Encountering challenges during drilling is common in the industry, which is why thorough preparation is crucial. Factors like complex geology and equipment issues can create obstacles during operations. This guide explores 11 common drilling challenges and offers practical solutions to overcome them. By understanding and preparing for these hurdles, professionals can improve efficiency, safety, and overall success in drilling projects.
Mechanical Problems
Mechanical problems in drilling refer to issues or malfunctions with the equipment or machinery used in the drilling process. These problems can arise from various reasons such as worn-out parts, faulty components, or improper maintenance. When mechanical problems occur, they can disrupt the drilling operation, causing delays and potentially increasing costs.
1. Hole Deviation
Hole deviation happens when the drilled hole veers off course from the intended path. This can occur due to factors like uneven rock formations or improper alignment of the drilling equipment. When the hole deviates, it may not reach the desired target depth or location, causing inefficiency and potentially requiring corrective measures to realign the drilling trajectory.
2. Pipe Failure
Pipe failure refers to the malfunction or damage of the pipes used in the drilling process. Pipes may fail due to factors such as corrosion, excessive pressure, or manufacturing defects. When pipes fail, it can disrupt the drilling operation, leading to downtime for repairs or replacements. Additionally, pipe failure can result in safety hazards and environmental risks if not addressed promptly and effectively.
Wellbore Problems
Wellbore problems in drilling refer to challenges or complications encountered while drilling the wellbore, which is the hole drilled into the earth to extract oil, gas, or other resources. These problems can arise from various factors such as geological formations, fluid properties, or equipment limitations.
3. Borehole Instability
Borehole instability occurs when the walls of the drilled hole become unstable or prone to collapse. This can happen due to various reasons such as changes in formation pressure, the presence of weak or fractured rocks, or inadequate drilling fluid properties. When borehole instability occurs, it can pose risks to the drilling operation by causing hole enlargement, formation of cuttings or debris, and even equipment getting stuck.
Mitigating borehole instability often involves proper selection and maintenance of drilling fluids, the use of casing or liners to support unstable sections, and careful monitoring of drilling parameters to detect signs of instability early on.
4. Formation Damage
Formation damage refers to the impairment or alteration of the reservoir rock surrounding the wellbore during drilling operations. This damage can occur due to factors such as invasion of drilling fluids into the formation, mechanical stress from drilling activities, or chemical reactions between fluids and rock minerals.
Formation damage can reduce the permeability of the reservoir rock, impede the flow of hydrocarbons, and ultimately decrease well productivity. Preventing formation damage involves employing techniques such as the proper selection of drilling fluids, controlling drilling parameters to minimize formation stress, and implementing effective wellbore cleanup procedures after drilling.
5. Lost Circulation
Lost circulation happens when drilling fluid escapes into permeable formations instead of circulating back to the surface, resulting in a loss of fluid from the wellbore. This can occur in formations with fractures, vugs, or other pathways for fluid escape.
Lost circulation can lead to increased costs due to the need for additional drilling fluid, reduced drilling efficiency, and potential well control issues. Managing lost circulation involves using specialized drilling fluids or additives designed to seal off loss zones, implementing techniques such as wellbore strengthening, and adjusting drilling parameters to minimize fluid loss.
6. Pipe Sticking
Pipe sticking occurs when the drill string (the assembly of drill pipe and other tools) becomes trapped or adheres to the walls of the wellbore, preventing further movement or extraction. This can happen due to factors such as differential pressure, wellbore geometry, or mechanical obstructions.
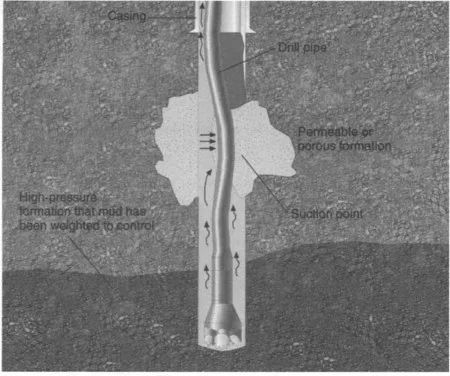
Pipe sticking can cause downtime, equipment damage, and even necessitate costly fishing operations to retrieve stuck components. Preventing pipe sticking involves careful monitoring of drilling parameters, maintaining proper wellbore conditions to minimize friction, and employing techniques such as lubrication or jarring to free stuck pipes.
Mud Problems
Mud problems in drilling refer to challenges or issues related to the drilling mud, also known as drilling fluid, used during the drilling process. Drilling mud serves several purposes, including cooling and lubricating the drill bit, carrying rock cuttings to the surface, and providing pressure control in the wellbore.
However, various problems can arise with the drilling mud, such as changes in viscosity, contamination, or loss of fluid properties. These mud problems can affect drilling efficiency, wellbore stability, and overall drilling success. Managing mud problems effectively is crucial for maintaining safe and efficient drilling operations.
7. Mud Contamination
Mud contamination occurs when unwanted substances or materials mix with the drilling mud, affecting its properties and performance. Contaminants can include foreign solids, chemicals, or fluids from the formation being drilled.
Contaminated mud can lead to issues such as reduced lubrication effectiveness, increased viscosity, or impaired cuttings transport. This can result in difficulties in maintaining well control, increased wear on drilling equipment, and compromised wellbore integrity.
Preventing mud contamination involves proper storage and handling of drilling materials, monitoring drilling fluid properties regularly, and implementing filtration or treatment processes to remove contaminants.
8. Poor Hole Cleaning
Poor hole cleaning refers to insufficient removal of drilled cuttings and debris from the wellbore during drilling operations. When the drilling mud fails to effectively carry cuttings to the surface, they can settle in the wellbore, obstructing further drilling progress and potentially causing wellbore instability.
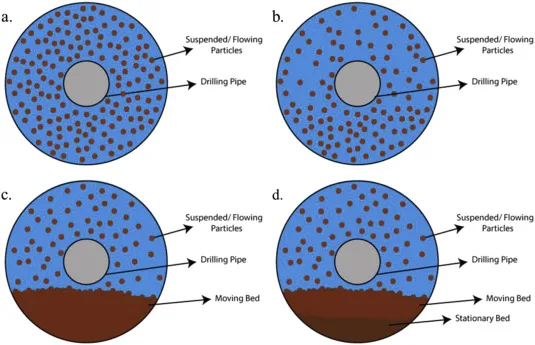
Poor hole cleaning can result from factors such as inadequate fluid velocity, improper mud rheology, or formation characteristics. It can lead to increased drilling time, higher drilling costs, and risks of equipment damage or stuck pipe. Improving hole cleaning involves optimizing drilling fluid properties, adjusting drilling parameters such as flow rate and circulation rate, and using specialized tools or techniques to enhance cuttings transport to the surface.
Other Drilling Problems
Aside from mechanical, wellbore, and mud problems, some other drilling problems may arise during the drilling activity are as follow.
9. Equipment and Personnel-related Problems
Equipment and personnel-related problems in drilling encompass issues stemming from both the machinery used and the people operating it. Equipment problems can include mechanical failures, malfunctions, or shortages of essential tools and parts. Personnel-related challenges may involve inadequate training, lack of experience, or safety incidents.
All of the mentioned problems can disrupt drilling operations, lead to downtime, and pose risks to safety and efficiency. To address equipment and personnel-related challenges, it’s essential to ensure regular maintenance of equipment, provide comprehensive personnel training, enforce safety protocols, and maintain effective communication among team members.
10. H2S-bearing Zones
H2S-bearing zones refer to geological formations containing hydrogen sulfide gas, a highly toxic and corrosive substance commonly encountered in oil and gas drilling. Drilling through H2S-bearing zones poses significant safety risks to personnel and equipment due to the potential for gas releases and exposure.
Additionally, H2S can corrode drilling equipment, leading to damage and failures. Effective management of H2S-bearing zones involves implementing safety measures such as gas detection systems, proper ventilation, personal protective equipment (PPE), and specialized drilling procedures to minimize exposure and mitigate risks.
11. Shallow Gas Zones
Shallow gas zones are geological formations containing natural gas found relatively close to the surface. Drilling through shallow gas zones presents several challenges, including the risk of gas kicks, blowouts, and formation instability. Gas kicks occur when natural gas flows uncontrollably into the wellbore, posing safety hazards and potential well control issues.
Blowouts can result from the uncontrolled release of gas and formation fluids, leading to equipment damage, environmental damage, and safety risks. Managing shallow gas zones requires thorough geological analysis, well planning, and implementation of well control measures such as blowout preventers (BOPs), mud weight control, and proper casing and cementing practices to prevent gas influx and maintain well integrity.
In conclusion, addressing drilling challenges requires proper preparation and training. PetroSync offers comprehensive drilling training programs such as HPHT training, Well Log training, and Stuck Pipe prevention training to equip professionals with the necessary knowledge and skills to tackle these challenges effectively.
By investing in quality training, you can enhance your expertise and confidence, leading to improved performance, safety, and success in drilling operations. With PetroSync’s training, you can navigate the complexities of drilling with greater efficiency and proficiency, ultimately driving better outcomes for your projects and organizations.
Credit header image: kherkhergarcia
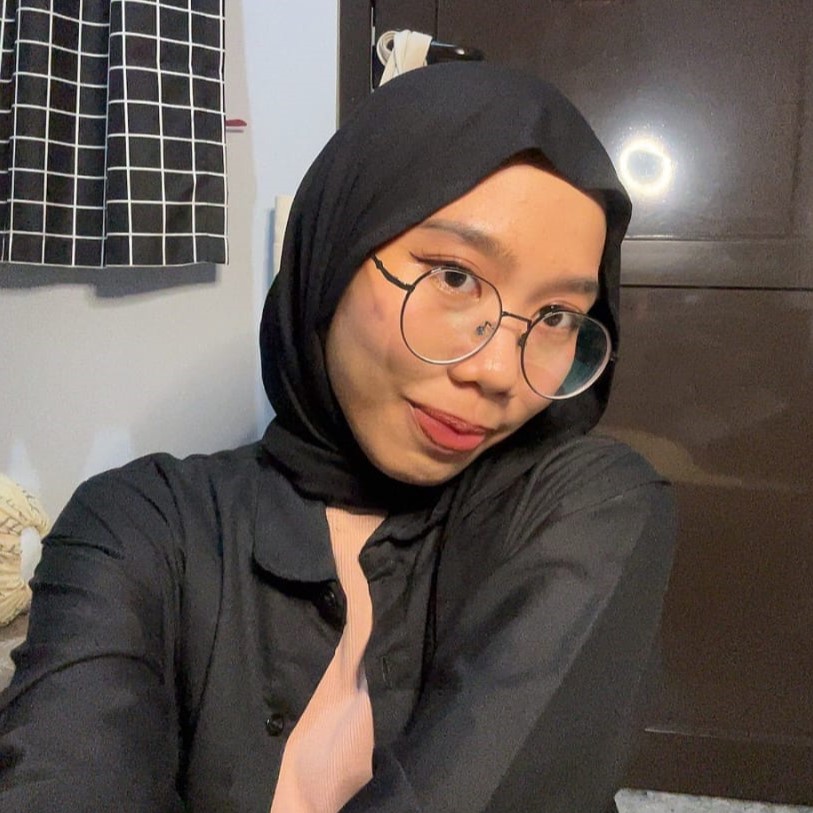
SEO specialist by day, fact-checker by night. An avid reader and content writer dedicated to delivering accurate and engaging articles through research and credible sources.