In industries where safety, precision, and compliance are paramount—such as oil and gas, petrochemical, and manufacturing—non-destructive testing (NDT) methods are critical for maintaining asset integrity. One of the most reliable methods to detect internal flaws is Radiographic Testing (RT).
Many industries still rely on RT in inspection scenarios, especially when surface-based methods can’t detect internal, volumetric defects. Let’s explore what radiographic testing is, how it works, and how you can build expertise in this vital technique.
What is the Radiographic Testing?
Radiographic Testing (RT) is a non-destructive testing technique used to inspect the internal structure of materials, particularly metals and welds, without damaging the component itself. The method uses X-rays or gamma rays to penetrate solid objects and produce an image (radiograph) that reveals subsurface discontinuities.
Radiographic Testing is widely used to detect:
- Cracks
- Porosity
- Incomplete fusion in welds
- Shrinkage cavities in castings
Because of its ability to detect defects deep within materials, Radiographic Testing is a preferred method in pipeline inspections, pressure vessel, aircraft components, and nuclear systems. Its detailed imaging makes it one of the most accurate and auditable NDT methods available.
How Radiographic Testing Works
Radiographic Testing operates on the principle of differential absorption of radiation. Here’s a simplified breakdown of the process:
1. A radiation source (either an X-ray tube or a radioactive isotope like Iridium-192 or Cobalt-60) emits rays toward the object under test.
2. The rays pass through the material and are partially absorbed depending on the material’s thickness and density.
3. Behind the object, a detector (such as radiographic film or a digital panel) captures the intensity of the rays that pass through.
4. The result is a radiograph—an image showing internal features, where darker areas indicate thinner or less dense regions, possibly suggesting voids or cracks.
The success of RT relies heavily on material type, object geometry, radiation energy, and exposure duration. A trained technician is essential to interpret these images accurately and determine whether a component passes inspection.
Tools and Equipment Used in Radiographic Testing
The effectiveness of radiographic testing depends significantly on the quality of equipment and proper setup. The main tools used include:
1. Radiation Sources
- X-ray generators: Used for precise, controlled testing in laboratories or field setups.
- Gamma-ray sources: Iridium-192 and Cobalt-60 are commonly used in industrial applications due to their portability.
2. Imaging Media
- Radiographic Film: Traditional method that requires development in a darkroom.
- Computed Radiography (CR): Uses phosphor plates that are scanned digitally.
- Digital Radiography (DR): Direct digital capture using flat-panel detectors; faster and eco-friendly.
3. Support Tools
- Collimators: Direct and shape radiation beams.
- Lead Shields & Barriers: Protect technicians from radiation exposure.
- Dosimeters: Measure and monitor exposure levels for safety compliance.
- Image Quality Indicators (IQIs): Standard markers used to verify image resolution and inspection quality.
Proper calibration and maintenance of these tools are crucial to ensuring valid results. Additionally, Radiographic Testing setups must comply with international radiation safety standards, such as those set by the IAEA or local regulatory bodies (e.g., BAPETEN in Indonesia).
Types of Radiographic Testing Techniques
Radiographic Testing has evolved to include several techniques, each with its own application strengths:
1. Conventional Film Radiography
This traditional method uses photographic film to capture radiation. It offers high resolution and is widely accepted by code standards. However, it requires chemical processing and has longer turnaround times.
2. Computed Radiography (CR)
In CR, an image plate replaces the film. After exposure, the plate is scanned using a laser-based digitizer. CR improves workflow and reduces chemical waste.
3. Digital Radiography (DR)
Digital Radiography provides real-time imaging through digital sensors. It enables faster decision-making, enhanced flaw detection, and better data management. DR is increasingly preferred in high-volume inspections such as pipeline girth welds.
4. Real-Time Radiography
Also called fluoroscopy, this method uses video feeds to view dynamic components under stress. Though costly, it’s valuable in aerospace and automotive part testing.
Inspectors select each technique based on inspection speed, accessibility, regulatory requirements, and cost-efficiency.
Join PetroSync’s Training to Advance Your Expertise
In today’s competitive industrial landscape, technical knowledge alone isn’t enough. What sets professionals apart is their commitment to continuous learning—they turn practical experience into structured expertise that others recognize and respect. PetroSync’s professional training programs help you grow with clear purpose.
Whether you’re looking to build confidence in the field, stay updated with the latest industry standards, or prepare for globally recognized certifications, this is your opportunity to invest in yourself. Our programs connect technical theory with real-world practice, guided by industry experts who understand the challenges you face every day.
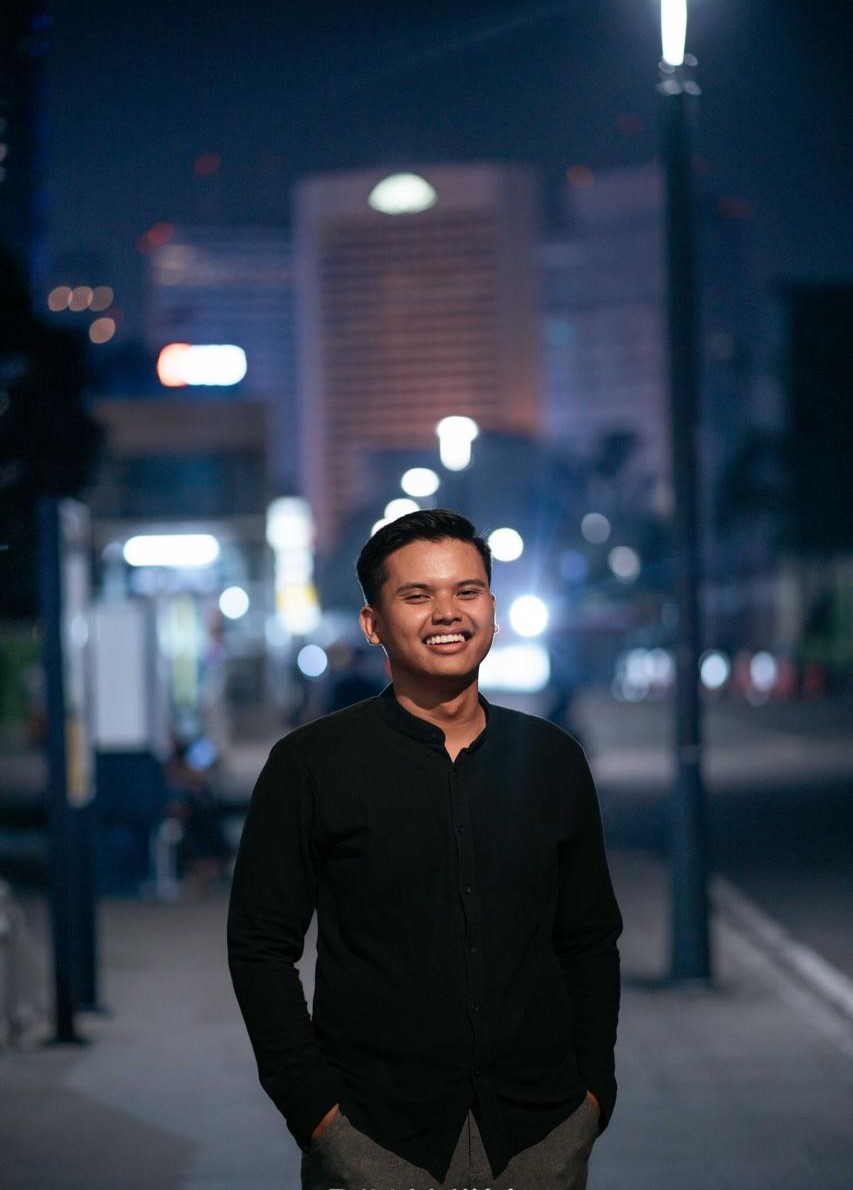
Results-oriented and thorough SEO specialist with extensive experience in conducting keyword research, developing and implementing digital website promotion strategies and plans, managing campaigns to develop company websites in the digital world, excellent knowledge of marketing techniques and principles, and attentive strong attention to detail.