Fired heaters are like the engines of refineries, powering energy creation. They’re responsible for heating things in the refining process, turning raw materials into valuable products. In this guide, we’ll look closely at fired heaters in refineries, discussing the kinds available, how they operate, the importance of maintenance, their impact on the environment, and what the future holds for them.
What Is Fired Heaters?
Fired heaters are industrial devices designed to generate heat by burning fuels such as natural gas or oil. These heaters operate within an insulated enclosure that utilizes the heat produced by fuel combustion to heat fluids contained inside coils. Fired heaters play a crucial role in various applications, including heating processes in refineries, chemical plants, and other industries.
Contributing to the efficient operation of industrial processes requiring elevated temperatures. This process involves a controlled combustion reaction within the fired heater, creating high-temperature gases. These gases then transfer their heat to the coils, warming the fluids circulating within. The process directs the heated fluids, often in the form of oil or water.
To different parts of industrial operations for applications such as steam generation or maintaining specific temperatures in chemical reactions. Fired heaters come in various types, each tailored to specific industrial needs. Whether used in petrochemical refineries or manufacturing plants, their versatility and efficiency make them indispensable for sustaining crucial processes.
What Are The Functions of Fired Heaters?
1. Heat Generation
Fired heaters are like industrial furnaces. They burn fuels such as natural gas or oil in a controlled manner, creating intense heat through a process called combustion. This heat generation is fundamental for many industrial activities that require high temperatures.
2. Fluid Heating
Inside the fired heater, there are coils. These coils get heated by the intense heat generated during combustion. Fluids, often oil or water, flow through these coils, absorbing the heat. This process warms the fluids, turning them into valuable resources for various industrial uses.
3. Steam Generation
One of the crucial uses of the heated fluids is steam generation. The hot fluids are directed to a separate part of the industrial process where they turn into steam. Steam is versatile and is used in many industries for tasks like powering turbines or heating spaces.
4. Temperature Maintenance
Fired heaters play a role in ensuring that specific temperatures are maintained in industrial processes. This is especially important in chemical reactions where precise temperatures are often required for the reactions to occur effectively.
5. Process Optimization
By providing the necessary high temperatures, fired heaters contribute to the efficient running of industrial processes. This optimization is crucial for industries to achieve their production goals and maintain consistent product quality.
6. Versatile Industrial Applications
Fired heaters find applications in various industries, including refineries and chemical plants. Their adaptability allows them to be used in different settings, contributing to the diverse needs of industrial processes. Understanding these functions showcases the importance of fired heaters in industrial settings, where their reliable operation is essential for the success of various manufacturing and production processes.
What Are The Components of Fired Heaters?
1. Casing
The casing of a fired heater serves as the outer protective shell, enveloping and safeguarding the internal components. Its primary function lies in providing structural support and insulation, preventing heat loss to the surrounding environment. This outer layer ensures the fired heater’s durability and efficiency by containing the heat generated within the system.
2. Tubes
Within the fired heater, tubes act as hollow conduits through which hot gases pass, facilitating the transfer of heat to the process fluid. These metal pipes play a crucial role in the exchange of thermal energy, allowing the combustion gases to impart their heat to the material being heated, contributing to the overall efficiency of the system.
3. Return Bends
Return bends, shaped like U-shaped tubes, redirect the flow of hot gases back through the fired heater. This design enhances heat transfer efficiency by ensuring that combustion gases make multiple passes within the system. By facilitating this redirection, return bends contribute to optimizing the utilization of heat generated during the combustion process.
4. Tube Supports
Tube supports are essential structures that hold and stabilize the tubes within the fired heater. They maintain proper spacing and alignment, preventing issues such as tube sagging or damage. By ensuring the stability of the tubes, these supports contribute to the longevity and reliability of the overall heating system.
5. Burners
Burners within the fired heater are devices responsible for mixing fuel and air for combustion, producing the flame required to generate heat. Playing a pivotal role in initiating and sustaining the combustion process, burners are critical components that directly impact the efficiency and effectiveness of the heating system.
6. APH/SAPH (Air Preheater/Steam Air Preheater)
APH/SAPH units, or Air Preheaters and Steam Air Preheaters, are heat exchangers that preheat combustion air by utilizing waste heat from the flue gas. This process recovers and utilizes heat that would otherwise be lost, enhancing overall efficiency and making the fired heater more energy-efficient.
7. ID & FD Fans (Induced Draft & Forced Draft Fans)
Induced Draft (ID) and Forced Draft (FD) fans are responsible for controlling the flow of air and gases within the fired heater. These fans play a crucial role in maintaining the proper balance of air and fuel, ensuring efficient combustion and contributing to the overall effectiveness of the heating system.
8. Pilot
A pilot flame, smaller in size, serves as the ignition source for the main burners when the fired heater is started. This component is instrumental in initiating the combustion process in the main burners, ensuring a controlled and reliable start-up.
9. Radiant, Shield, and Convection Zone
The fired heater consists of distinct zones, namely radiant, shield, and convection, each contributing to the heat transfer process in unique ways. Radiant zones absorb and radiate heat, shield zones protect sensitive components, and convection zones enhance overall heat transfer efficiency.
10. Duct
Ducts within the fired heater are passages or channels that guide combustion gases from the burners to the heat exchanger. They play a crucial role in directing the flow of hot gases through the system, ensuring an efficient and controlled movement within the heating unit.
11. Damper
Adjustable dampers are plates or valves within the fired heater that control the airflow, regulating the intensity of combustion. By adjusting the damper, operators can maintain optimal operating conditions, ensuring efficient and controlled combustion processes.
12. Stack
The stack serves as the vertical structure through which combustion gases exit into the atmosphere. The system safely releases combustion byproducts into the air, preventing environmental or safety hazards associated with disposing of such gases.
13. Refractory
Refractory materials line the interior of the fired heater, offering heat resistance and protection to structural components. This lining safeguards against extreme temperatures, preventing damage to the inner structure and enhancing insulation, crucial for the longevity and reliability of the heating system.
14. Louvers/Air Registers
Louvers or air registers are adjustable openings within the fired heater that control the inflow of air. By regulating the air supply for combustion, these components ensure optimal efficiency and heat transfer, contributing to the overall performance of the heating system.
Fired heaters are crucial in the oil and gas industry, serving as essential tools for heating materials in various processes like refining and petrochemical operations. These heaters ensure precise heat transfer and efficient combustion. If you are a petroleum engineer, you must grasp the complexities of fired heaters, as your expertise directly impacts the safety, reliability, and efficiency of operations in the oil and gas sector
If you want to boost your fired heater know-how, PetroSync offers specialized training course. These sessions dive into the details of fired heaters, providing comprehensive insights into their design, operation, and maintenance.
By joining this Fired Heaters Training by PetroSync, you can get valuable opportunities to stay updated on industry practices and enhance your fire-heater expertise. Claim your seat to unlock a wealth of knowledge and elevate your proficiency in this crucial aspect of the oil and gas sector.
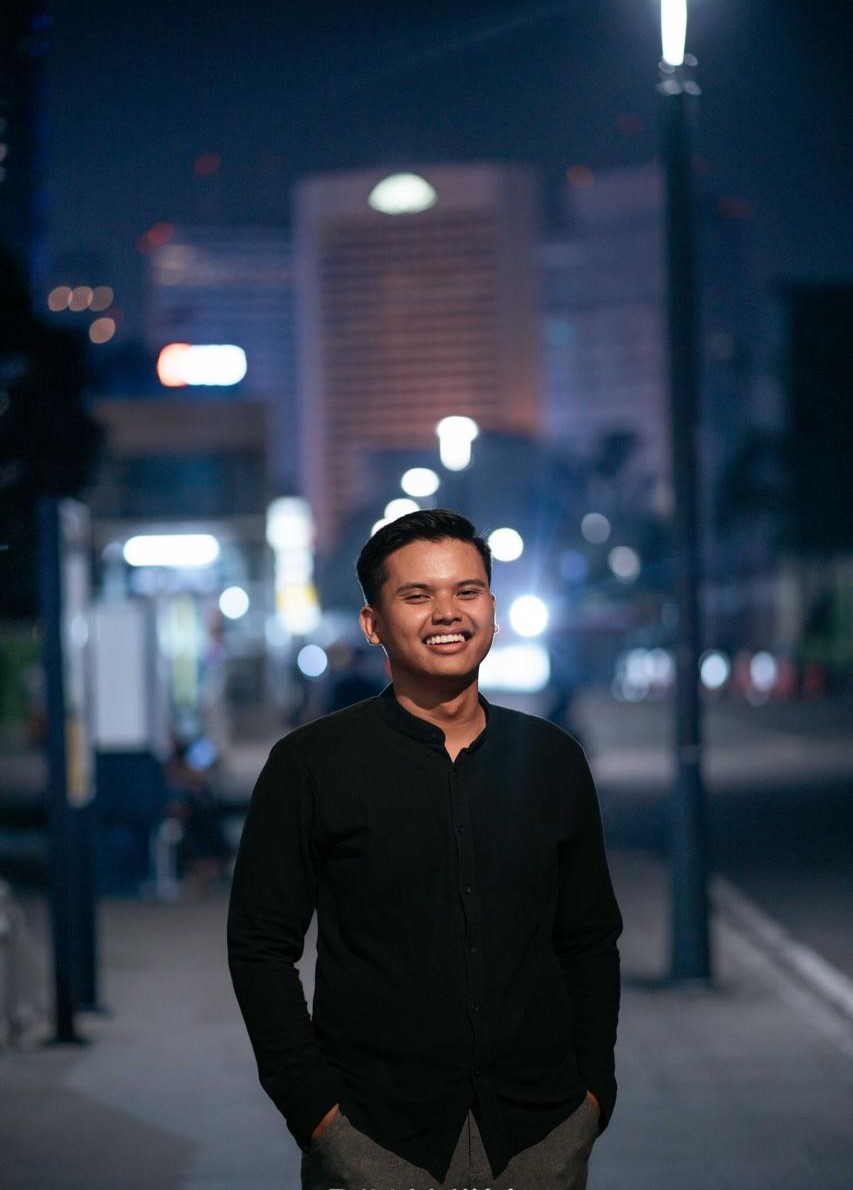
Results-oriented and thorough SEO specialist with extensive experience in conducting keyword research, developing and implementing digital website promotion strategies and plans, managing campaigns to develop company websites in the digital world, excellent knowledge of marketing techniques and principles, and attentive strong attention to detail.