In the oil and gas industry, pressure vessel are essential components as they enable the secure containment of fluid under high pressure and often adverse environmental circumstances. Designing these crucial components is not something that comes easily; you must walk a fine line between safety, efficiency and strict compliance with the regulations.
Design refers to the development of facilities for pressure vessel engineers Package Title: Design Data Handbook The Construction. Maintaining of the pressure vessel means that the engineers should have the knowledge of design techniques.At the same time, continuous technological and material developments – such as the introduction of Type 4 pressure vessels – continue to shape industry norms.
These fundamental subjects are examined in this article along with ways that engineers can further their knowledge through formal education.
What is the theory of pressure vessel design?
The scientific theory that regulates how specific materials react to both internal and external efforts is the base premise of pressure vessel design. First and foremost, we want the walls of the containing vessel to be able to bear the forces that the fluid imparts on it without cracking.
Primary stresses are the hoop stress, which occurs around the circumference of the vessel and the longitudinal stress that operates along the vessels axis. The design procedure is usually bound by rigid codes such as the ASME Boiler and Pressure Vessel Code (BPVC) and is primarily founded upon the conceptual framework of structural analysis and classical theory of elasticity.
In these specifications, acceptable stresses are set when considering material properties and operation conditions, and leave strength margins to us. The theories also consider fatigue cracking due to cyclic loading, stress corrosion cracking, plastic deformation, and elastic deformation as failure mechanisms.
It reduces the probability of catastrophic failures, which would make structures unsafe and could lead to substantial financial losses, by “designing right.”
How to design a pressure vessel calculation?
Designing a pressure vessel involves a systematic process combining empirical formulas, material science, and engineering judgment:
1. Identify Design Parameters:
Determine the maximum operating pressure, temperature range, fluid properties, and vessel dimensions.
2. Material Selection:
Choose materials that meet strength, ductility, and corrosion resistance requirements for the operating environment.
3. Calculate Wall Thickness:
Use established formulas to compute the minimum required thickness. This calculation factors in the design pressure, radius of the vessel, allowable stress for the material, and welding efficiency. The wall thickness must be sufficient to withstand internal pressures without exceeding stress limits.
4. Stress Analysis:
Calculate hoop, longitudinal, and radial stresses. These must remain below allowable stress levels to ensure safety.
5. Consider Corrosion Allowance and Manufacturing Tolerances:
Additional thickness is often added to account for material loss over time and production variances.
6. Validate Design Against Standards:
Confirm that the design complies with relevant codes like ASME BPVC and API 510.
The advent of Finite Element Analysis (FEA) software has revolutionized this process, enabling detailed simulations of stress distribution and identification of potential failure points, thereby optimizing designs for safety and cost.
What is the basic requirement to design the pressure vessel?
Several key requirements guide the effective design of pressure vessels:
- Structural Integrity: Materials and design must ensure the vessel can withstand operational pressures and temperatures without deformation or failure.
- Safety Margins: A factor of safety, commonly between 1.5 and 4, is incorporated to mitigate uncertainties in loading conditions.
- Compliance with Codes: Design must conform to internationally recognized standards (e.g., ASME BPVC, API 510), which dictate materials, fabrication, inspection, and testing criteria.
- Corrosion and Fatigue Resistance: Given exposure to harsh fluids and cyclic pressures, vessels must resist corrosion and fatigue to maintain longevity.
- Accessibility for Inspection and Maintenance: Designs should facilitate routine checks and repairs, enhancing operational reliability.
Meeting these requirements is crucial not only for safety but also for reducing downtime and operational costs.
What are the design conditions for a pressure vessel?
Design conditions encompass the environmental and operational factors influencing vessel design:
- Operating and Test Pressures: Include maximum pressures during normal operation and pressure testing phases.
- Temperature Ranges: Both high and low extremes affect material performance.
- Fluid Characteristics: Corrosiveness, toxicity, and phase (gas or liquid) impact material and sealing choices.
- External Conditions: Exposure to elements such as weather, seismic activity, or chemical environments must be accounted for.
- Pressure Cycling: Frequency and variation of pressure changes can induce fatigue damage.
- Geometry and Dimensions: Vessel shape and size directly affect stress distribution and structural stability.
A thorough assessment of these conditions ensures a design that balances safety, durability, and efficiency.
What is a Type 4 pressure vessel?
Type 4 pressure vessels represent a significant technological advancement. Unlike traditional metallic vessels, these are constructed primarily from composite materials with a polymer liner, reinforced by carbon fiber or fiberglass.
Key advantages include:
- Lightweight: They can weigh up to 50% less than steel vessels, enhancing portability and reducing structural load.
- Corrosion Resistance: The composite materials resist chemical degradation, extending service life.
- High Strength: Carbon fiber reinforcement delivers exceptional tensile strength to withstand high pressures.
- Applications: Widely used in hydrogen storage, fuel cell vehicles, aerospace, and emerging clean energy sectors.
Their innovative design supports industry moves toward more efficient, safer, and environmentally friendly energy storage solutions.
PetroSync Training: Join Now to Enhance Your Engineering Skills
In a sector where technological advances and safety demands are ever-evolving, continuous learning is essential. PetroSync offers tailored training programs for oil and gas engineers, focusing on practical and theoretical mastery of pressure vessel design and related engineering disciplines.
Through experienced instructors, hands-on projects, and updated curriculum aligned with industry standards, PetroSync equips professionals with skills that directly enhance their productivity and accuracy. According to internal company reports,
PetroSync graduates improve operational efficiency by up to 20% and reduce design errors significantly, positively impacting organizational growth and safety outcomes. Investing in PetroSync’s training is an investment in your professional growth and the future success of your company. Take the step today to advance your engineering expertise and career prospects.
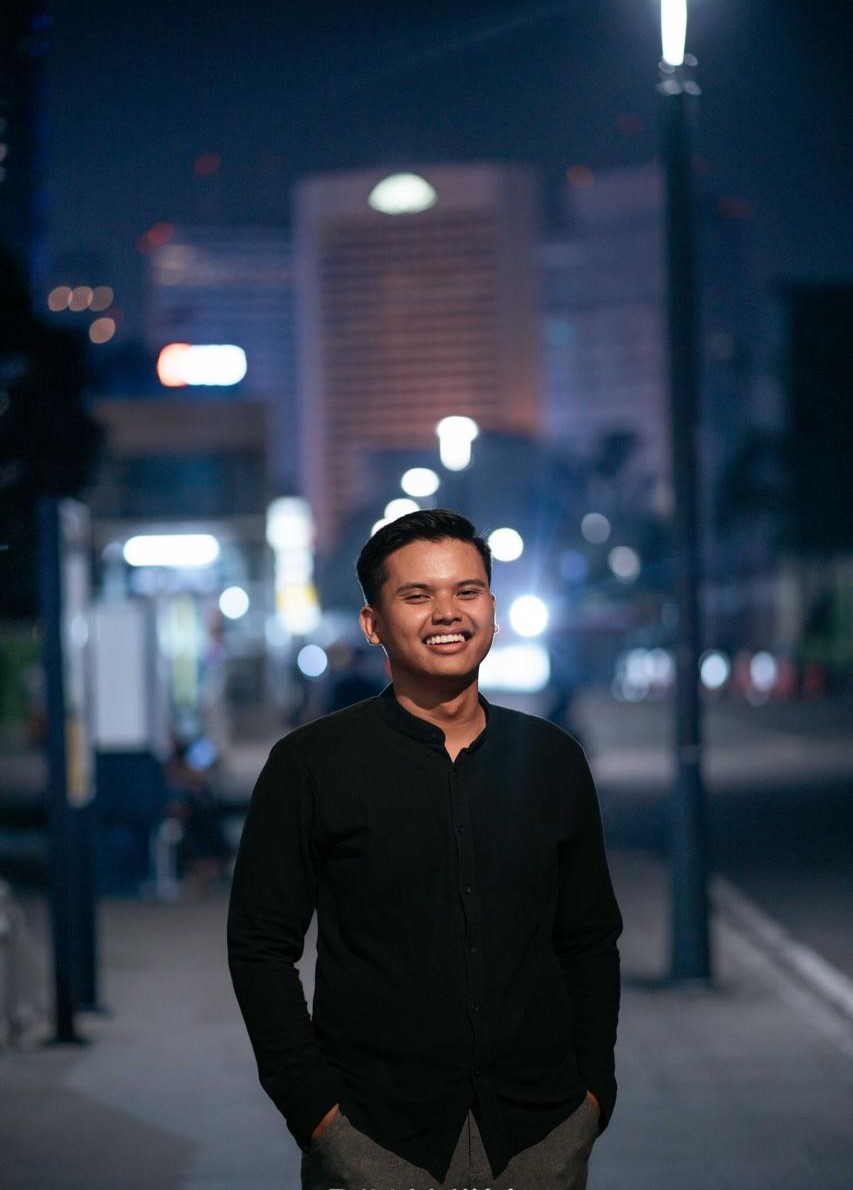
Results-oriented and thorough SEO specialist with extensive experience in conducting keyword research, developing and implementing digital website promotion strategies and plans, managing campaigns to develop company websites in the digital world, excellent knowledge of marketing techniques and principles, and attentive strong attention to detail.