In the rapidly evolving and safety-critical sectors of oil and gas, petrochemicals, and energy, the demand for dependable inspection processes has reached new heights. Maintaining the integrity and safety of structures, machines, and materials is vital for smooth operations, avoiding accidents, and following industry regulations.
Non-Destructive Testing (NDT) has evolved as a breakthrough approach of evaluating material quality that does not cause damage. This approach has become the norm in industrial inspection. In this talk, we will go over the fundamentals of NDT, its many methodologies and applications, and its importance in current manufacturing operations.
What Is NDT?
Non-Destructive Testing (NDT) is a set of inspection techniques used to assess the qualities of a material, component, or system without causing damage. This technique is critical in businesses where safety, dependability, and quality are paramount concerns. Using physical concepts such as electromagnetic radiation, sound waves, and magnetic fields.
NDT enables inspectors to discover faults such as cracks, corrosion, and vacancies without disturbing operations or compromising the integrity of the tested component. Ultrasonic testing, radiographic testing, magnetic particle testing, dye penetrant testing, and eddy current testing are all types of NDT methods.
Each method is useful for a certain purpose, depending on the material under inspection and the type of defect sought. Ultrasonic testing, for example, detects internal faults using high-frequency sound waves, whereas radiographic testing captures images of a structure’s interior using X-rays or gamma rays.
NDT has become an essential aspect of asset integrity management, especially in high-risk industries like oil and gas, where errors can have disastrous implications.
What Are NDT Qualifications?
Inspectors must have the necessary qualifications and certificates to efficiently perform NDT. These certificates ensure that experts have the requisite technical knowledge and hands-on abilities to correctly conduct NDT techniques and interpret the results.
NDT personnel certificates are usually divided into three levels:
1. Level I:
Technicians at this level are trained to carry out specific NDT tasks under the guidance of higher-level inspectors. They follow established procedures and may assist with equipment setup and basic tests.
2. Level II:
Level II inspectors are more experienced technicians who can set up and calibrate equipment, run tests, and assess results independently. They can also oversee Level I professionals and should be able to handle more difficult testing scenarios.
3. Level III:
Level III inspectors are the most qualified, able to create NDT procedures, evaluate new testing methods, and provide technical oversight. They frequently perform administrative duties and supervise the certification of Level I and II inspectors
We issue certifications based on an individual’s training hours, exam results, and practical experience, following certification criteria defined by internationally recognized standards such as ISO 9712 and ASNT (American Society of Nondestructive Testing).
Non-Destructive Testing (NDT): Definition, Methods, & Applications
-
Definition:
NDT is a collection of testing processes used to inspect and analyze the physical qualities of materials, components, or systems without changing or destroying them. This inspection aims to detect fractures, voids, corrosion, and other flaws that could threaten structural integrity or operation.
-
Methods:
From ultrasonic testing to radiographic analysis, NDT offers a diverse range of inspection techniques tailored to specific applications and sectors.
-
Applications:
NDT offers a wide range of applications, including as ensuring pipeline safety in oil and gas, examining aircraft components in aviation, and determining the longevity of construction materials.
What Are Non-Destructive Testing Methods?
NDT employs a variety of techniques to ensure accurate inspection. Some of the most commonly used approaches are:
-
Ultrasonic Testing (UT):
Uses high-frequency sound waves to detect inner flaws and calculate material thickness.
-
Radiographic Testing (RT):
X-rays or gamma radiation are used to analyze the internal structure of materials.
-
Magnetic Particle Testing (MPT):
Detects surface and near-surface discontinuities in ferromagnetic materials via magnetic fields.
-
Liquid Penetrant Testing (LPT):
Detects surface-breaking flaws using a penetrant fluid.
-
Eddy Current Testing (ECT):
Uses electromagnetic induction to detect surface and subsurface faults in conductive materials.
-
Visual Testing (VT):
The simplest method, which relies on the inspector’s eye and basic instruments to detect flaws.
Each of these techniques is selected based on the substance being tested, the sort of problem being investigated, and the testing conditions.
How Does NDT Work?
NDT’s functionality is predicated on its ability to reveal hidden flaws utilizing physics-based principles. As an example :
-
Detection Process:
Ultrasonic and radiographic testing procedures rely on energy waves to penetrate materials and reflect signals that reveal faults or abnormalities.
-
Data Interpretation:
Results are captured using tools like as scanners or imaging devices, which are subsequently evaluated by professional technicians.
-
Non-Destructive Analysis:
Unlike destructive testing, which jeopardizes material integrity, NDT assures that the tested material stays intact and ready for immediate use.
NDT’s success is greatly dependent on the technician’s experience and the precision of the tools used in the process.
What Are the Advantages of Using NDT?
Non-Destructive Testing has various features that make it an indispensable tool across sectors.
-
Safety Assurance:
Detects faults before they become dangerous, hence ensuring workplace safety.
-
Cost Efficiency:
Equipment failures and downtime can be reduced by fixing issues in advance.
-
Preservation of Materials:
Unlike destructive testing, NDT ensures that components remain intact and operational after examination.
-
Wide Applicability:
It works with a wide range of materials, including metals, composites, and polymers.
-
High Accuracy:
Advanced processes offer thorough and exact information about material properties.
Where Is Non-Destructive Testing Applied To?
NDT has a wide range of applications in the following industries:
-
Oil and Gas:
Inspects pipelines, pressure vessels, and storage tanks to avoid leaks and breakdowns.
-
Aerospace:
Ensures the structural integrity of aircraft components and engines.
-
Construction:
Verifies the quality of bridge and building materials such as steel, concrete, and welds.
-
Power Generation:
monitors the condition of turbines, boilers, and other important equipment.
-
Manufacturing:
Ensures product quality during manufacturing and assembly.
-
Transportation:
Inspects railroad rails, vehicles, and infrastructure to ensure safety and reliability.
These applications highlight the vital role that NDT plays in assuring operational safety and efficiency across several industries.
What Are the Standards of Practice Used for Non-Destructive Testing (NDT)?
To assure uniformity, reliability, and safety, NDT methods are governed by international standards.
-
ISO 9712:
Outlines the credentials and certifications required for experts who undertake Non-Destructive Testing (NDT).
-
ASME Boiler and Pressure Vessel Code:
Defines standardized methods for several NDT techniques.
ASTM Standards:
Inspection of important infrastructure in the oil and gas industry, including pressure vessels, pipelines, and storage tanks.
API 510, 570, and 653:
Adherence to these criteria ensures that NDT techniques meet worldwide safety and quality requirements.
Join Petrosync’s Comprehensive Non-Destructive Testing (NDT) Training and Elevate Your Expertise!
Are you looking to enhance your NDT abilities and further your career in the oil and gas, petrochemical, or energy industries? Petrosync‘s comprehensive NDT training programs are intended to offer professionals with in-depth knowledge and hands-on experience. Our training covers the latest recent NDT methodology and technology.
As well as practical applications in real-world scenarios and compliance with industry norms and laws. Industry professionals deliver our courses, tailoring them to meet the needs of engineers, technicians, and managers aiming to excel in NDT procedures. Don’t pass up this opportunity to learn about cutting-edge Non-Destructive Testing.
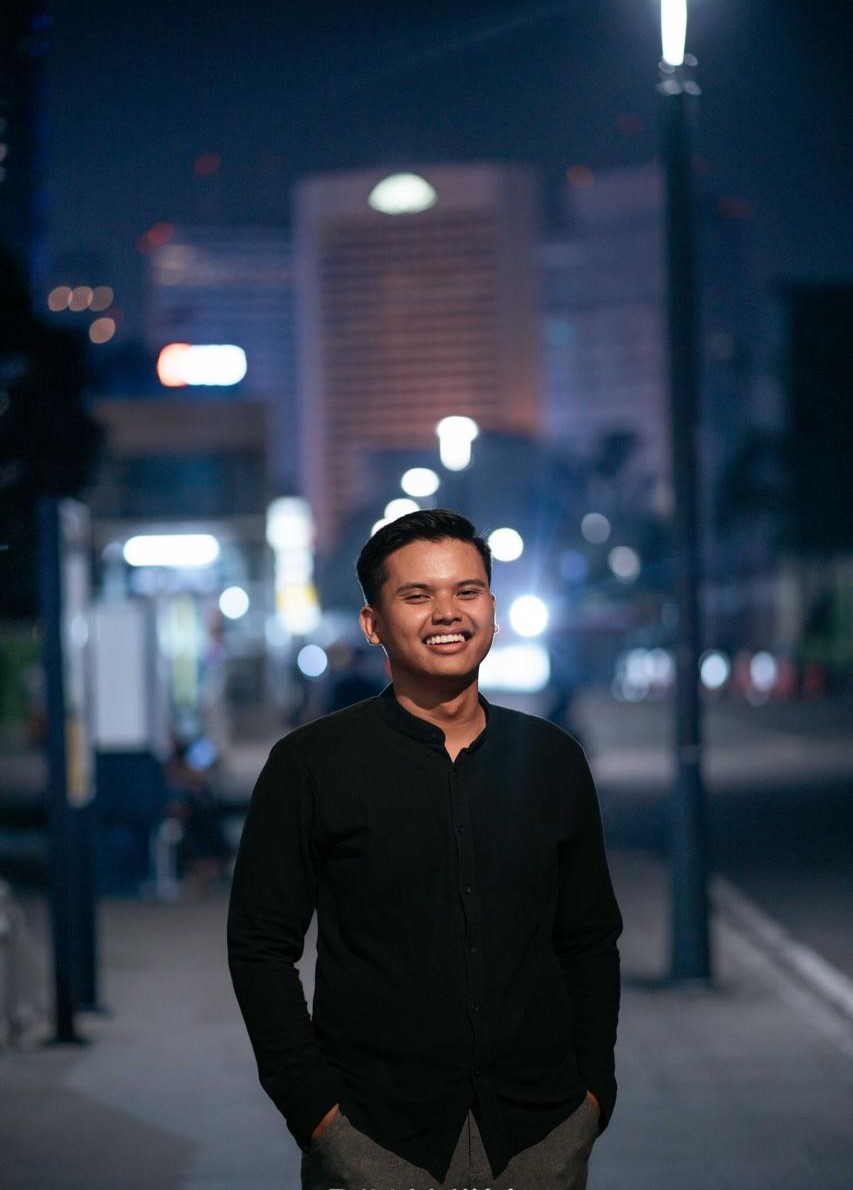
Results-oriented and thorough SEO specialist with extensive experience in conducting keyword research, developing and implementing digital website promotion strategies and plans, managing campaigns to develop company websites in the digital world, excellent knowledge of marketing techniques and principles, and attentive strong attention to detail.