Corrosion Under Insulation (CUI) presents a significant challenge for industries relying on insulated equipment. The insulation meant to conserve energy can inadvertently lead to corrosion. Left unchecked, CUI can cause extensive damage, jeopardize safety, and incur substantial costs. This article provides an in-depth exploration of CUI, covering its causes, detection methods, preventive measures, and effective mitigation strategies. By understanding and implementing proactive approaches, industries can protect their assets and ensure long-term reliability.
What Is Corrosion Under Insulation?
Corrosion Under Insulation (CUI) refers to the occurrence of corrosion caused by moisture on the outer surface of insulated equipment. Corrosion Under Insulation (CUI) can be caused by various factors and affects equipment operating in different conditions, including ambient, low, and heated services.
It can happen to thermally insulated equipment whether it is in use, out of use, or undergoing cyclic service. Since these surfaces are typically not visible for inspection, detecting the early signs of corrosion is challenging. In severe cases, it can lead to significant corrosion and compromise the integrity of the system.
What Are Some Types of Corrosion Under Insulation?
To prevent corrosion under insulation, it is important to identify the different types of corrosion that can occur and use suitable materials and construction methods. The main issue in Corrosion Under Insulation (CUI) is water intrusion.
According to National Board of Boiler and Pressure Vessel Inspectors, there are three types of corrosion In CUI:
1. Galvanic Corrosion
Galvanic corrosion typically occurs when insulation becomes wet and contains an electrolyte or salt, enabling an electrical current to flow between different metals. This happens between the insulated metal surface and the outer jacket or accessories.
2. Alkaline or Acidic Corrosion
Alkaline or acidic corrosion occurs when certain fibrous or granular insulations are exposed to moisture along with alkali or acid substances.
3. Chloride Corrosion
Chloride corrosion may arise when moisture is present and temperatures exceed 140°F, combining insulation that contains leachable chlorides with surfaces made of 300 series austenitic stainless steel.
During the design phase, it is crucial to avoid promoting corrosion by preventing water from entering the system, whether directly or through capillary action. Moisture can come from external sources or be present within the insulation itself. By being aware of these factors and taking appropriate precautions, piping inspectors can effectively combat corrosion and protect the equipment.
What Causes Corrosion Under Insulation?
Corrosion Under Insulation (CUI) occurs when moisture becomes trapped between the insulation and the equipment surface. This moisture, which can enter through leaks or improper installation, creates a corrosive environment that deteriorates the underlying material.
Additionally, corrosive substances and temperature changes contribute to the corrosion process. If left unaddressed, CUI can cause significant damage and compromise system integrity. Understanding the causes of CUI is essential for implementing effective prevention measures and safeguarding the equipment from corrosion-related issues.
How To Prevent Corrosion Under Insulation?
Preventing Corrosion Under Insulation (CUI) is vital for preserving the integrity and lifespan of insulated equipment. By implementing proactive measures and proper practices, the risk of CUI can be significantly reduced.
Cited from National Board of Boiler and Pressure Vessel Inspectors, there are five methods to prevent corrosion under insulation:
1. Insulation Selection
When selecting insulation, it is crucial to consider the specific conditions of the area, such as spills or high humidity. Some insulations are less affected by defects in weatherproofing or paint films because they are nonabsorbent and chemically nonreactive.
Insulations like calcium silicate, glass fiber, and cellular plastic foams tend to absorb and retain liquids and vapors. Additional flashing is required in areas where spills, leaks, or washdowns may occur. The only completely nonabsorbent insulation is cellular glass, which should be used when corrosive or flammable liquids are present.
2. Equipment Design
When it comes to insulating pressure vessels, tanks, and piping, it is essential to carefully design the support and connection of the insulation material. The Midwest Insulation Contractor’s Association handbook provides valuable information on the subject.
Plant operators have noted that weather barriers for insulation often fail due to inadequate initial equipment details or insufficient space allocated around the insulation. Enhancements in design can be achieved by addressing insulation specifications early in the vessel design process and by simplifying the surface that needs to be insulated.
3. Protective Paints and Coatings
The coating system must provide long-term protection against water and corrosives. Highly permeable coatings can allow corrosion to occur behind the coating, even without visible breaks or pinholes.
Consider temperature and abrasion resistance, as well as the coating’s ability to withstand immersion in water or corrosive chemicals when making your selection. Visual inspection of coatings under insulation is challenging, so plan for recoating every 10-15 years unless corrosion or insulation failure requires re-insulating the entire setup.
4. Weather Barriers
The weather/vapor jacket of the insulation acts as the primary barrier to water, allowing for inspection and cost-effective repairs. It must prevent liquid entry while facilitating evaporation. A weatherproofing rating of two perms (ASTM Standard E 398) is acceptable. The jacket should be durable, flame-spread resistant, and economically viable. Regular maintenance every two to five years is essential for its effectiveness.
5. Maintenance Practices
Additionally, regular maintenance is necessary to identify defects caused by deterioration or misuse. If the system is opened for maintenance or inspection, it is crucial to promptly close it once the work is finished. A plant shared an incident where openings made in a metal vessel’s insulation for acoustic emission tests were left unclosed, resulting in severe corrosion.
What Are Some of The Relevant Codes, Standards, and Best Practices Related to Corrosion Under Insulation (CUI)?
Some of the relevant standards that discuss about corrosion under insulation are:
1. API 510 – Pressure Vessel Inspector
API 510 is a certification for Pressure Vessel Inspectors, validating their competence in assessing and ensuring the safety and compliance of pressure vessels. CUI inspection is covered in section 5.5.6 of the standard (Tenth Edition released April 2014).
2. API 570 – Piping Inspector Course
API 570 offers guidance on identifying the piping systems most vulnerable to Corrosion Under Insulation (CUI) (section 5.2.1). It also highlights common locations where CUI is often found on those susceptible systems (section 5.4.2). (Third Edition released November 2009).
3. API 574 – Inspection Practices for Piping System Components
API 574 provides inspection practices for various components of piping systems, ensuring their integrity and compliance with industry standards and regulations. CUI is covered in section 6.3.3 (Third Edition released November 2009).
4. API RP 583 – Corrosion Under Insulation and Fireproofing
The guide deals with Corrosion Under Insulation (CUI) in pressure vessels, piping, storage tanks, and spheres. It covers prevention, maintenance, inspection, and risk assessment for CUI in equipment or structural steel. (First Edition released May 2014)
Corrosion under insulation is a vital concern for engineers in industries like oil and gas, refineries, and chemicals. It occurs when moisture gets trapped under insulation, leading to metal corrosion.
To address this issue effectively, you should consider API 570 training and API 510 training by PetroSync. Our API 570 course and 510 course provide in-depth knowledge of corrosion management, inspection techniques, and mitigation strategies, ensuring improved asset integrity and operational safety. Invest in handle corrosion under insulation skills and enhance your professional expertise with PetroSync!
Credit header image:
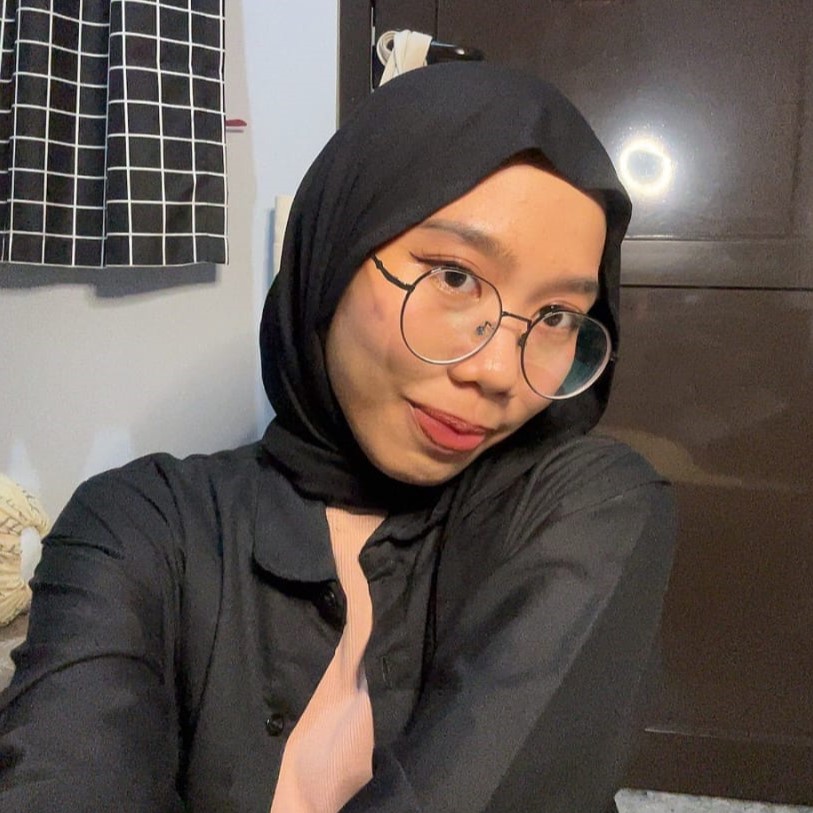
SEO specialist by day, fact-checker by night. An avid reader and content writer dedicated to delivering accurate and engaging articles through research and credible sources.