Understanding remaining life calculation is vital because it allows you to predict when equipment might fail or require maintenance. As an authorized inspector, your primary responsibility is to determine when equipment needs inspection. Typically, to establish an accurate inspection schedule, you must be proficient in measuring both corrosion rates and remaining life calculation.
What Is the Remaining Life Calculation?
Remaining life calculation refers to the process of estimating the amount of time a piece of equipment or machinery is expected to continue functioning effectively before reaching the end of its useful life. This calculation takes into account factors such as the equipment’s age, condition, maintenance history, and expected future usage. By performing remaining life calculations, you can make informed decisions about when to repair, replace, or retire equipment to optimize performance, minimize downtime, and ensure safety in industrial settings.
How Do You Calculate Remaining Life for Piping?
To calculate the remaining life for piping system, you will need to follow a specific formula:
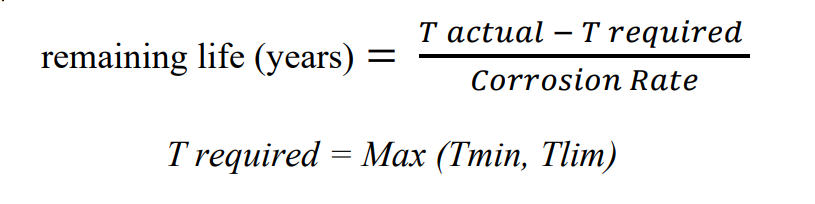
Following the above calculation, you need to determine the difference between the actual thickness of the pipe and the required thickness for safe operation. This required thickness is based on factors like the material of the pipe and the operating conditions, such as temperature and pressure. The actual thickness is measured during inspections, while the required thickness is calculated using design formulas and considering allowances for corrosion and mechanical factors.
The minimum required thickness is determined by standards like ASME B31.3, and the limiting thickness is specified by API 579. By comparing these values and accounting for corrosion rates, you can calculate the remaining life of the piping system in years. This assessment aims to ensure that the piping can continue operating safely within normal conditions for an extended period, typically targeting a life extension of 20 years from the assessment date.
Why Remaining Life Calculation Is Important?
Calculating the remaining life of piping systems is crucial for several reasons, primarily centered around safety, efficiency, and cost-effectiveness.
1. Safety
Piping systems are integral components of various industrial processes, including those in high-risk industries such as oil and gas, petrochemicals, and power generation. Any failure or malfunction in these systems can have catastrophic consequences, leading to accidents, injuries, environmental damage, and even loss of life.
2. Asset Integrity
Piping systems represent significant investments for industries, both in terms of installation costs and ongoing maintenance expenses. Understanding the remaining life of these assets allows organizations to optimize maintenance schedules, allocate resources effectively, and extend the lifespan of their infrastructure.
3. Regulatory Compliance
Many industries are subject to strict regulatory requirements governing the inspection, maintenance, and operation of piping systems. Compliance with these regulations is essential for ensuring environmental protection, public safety, and legal liability.
4. Cost Saving
Conducting routine inspections and maintenance activities on piping systems can be resource-intensive and costly. By accurately assessing the remaining life of these assets, organizations can prioritize maintenance activities based on actual condition rather than arbitrary schedules.
5. Reliability and Performance
Piping systems play a critical role in transporting fluids, gasses, and other materials essential for industrial processes. Any degradation or deterioration in these systems can compromise their reliability and performance, leading to operational inefficiencies, production losses, and quality issues.
In summary, calculating the remaining life of piping systems is essential for maintaining safety, optimizing asset integrity, ensuring regulatory compliance, achieving cost savings, and preserving reliability and performance in industrial operations.
FAQs About Remaining Life Calculation
1. How Do You Calculate Corrosion Rate?
To calculate corrosion rate, you typically measure the thickness or weight loss of the metal surface that has corroded uniformly over the exposed area. The corrosion rate (R) is calculated using the formula R = d/t expressed in µm/y, where d represents the total thickness or weight loss in micrometers, and t represents the time in years.
This rate can be expressed in various units such as micrometers per year, grams per square meter, milligrams per decimeter squared per day, or ounces per square foot. It’s important to note that comparing corrosion rates calculated over short periods may not provide accurate results due to fluctuating environmental conditions.
2. How Do You Calculate Fitness for Service Assessment?
To calculate fitness for service assessment, you start by examining the thickness profile and minimum measured thickness using historical inspection data. Then, you calculate the wall thickness to be used (Tc) by considering the nominal wall thickness from the manufacturer and adding the future corrosion allowance for each piping line.
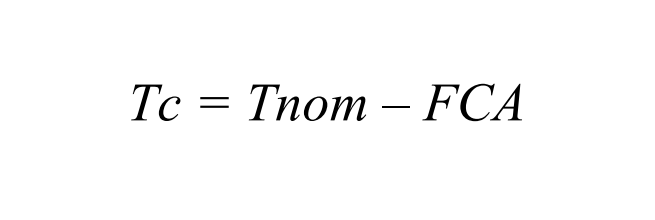
Once you have the Tc, you compute the remaining thickness ratio (R) using the formula provided below. This process helps determine the structural integrity and remaining lifespan of the piping system, ensuring safe and reliable operation.
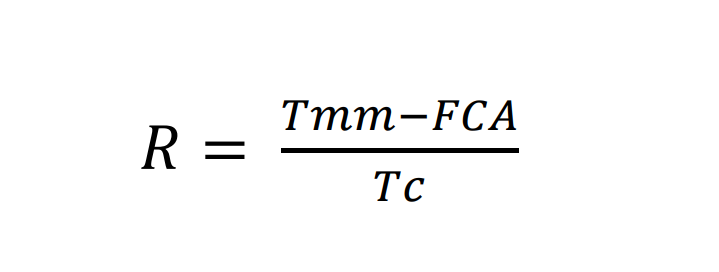
In conclusion, the calculation of remaining life for piping systems is a critical aspect of asset management in various industries. By accurately assessing the remaining life of piping infrastructure, organizations can prioritize maintenance activities, ensure regulatory compliance, optimize asset integrity, and enhance safety and reliability. This proactive approach to asset management not only minimizes operational risks and costs but also prolongs the lifespan of critical infrastructure, ultimately contributing to the overall success and sustainability of industrial operations.
Credit header image: Vecteezy
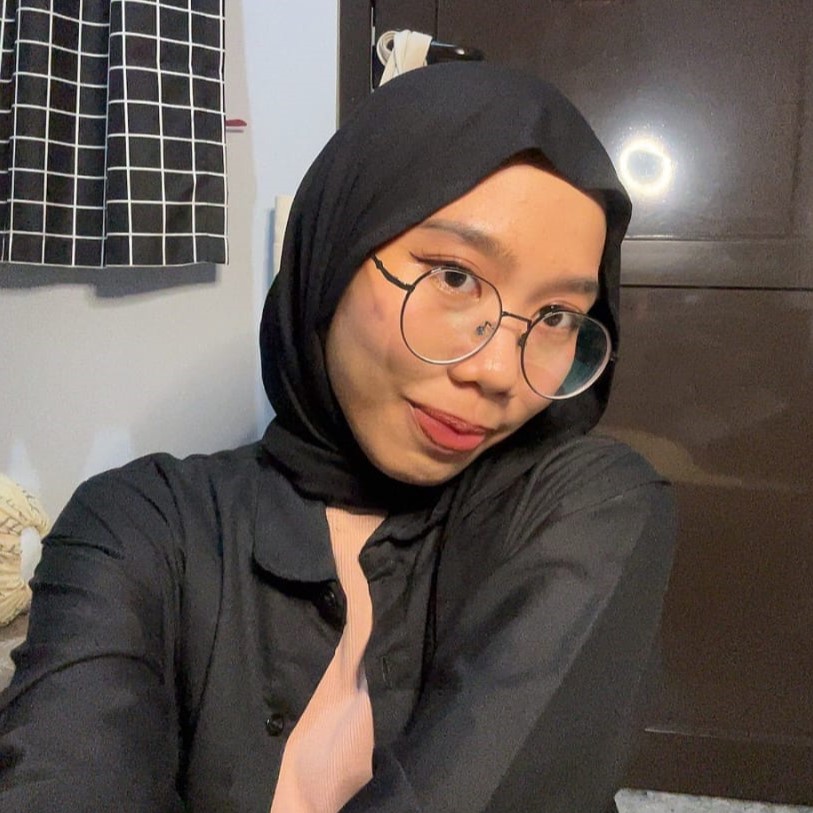
SEO specialist by day, fact-checker by night. An avid reader and content writer dedicated to delivering accurate and engaging articles through research and credible sources.