In the high-stakes world of industrial inspection, particularly in sectors like oil and gas, aviation, manufacturing, and heavy machinery, ensuring the structural integrity of materials is non-negotiable. Failures in detecting material defects can result in financial loss, operational downtime, or even endanger lives.
This is where Non-Destructive Testing (NDT) methods, such as Magnetic Particle Testing (MPT), come into play as reliable and efficient solutions. MPT has become a cornerstone of quality control strategies across industries. As organizations face increasing pressure to meet safety regulations and global standards, understanding and mastering this method can provide significant value for both individuals and businesses.
What is Magnetic Particle Testing?
Magnetic Particle Testing (MPT) is also known as Magnetic Particle Inspection (MPI), is a type of Non-Destructive Testing method used to detect surface and near-surface defects in ferromagnetic materials such as iron, nickel, and cobalt. This technique relies on the principles of magnetism to identify discontinuities like cracks, seams, or inclusions that are not visible to the naked eye.
MPT is often applied in industries where the failure of components can lead to catastrophic outcomes. Its ability to quickly and accurately pinpoint defects makes it a preferred choice in high-risk environments, including pipelines, pressure vessels, automotive parts, and aerospace components.
How Magnetic Particle Testing Works
The process begins by magnetizing the test specimen using either direct or indirect magnetization. In direct magnetization, an electric current passes through the object, while indirect magnetization involves placing the object in a magnetic field generated by external sources. Once magnetized, fine magnetic particles—either dry or suspended in liquid—are applied to the surface.
These particles are attracted to areas where magnetic flux leakage occurs, usually around a defect. As a result, the particles accumulate at the flaw, forming a visible indication that can be examined under proper lighting conditions. Modern MPT can also be performed under ultraviolet (UV) light using fluorescent particles to enhance visibility, especially for intricate inspections in low-light environments.
Advantages and Limitations of Magnetic Particle Testing
1. Advantages:
- Speed and simplicity: MPT is relatively quick and straightforward to perform, requiring minimal surface preparation.
- Cost-effective: Compared to other NDT methods, MPT is generally more affordable while still delivering reliable results.
- High sensitivity to surface defects: Particularly effective in detecting small cracks or discontinuities on or near the surface.
- Real-time results: Technicians can immediately interpret indications during inspection.
2. Limitations:
- Restricted to ferromagnetic materials: Non-magnetic metals like aluminum or austenitic stainless steel cannot be inspected using MPT.
- Surface accessibility: The technique requires direct access to the component surface.
Depth limitation: MPT can detect only surface and near-surface flaws, not deep internal defects. - Demagnetization required: Post-inspection demagnetization may be necessary, especially in components sensitive to magnetic fields.
Magnetic Particle Testing vs Other NDT Methods
MPT stands alongside other prominent NDT techniques like Ultrasonic Testing (UT), Radiographic Testing (RT), and Dye Penetrant Testing (DPT). Each has its own strengths and limitations:
- Compared to Ultrasonic Testing: MPT is more effective for surface-level flaws, whereas UT is better suited for detecting internal discontinuities.
- Compared to Radiographic Testing: RT provides a detailed image of internal structures but is more expensive and involves radiation hazards, unlike MPT.
- Compared to Dye Penetrant Testing: Both detect surface flaws, but MPT is faster and does not require dye or developer, making it less messy.
Selecting the right method depends on factors such as material type, defect location, and inspection environment. However, for ferromagnetic components with suspected surface cracks, MPT offers unmatched practicality.
What is the Maximum Temperature for Magnetic Particle Testing?
Temperature plays a crucial role in the accuracy of Magnetic Particle Testing. As per industry standards such as ASTM E709, the recommended maximum surface temperature for effective MPT is around 600°F (315°C) when using dry powder techniques. For wet methods, the limit is generally lower, often around 125°F (52°C).
Testing at high temperatures requires special considerations such as heat-resistant equipment, quick particle application, and technician safety. Operating beyond these limits may reduce the effectiveness of magnetization and lead to false results or missed defects.
Understanding these thresholds is essential, particularly in industries like petrochemicals or power plants where components operate under extreme conditions.
Join Industry-Recognized Training with PetroSync
As industries evolve and regulatory standards grow more rigorous, mastering Magnetic Particle Testing is not just an advantage—it’s a necessity. Whether you’re a technician aiming to upskill or a company looking to standardize inspection processes, quality training is the first step.
PetroSync offers industry-recognized training programs designed to equip professionals with practical skills and internationally accepted certification in Magnetic Particle Testing. With experienced instructors, hands-on practice, and compliance to global standards like ASNT and ISO, PetroSync ensures participants are ready to meet the demands of real-world inspections.
Studies have shown that structured NDT training can improve detection accuracy by over 30% and reduce equipment failure rates by nearly 40%. In a business context, this translates to reduced downtime, increased safety, and stronger client trust.
Don’t miss the opportunity to future-proof your career. Join PetroSync’s Magnetic Particle Testing training and be part of a growing community of certified NDT professionals.
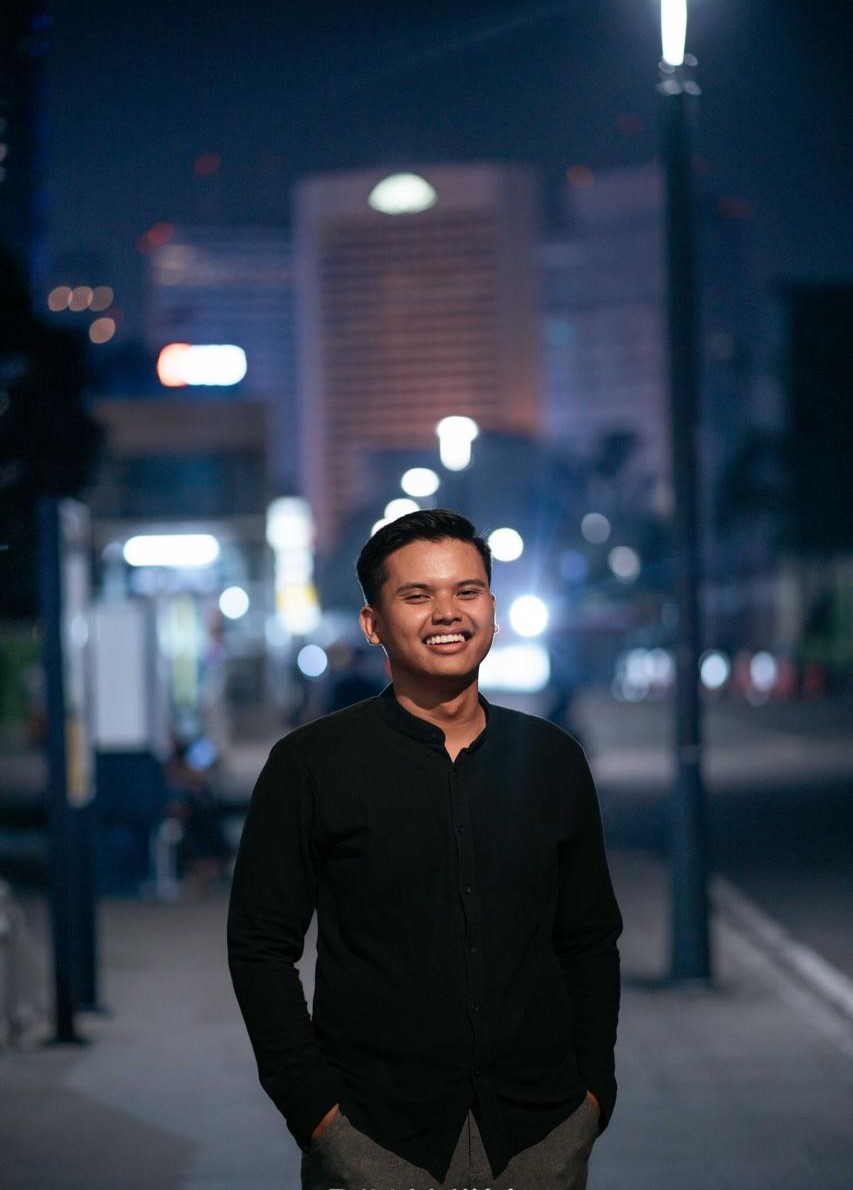
Results-oriented and thorough SEO specialist with extensive experience in conducting keyword research, developing and implementing digital website promotion strategies and plans, managing campaigns to develop company websites in the digital world, excellent knowledge of marketing techniques and principles, and attentive strong attention to detail.