Corrosion monitoring is a crucial process that aids in the identification and assessment of the detrimental impact of corrosion. By utilizing specialized techniques, this monitoring plays a pivotal role in guaranteeing the safety and dependability of structures, equipment, and materials. In this article, we will delve into the significance and methodologies of corrosion monitoring, emphasizing its types and utilities.
What Is Corrosion Monitoring?
Corrosion monitoring involves employing a corrosion meter or various techniques and tools to gather data on corrosion rates (measured in mpy) and provide crucial information for proactive corrosion prevention and protection measures.
Corrosion is a natural process where metals or alloys react with their environment, leading to material degradation. This can result in structural damage, reduced efficiency, and safety risks in different industries.
The purpose of corrosion monitoring is to assess and measure the corrosion rate of a material or its surroundings. By monitoring corrosion, you can make informed decisions about material selection, maintenance schedules, and corrosion control methods.
What Is Corrosion Measured In?
Corrosion is measured in microns per year (µpy), indicating the thickness loss in thousandths of a millimeter per year. The rate depends on environmental factors and the metal’s type and condition. It signifies the extent of corrosion penetration annually in terms of microns.
What Is The Difference between Monitoring and Inspecting?
Monitoring and inspecting are distinct activities that can occur concurrently, but they serve different purposes. Monitoring involves observing and assessing specific areas or parameters of an asset and typically occurs more frequently than inspecting. It focuses on gathering:
- continuous or periodic data to track the performance
- condition, or
- behavior of the monitored area.
Monitoring provides ongoing insights into the selected aspects of the asset, facilitating proactive management and decision-making based on the collected data.
Inspecting, on the other hand, involves a comprehensive evaluation of the entire asset and generally takes place less frequently than monitoring. It entails a careful examination of the entire asset or specific components, aiming to assess:
- its overall condition
- integrity, or
- compliance
Inspections are typically conducted at discrete time points, often following predetermined criteria, standards, or regulations. Specialized tools or techniques may be employed during inspections to assess specific parameters of interest.
What Are Corrosion Monitoring Techniques?
Corrosion monitoring techniques assist in evaluating the rate and extent of corrosion, helping experts to make well-informed choices concerning material choice, maintenance schedule, and corrosion control measures. Two big categories of corrosion monitoring are direct and indirect techniques.
1. Direct Techniques
Direct techniques in corrosion monitoring refer to methods that directly measure the corrosion rates or related factors on the material’s surface. These techniques offer real-time or near-real-time information about the corrosion process. Let’s explore a few commonly used direct techniques in corrosion monitoring:
a. Corrosion Coupons (Intrusive)
Corrosion coupons are standardized test samples used to evaluate how metals or alloys are affected by corrosion in a particular environment. These coupons are small, flat, and usually rectangular in shape. They are made from the same material as the metal being assessed and are exposed to the same conditions as the equipment or structure they represent.
The purpose of using corrosion coupons is to monitor and measure the rate and type of corrosion that occurs in a specific system. By placing these coupons in the field or lab environment, we can get a representative sample of how the material corrodes.
Corrosion coupons are typically installed in a specific location within a system, like a pipeline or a vessel, and left there for a set period, a few weeks or several months.
After the exposure period, the corrosion coupons are removed and analyzed. Inspectors can determine the extent and type of corrosion by measuring parameters like weight loss, surface appearance, or changes in material properties.
b. Electrical Resistance (Intrusive)
In corrosion monitoring, electrical resistance is a technique that measures changes in the electrical resistance of a metal to determine its corrosion rate. This method requires direct contact with the metal surface.
To perform intrusive electrical resistance monitoring, small metal probes or electrodes are inserted into the system or equipment being monitored. These probes are made from the same material as the metal being assessed. Over time, as corrosion occurs, the metal surface changes, causing variations in electrical resistance.
Periodically, the electrical resistance of the probes is measured using specialized equipment. By tracking these resistance changes, we can determine the extent and speed of corrosion. Higher resistance values indicate less corrosion, while lower values suggest a higher corrosion rate.
Intrusive electrical resistance monitoring provides real-time data on corrosion activity, enabling prompt detection of corrosion problems. It is commonly used in applications where continuous monitoring and rapid response to corrosion are crucial, such as pipelines, storage tanks, or critical infrastructure.
c. Inductive Resistance Probes (Intrusive)
Inductive resistance probes are corrosion monitoring devices that measure changes in the electrical impedance of metals to evaluate corrosion rates. Unlike intrusive methods, these probes do not require direct contact with the metal surface.
Inductive resistance probes work based on electromagnetic principles. They consist of a coil that creates a magnetic field around the metal being monitored. As corrosion occurs, the metal’s electrical impedance changes, modifying the magnetic field. The inductive resistance probe detects these changes and translates them into corrosion data.
This monitoring technique is particularly useful when inserting probes directly into the system is impossible or preferable. For instance, it is effective for monitoring the corrosion of external surfaces like pipelines or structures.
Inductive resistance probes offer continuous monitoring, providing real-time detection of corrosion activity. By tracking the changes in electrical impedance, we can evaluate the corrosion rate and severity. Higher impedance values usually indicate lower corrosion rates, while lower values suggest a higher rate of corrosion.
d. Linear Polarization Resistance (Intrusive)
Linear polarization resistance is a corrosion monitoring technique that measures how well a metal resists corrosion. It works by applying a small electrical charge to the metal’s surface and measuring the resulting current. This measurement helps determine the metal’s corrosion rate.
Higher values of polarization resistance indicate lower rates of corrosion, while lower values suggest a higher corrosion rate. This method is widely used in corrosion studies and monitoring systems.
Linear polarization resistance is a non-destructive and straightforward technique that provides real-time corrosion monitoring. It is commonly used in various applications, such as pipelines, storage tanks, and metal structures, to assess the effectiveness of corrosion protection methods and identify any changes in corrosion rates over time.
The advantages of linear polarization resistance include its simplicity, quick measurement time, and continuous monitoring capabilities. However, it is important to note that this technique is best suited for assessing uniform corrosion and may not be as effective for localized or pitting corrosion.
e. Electrochemical Impedance Spectroscopy (Intrusive)
Electrochemical impedance spectroscopy is a corrosion monitoring technique that uses impedance measurements to study how metals corrode. It is an advanced method based on electrochemical principles and provides valuable insights into corrosion processes.
In this technique, a small alternating current is applied to the metal surface at different frequencies. By measuring the resulting electrical response, we obtain an impedance spectrum. This spectrum gives us information about various electrochemical processes happening on the metal surface, such as corrosion reactions and the formation of protective films.
Analyzing the impedance spectrum helps us determine important parameters like corrosion rate, the integrity of protective coatings, and the effectiveness of corrosion inhibitors. It can also detect localized corrosion or pitting.
Electrochemical impedance spectroscopy is a versatile technique that provides both qualitative and quantitative information about corrosion processes. It allows us to understand the complex behavior of metals in corrosive environments.
f. Electrochemical Frequency Modulation (Intrusive)
Electrochemical Frequency Modulation (EFM) is a corrosion monitoring technique that helps us understand how metals corrode. It works by applying a small alternating current to the metal and observing the changes in its electrochemical response.
EFM focuses on the modulation of the current’s frequency, allowing us to determine important factors like the corrosion rate and the type of corrosion occurring. This technique provides quantitative data about the extent of corrosion and can differentiate between different corrosion types, such as uniform corrosion or localized corrosion.
One advantage of EFM is its ability to monitor corrosion in real-time and detect changes in the corrosion rate. It is a non-destructive method suitable for various environments, including aqueous solutions and high-temperature systems.
EFM is commonly used in both research and industrial settings to evaluate the effectiveness of corrosion inhibitors, assess the performance of protective coatings, and gain insights into factors influencing corrosion rates.
g. Harmonic Analysis (Intrusive)
Harmonic analysis is a corrosion monitoring technique that involves studying specific frequency components in a signal to understand how metals corrode. This method analyzes the electrical response of the metal and identifies harmonic frequencies associated with corrosion processes.
By examining the amplitudes and phases of these harmonic components, we can gather valuable information about the corrosion rate and severity. Harmonic analysis helps us detect different types of corrosion, such as localized or pitting corrosion, and enables us to track changes in corrosion behavior over time.
This non-destructive technique can be used in various environments, including water solutions, atmospheric conditions, and industrial settings. It provides insights into the effectiveness of corrosion control measures and helps optimize strategies for preventing corrosion.
In summary, harmonic analysis is a corrosion monitoring method that focuses on specific frequency components to understand how metals corrode. By analyzing these components, we can determine corrosion rates and types. This technique is non-destructive and assists in evaluating and improving corrosion prevention measures.
h. Electrochemical Noise (intrusive)
Electrochemical noise (intrusive) is a corrosion monitoring technique that involves studying the random fluctuations in electrical signals to understand how metals corrode. This method requires direct contact with the metal surface.
To monitor electrochemical noise, electrodes or probes are placed into the system or equipment being observed. These electrodes detect the small electrical signals generated by corrosion processes on the metal surface. By analyzing the random variations in these signals, known as electrochemical noise, we can gather information about the corrosion rate, localized corrosion, and other important corrosion-related factors.
By examining characteristics like signal amplitude, frequency distribution, and duration, we can gain insights into corrosion mechanisms and the effectiveness of corrosion control measures.
Electrochemical noise monitoring is especially valuable for detecting and assessing localized corrosion, which can cause significant damage even with low overall corrosion rates. It provides real-time monitoring capabilities and can be used in different environments, including water solutions, atmospheric conditions, and industrial settings.
i. Zero Resistance Ammetry (intrusive)
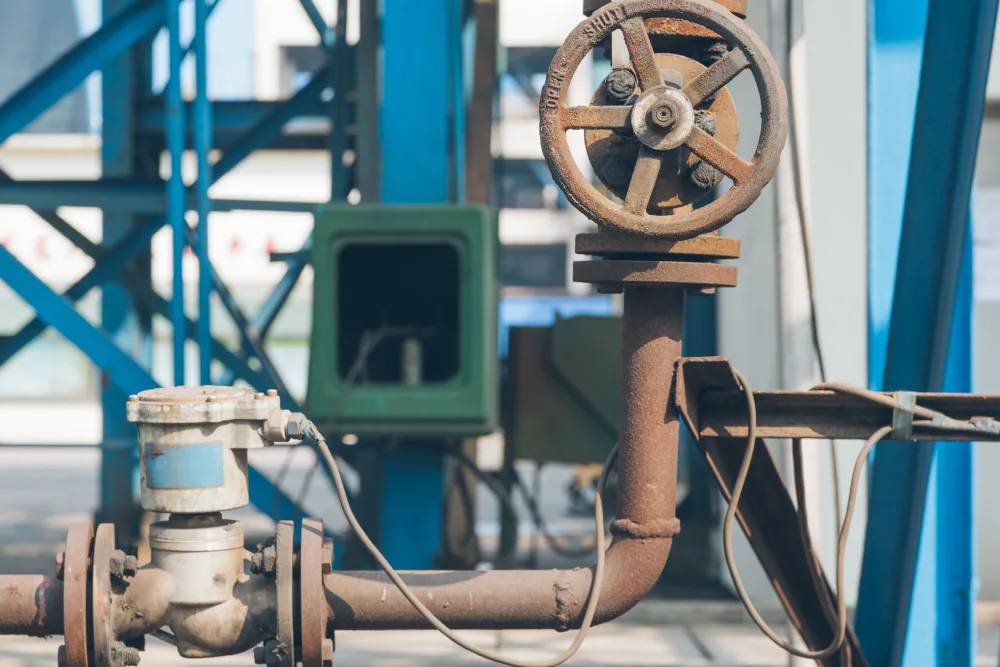
Zero Resistance Ammetry (ZRA) is a corrosion monitoring technique used to measure the immediate corrosion current in metals or alloys. This method works by applying a low resistance to the metal-electrolyte interface.
In ZRA, a small electrical potential is applied to the metal surface, which causes a flow of current. To ensure accurate measurement of the corrosion current, a specialized device called a zero resistance ammeter is used. This device has a very low internal resistance, allowing for precise measurement of the immediate corrosion current.
By measuring the corrosion current using ZRA, we gain important information about the corrosion rate and the effectiveness of corrosion control measures. This technique is especially helpful in situations where rapid changes in corrosion rate need to be monitored, such as when localized corrosion starts or in highly aggressive environments.
ZRA is commonly employed in research and industry settings where accurate and real-time corrosion monitoring is required. It enables continuous monitoring of corrosion behavior and aids in making informed decisions about maintenance, corrosion prevention strategies, and material selection.
j. Potentiodynamic Polarization (intrusive)
Potentiodynamic polarization is a corrosion monitoring technique that assesses the corrosion resistance of metals. It involves measuring the relationship between current and voltage while changing the metal’s potential.
In potentiodynamic polarization, the metal is exposed to different potentials, and the resulting current is recorded. This data helps us understand the metal’s corrosion behavior.
By analyzing the polarization curve, which shows the relationship between current and potential, we can determine important corrosion parameters. These include the corrosion potential, which indicates the metal’s tendency to corrode, and the polarization resistance, which reflects its ability to resist corrosion.
Potentiodynamic polarization allows us to evaluate various corrosion phenomena like general corrosion, pitting, and passivation. It helps identify critical potentials where corrosion is likely to occur and provides insights into the effectiveness of corrosion control measures.
k. Thin Layer Activation and Gamma Radiography (intrusive or non-intrusive)
Thin Layer Activation (TLA) and Gamma Radiography are corrosion monitoring techniques that use radioactive materials to assess the corrosion of materials and their structural integrity.
In Thin Layer Activation, a thin layer of a radioactive substance is applied to the material’s surface. This radioactive material emits radiation that interacts with the material and its corrosion products. By measuring the emitted radiation, we can determine the extent and location of corrosion on the material’s surface.
Gamma Radiography, on the other hand, involves using a gamma ray source to examine the internal structure of the material. Gamma rays can penetrate through the material, and by measuring the intensity of the transmitted gamma rays, we can detect any internal corrosion or degradation.
Both TLA and Gamma Radiography provide valuable insights in corrosion monitoring. TLA helps us understand surface corrosion, while Gamma Radiography allows us to assess internal corrosion or degradation. These techniques are particularly useful when we need to evaluate materials without causing damage or when the structure is complex and hard to access.
l. Electrical Field Signature Method (non-intrusive)
The Electrical Field Signature Method (non-intrusive) is a corrosion monitoring technique that evaluates how metals corrode without directly touching them. Instead, it measures and analyzes the electrical field changes associated with corrosion processes.
In this method, sensors or probes are placed near the metal surface, but they don’t make direct contact. These sensors detect and analyze the electrical field variations caused by corrosion reactions happening on the metal surface.
By studying these electrical field signatures, we can gather important information about the corrosion rate, the type of corrosion occurring, and even localized corrosion. This technique allows for real-time monitoring and provides insights into how the metal is corroding.
The non-intrusive nature of the Electrical Field Signature Method makes it suitable for monitoring large structures or areas where it’s difficult to directly access the metal surface.
m. Acoustic Emission (non-intrusive)
Acoustic Emission (non-intrusive) is a corrosion monitoring technique that assesses the corrosion behavior of materials by listening to the sounds they produce. It is a non-intrusive method, meaning it doesn’t require direct contact with the material.
In Acoustic Emission monitoring, sensors or devices are placed on or near the material’s surface to capture the sounds generated during corrosion. These sounds can be related to activities like cracking, hydrogen release, or material deterioration.
By analyzing the characteristics of these sounds, such as their loudness, frequency, and duration, we can gain valuable information about the corrosion activity, how fast it’s happening, and whether any damage is occurring.
Acoustic Emission is particularly useful for detecting and monitoring localized corrosion or changes happening inside the material. It provides real-time monitoring and can be used with different materials like metals, composites, and coatings.
2. Indirect Techniques
Indirect techniques in corrosion monitoring are methods that indirectly assess the corrosion behavior of materials. Instead of directly measuring corrosion rates or damage, they rely on secondary indicators that provide insights into the corrosion process.
These techniques include measuring factors like electrical resistance, changes in weight or size, surface roughness or color, and alterations in mechanical properties or ultrasonic wave propagation. Some of the indirect techniques of corrosion monitoring are:
a. Corrosion Potential (non-intrusive)
Corrosion Potential (non-intrusive) is a corrosion monitoring technique that helps us understand the probability of corrosion occurring on metal surfaces. It is a non-intrusive method, meaning it doesn’t require direct contact with the material.
The corrosion potential represents the difference in electrical potential between the metal surface and its surrounding environment. It gives us an idea of how likely the metal is to corrode or remain protected. To measure it, we use reference electrodes or other non-contact methods.
By monitoring the corrosion potential over time, we can identify changes that may indicate an increased risk of corrosion or the effectiveness of corrosion prevention measures. If the corrosion potential shifts towards more positive or negative values, it suggests changes in the metal’s corrosion behavior.
b. Hydrogen Flux Monitoring (non-intrusive)
Hydrogen Flux Monitoring (non-intrusive) is a corrosion monitoring technique that helps us understand the presence and behavior of hydrogen gas, which can contribute to corrosion. It is a non-intrusive method, meaning it doesn’t require direct contact with the material.
To monitor hydrogen flux, we place sensors or probes near the material surface to detect and measure the flow of hydrogen gas. These sensors detect how hydrogen moves through the material or is released during corrosion.
By monitoring the hydrogen flux, we gain valuable information about the concentration of hydrogen, its presence, and how it interacts with the material. This information helps us understand the risk of hydrogen-induced corrosion and evaluate the effectiveness of corrosion control measures.
Hydrogen Flux Monitoring is particularly useful for materials that are vulnerable to hydrogen embrittlement or in environments where hydrogen gas is present, like in the oil and gas industry.
This technique assists in making informed decisions about material selection, design considerations, and implementing preventive measures to minimize the impact of hydrogen-induced corrosion.
c. Chemical Analyses
Chemical analyses in corrosion monitoring refer to the process of examining and evaluating the chemical changes that occur in a corroding system.
It involves studying the composition of corrosive solutions, analyzing corrosion by-products, and identifying different chemical substances involved in the corrosion process. Chemical analyses employ various techniques, such as:
d. Corrosion Product Analysis
This method involves examining the nature and properties of the corrosion products formed during corrosion. Techniques like X-ray diffraction and scanning electron microscopy are used to identify and analyze these products.
e. Electrochemical Analysis
This technique measures electrochemical parameters like pH, potential, and ion concentration to understand the corrosive environment’s effect on the material. Methods such as potentiometry and ion chromatography are used for electrochemical analysis.
f. Spectroscopic Analysis
Spectroscopic techniques, including infrared spectroscopy, Raman spectroscopy, and atomic absorption spectroscopy, are employed to identify and quantify specific chemical species or elements present in the corrosive environment.
g. Wet Chemical Analysis
This method involves using chemical reagents and titration techniques to determine the concentration of particular ions or compounds in the corrosive solution. For example, silver nitrate titration is used to measure chloride concentration.
What Are The Main Equipment of Corrosion Monitoring System?
In a corrosion monitoring system, the main equipment includes
1. Corrosion Probes/Sensors
These devices are installed to directly measure corrosion rates in the monitored system. They come in different types such as probes for linear polarization resistance (LPR), electrochemical noise (EN), galvanic corrosion, and corrosion coupons.
2. Data Loggers
These devices collect and store data from the corrosion probes or sensors. They record important parameters like corrosion rate, temperature, humidity, and other environmental conditions.
3. Transmitters
Transmitters send the data collected by the probes or loggers to a central monitoring system. They can be either wired or wireless, depending on the monitoring setup.
4. Central Monitoring System
This system receives and processes the data sent by the probes or loggers. It typically consists of software and hardware components for analyzing, visualizing, and reporting the data. The central monitoring system helps corrosion engineers or operators keep an eye on corrosion trends, detect abnormalities, and make informed decisions about maintenance and prevention strategies.
5. Reference Electrodes
Reference electrodes work together with the corrosion probes or sensors to establish a reference potential for accurate corrosion measurements. Common types include silver/silver chloride (Ag/AgCl) electrodes and saturated calomel electrodes (SCE).
6. Wiring and Cabling
Proper wiring and cabling are necessary for reliable connections between the probes, data loggers, transmitters, and the central monitoring system. These components should be designed to withstand environmental conditions and resist corrosion.
7. Power Supply
Corrosion monitoring systems need a stable power source to operate. This can involve batteries, AC power sources, or a combination of both, depending on the specific setup.
8. Ancillary Equipment
Additional equipment may be required based on the application and needs. This can include weatherproof enclosures for outdoor installations, mounting brackets or clamps to secure the probes, calibration standards for periodic sensor calibration, and protective coatings or coating coupons for reference purposes.
It’s important to consider that the equipment used in a corrosion monitoring system can vary depending on the industry, application, and level of detail needed for corrosion analysis. Consulting with corrosion experts or specialized suppliers can help determine the most suitable equipment for a specific monitoring project.
Why Is Corrosion Monitoring Important?
Monitoring corrosion holds significant importance for the following reasons:
1. Preservation of Assets
Monitoring corrosion helps maintain the structural integrity of various assets, such as structures, equipment, and materials. By promptly identifying and addressing corrosion issues, we can prevent major failures and ensure the longevity of our assets.
2. Ensuring Safety
Corrosion-related failures can pose serious safety hazards, particularly in industries like oil and gas, transportation, and infrastructure. Regular corrosion monitoring allows us to proactively identify potential risks and take necessary measures to ensure a safe working environment.
3. Cost-Efficiency
Corrosion can lead to costly repairs, replacements, and downtime. Through vigilant corrosion monitoring, we can schedule maintenance activities more efficiently, implement appropriate corrosion control measures, and ultimately save costs associated with extensive repairs and asset replacements.
4. Optimizing Performance
Corrosion negatively impacts the performance and efficiency of equipment and systems. By monitoring corrosion levels, we can detect early signs of degradation and take corrective actions, whether through adjustments, repairs, or replacements, to maintain optimal performance.
5. Regulatory Compliance
Many industries have regulations and standards in place to ensure operational safety and integrity. By actively monitoring corrosion, we can demonstrate compliance with these regulations, ensuring that our operations meet the required industry standards.
6. Environmental Protection
Corrosion can result in leaks or spills of hazardous materials, posing risks to the environment. Through diligent corrosion monitoring, we can identify potential leakage sources, prevent environmental contamination, and minimize the impact on surrounding ecosystems.
In summary, corrosion monitoring plays a vital role in safeguarding asset integrity, ensuring safety, reducing costs, optimizing performance, meeting regulatory requirements, and protecting the environment. By proactively addressing corrosion-related issues, we promote efficient and sustainable operations while prolonging the lifespan of our valuable assets.
Monitoring corrosion is an important task for piping inspectors. It is vital for you to learn the correct methods for monitoring corrosion. By understanding the right way to monitor corrosion, you can accurately assess pipe conditions, detect problems early, and take prompt maintenance actions.
Monitoring corrosion is a key aspect highlighted in API 570. It provides guidelines for effectively monitoring corrosion, stressing regular inspections and proper techniques to assess its extent and rate. To become a skilled piping inspector and master corrosion, including monitoring, it’s highly recommended that you join PetroSync’s API 570 course.
Our specialized program covers the comprehensive requirements of API 570. You will gain in-depth knowledge of corrosion monitoring techniques, learning how to effectively assess and manage it in piping systems. By enrolling, you can enhance your skills, deepen your understanding of corrosion mechanisms, and develop expertise in monitoring strategies.
Join the API 570 training by PetroSync and stay updated with industry best practices with PetroSync!
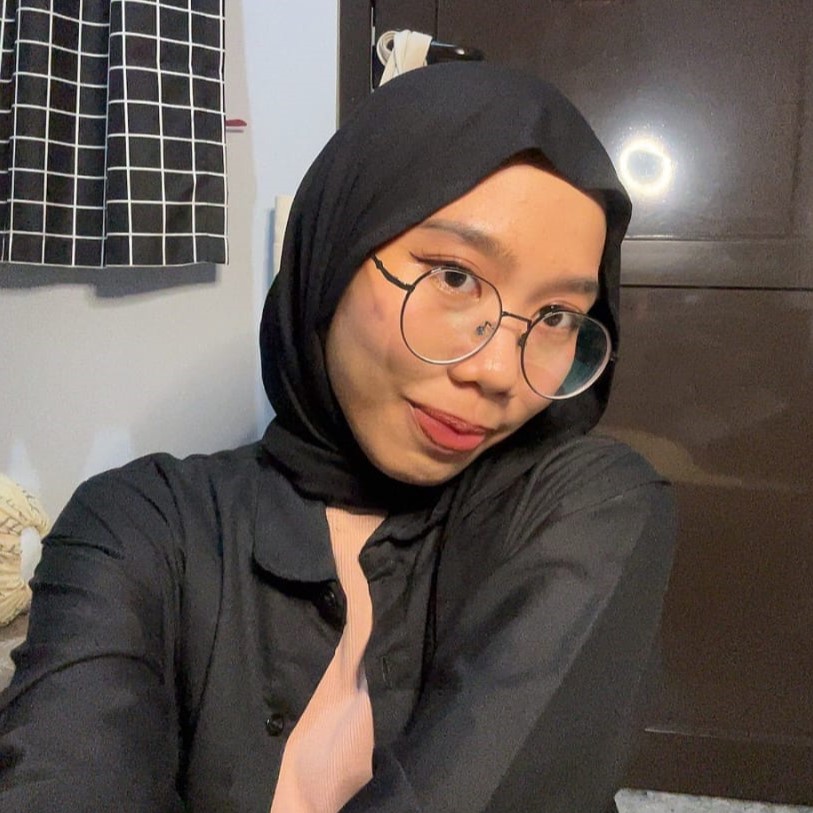
SEO specialist by day, fact-checker by night. An avid reader and content writer dedicated to delivering accurate and engaging articles through research and credible sources.