Ensuring product quality and structural integrity has never been more critical across industries like aerospace, automotive, and manufacturing. Surface cracks and defects, if left undetected, can lead to costly failures, operational downtime, and even safety hazards.
This is where Dye Penetrant Testing (DPT) steps in as a reliable, cost-effective non-destructive testing method. Before exploring how dye penetrant testing works and why it remains essential in modern industries, let’s understand the basics behind this important inspection process.
What is Dye Penetrant Testing?
Dye Penetrant Testing (DPT), sometimes called Liquid Penetrant Testing (LPT), is a non-destructive evaluation (NDE) technique used to locate surface-breaking defects in non-porous materials such as metals, ceramics, and plastics. The method relies on the principle of capillary action, where a special liquid penetrates surface flaws, making them visible after developing.
DPT has evolved since its early adoption in the 1940s during wartime aircraft inspections. Today, it continues to provide manufacturers and engineers with an effective tool for ensuring component reliability and safety.
How Dye Penetrant Testing Works: Step-by-Step Procedure
Dye penetrant inspection is a systematic process involving several critical steps:
1. Surface Preparation
The test surface must be thoroughly cleaned to remove any contaminants that could block penetrant entry. Cleaning methods include solvent wiping, detergent scrubbing, or abrasive blasting.
2. Application of Penetrant
A visible or fluorescent dye penetrant is evenly applied to the surface to seep into any present defects.
3. Dwell Time
The penetrant remains on the surface for a set period (typically 5–30 minutes) to allow it to enter any flaws fully.
4. Removal of Excess Penetrant
Excess penetrant is gently removed without flushing penetrant out of the defects.
5. Application of Developer
A developer draws the trapped penetrant back to the surface, highlighting any flaws through visible indications.
6. Inspection
The inspector examines the surface under suitable lighting—white light for visible dyes, UV light for fluorescent types.
7. Post-Inspection Cleaning
The component is cleaned again to remove all testing residues before returning to service.
Types of Dye Penetrant Testing
Dye penetrant testing is typically categorized into two types based on the type of dye used:
1. Visible Dye Penetrant Testing
- Uses a red dye that can be easily seen under white light.
- Suitable for general industrial applications where basic sensitivity is acceptable.
2. Fluorescent Dye Penetrant Testing
- Involves a dye that fluoresces under ultraviolet light, enhancing detection sensitivity.
- Preferred in critical industries like aerospace and nuclear energy.
Choosing between the two depends on factors such as defect size sensitivity, environmental conditions, and inspection requirements.
Applications of Dye Penetrant Testing
Dye penetrant testing is indispensable in several industries:
- Aerospace: Inspecting fuselage skins, landing gears, and turbine blades.
- Automotive: Verifying the integrity of axles, engine blocks, and wheels.
- Power Generation: Checking boiler parts, piping systems, and turbine components.
- Manufacturing and Construction: Ensuring the quality of welds, castings, and structural parts.
According to NDT.net, consistent application of non-destructive testing, including DPT, has resulted in a 20–30% reduction in structural failures across industries.
Advantages and Limitations of Dye Penetrant Testing
1. Advantages
- Cost-effective: Minimal equipment and material costs.
- High sensitivity: Excellent for detecting small surface flaws.
- Easy to apply: Requires basic equipment and straightforward training.
- Versatile: Works on metals, plastics, and ceramics.
2. Limitations
- Surface-only: Cannot detect internal defects below the surface.
- Surface preparation critical: Contaminants can mask flaws.
- Material restrictions: Ineffective on porous materials.
- Environmental concerns: Proper disposal of chemicals is necessary.
By understanding these strengths and constraints, you can select the right method for each inspection need.
Standards and Best Practices
Reliable dye penetrant testing requires strict adherence to international standards:
- ASTM E1417/E1417M: Standard Practice for Liquid Penetrant Testing.
- ISO 3452: International standard for penetrant testing.
Personnel involved in DPT typically attain certifications like ASNT SNT-TC-1A or ISO 9712, ensuring their competency through structured training and examination.
Certified inspectors help maintain inspection integrity and contribute to safer, higher-quality production outcomes.
Why Mastery of Dye Penetrant Testing Matters for Business Growth
In today’s highly competitive landscape, businesses that invest in rigorous inspection practices position themselves ahead of the curve. Mastery of techniques like dye penetrant testing not only ensures regulatory compliance but also drives tangible business benefits.
Research published by ResearchGate found that manufacturers implementing strong non-destructive testing strategies reported:
- 35% fewer product recalls
- 22% faster time-to-market
compared to companies with weaker quality control measures.
Investing in skill development—both individually and organizationally—translates directly into better products, higher customer trust, and stronger market performance.
Join PetroSync Training to Elevate Your Expertise in Non-Destructive Testing
In a rapidly evolving industry landscape, staying ahead requires more than experience alone—it demands a commitment to continuous learning and professional development.
Employers today are looking for professionals who not only understand inspection techniques but also demonstrate the ability to apply global best practices with confidence.
At PetroSync, we believe that investing in knowledge is the foundation for long-term career growth. We design our specialized training programs to bridge the gap between theory and practical application, giving participants real-world insights into non-destructive testing (NDT) practices.
Through our training, you will not only refine your technical skills but also gain certifications that are highly respected across industries. This can open new career opportunities, enhance your credibility, and empower you to contribute more significantly to your organization’s quality and safety objectives.
If you aspire to build a strong professional profile and stay competitive in today’s demanding environment, specialized training is a step in the right direction. Join PetroSync Training today and take your expertise to the next level—where opportunity meets preparation.
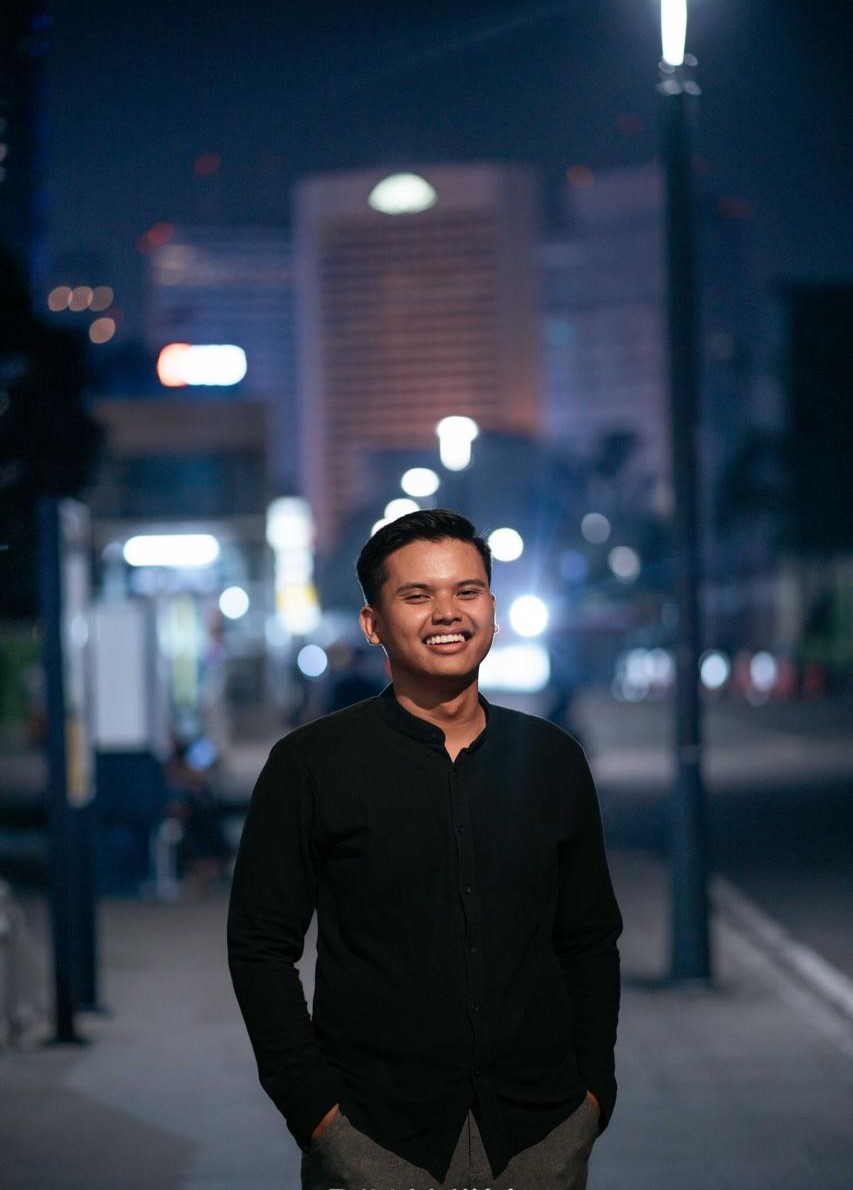
Results-oriented and thorough SEO specialist with extensive experience in conducting keyword research, developing and implementing digital website promotion strategies and plans, managing campaigns to develop company websites in the digital world, excellent knowledge of marketing techniques and principles, and attentive strong attention to detail.