Piping systems are critical in the energy business to ensure smooth operations, whether in the oil and gas, petrochemical, or energy industries. This article will go into detail on what a piping system is, its components, types, and how it is utilized in buildings, as well as strategies for increasing piping system adaptability.
What Is a Piping System?
A piping system is a collection of pipes, fittings, and valves designed to fulfill specific functions, such as moving fluid from one piece of equipment to another. Its dimensions might range from a tiny diameter tube to a huge sophisticated system for reaching facilities. A piping system built to meet primary criteria such as fluid flow, pressure, temperature, and other parameters must adhere to regulatory and safety standards. Common examples of piping systems include water supply networks in homes, as well as steam piping in power plants, paint piping in paint manufacturers, oil piping in oil refineries, and others.
Related article : Piping for Process Plants: Leak Testing and Verification
What Are The Components of Piping Systems?
The word “piping system” refers to a network of pipes, fittings, flanges, valves, and other components that can be combined to form a channel system for fluid flow. The way a good piping system distributes fluids from one place to another by processing and conditioning the fluids means that the components in the piping are critical to the system’s operation. Although there are various types of plumbing systems, the components employed in each are crucial. So that each piping system is made up of the following components:
1. Pipes
Pipe bends and offsets can also provide flexibility and accommodate changes in direction or alignment.
2. Fittings
Valves are utilized to manage the fluid flow within the piping system. They can control the flow by regulating it, fully stopping it, or enabling partial flow.
3. Valves
Valves are utilized to manage the fluid flow within the piping system. They can control the flow by regulating it, fully stopping it, or enabling partial flow.
4. Fittings
Fittings are utilized to link pipes and alter the direction or flow of fluids. These fittings may comprise elbow joints, tees, reducers, and couplings.
Related article : API RP 574: Piping System Inspection Practices Guide
5. Flanges
Flanges are utilized to join pipes or fittings together and form a sealed joint. They are commonly bolted together and can be readily dismantled for maintenance or repair purposes. One of the most common types of flanges is flanged joints.
6. Supports
Supports are used to bear the weight of the piping system and hold it in position. Such supports may involve hangers, brackets, and clamps.
7. Elbows
Elbows are piping system components that change the direction of flow. Typically, elbows are available in a variety of angles, including 45 degrees and 90 degrees.
8. Add A Cap
A cap is used to close the end of a pipe, preventing fluid from exiting the pipe that is not attached to another component.
9. Gasket
A gasket is a substance that is installed between two flanges to prevent leaks at the connection.
10. Acrylonitrile Butadiene Styrene (ABS)
ABS is a type of plastic that is frequently used in plumbing systems due to its lightweight, robust, and corrosion-resistant qualities.
What are The Types of Piping Systems?
Piping systems are divided into different types based on a variety of parameters. Piping systems are classified into the following types:
1. Based on fluid:
- Water Piping System
- Oil Piping System
- Gas piping system
- Steam piping system
- Slurry Piping system
- Ash handling piping system.
- Compressed air piping system.
- Chemical piping system
- Vacuum Piping System.
2. Based on the sector where the piping is used :
- Plumbing systems/Building Services Piping System: Potable water and garbage are conveyed through buildings, residences, and other structures.
- Fire protection systems: In the event of a fire, water is supplied to sprinklers and hoses.
- Natural gas and propane systems: Designed to transport natural gas and propane from the main supply line to appliances such as furnaces, stoves, and water heaters.
- Steam systems/Power systems Piping: Steam is conveyed from boilers to steam-powered equipment and operations.
- Process piping systems: Chemicals, liquids, gasses, and other materials are transported using these systems in industrial processes.
- HVAC systems: Conveying air and liquids to and from air conditioners, furnaces, and heat exchangers is how buildings are heated and cooled.
- Medical gas systems: In healthcare facilities, they are used to transport medical gases such as oxygen, nitrous oxide, and medical air.
- Fuel oil systems: Fuel oil is conveyed in heating systems and backup generators.
- Cryogenic Piping System: Useful for transporting cryogenic fluids.
- Hazardous Piping System: It is used to transport hazardous fluids.
- Fuel Gas distribution Piping System
3. Based on the pipe material used:
- Metallic Piping System
- Non-Metallic Piping System
- Composite Piping System
- Internally Lined Piping System
- Concrete Piping System
- Glass Piping System, etc
4. Based on the actual piping system directed:
- Aboveground Piping System
- Buried Piping System
- Underground Piping System
What Are The Methods to Incorporate Flexibility in Piping Systems?
Flexibility is a vital aspect when it comes to designing piping systems. Without it, the movements of materials transported inside can cause excessive stresses, leading to leaks, cracks, or other failures.
Related article : Dive into Differences of Boiler Proper & Boiler External Piping
Therefore, the design and construction of piping systems must incorporate sufficient flexibility to accommodate these movements while maintaining structural integrity and preventing leaks or failures. ASME B31.3 provides several methods to incorporate flexibility into piping systems.
1. Expansion Loops
Expansion loops are typically used in long straight pipe runs to accommodate thermal expansion and contraction
2. Expansion joints
Expansion Joints are installed at specific locations in the piping system to absorb movements caused by thermal expansion, vibration, or equipment movement.
3. Flexible Hoses
Flexible hoses can be used to connect rigid pipe sections or to accommodate small amounts of movement.
4. Pipe Bends and Offsets
Pipe bends and offsets can also provide flexibility and accommodate changes in direction or alignment.
Optimize Your Engineering Skills with PetroSync Piping System Training
The process of designing and choosing these flexible components should take into account various factors such as the operating pressure and temperature, the fluid characteristics, and the projected range of motion. It’s crucial to ensure that adding flexibility to piping systems doesn’t undermine the system’s safety.
Joining PetroSync’s ASME B31.3 – Process Piping Code Design Requirements training course is vital for you to excel in the field of piping systems. This program offers in-depth knowledge and practical skills that are essential for designing, constructing, and maintaining piping systems.
By participating in this training, you will learn about the latest industry standards, codes, and regulations that are crucial to ensuring the safety, reliability, and efficiency of piping systems.
With the knowledge gained from the ASME B31.3 course, you will be well-equipped to tackle any piping project with confidence and precision, setting you apart as a highly skilled and sought-after professional in the field. Reserve your ASME B31.3 training spot and let’s boost your proficiency and expertise in piping by acquiring practical knowledge and skills with PetroSync!
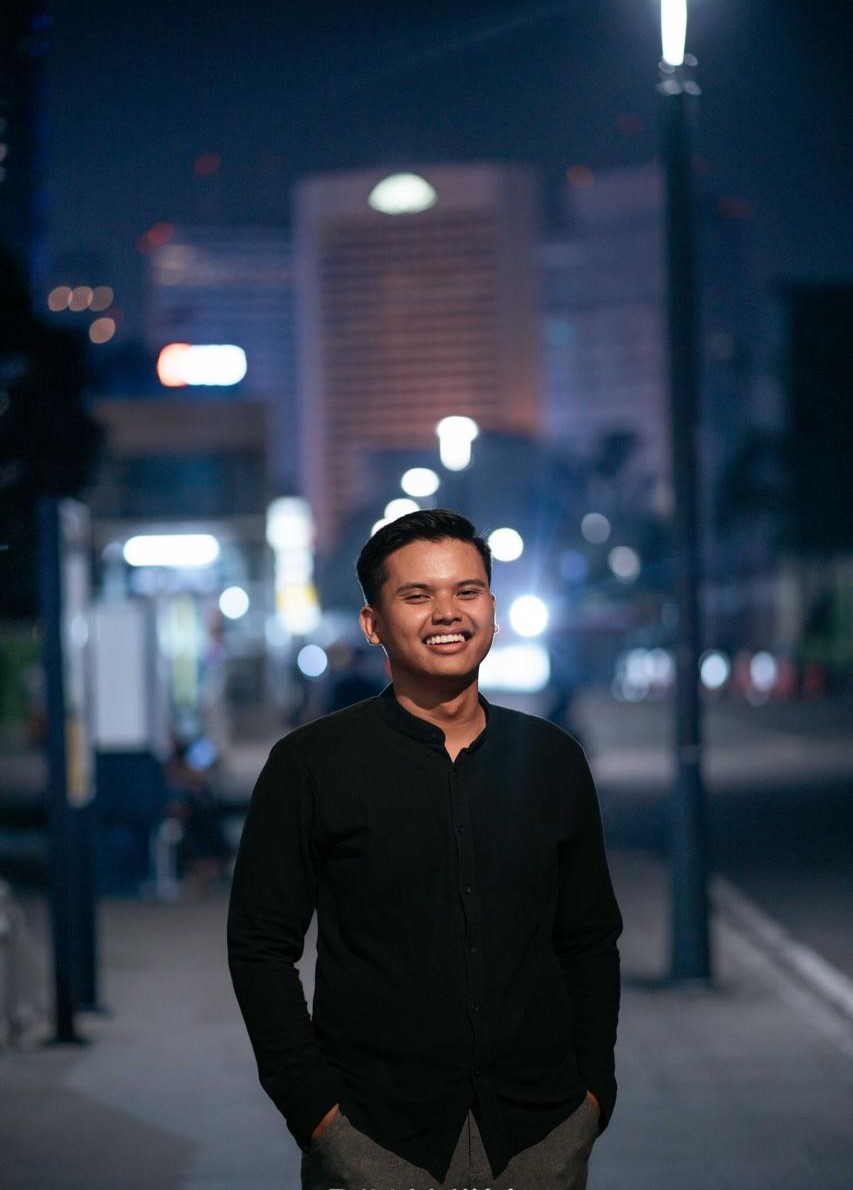
Results-oriented and thorough SEO specialist with extensive experience in conducting keyword research, developing and implementing digital website promotion strategies and plans, managing campaigns to develop company websites in the digital world, excellent knowledge of marketing techniques and principles, and attentive strong attention to detail.