Embarking on the journey through refining processes reveals the vital role of fired heaters in ensuring efficient and precise operations within these industrial settings. This article thoroughly explores the fired heaters application in refineries, uncovering their importance in processes such as heating hot oil and converting heavy hydrocarbons.
What Is A Fired Heater?
A fired heater is an industrial device used for heating various fluids, often in the context of oil refineries. Its primary purpose is to transfer heat to a fluid (commonly a hydrocarbon-based substance) by burning fuel.
This combustion process occurs in a combustion chamber within the fired heater, generating hot gasses. These hot gasses then pass through tubes or coils that contain the fluid to be heated. As the fluid circulates through these tubes or coils, it absorbs the heat from the combustion gasses, causing its temperature to rise.
In refineries, fired heaters play a crucial role in several processes. One key application is in the refining of crude oil. The crude oil contains different hydrocarbons, and some need to be heated to specific temperatures for various refining processes.
Fired heaters facilitate these temperature adjustments, aiding in the separation, conversion, and treatment of different components within the crude oil. Additionally, fired heaters are integral to processes such as distillation, cracking, and reforming, where precise temperature control is essential for the efficient production of refined products like gasoline, diesel, and various petrochemicals.
What Are The Application of Fire Heaters?
Some of the applications of fire heaters as follows.
1. Hot Oil
Fired heaters are commonly used in systems that require heating of hot oil. This application is crucial in various industrial processes where maintaining a specific temperature in the hot oil is essential for efficient operations. Hot oil heaters find use in industries such as chemical processing, asphalt production, and others where precise temperature control is required.
By utilizing fired heaters to maintain precise temperatures in the hot oil, industries can ensure efficient heat transfer, enhancing the performance of systems such as heat exchangers and reactors. This leads to improved process efficiency, reduced energy consumption, and the ability to maintain optimal operating conditions in diverse applications.
2. Crude
In the refining of crude oil, fired heaters play a pivotal role. The application of fired heaters is for heating crude oil to specific temperatures in processes like distillation. This heating is essential for separating the various components of crude oil.
Heating crude oil to specific temperatures in processes like distillation effectively separates its components based on their boiling points. This enhances the overall efficiency of the refining process, allowing for the production of essential products like gasoline, diesel, and various petrochemicals.
3. Vacuum
Vacuum distillation units use the second fired heaters application to heat crude oil under reduced pressure. This application is critical for separating heavier components from crude oil. This process improves the quality of refined products by removing heavier fractions, contributing to the production of lighter, more valuable products.
4. Delayed Coker
Fired heaters are an integral part of delayed coking units. In these units, high temperatures are applied to convert heavy residual oils into valuable products like petroleum coke and lighter hydrocarbons. The fired heater ensures the required temperatures for effective coking reactions.
The application of fired heaters in delayed coking units provides the benefit of facilitating the conversion of heavy residual oils. This process allows industries to extract additional value from heavier feedstocks, contributing to the optimization of overall refining operations.
5. Visbreaker
Visbreaking units use fired heaters to heat heavy hydrocarbons, causing them to break down into lighter products. Breaking down heavy hydrocarbons into lighter products lowers the viscosity of crude oil, making it easier to refine further.. This enhances the overall efficiency of refining operations.
6. Reformer
Reforming processes rely on fired heaters to transform hydrocarbons into more valuable products. Reformer heaters play a key role in providing the heat required for the chemical reactions that enhance the quality and yield of products like hydrogen and high-octane gasoline.
7. Hydrocrackers
Hydrocracking units employ fired heaters to break down heavy hydrocarbons into lighter, more valuable products. These heaters ensure the elevated temperatures needed for the hydrocracking reactions to occur, resulting in the production of valuable fuels. This process contributes to the production of valuable fuels with improved properties, including higher cetane numbers in diesel fuel, resulting in enhanced overall product quality.
8. Steam Reformers
Fired heaters are utilized in steam reforming processes for the production of hydrogen. These heaters play a crucial role in providing the necessary heat for the endothermic reactions involved in converting hydrocarbons into hydrogen and carbon monoxide. These heaters enable steam reforming reactions, efficiently producing hydrogen for ammonia and refining applications.
9. Ethylene Cracking Heaters
In the production of ethylene through cracking processes, operators use fired heaters to provide the high temperatures needed to break down hydrocarbons into ethylene and other valuable products. These heaters ensure the efficiency of the cracking reactions, contributing to the production of ethylene for various industrial applications.
This contributes to the efficient production of ethylene, a key building block for the petrochemical industry. Precise temperature control by these heaters optimizes ethylene production, boosting process efficiency and increasing product yield.
Fired heaters in refining optimize essential processes, playing a vital role in producing high-quality refined products. From heating hot oil to facilitating the distillation of crude oil, fired heaters provide the necessary heat for crucial operations.
Join PetroSync Training and Network with Industry Leaders
For a comprehensive understanding of fired heaters and their pivotal role in general refinery service, consider the API 560 Training offered by PetroSync. This training program provides you with in-depth insights into the principles, design, and operation of fired heaters, equipping you with the knowledge necessary to excel in refining. industry.
This training enhances your expertise in optimizing fired heater performance, ensuring safe and efficient refinery operations. By enrolling in this program, you’ll gain valuable insights, practical skills, and a solid foundation in the critical role that fired heaters play in refining processes. Take the opportunity to advance your knowledge and expertise by participating in the API 560 Training with PetroSync, and empower yourself for success in the dynamic field of refining.
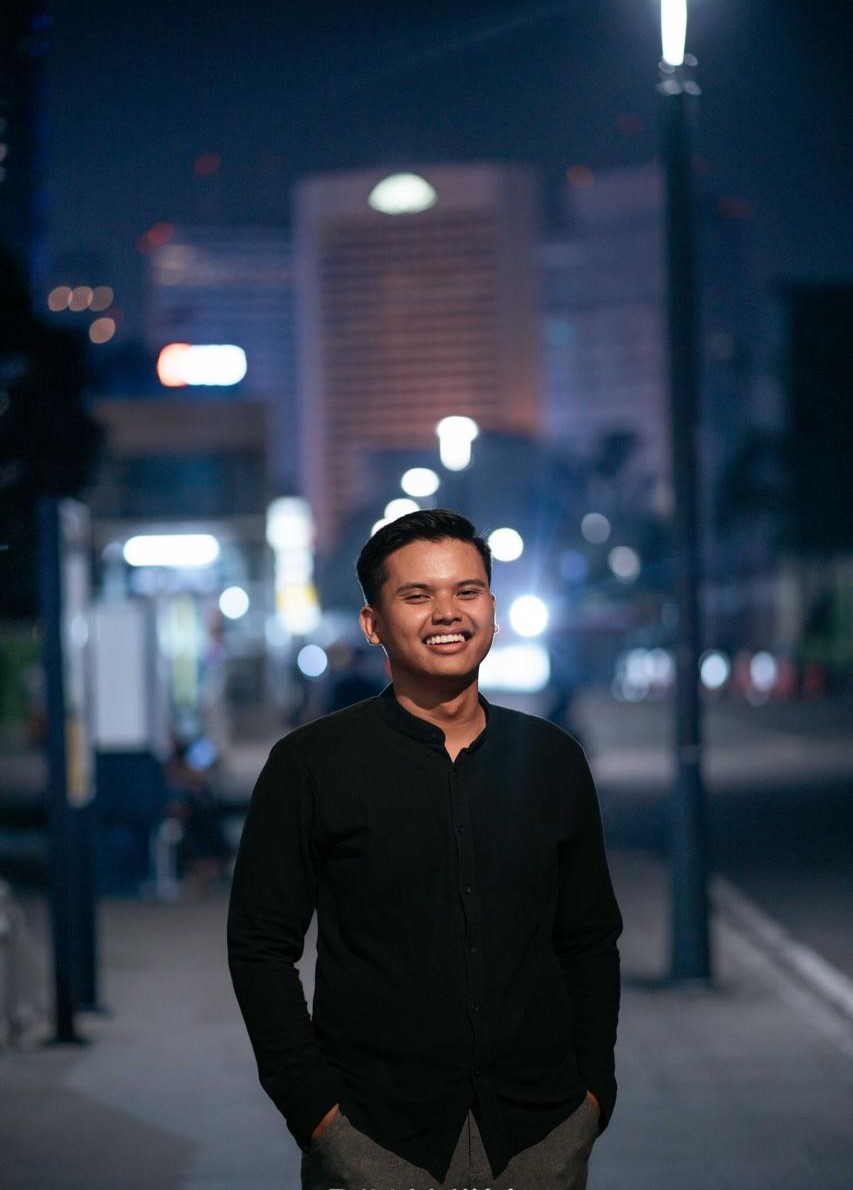
Results-oriented and thorough SEO specialist with extensive experience in conducting keyword research, developing and implementing digital website promotion strategies and plans, managing campaigns to develop company websites in the digital world, excellent knowledge of marketing techniques and principles, and attentive strong attention to detail.