In today’s changing industrial world, using predictive maintenance is important for businesses to manage their assets well and keep operations running smoothly. This article will explain the basics of predictive maintenance, its benefits, and how it is done. By learning about predictive maintenance, you will understand how it helps to make equipment more reliable, reduces downtime, and boosts productivity for different industries.
What Is Predictive Maintenance?
Predictive maintenance is a method used by industries to predict when equipment failure might occur and to prevent its occurrence by performing maintenance. It involves collecting data from the equipment, analyzing it using various techniques like machine learning or statistical modeling, and then making predictions about when maintenance will be needed.
This proactive approach allows businesses to schedule maintenance tasks at optimal times, avoiding disruptions to operations and maximizing productivity. By leveraging advanced technologies and data analysis, predictive maintenance enables organizations to stay ahead of potential equipment failures, ensuring smooth and efficient operations. Ultimately, it helps companies maintain their equipment in top condition, extend its lifespan, and enhance overall reliability, leading to improved performance and customer satisfaction.
What Are The Main Types of Predictive Maintenance?
1. Corrective Maintenance
Corrective maintenance is needed when there’s a problem with equipment. Its main job is to fix the equipment so it works properly again. This fixing can happen either as part of a planned schedule or when the issue suddenly arises. If it’s not planned, fixing the equipment can be expensive because it wasn’t budgeted for. But if it’s planned, it’s more cost-effective since it’s part of a planned maintenance routine.
Corrective maintenance is important for keeping downtime to a minimum and making sure equipment keeps running smoothly. However, relying too much on corrective maintenance can end up costing more and causing disruptions. So, organizations need to balance it out with proactive maintenance to prevent future problems.
2. Preventative Maintenance
Preventive maintenance focuses on reducing the likelihood of equipment breakdowns by preventing potential issues from arising. Maintenance teams analyze historical data and past failures to establish well-structured maintenance programs. By doing so, they can identify potential failure points and take preventive actions to mitigate risks.
Preventive maintenance is considered planned as it follows a predefined maintenance schedule, which can be efficiently managed through a Computerized Maintenance Management System (CMMS). Implementing preventive maintenance ensures prolonged equipment lifespan and sustained productivity.
This proactive approach helps extend the equipment’s life and maintain consistent productivity levels by addressing potential problems before they escalate into major issues, thus reducing downtime and minimizing disruptions to operations.
3. Risk-Based Maintenance
Risk-based maintenance efficiently allocates resources to minimize risks associated with equipment failure. By prioritizing maintenance activities based on the criticality of assets and potential consequences of failure, this approach enhances cost-effectiveness and overall operational efficiency while safeguarding critical equipment. It helps organizations focus their efforts and resources where they are most needed, reducing the likelihood of costly downtime and ensuring continuous operations.
4. Condition-Based Maintenance
Condition-based maintenance relies on real-time sensor data to trigger maintenance actions only when equipment performance declines. By monitoring key indicators of equipment health, such as temperature, vibration, or pressure, this approach allows for timely interventions to address emerging issues before they escalate into major problems.
While offering long-term cost savings by minimizing unnecessary maintenance, condition-based maintenance requires regular monitoring and analysis to ensure optimal performance and reliability.
5. Predetermined Maintenance
Predetermined maintenance relies on manufacturer-provided programs and historical data to schedule maintenance activities. However, it lacks the precision of condition-based maintenance, as it may not account for variations in equipment usage or environmental conditions.
While this approach may help in establishing basic maintenance schedules, it carries the risk of overlooking critical issues and potentially leading to unexpected equipment breakdowns, impacting productivity and increasing maintenance costs.
6. Reliability-Centered Maintenance
Reliability-centered maintenance focuses on identifying the most critical components of equipment and developing maintenance strategies tailored to their specific needs. By conducting thorough risk assessments and analyzing failure modes and consequences, organizations can prioritize maintenance tasks and allocate resources effectively.
This predictive approach aims to optimize maintenance efforts, enhance equipment reliability, and minimize downtime, ultimately improving overall operational performance and reducing lifecycle costs.
What Are Some Types of Predictive Maintenance Technologies?
1. Oil Analysis
By regularly testing lubricants for contaminants and wear particles, maintenance teams can detect problems like bearing wear and fluid contamination early, allowing for optimized lubrication practices and extended equipment lifespan.
2. Time Domain Reflectometry (TDR)
TDR helps diagnose cable faults by sending electrical pulses along cables and measuring their reflections, enabling quick identification and repair of issues like open circuits and shorts, thus minimizing system downtime.
3. Vibration Analysis
Widely used in manufacturing plants with rotating machinery, vibration analysis detects issues like imbalance, misalignment, and bearing wear, helping to prevent unexpected breakdowns and ensure smooth equipment operation.
4. Spectroscopy
This technique analyzes the chemical composition of lubricants and fluids, allowing maintenance teams to identify wear particles and contaminants early, facilitating timely maintenance interventions and equipment reliability.
5. Proximity Probes
These probes monitor the gap between rotating components, detecting changes that indicate wear, misalignment, or imbalance, enabling maintenance teams to take corrective actions before problems escalate and affect equipment performance.
6. Tribology Monitoring
By studying friction, wear, and lubrication of machinery surfaces, maintenance teams can optimize lubrication practices, identify potential wear-related issues, and make informed maintenance decisions, ensuring equipment reliability and longevity.
7. Performance Trending
This data-driven technique tracks equipment performance over time, identifying trends and deviations from normal behavior, enabling proactive maintenance actions to prevent unexpected failures and optimize equipment performance.
What Is The Difference between Predictive and Preventive Maintenance?
The main difference between predictive and preventive maintenance lies in their approaches. Preventive maintenance is scheduled regularly based on triggers like time and usage, while predictive maintenance involves predicting when equipment failure might occur based on data analysis and then performing maintenance just before it happens. This approach aims to minimize downtime and reduce costs by addressing issues before they escalate.
What Are Some Industry Use Cases Related to Predictive Maintenance?
Predictive maintenance technologies are widely used across various industries to enhance equipment reliability and productivity
1. Energy
Energy companies utilize predictive maintenance to prevent power outages, which can incur significant costs and lead to customer dissatisfaction.
2. Manufacturing
Manufacturers employ predictive maintenance to prevent equipment failures and unplanned downtime, which can increase production costs and disrupt supply chains.
3. Telecommunications
Telecom companies rely on predictive maintenance to quickly address network errors, ensuring high-quality service and minimizing disruptions for customers.
4. Railways
Railway operators use predictive maintenance to identify and address issues with points, brakes, or track deformations, preventing service interruptions and ensuring passenger safety.
5. Civil infrastructure
Predictive maintenance helps assess structural integrity during inspection cycles, reducing economic disruptions and safety concerns related to infrastructure failures.
6. Defense
Military organizations utilize predictive maintenance to enhance the safety of equipment like helicopters by providing warnings of potential failures and improving operational readiness and troop safety.
In high-risk industries such as oil and gas, petroleum, petrochemicals, and energy, predictive maintenance plays a crucial role in enhancing operational efficiency and safety. By leveraging advanced technologies to predict equipment failures before they occur, these industries can minimize the risk of costly downtime, prevent accidents, and ensure uninterrupted production.
Predictive maintenance allows for proactive maintenance planning and resource allocation, optimizing asset performance and extending equipment lifespan. Ultimately, implementing predictive maintenance strategies helps high-risk industries maintain a competitive edge, improve asset reliability, and safeguard both personnel and the environment.
To safeguard your equipment and perform asset management more effectively, it’s essential to delve deeper into predictive maintenance strategies tailored to your industry. Consider exploring specialized training programs, workshops, or online resources that provide in-depth knowledge about predictive maintenance techniques and technologies.
Additionally, engaging with industry experts, attending conferences, and networking with peers can offer valuable insights and best practices for optimizing asset performance and mitigating risks. By continuously learning and staying updated on advancements in predictive maintenance, you can enhance operational efficiency, maximize asset reliability, and ensure long-term success in high-risk industries like oil and gas, petroleum, petrochemicals, and energy.
Credit header image: Freepik
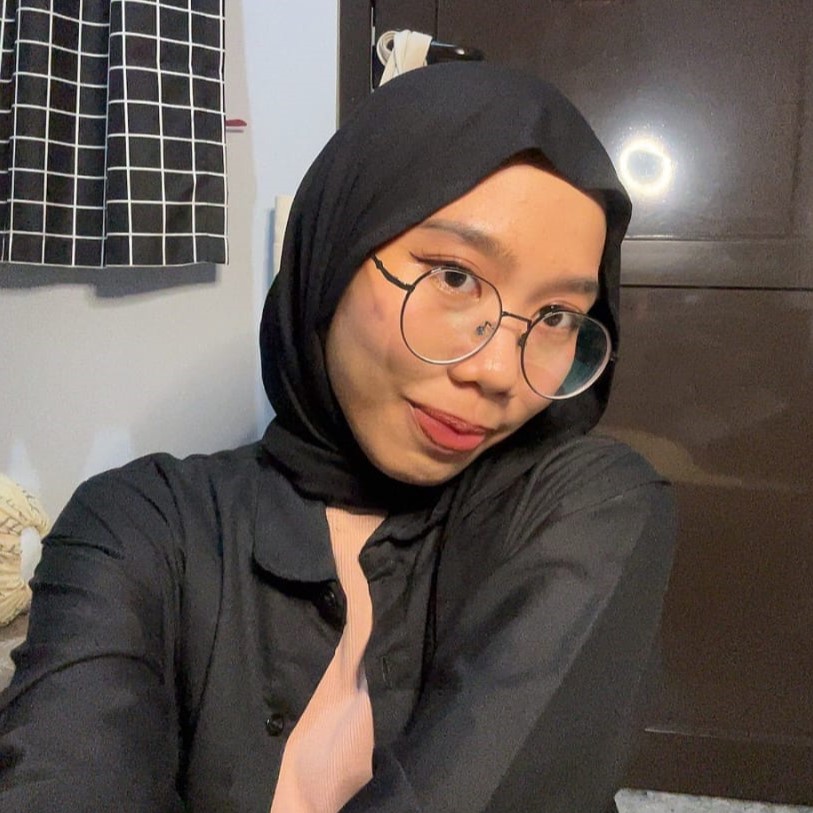
SEO specialist by day, fact-checker by night. An avid reader and content writer dedicated to delivering accurate and engaging articles through research and credible sources.