What Is Pipe Stress Analysis?
Pipe Stress Analysis is a testing method that examines a piping system’s behavior under different loading situations, assessing how pipes respond to various forces and conditions. This method helps engineers understand if a piping system can handle stress caused by factors like pressure, temperature changes, or external forces.
This analysis involves sophisticated calculations and simulations to predict potential points of weakness or failure in the piping system. Engineers use specialized software to model the behavior of pipes, taking into account factors such as material properties, pipe dimensions, and the nature of the substances flowing through them.
By identifying potential stress points, engineers can make informed decisions about the design and support structures of the piping system. Adjustments can be made to mitigate stress concentrations, ensuring that the pipes can withstand the demands placed on them during regular operation.
Why Do You Need To Perform Pipe Stress Analysis?
Performing Pipe Stress Analysis is essential for several reasons. Notably, it helps ensure the safety and reliability of a piping system. Engineers can identify potential stress points that might lead to failures, leaks, or other issues by subjecting the system to various loading situations.
1. Observing Pipe Flexibility and Stiffness
Pipe Stress Analysis enables engineers to assess how a pipe material responds to pressure, temperature changes, fluid flow, and support conditions. This helps in understanding the flexibility and stiffness of the pipe, crucial factors in designing a system that can adapt to varying conditions.
2. Determining Maximum Stresses, Forces, Displacements, and Restraints
The analysis provides valuable insights into key parameters such as maximum stresses, forces, displacements, and restraints. This data aids engineers in designing a robust system that can withstand the forces it will encounter during its operational life.
3. Monitoring Stress Limits in Piping Components
Engineers use Pipe Stress Analysis to monitor stress limits in piping components, ensuring that they comply with relevant standards. This is essential for maintaining the piping’s integrity and preventing potential failures.
4. Deciding on the Right Support Systems
Engineers can make informed decisions about the appropriate support systems by understanding how pipes respond to different forces. This helps ensure that loads and movements are correctly managed and piping supports are carefully chosen, avoiding using materials that may not support the required loads and pressures.
5. Identifying Potential Disengagements
Pipe Stress Analysis helps engineers notice potential disengagements from support structures and pipes, enabling them to take preventive measures to secure the system and prevent unintended disconnections.
6. Anticipating Mechanical Vibrations, Seismic Loads, or Acoustic Vibrations
Engineers can use the analysis to foresee how mechanical vibrations, seismic loads, or acoustic vibrations might influence pipe operations. This proactive approach allows for implementing measures to mitigate these external factors’ impact on the system.
7. Ensuring Leak-Proof Pipes
Pipe Stress Analysis is crucial in guaranteeing that pipes are leak-proof. By assessing the material’s response to different conditions, engineers can design a system that minimizes the risk of leaks, contributing to the overall safety and reliability of the piping infrastructure.
8. Selecting Appropriate Materials
The analysis aids in selecting appropriate materials that meet the strength and durability requirements of the piping system. This ensures that the chosen materials can withstand the anticipated stresses and forces, contributing to the longevity and efficiency of the overall infrastructure.
What Are The Main Types of Pipe Stress Analysis?
Various factors like pressure, temperature, vibration, and occasional loads can affect pipe systems. There are five main types of stresses that impact pipes, each with its own characteristics.
Piping Stress Type |
Description |
Hoop Stress | Uniform pressure applied internally or externally, influencing the pipe’s diameter and wall thickness. |
Axial Stress | Arises from factors like thermal or pressure expansions, as well as applied forces causing the pipe’s restrained axial growth. It’s crucial to detect as different materials respond uniquely to this stress. |
Bending Stress | Originates from body forces, either concentrated (e.g., valve-related) or occasional (e.g., atmospheric forces like seismic movements or extreme wind events). Detected through forced displacements impacted by the growth of other equipment and piping. |
Torsional Stress | Caused by body forces creating rotational moments around the pipe axis. |
Fatigue Stress | Resulting from the combination of continuous stresses affecting specific pipe systems. |
Understanding these stresses is crucial for ensuring the reliability and safety of piping systems.
When To Perform A Pipe Stress Analysis?
Performing a Pipe Stress Analysis is essential at various stages in the lifecycle of a piping system. It is typically conducted
1. During Design Phase
- Before the installation of a new piping system or modification of an existing one.
- To ensure the system can withstand expected loads, pressures, and environmental conditions.
2. Prior to System Changes
- Before making significant alterations or additions to the existing piping infrastructure.
- To assess the impact of changes on stress levels and overall system performance.
3. Following System Modifications
- After any adjustments or repairs to the piping system.
- To confirm that the modifications have not introduced unforeseen stresses or weaknesses.
4. Regular Maintenance Intervals
- As part of routine inspections or maintenance procedures.
- To identify any emerging issues and prevent potential failures.
5. After External Factors
- Following events like seismic activities, extreme weather conditions, or other external forces.
- To evaluate the system’s resilience and detect any stress-related issues caused by external factors.
6. Periodically Throughout System Life
- At intervals over the operational life of the piping system.
- To ensure ongoing safety, reliability, and compliance with industry standards.
By incorporating Pipe Stress Analysis at these key points, engineers can proactively address potential issues, optimize system design, and maintain the integrity of piping systems throughout their lifecycle.
How To Perform A Pipe Stress Analysis?
Performing a Pipe Stress Analysis requires a systematic approach to ensure accuracy and reliability. Here are detailed steps for conducting a comprehensive analysis as a piping engineer:
1. Gather System Information:
Collect detailed information about the piping system, including dimensions, material specifications, operating conditions, and design drawings.
2. Define Boundary Conditions:
Establish the boundary conditions for the analysis, considering restraints, supports, and connections to other equipment.
3. Determine Loadings and Forces:
Identify and quantify all relevant loads and forces acting on the piping system, including pressure, thermal expansion, external loads, and occasional loads.
4. Model the Piping System:
Use specialized software to create a 3D model of the entire piping system, incorporating accurate representations of pipes, supports, restraints, and connected equipment.
5. Apply Material Properties:
Assign appropriate material properties to each component in the model, considering factors like elasticity, thermal expansion coefficients, and other material-specific characteristics.
6. Define Analysis Parameters:
Specify parameters for the analysis, such as allowable stresses, design codes, and any applicable industry standards.
7. Perform Static Analysis:
Conduct a static analysis to evaluate the system’s response to steady-state conditions, including pressures, temperatures, and sustained loads.
8. Perform Dynamic Analysis:
If required, perform dynamic analyses to assess the system’s behavior under transient conditions, such as seismic events or rapid changes in operating conditions.
9. Review Analysis Results:
Analyze the results to identify areas of concern, including excessive stresses, displacements, or other anomalies.
10. Make Necessary Adjustments:
Modify the piping system model as needed to address identified issues. This may involve adjusting support locations, modifying components, or revising material selections.
11. Iterative Analysis:
Perform iterative analyses as required, especially after making adjustments, to ensure that the system meets safety and performance criteria.
12. Documentation and Reporting:
Document the analysis process, including all assumptions, input data, and results. Prepare a comprehensive report outlining the findings, recommendations, and any necessary follow-up actions.
13. Validation and Verification:
Validate the analysis results against known system behavior or, if possible, field measurements to verify the accuracy of the model and analysis.
14. Peer Review:
Subject the analysis and results to peer review, encouraging collaboration and ensuring that multiple perspectives contribute to the final assessment.
By following these detailed steps, a piping engineer can conduct a thorough and accurate Pipe Stress Analysis, contributing to the overall safety, reliability, and performance of the piping system.
To further enhance your proficiency in Pipe Stress Analysis and ensure compliance with industry standards like ASME B31.3, consider investing in professional development. PetroSync offers comprehensive ASME B31.3 training programs designed to deepen your understanding of piping systems, stress analysis methodologies, and the practical application of standards.
By enrolling in PetroSynindustryc’s training, you gain access to expert-led sessions, real-world case studies, and hands-on experiences that will equip you with the skills needed to excel in the field of piping engineering. This training not only enhances your technical knowledge but also provides valuable insights into the best practices and methodologies endorsed by ASME B31.3.
Take the initiative to further your career and contribute to the success of your projects by acquiring in-depth knowledge of Pipe Stress Analysis through PetroSync’s ASME B31.3 training. Investing in continuous learning and staying abreast of industry standards will undoubtedly position you as a proficient and sought-after professional in the dynamic field of piping engineering. Enroll now to secure your place in PetroSync’s training and elevate your expertise to new heights.
Credit header image: iStock
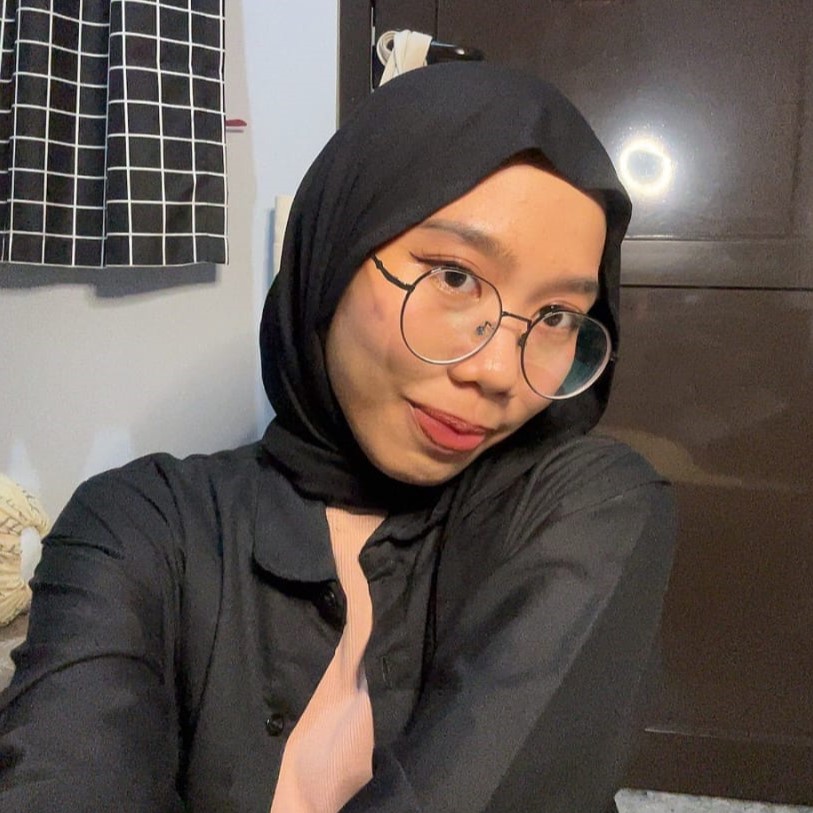
SEO specialist by day, fact-checker by night. An avid reader and content writer dedicated to delivering accurate and engaging articles through research and credible sources.