Process piping is a critical part of many industries, playing a crucial role in the transportation of fluids and gases for various processes. Whether in chemical plants, power generation facilities, or pharmaceutical manufacturing, process piping is essential for many industrial operations. In this article, we will explore the fundamentals of process piping, its design considerations, and the importance of proper maintenance to maximize its efficiency and lifespan.
What Is Process Piping?
Process piping is a technique used to transform chemicals, gases, and liquids into valuable and tangible products. In simpler terms, process piping is utilized to convert raw materials like fuels, liquids, chemicals, and gases into usable and valuable end products in an industrial process.
Process piping is commonly used in various industries, such as petroleum refining, chemical processing, power generation, and pharmaceutical manufacturing.
The design and construction of process piping systems involve multiple stages, including selecting the appropriate materials, determining the required flow rate, calculating pressure drop and thermal expansion, and taking into account safety and environmental factors.
Process piping systems usually consist of pipes, valves, fittings, pumps, and other components that are interconnected to form a network. Process piping must follow ASME B31.3 regulation because it is a recognized standard that provides guidelines for the safe design, construction, and operation of process piping systems.
ASME B31.3 specifies the minimum requirements for materials, design, fabrication, testing, and inspection of process piping systems. It covers a wide range of topics, including pipe sizing, pressure design, allowable stresses, corrosion protection, thermal expansion and contraction, and more.
To ensure safety and reliability, process piping systems must be designed and installed in compliance with industry standards and regulations. Regular maintenance and inspections are also essential to maintaining the integrity and effectiveness of the system over time.
What Are Piping Materials Used in Process Piping?
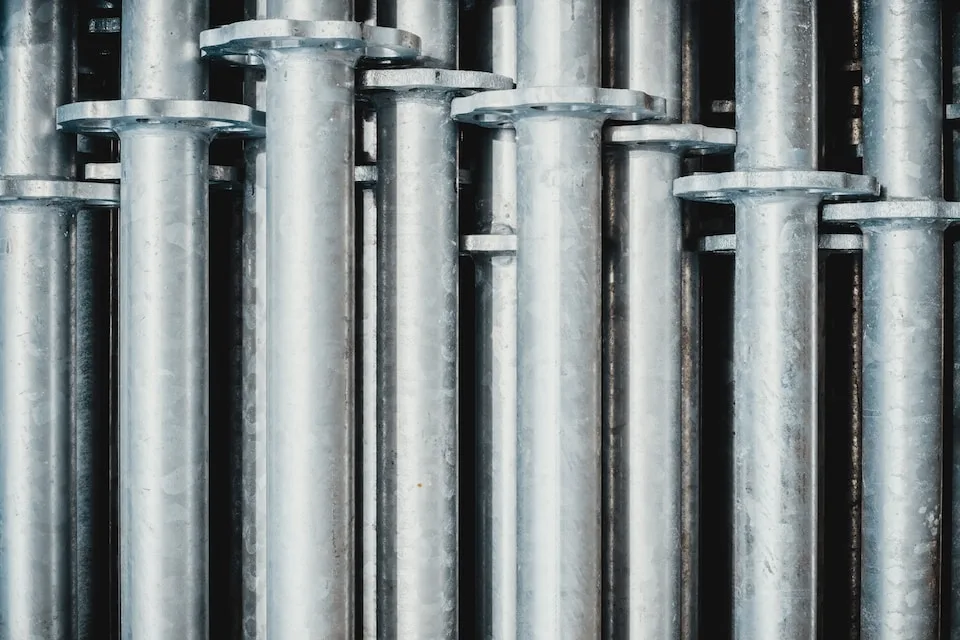
ASME B31.3 specifies the materials that can be used in process piping systems. The materials are regulated based on their strength, corrosion resistance, and other mechanical properties. They must also be able to withstand the temperature, pressure, and other conditions of the process. Some common materials used for process piping include:
- Carbon Steel
- Stainless Steel
- Alloy Steel
- Copper
- Nickel, and
- Plastic
Choosing suitable materials depends on various aspects, such as the nature of the fluid or gas being conveyed, the temperature and pressure conditions of the process, and the environmental factors at the installation location.
What Are Design Conditions, Pressure, and Temperature for Process Piping?
The term “design conditions” pertains to the highest anticipated operating conditions of the piping system, which includes the highest possible temperature and pressure of the fluid, as well as other factors like the existence of fluids that may cause corrosion or erosion.
Design pressure is the highest pressure that the piping system is intended to endure, and it is commonly determined using the design conditions, material characteristics, and safety margins. Design temperature is the upper limit of temperature that the piping system is designed to endure, and its calculation also takes into account the design conditions, material properties, and safety factors.
Design of Process Piping Components for Internal Pressures
ASME B31.3 provides guidelines for designing piping components to withstand internal pressures by examining the maximum allowable working pressure (MAWP), design pressure, fluid temperature, and material properties of the piping components.
Material selection is based on the fluid’s corrosiveness and temperature, and the thickness of the piping components is calculated based on design pressure and temperature. Thermal expansion and contraction effects on the system must be well calculated to prevent excessive stresses or displacements.
Design of Process Piping Components for External Pressures
When designing piping components to withstand external pressures, it is important to consider various factors, such as the maximum pressure that the piping systems can withstand (MAWP), the design pressure, and the external loads that the system may experience. To calculate the design pressure, the maximum anticipated operating conditions should be taken into account.
The MAWP, which is higher than the design pressure, is the maximum pressure that the system can operate safely. Additionally, external loads such as wind, snow, or seismic loads should also be considered during the design process to ensure that the components can withstand these loads without causing failure or excessive deformation. All of the recommendations above are regulated by ASME B31.3.
This five days training aims to equip attendees with a comprehensive understanding of the ASME B31.3 Process Piping Code and its practical applications, covering all aspects from piping design to testing and certification. PetroSync‘s ASME B31.3 – Process Piping Code Design Requirements training course provides detailed insight into code requirements related to piping components, branch connections, selection of flanges, fittings, flexibility considerations, materials requirements, fabrication, welding, NDT examination, and pressure testing.
We customize our training to focus on piping systems that are commonly used in petroleum industries, refineries, petrochemical, and power plants. Through in-class problem-solving exercises, you can learn to apply the rules and equations of the B31.3 Code for various design and operating conditions. Upon completion, attendees will be competent in applying the ASME B31.3 Pressure Piping Code in your professional work. Join our ASME B31.3 training and enhance your understanding and abilities in piping by gaining practical knowledge and insights with PetroSync!
Credit Header Image: Freepik
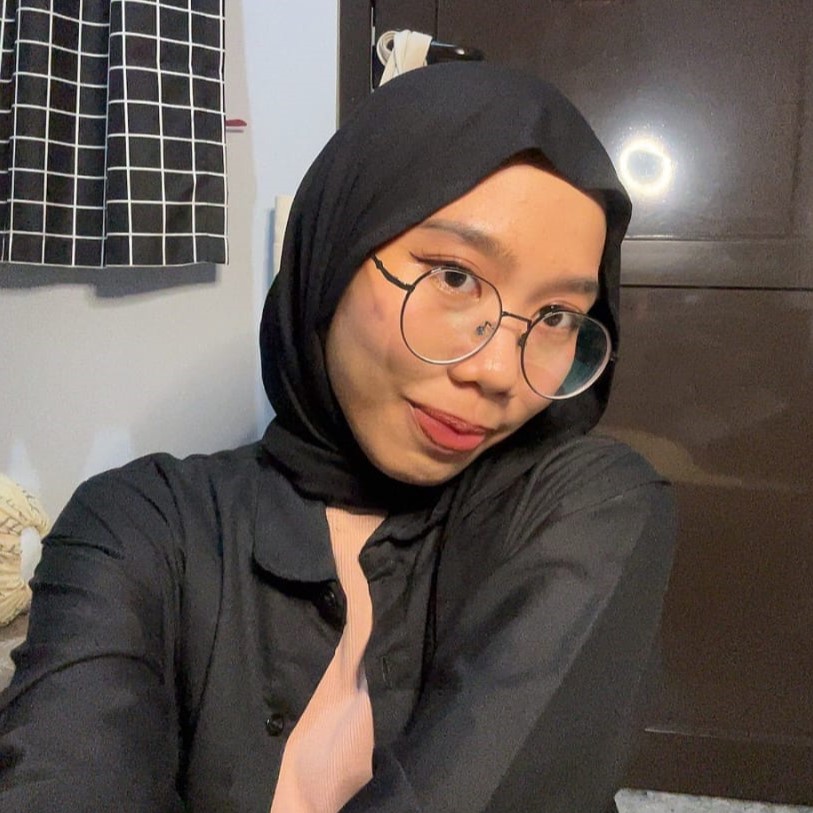
SEO specialist by day, fact-checker by night. An avid reader and content writer dedicated to delivering accurate and engaging articles through research and credible sources.