The oil and gasoline employer faces intricate challenges when it comes to optimizing hydrocarbon manufacturing from subsurface reservoirs. One of the most crucial phases in this manner is precise completion. Often regarded as the ultimate hyperlink between drilling operations and production, desirable completion performs a quintessential feature in making certain that sources can be extracted efficiently, safely, and economically.
But what exactly does well completion involve? How is it designed? And why is this process essential for long-term production success? Let’s explore in detail.
What is Meant by Well Completion?
Well completion refers to the sequence of technical steps taken after drilling a wellbore, getting ready it for safe, efficient, and managed manufacturing of oil or gas. This area transforms a drilled correct into a production-ready machine that approves hydrocarbons to waft from the reservoir to the surface.
Completion consists of inserting in vital equipment, such as casing, tubing, packers, perforations, and on event specialised tools like sand manage constructions or security valves. The essential aim is to make sure ideal glide rates, guard the wellbore, and maximize healing over the well’s lifespan.
A well-completed system moreover provides crucial obstacles to stop environmental risks, such as leaks or blowouts. In short, barring acceptable completion, even the most promising reservoir may also moreover underperform or pose massive protection hazards.
What Are the Three Types of Well Completion?
The oil and gasoline industry normally categorizes nicely completions into three fundamental types, every perfect to unique reservoir traits and manufacturing objectives:
1. Open Hole Completion
In this approach, the decrease section of the wellbore stays uncased, permitting hydrocarbons to go with the flow at once from the formation into the well. Open gap completions are frequently used in able formations the place borehole balance is no longer a concern.
- Advantages:
Minimal hardware, reducing cost
High productivity potential in homogeneous formations
- Disadvantages:
Limited control over production zones
Higher risk of formation damage if conditions change
2. Cased and Perforated Completion
This is the most common completion method, where steel casing is cemented in place, and specific production zones are accessed by perforating the casing with controlled charges.
- Advantages:
Precise manipulate over manufacturing zones
Better wellbore stability and integrity
Flexibility for stimulation operations (e.g., hydraulic fracturing)
- Disadvantages:
Higher upfront cost
Requires distinct reservoir know-how for exceptional perforation placement
3. Liner Completion
Liners are short casing sections set in the reduce area of the wellbore, supplying a hybrid reply between open hole and fully cased completions. They provide mechanical assist whilst retaining reservoir access.
- Advantages:
Reduced casing costs compared to full casing
Maintains borehole stability
Adaptable to complex well trajectories
The selection of completion type depends on formation properties, production targets, economic factors, and long-term field development strategies.
What is Well Completion and Workover?
Well completion prepares a top for preliminary production, workover refers to protection or remedial operations carried out on an current well to restore, enhance, or alter its performance. Workovers can be minor, involving flooring interventions, or major, requiring re-entry into the wellbore.
Common reasons for workover include:
- Replacing damaged equipment (e.g., tubing, packers)
- Cleaning out wellbore obstructions
- Enhancing production through stimulation (acidizing, fracturing)
- Converting a well from production to injection, or vice versa
What is the Well Completion Design Process?
Designing an effective well completion system is a multidisciplinary process requiring collaboration between geologists, reservoir engineers, and drilling experts. The goal is to tailor the completion to the reservoir’s characteristics while ensuring technical and economic efficiency.
Key Steps in Completion Design:
1. Reservoir Evaluation:
Analyze formation properties, pressure, permeability, and fluid characteristics.
2. Production Objectives:
Define target flow rates, recovery factors, and lifecycle expectations.
3. Completion Selection:
Choose between open hole, cased and perforated, or liner completions based on reservoir complexity.
4. Well Integrity Planning:
Design barriers, security valves, and manage structures to mitigate risks
5. Sand Control & Stimulation Considerations:
Assess the want for sand screens, gravel packs, or hydraulic fracturing to decorate productivity.
6. Economic Feasibility:
Balance technical overall performance with price concerns to make sure venture viability.
Join PetroSync and Advance Through Certified Training
For professionals and decision-makers in the oil and gasoline sector, staying previously requires greater than actually operational information – it needs mastery of existing day completion technologies, properly design principles, and intervention strategies.
PetroSync gives globally diagnosed education packages tailor-made for engineers, managers, and executives in search of to beautify their information in nicely completion and manufacturing optimization. Through hands-on workshops and expert-led sessions, you will attain insights into:
- Latest properly completion techniques
- Cost-effective workover strategies
- Real-world case research to improve discipline productivity
- Compliance with enterprise requirements and protection protocols
Equip your self with the abilities to optimize your company’s manufacturing overall performance and prolong properly lifestyles effectively. Explore upcoming well engineering and production courses at PetroSync Drilling & Well Engineering Training.
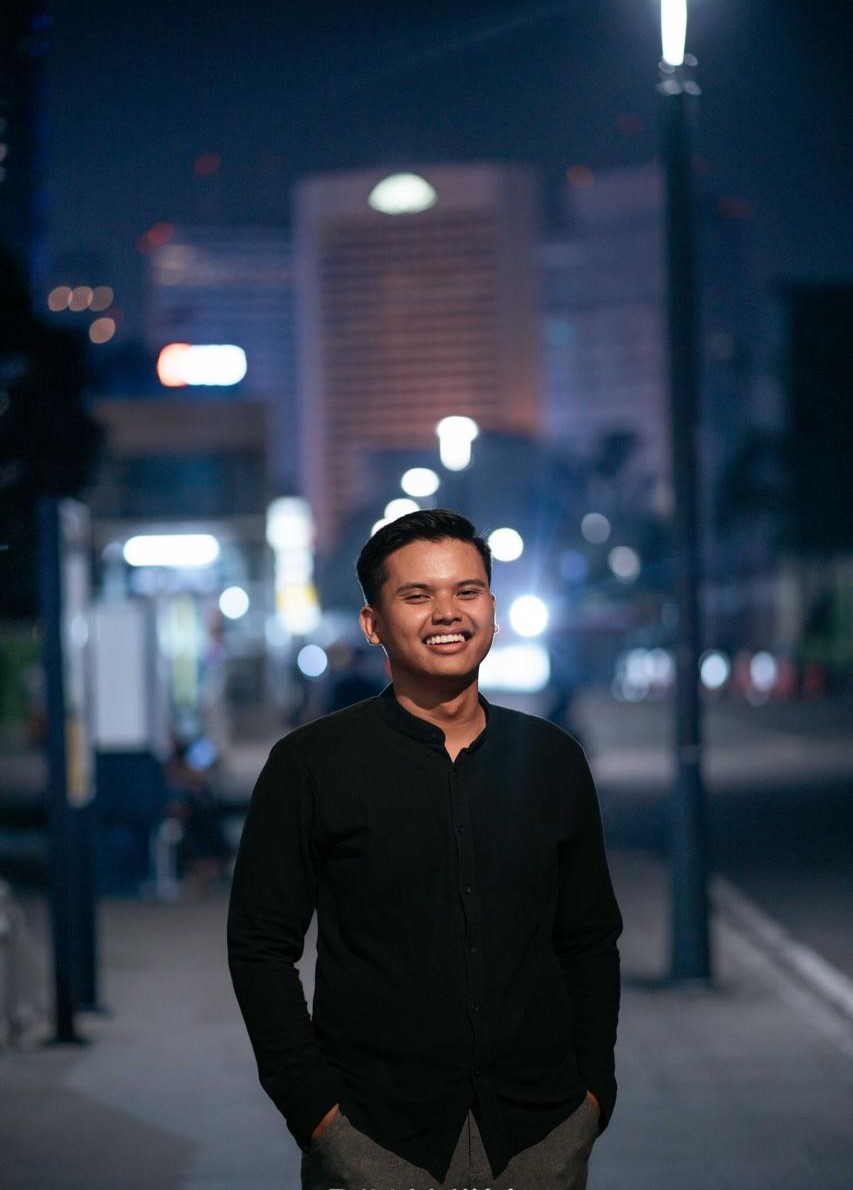
Results-oriented and thorough SEO specialist with extensive experience in conducting keyword research, developing and implementing digital website promotion strategies and plans, managing campaigns to develop company websites in the digital world, excellent knowledge of marketing techniques and principles, and attentive strong attention to detail.