API RP 574 is a standard created by the American Petroleum Institute (API) for professionals responsible for inspecting and maintaining piping systems. This document provides valuable advice and methods for evaluating the condition and strength of different parts within piping systems. This article explores the main principles and recommendations found in API RP 574, highlighting its importance in safeguarding asset integrity and reducing risks related to piping system failures.
What is API 574?
API 574 – Inspection Practices for Piping System Components is a standard created by the American Petroleum Institute (API) that provides guidelines for the inspection and maintenance of piping systems in the petroleum and chemical industries.
The standard covers topics such as inspection techniques, assessment of piping conditions, and recommended repair practices to ensure the safety and integrity of piping systems. API 574 helps industry professionals maintain compliance with regulatory requirements and implement effective maintenance strategies to prevent accidents and ensure reliable operation of piping systems.
What Is The Scope of API 574?
The scope of API 574 is to complement API 570 by providing piping inspectors with valuable information to enhance their skills and knowledge of inspection practices. This recommended practice describes inspection practices for various components such as
- Piping
- Tubing
- Valves (excluding control valves), and
- Fittings
These components are commonly found in petroleum refineries and chemical plants. It covers topics such as inspection planning, intervals, and techniques, as well as types of records to aid inspectors in implementing API 570. However, it does not cover the inspection of specialty items like instrumentation, furnace tubulars, and control valves.
Why Does API 574 Inspection Need to Be Done?
API 574 inspection is necessary to ensure the safety, integrity, and reliability of piping systems in industries such as petroleum refining and chemical processing. It helps identify potential issues, assess the condition of piping components, and implement timely repairs or replacements to prevent accidents and ensure operational continuity.
1. General Purposes of Inspection
Inspection is crucial for observing, reporting, and quantifying damage in piping systems. By identifying credible damage mechanisms and assessing the physical condition of the piping, inspectors can determine the causes and rates of deterioration. Developing a database of inspection history enables predicting future repairs, preventing further deterioration, and ultimately avoiding loss of containment. This proactive approach enhances operating safety, reduces maintenance costs, and ensures reliable and efficient operations.
2. Process and Personnel Safety
The integrity of piping systems is essential for process and personnel safety, especially in industries handling hazardous fluids. Leaks or failures in piping systems containing flammable, toxic, or harmful fluids can lead to process safety incidents or environmental consequences. Adequate inspection helps maintain piping systems in a safe and reliable condition, preventing potential hazards to personnel and the environment.
3. Regulatory Compliance
Regulatory requirements mandate the inspection of piping systems that pose risks to personnel, process safety, and the environment. Regulations like OSHA 29 CFR 1910.119 in the United States require equipment, including piping, handling hazardous chemicals, to be inspected according to accepted codes and standards such as API 570. Compliance with local and state regulations ensures that piping inspection and maintenance are conducted effectively to mitigate risks.
4. Ensuring Reliable Operation
In addition to safety considerations, thorough inspection and maintenance of piping systems are essential for ensuring reliable operation and meeting business objectives. Detailed inspection records, data analysis, and maintenance schedules help maintain acceptable process reliability and prevent unplanned outages. Scheduled maintenance turnarounds are coordinated with maintenance and replacement schedules to minimize production disruptions and maximize operational efficiency.
How To Develop an Inspection Plan based on API 574?
By establishing a structured plan, organizations can systematically assess the condition of piping components, identify potential issues, and implement timely maintenance or replacement actions to prevent accidents and ensure continuous operation.
1. Collaborative Development
The inspection plan is typically developed collaboratively by a team comprising the inspector, piping engineer, corrosion specialist, and operating personnel. This multidisciplinary approach ensures that various perspectives and expertise are considered in the development process.
The team analyzes several factors such as operating temperature and pressure ranges, corrosive contaminant levels in process fluids, piping material, system configuration, and inspection history to formulate an effective inspection plan.
2. Information Consideration
The team gathers information from various sources, including industry publications such as API and NACE, to understand similar systems’ experiences and define potential damage types and locations. This information serves as a foundation for identifying specific damage mechanisms and determining suitable inspection techniques to address them effectively.
3. Selection of Inspection Techniques
Knowledge of non-destructive examination (NDE) techniques’ capabilities and limitations helps in choosing the appropriate examination methods to detect specific damage mechanisms in particular locations. References like API RP 571 and ASME PCC-3 provide valuable insights into inspection techniques and their applications for specific damage mechanisms.
4. Ongoing Communication
Continuous communication with operating personnel is crucial to keeping the inspection plan updated, particularly when process changes or upsets occur that could affect damage mechanisms and rates.
Integrity Operating Windows (IOWs) are established to set key thresholds for process changes that impact mechanical integrity, ensuring timely adjustments to the inspection plan. API RP 584 offers further guidance on this aspect.
5. Addressing Piping Systems Components
The inspection plan should encompass various components of piping systems, including condition monitoring locations (CMLs), pipe supports, corrosion under insulation (CUI), injection points, process mixing points, soil-to-air interfaces (SAIs), deadleg sections, and critical valves. Additionally, auxiliary piping, vents/drains, internal linings, expansion joints, and critical utility piping should be considered to ensure comprehensive coverage.
6. Miscellaneous Considerations
Careful consideration should be given to incorporating overlooked piping and tubing components into the inspection plan, such as instrument bridles, temporary piping used during maintenance outages, and swing-out spools. Despite being outside routine inspection programs, these components may still pose reliability concerns and warrant inclusion in the plan.
7. Risk Assessment and Intervals
Inspection plans may be based on various criteria, including risk assessment or fixed intervals as defined in API 570. Incorporating risk-based inspection principles ensures that resources are allocated efficiently, focusing efforts on areas with the highest risk of failure. For further guidance on Risk Based Inspection, refer to section 8.2 of relevant standards.
In conclusion, API 574 plays a critical role in ensuring the safety, reliability, and integrity of piping systems within the oil and gas, petrochemical, and energy industries. By providing guidelines for inspection practices, API 574 enables organizations to systematically assess the condition of piping components, identify potential issues, and take proactive measures to prevent accidents and maintain operational continuity.
Adhering to API 574 standards not only enhances safety and reliability but also helps organizations minimize downtime, reduce maintenance costs, and optimize overall operational efficiency, thus contributing to the long-term success and sustainability of these vital industries.
To give you a more comprehensive understanding of piping standards, you should consider taking API 570 training offered by PetroSync, as it provides a more comprehensive understanding of the standards for Piping Inspectors. In particular, on day 4 of the training, you will delve into API 574, which is a crucial aspect of ensuring the safety and integrity of piping systems.
Our API 570 training will equip you with the knowledge and skills needed to effectively inspect piping systems, enhancing your capabilities as a Piping Inspector and contributing to the overall reliability and safety of your organization’s operations.
Credit Vecteezy
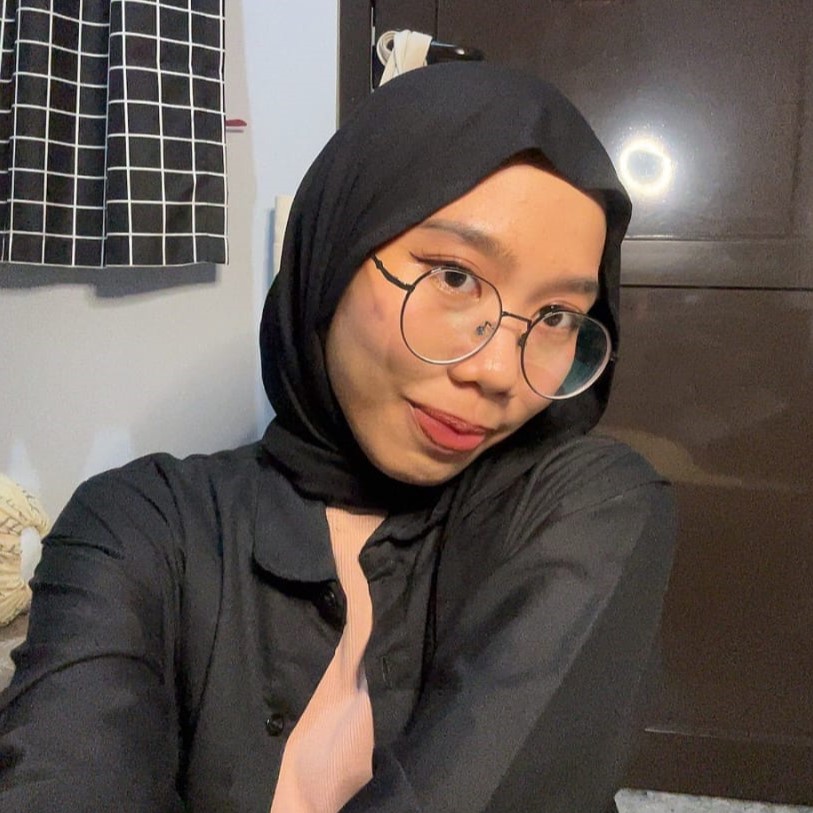
SEO specialist by day, fact-checker by night. An avid reader and content writer dedicated to delivering accurate and engaging articles through research and credible sources.