In the world of materials and structures, corrosion poses a significant threat, silently causing metals to deteriorate over time. This article aims to simplify the concept of corrosion, offering clear insights into its types, real-world examples, and, most importantly, preventive measures.
Whether you work in an industry susceptible to corrosion challenges or are simply curious about the processes that can harm metal integrity, this exploration will provide a comprehensive understanding. Join us as we delve into the complexities of corrosion, unravel its nuances, and discover practical strategies to guard against its corrosive impact.
What Is Corrosion?
Corrosion is a natural process that occurs when a refined metal is naturally converted to a more stable form, such as its oxide, hydroxide, or sulphide state. This leads to the gradual deterioration of the material due to reactions with elements like moisture, air, or chemicals, forming rust or other corrosion products.
Over time, this can weaken the metal, affecting its structural integrity and potentially causing damage or failure. Preventive measures, such as protective coatings or regular maintenance, are commonly employed to mitigate the impact of corrosion and extend the lifespan of metal structures.
Does Corrosion Mean Rusting?
Yes, corrosion often involves rusting, and it’s important to note that corrosion includes rust. Corrosion is a broader term that encompasses various processes where metals gradually break down due to reactions with their environment. Rusting specifically refers to the corrosion of iron and its alloys when they react with oxygen and moisture, forming a reddish-brown substance. In summary, while rusting is a type of corrosion, corrosion itself includes a range of processes beyond just the formation of rust.
What Causes of Corrosion?
Corrosion occurs when metals interact with environmental factors, leading to their gradual deterioration. Exposure to moisture, especially in the form of rain or high humidity, triggers chemical reactions that result in the formation of corrosion products like rust. Additionally, contact with air, specifically oxygen, causes metals, particularly iron and steel, to undergo oxidation, weakening their structure over time.
Chemical exposure is another significant cause of corrosion. When metals encounter substances like acids or salts, chemical reactions expedite the corrosion process. The specific reactions depend on the type of metal and the nature of the chemical involved.
Environmental pollutants, including industrial emissions or airborne contaminants, contribute to corrosion by accelerating corrosive reactions on metal surfaces, especially in urban or industrial areas.
Salt exposure is a prominent cause, prevalent in coastal regions or winter climates where de-icing salts are used on roads. Salt enhances corrosion by promoting the formation of more aggressive corrosion products.
The proximity of different metals in an environment can induce galvanic corrosion. When dissimilar metals are close, an electrochemical reaction occurs, accelerating the corrosion of the less noble metal.
To counteract these corrosion causes, implementing preventive measures such as protective coatings, regular maintenance, and selecting materials suited to the environment is crucial.
What Are The 3 Types of Corrosion?
Three of the most common types of corrosion are general attack corrosion, localised corrosion, and galvanic corrosion.
1. General Attack Corrosion
General Attack Corrosion is a common form of corrosion that uniformly deteriorates metals across their exposed surfaces and attacks the entire surface of a metal structure. This occurs due to chemical reactions with the surrounding environment, causing the metal to gradually wear away.
It’s a widespread and predictable type of corrosion that can affect various metals when exposed to corrosive elements like moisture or certain chemicals. Preventive measures, such as protective coatings, are often employed to mitigate general attack corrosion and preserve the integrity of metal structures.
2. Localised Corrosion
Localized corrosion is a specific type of corrosion that occurs in concentrated areas on a metal surface, in which there is an intense attack at localized sites on the metal surface, rather than uniformly across the entire surface. In this process, certain spots on the metal are more prone to corrosion, creating small, distinct areas of damage.
Common forms of localized corrosion include pitting corrosion, where small pits or holes form, and crevice corrosion, which occurs in confined spaces between surfaces. This type of corrosion can lead to localized weakening of the metal and, if not addressed, may result in structural issues over time.
3. Galvanic Corrosion
Galvanic corrosion occurs when two dissimilar metals are immersed in a conductive solution and are electrically connected. In this process, one metal acts as the anode (where corrosion occurs), and the other acts as the cathode (where a protective reaction takes place).
The flow of electrons between the metals leads to the deterioration of the anode, making it susceptible to corrosion. This phenomenon is common in mixed-metal structures and requires preventive measures, such as insulation or protective coatings, to mitigate the effects of galvanic corrosion.
4. Stress Corrosion Cracking (SCC)
Stress Corrosion Cracking (SCC) is a type of corrosion-related damage characterized by the growth of cracks due to the simultaneous action of stress (nominally static and tensile) and a reactive environment.
Unlike other forms of corrosion, SCC often happens in specific conditions where a combination of stress and corrosive elements leads to cracks in the material. This phenomenon can result in the unexpected failure of the metal, making it a critical concern in industries where materials are subjected to both stress and corrosive environments. Preventive measures, such as material selection and stress management, are crucial in minimizing the risk of Stress Corrosion Cracking.
5. Intergranular Corrosion
Intergranular corrosion is a type of corrosion that occurs along the boundaries between the grains of a metal—an attack that occurs at the grain boundaries of a metal or alloy due to the precipitation of the secondary phase.
In simpler terms, it’s the deterioration of metal at the microscopic level, specifically where the grains meet. This type of corrosion can weaken the metal structure, leading to potential issues such as cracking or failure. Preventive measures, like using corrosion-resistant alloys or controlling the metal’s environment, are often employed to mitigate the risk of intergranular corrosion and ensure the longevity of the material.
6. Crevice Corrosion
Crevice corrosion is a type of corrosion that occurs as a localized attack on a metal surface at, or immediately adjacent to, the gap or crevice between two joining surfaces when exposed to a stagnant electrolyte. In these tight areas, stagnant conditions can develop, leading to the concentration of corrosive substances.
This localized corrosion can result in damage to the metal surfaces, compromising their integrity over time. It is important to address crevice corrosion through preventive measures, such as proper design considerations, material selection, and regular inspections to minimize the risk of deterioration in confined spaces.
7. Pitting Corrosion
Pitting corrosion is a localized and often small-scale form of corrosion by which cavities or “holes” are produced in the material. In this process, tiny pits or craters develop due to the uneven breakdown of the metal. It is usually caused by factors such as exposure to corrosive substances, environmental conditions, or the metal’s composition.
Pitting corrosion can be challenging to detect early on, making preventive measures crucial to mitigate potential damage. If left unchecked, it has the potential to compromise the structural integrity of the metal over time.
8. Uniform Corrosion
Uniform corrosion is a type of corrosion characterized by the uniform loss of metal over an entire surface. In this process, metal surfaces degrade evenly across their exposed area, resulting in a consistent level of deterioration. It often occurs due to exposure to environmental elements like moisture or chemicals.
While uniform corrosion may affect the appearance of the metal, its impact is spread evenly, and preventive measures such as protective coatings are commonly used to mitigate this type of corrosion and prolong the life of the metal.
How to Prevent Corrosion?
To safeguard metal structures from the detrimental effects of corrosion, implementing effective preventive measures is crucial.
1. Protective Coatings
Applying protective coatings is a fundamental method to prevent corrosion. These coatings act as barriers, shielding metals from direct contact with environmental elements such as moisture and air. Common coatings include paints, varnishes, or specialized corrosion-resistant materials that form a barrier over the metal surface. Regular inspection and reapplication of coatings are essential to ensure ongoing protection.
2. Material Selection
Choosing corrosion-resistant materials is a proactive approach to prevent corrosion. Opting for metals that inherently resist corrosion in specific environments can significantly extend the lifespan of structures. For instance, stainless steel and aluminum possess natural corrosion resistance, making them suitable choices for various applications.
3. Cathodic Protection
Cathodic protection is a technique used to safeguard metal structures by making them the cathode in an electrochemical cell. This method involves attaching sacrificial anodes, typically made of more reactive metals like zinc, to the structure. These sacrificial anodes corrode instead of the protected metal, preserving its integrity.
4. Environmental Modifications
Modifying the surrounding environment can also prevent corrosion. For instance, controlling moisture levels through proper drainage and ventilation helps mitigate one of the primary causes of corrosion. Additionally, minimizing exposure to corrosive substances and pollutants contributes to long-term protection.
5. Regular Maintenance
Regular maintenance is crucial for preventing corrosion. Inspection and cleaning allow early detection of any signs of corrosion, enabling timely intervention. Prompt removal of corrosion products and application of protective measures, such as coatings or inhibitors, can prevent further deterioration.
Implementing a combination of these preventive measures is often the most effective strategy. Tailoring the approach to the specific environment and considering the type of metal used ensures a comprehensive and sustainable corrosion prevention plan.
Enhance your expertise in tackling corrosion challenges by enrolling in PetroSync’s API 571 training. This specialized training provides comprehensive knowledge and practical insights into corrosion mechanisms, assessment techniques, and risk management strategies.
By participating in API 571 training, you’ll develop the essential skills to effectively identify, evaluate, and address corrosion issues, especially in industries prone to such challenges, like oil and gas. Invest in your professional growth and stay ahead in the field by undergoing API 571 training, ensuring you are well-equipped to manage and mitigate corrosion risks in your work environment.
Credit: Pexels
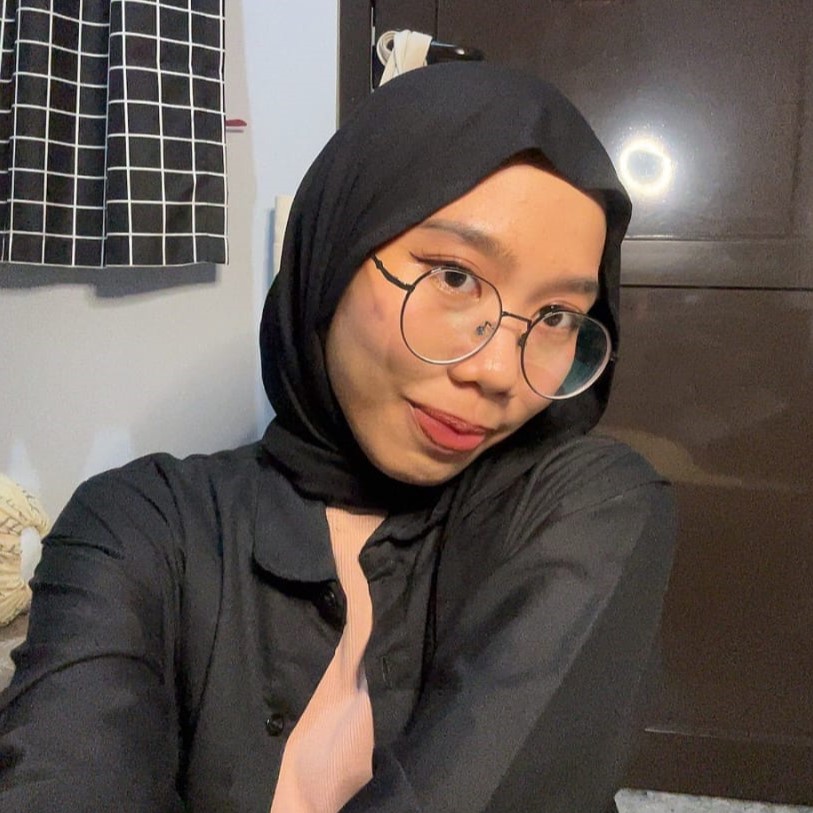
SEO specialist by day, fact-checker by night. An avid reader and content writer dedicated to delivering accurate and engaging articles through research and credible sources.