., truncation, test–to-failure, degradation) for various product development phases. (Create)
- Test environment
- Evaluate the environment in terms of system location and operational conditions to determine the most appropriate reliability test. (Evaluate)
- Testing during development
- Describe the purpose, advantages, and limitations of each of the following types of tests, and use common models to develop test plans, evaluate risks, and interpret test results. (Evaluate)
- Accelerated life tests (e.g., single-stress, multiple-stress, sequential stress, step-stress)
- Discovery testing (e.g., HALT, margin tests, sample size of 1),
- Reliability growth testing (e.g., test, analyze, and fix (TAAF), Duane)
- Software testing (e.g., white-box, black-box, operational profile, and fault-injection)
- Product testing
- Describe the purpose, advantages, and limitations of each of the following types of tests, and use common models to develop product test plans, evaluate risks, and interpret test results. (Evaluate)
- Qualification/demonstration testing (e.g., sequential tests, fixed-length tests)
- Product reliability acceptance testing (PRAT)
- Ongoing reliability testing (e.g., sequential probability ratio test [SPRT])
- Stress screening (e.g., ESS, HASS, burn-in tests)
- Attribute testing (e.g., binomial, hypergeometric)
- Degradation (wear–to-failure) testing
- Case Study/Exercise: Working through a system of their choosing to study failure degradation mechanisms (physics of failure) as well as predict using statistical methods the optimal maintenance periodicity.
Day 5: Maintainability and Availability
- Management strategies
- Planning
- Develop plans for maintainability and availability that support reliability goals and objectives. (Create)
- Maintenance strategies
- Identify the advantages and limitations of various maintenance strategies (e.g., reliability-centered maintenance (RCM), predictive maintenance, repair or replace decision making), and determine which strategy to use in specific situations. (Apply).
- Availability tradeoffs
- Describe various types of availability (e.g., inherent, operational), and the tradeoffs in reliability and maintainability that might be required to achieve availability goals. (Apply)
- Maintenance and testing analysis
- Preventive maintenance (PM) analysis
- Define and use PM tasks, optimum PM intervals, and other elements of this analysis, and identify situations in which PM analysis is not appropriate. (Apply)
- Corrective maintenance analysis
- Describe the elements of corrective maintenance analysis (e.g., fault-isolation time, repair/replace time, skill level, crew hours) and apply them in specific situations. (Apply)
- Non-destructive evaluation
- Describe the types and uses of these tools (e.g., fatigue, delamination, vibration signature analysis) to look for potential defects. (Understand)
- Testability
- Use various testability requirements and methods (e.g., built in tests (BITs), false-alarm rates, diagnostics, error codes, fault tolerance) to achieve reliability goals (Apply)
- Spare parts analysis
- Describe the relationship between spare parts requirements and reliability, maintainability, and availability requirements. Forecast spare parts requirements using field data, production lead time data, inventory and other prediction tools, etc. (Analyze)
Data Collection and Use
-
- Data collection
- Types of data
- Identify and distinguish between various types of data (e.g., attributes vs. variable, discrete vs. continuous, censored vs. complete, univariate vs. multivariate). Select appropriate data types to meet various analysis objectives. (Evaluate)
- Collection methods
- Identify appropriate methods and evaluate the results from surveys, automated tests, automated monitoring and reporting tools, etc., that are used to meet various data analysis objectives. (Evaluate)
- Data management
- Describe key characteristics of a database (e.g., accuracy, completeness, update frequency). Specify the requirements for reliability-driven measurement systems and database plans, including consideration of the data collectors and users, and their functional responsibilities. (Evaluate)
- Data use
- Data summary and reporting
Who Should Attend Certified Reliability Engineer Training Course
Our Certified Reliability Engineer (CRE) course targets professionals who wish to improve their knowledge and abilities. Here are the target audiences:
1. Maintenance and reliability professionals.
2. Operations Managers
3. Engineering Managers
This training covers the body of knowledge (BOK) established by the American Society for Quality (ASQ) for Certified Reliability Engineer (CRE) certification. As a result, participants will gain a thorough understanding of reliability, maintenance technicians, quality technicians, and reliability engineering, as well as how they relate to the company’s success.
For professionals looking to advance their careers, the Certified Reliability Engineer (CRE) Training offers a valuable opportunity. This course is designed to enhance your critical skills, boost productivity, and prevent system failures. Enroll in our program today and take the first step towards professional growth and development!
Enhance Your Career with CRE Training – Join PetroSync Now!
In today’s competitive industry, Certified Reliability Engineer (CRE) certification is a game-changer for professionals looking to advance their careers in reliability, maintenance, and quality management. Join PetroSync’s CRE Training and gain in-depth expertise in reliability principles, risk management, and failure analysis—essential skills to drive operational excellence in your organization.
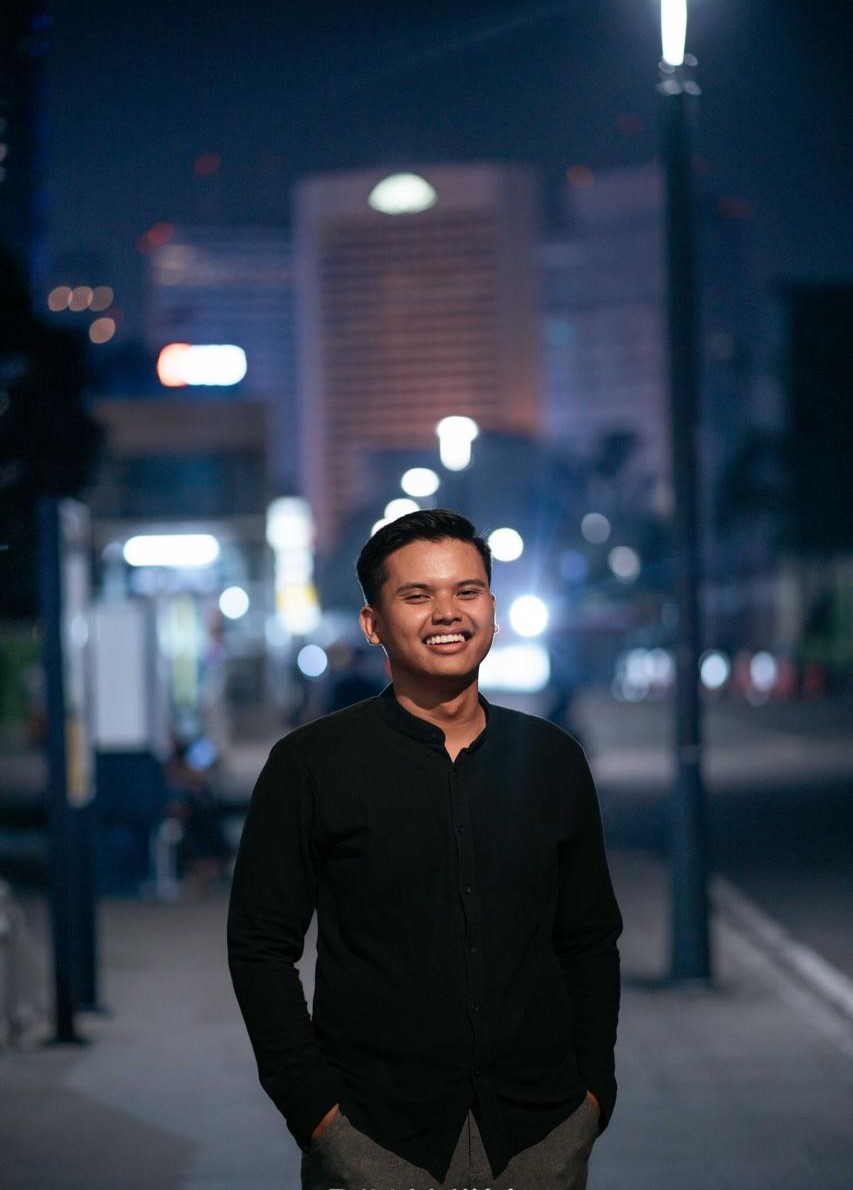
Results-oriented and thorough SEO specialist with extensive experience in conducting keyword research, developing and implementing digital website promotion strategies and plans, managing campaigns to develop company websites in the digital world, excellent knowledge of marketing techniques and principles, and attentive strong attention to detail.