Everything from the enormous refineries that process crude oil to the vast pipelines that run beneath oceans is built on steel and aluminum. Behind the strength of these materials, however, lies a slow but persistent force called corrosion, which, if ignored, can cause disastrous breakdowns.
In this high-stakes environment, corrosion engineers are the unsung heroes defending the safety and integrity of vital infrastructure. Despite the fact that they are sometimes overlooked, corrosion engineers’ efforts affect every barrel that is processed safely, every instance of downtime avoided, and every dollar saved on repairs.
What precisely does a corrosion engineer do, and why is corrosion engineering growing more and more significant?
What Does a Corrosion Engineer Do?
A corrosion engineer is primary goal is to shield materials – particularly metals – from the damaging effects of corrosion. This responsibility is even more important in the oil and gas industry, where harsh environmental conditions including high pressure, exposure to seawater, and chemical reactions are commonplace.
Their work is varied and frequently entails:
- Risk assessment and prediction for corrosion in tanks, pipelines, and structural elements
- Creating systems that prevent corrosion, such as cathodic protection and coatings
- Choosing materials that are resilient in challenging conditions
- As failures occur, looking into them and suggesting solutions to stop them from happening again
- Working together with multidisciplinary groups to incorporate corrosion control from design to upkeep
Although it may not be evident, a single poor material selection could cause a costly and hazardous leak or reduce a pipeline’s lifespan by decades. The purpose of corrosion engineers is to prevent that from ever occurring.
How Do You Become a Corrosion Engineer?
Becoming a corrosion engineer isn’t a career you stumble into. It typically begins with a degree in engineering – usually in chemical, materials, or mechanical disciplines. But formal education is just the start.
To truly specialize in corrosion, engineers often pursue certifications such as:
- NACE certifications (e.g., Cathodic Protection, Coating Inspector programs)
- API 571 (Damage Mechanisms Affecting Fixed Equipment)
- API 580 (Risk-Based Inspection)
These programs offer in-depth training on corrosion science, inspection techniques, and risk mitigation. Practical experience is just as important. Aspiring corrosion engineers are exposed to real-world situations through internships or employment in chemical processing facilities, offshore platforms, or refineries.
Every environment imparts a unique set of teachings that are frequently molded by ongoing adaptation and trial and error. Senior positions are frequently attained by engineers who pursue ongoing education, look for mentorship, and keep up with technology developments. In these positions, they assist in establishing safety and dependability standards for entire operations.
Why Is Corrosion Engineering Important?
It’s easy to underestimate corrosion – until it causes a million-dollar shutdown or worse, a catastrophic accident. Globally, corrosion is responsible for over $2.5 trillion in losses annually, according to data from the Association for Materials Protection and Performance (AMPP). That’s roughly 3-4% of the world’s GDP.
But it’s not just about money.
Unchecked corrosion has led to:
- Oil spills contaminating marine environments
- Explosions due to failed pressure vessels
- Structural collapses in offshore rigs
Beyond the financial toll and environmental harm, there’s also a human cost. That’s why corrosion engineering plays such a central role in asset integrity and operational safety.
Importantly, many of these failures are preventable. Studies suggest that 15% – 35% of corrosion-related losses can be avoided through effective prevention and management strategies. That’s the power of having the right corrosion engineers in place.
What Is the Role of a Corrosion Engineer?
Corrosion engineers work at the intersection of science, engineering, and operations. Their responsibilities span both proactive and reactive functions:
- Designing protection systems like cathodic protection or barrier coatings
- Advising on optimal material selection for specific environments
- Conducting failure analysis to determine causes of material breakdown
- Implementing monitoring systems to detect early signs of corrosion
- Developing and enforcing internal standards for corrosion control
Their role is not static. As industries evolve and materials change, corrosion engineers must adapt – staying informed about new technologies and emerging risks. Increasingly, they’re also involved in sustainability efforts, helping companies extend asset life and reduce environmental impact through better material management.
In high-risk sectors like oil and gas, having an experienced corrosion engineer on the team isn’t optional – it’s essential.
Emerging Technologies in Corrosion Monitoring
Today’s corrosion engineers are more than just scientists; they are also data analysts, early users of new technologies, and innovators. The monitoring tools are getting more advanced and have the ability to forecast results as the industry goes through a digital transition.
For instance:
- IoT sensors installed on pipelines can now track corrosion rates in real-time
- AI-driven software can forecast when a component is likely to fail, enabling preventive maintenance
- Digital twins allow engineers to simulate corrosion scenarios before any real-world consequences unfold
According to a 2021 study in the Journal of Loss Prevention in the Process Industries, AI-based maintenance solutions have reduced unexpected downtime in some refining operations by as much as 35%. These are not just futuristic solutions – they’re tools that are being implemented now, offering corrosion engineers new ways to protect assets.
Enhance Your Career with PetroSync Training: Join the Experts
The best option for engineers who wish to learn more about this topic or who wish to switch jobs and work in a high-demand, high-impact role is to invest in the necessary training. Here’s where PetroSync comes in handy. Two of PetroSync’s industry-focused training courses, API 571 and API 580, are designed to provide you hands-on experience that you can utilize immediately.
Every course prepares you for the challenges that lie ahead by combining theory, case studies, and useful tools. The presenters are seasoned experts who have worked in the industry for years. In addition to helping you stand out in a competitive employment market.
PetroSync’s corrosion courses have a significant impact on the integrity of industrial processes, whether your goal is to increase your technical expertise or get ready for certification.
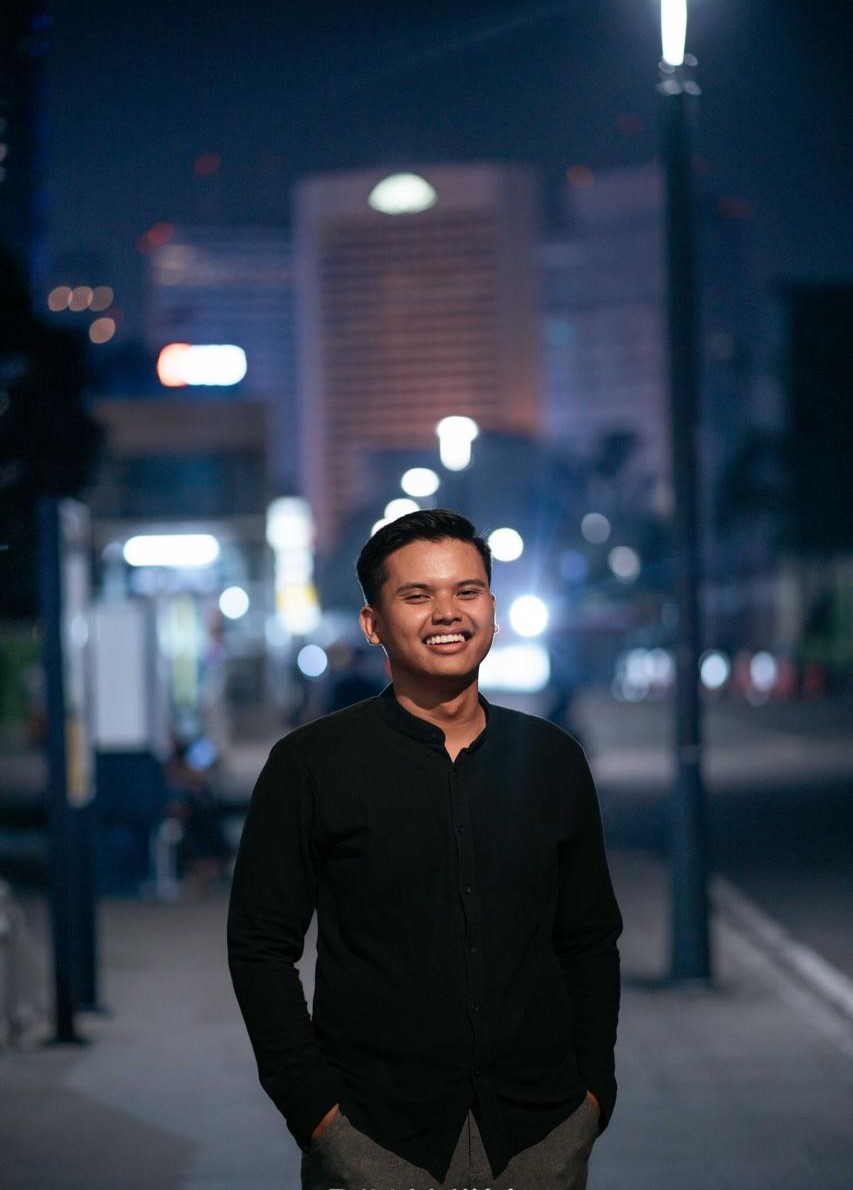
Results-oriented and thorough SEO specialist with extensive experience in conducting keyword research, developing and implementing digital website promotion strategies and plans, managing campaigns to develop company websites in the digital world, excellent knowledge of marketing techniques and principles, and attentive strong attention to detail.