Pressure vessels have become a widely used equipment in various industries. During the design phase of a pressure vessel, the manufacturer sets the MAWP (maximum allowable working pressure) which acts as a boundary to ensure the vessel’s ability to handle the highest anticipated pressure. In this article, we will dig deeper into the basics, calculations, and benefits of MAWP.
What Is Maximum Allowable Working Pressure (MAWP)?
American Petroleum Institute published API 579 fitness-for-service standard where “Maximum Allowable Working Pressure” or MAWP is highlighted. API 579 provides guidelines and procedures for determining the MAWP and assessing equipment’s fitness-for-service, especially when it has exceeded its design life or experienced damage or deterioration.
What Is The Difference Between MAWP and Design Pressure?
Design pressure is the maximum pressure that the equipment is designed to withstand. It considers various factors such as the materials used, temperature, and other operating conditions. The thickness of the equipment’s walls and other components is determined based on the design pressure to ensure that it can safely withstand the expected pressure.
MAWP, on the other hand, is the maximum safe operating pressure at which the equipment can operate without causing damage or failure. It is determined by considering the Design Pressure and other factors such as safety margins, fatigue, and corrosion allowances. The MAWP is always lower than the Design Pressure to provide a safety margin.
In short, the MAWP is always set lower than the design pressure to prevent equipment failure or damage. Therefore, the key difference between the two is that Design Pressure is the maximum pressure equipment is designed to withstand. In contrast, MAWP is the maximum pressure that equipment can operate safely.
How To Calculate MAWP?
The following equation (applies to cylindrical vessels) is used to find the MAWP:
(Credit: Fitness-For-Service Assessment for Pressure Equipment in Chemical Plants, sumitomo-chem.co.jp)
In API 579 or ASME FFS-1, the term MAWP pertains to the maximum permissible operating pressure of equipment under the assumption that there is no metal loss. The formula used to calculate MAWP includes parameters such as σa, which represents the allowable stress during design, E, which stands for the weld joint efficiency, and Ri, which denotes the inside diameter of the equipment.
The calculation of MAWPr, which stands for maximum allowable working pressure for equipment with metal loss in a particular area, is determined by using the following formulas:
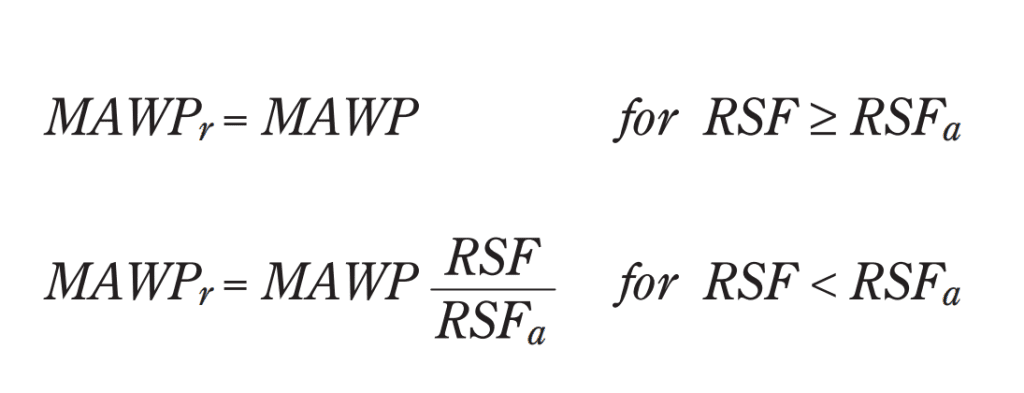
In accordance with API/ASME FFS-1 standards, pressure equipment that has suffered from localized metal loss can be safely operated at a pressure lower than or equal to MAWPr. The value of MAWPr is determined based on certain formulas, and RSFa is the permissible limit for the remaining strength factor (RSF) used in those formulas.
What Are The Benefits of Following MAWP and Design Pressure?
Following the Maximum Allowable Working Pressure (MAWP) and Design Pressure is very important for pressure equipment. There are three key benefits a company can get for following the industry regulation of MAWP and design pressure:
1. Safety and Reliability
Pressure equipment can operate safely and reliably under normal conditions, thereby reducing the risks of accidents, injuries, and equipment failure. This minimizes the chances of costly repairs, equipment downtime, and harm to workers.
2. Ability to Handle Pressure Surges
MAWP and Design Pressure requirements specify the maximum pressure that pressure equipment can handle, preventing any damage or failure that could occur due to overpressure during operation. This ensures that the equipment can handle unexpected pressure surges or spikes and operates reliably.
3. Compliance with Industry Standards and Regulations
By following the standard, any manufacturer can ensure that pressure equipment meets industry standards and regulations. This improves the overall safety and reliability of the equipment and prevents legal liabilities and potential fines for non-compliance with relevant regulations.
Knowing the concept of MAWP (Maximum Allowable Working Pressure) and how to calculate it is crucial in ensuring the safety and reliability of pressure vessels and piping systems. To calculate the MAWP, you must have a deep understanding of pressure vessel and piping codes and standards, as well as the ability to perform complex calculations.
PetroSync’s API 579 – Fitness For Service training course provides the attendees with the knowledge and skills needed to perform fitness-for-service evaluations on pressure equipment. As part of this training, you will learn about the concept of MAWP and how to calculate it, as well as other important topics related to pressure equipment safety and reliability.
You can also apply the disciplines of material science, stress analysis, NDT, and inspection practices directly to your related field. Sign up for PetroSync’s API 579 training and enhance your skills and knowledge in running, repairing, and replacing pressure equipment with PetroSync!
Credit header image: Freepik.com
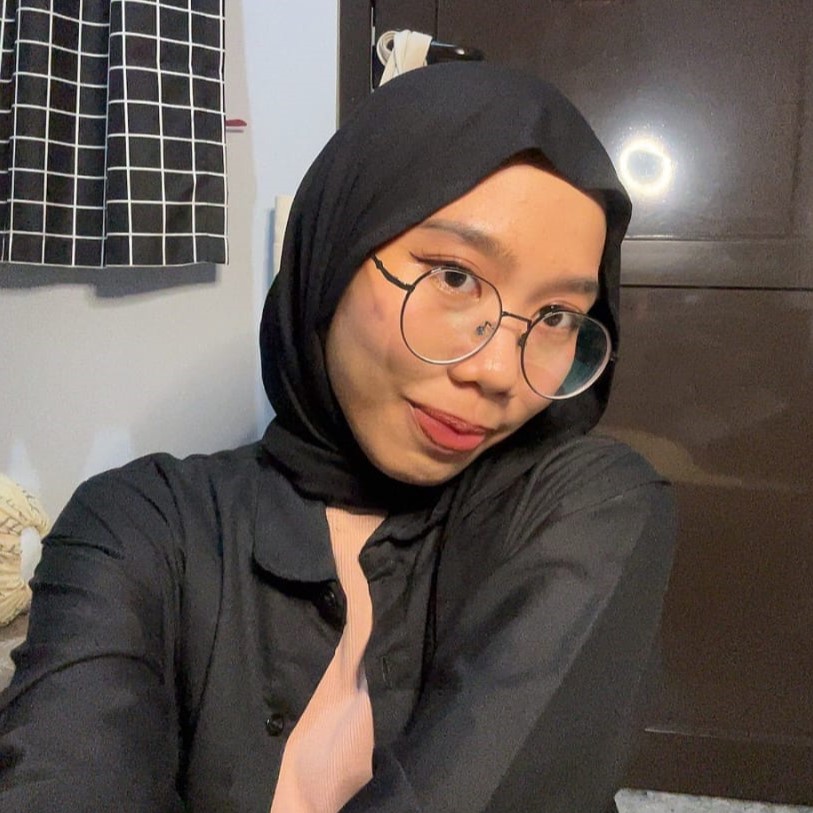
SEO specialist by day, fact-checker by night. An avid reader and content writer dedicated to delivering accurate and engaging articles through research and credible sources.