Refractories have become one of the critical aspects in maintaining structural integrity and ensuring safety across industries. To begin, let’s delve into the concept of refractory solutions and their vital significance in industries grappling with extreme temperatures. We will also discuss the various applications and materials integral to refractory solutions.
What Is Refractory?
Refractory materials are special substances designed to withstand extremely high temperatures. They are widely used in various industries to shield against intense heat, particularly in places like furnaces and kilns. These materials are crucial for preserving the strength and safety of structures and equipment when exposed to very hot conditions.
One of the most common refractory applications in the industry is in the steel and metal industry. Furnaces and crucibles used for melting and refining metals reach exceptionally high temperatures, often surpassing 2,000 degrees Celsius (3,600 degrees Fahrenheit). Refractory materials play a vital role in insulating and lining these furnaces, ensuring they can withstand the extreme heat and chemical reactions involved in metal production.
What Is The Historical Background of Refractories?
The historical background of refractories in industry traces back to ancient times when early civilizations recognized the need for materials that could withstand intense heat. In these early periods, people used basic materials like clay and mud bricks to line their kilns and furnaces for various purposes.
As time progressed and industries such as metalworking, glassmaking, and ceramics expanded, the demand for more resilient materials to handle high-temperature processes grew. The 19th century marked a significant turning point when firebricks, offering improved durability and heat resistance, were introduced. This development greatly enhanced the capabilities of refractories for industrial applications.
Fast forward to the present day, refractories have undergone substantial advancements and specialization to cater to the specific needs of diverse industries. They have become integral to processes in fields such as steel production, cement manufacturing, and petrochemical processing. The historical journey of refractories underscores humanity’s ongoing quest for materials capable of enduring extreme heat, solidifying their indispensable role in industrial progress.
How Is The Application of Refractory Across Industries?
Refractory industries are pivotal in supporting the efficient and safe operation of high-temperature processes across various sectors.
1. Iron and Steel Industry
In the Iron and Steel Industry, refractories are crucial for protecting equipment from extreme heat. They line furnaces, ladles, and other high-temperature vessels, preventing structural damage and ensuring the safe transportation of molten metal.
Monolithic refractories, a type of these materials, offer effective heat control by insulating these vessels. Their application extends to furnace lining, which preserves furnace integrity and performance. The benefits include enhanced equipment durability, improved energy efficiency, lower maintenance costs, and consistent product quality, all contributing to the industry’s success. Refractories are essential for a safe and efficient steel and iron production process.
2. Aluminum Industry
Refractories are vital in the Aluminum Industry, where high temperatures are central to the production process. These specialized materials are used to line furnaces and other equipment involved in the smelting and casting of aluminum. Here are a few of the roles that refractory materials play in the aluminum industry:
- Processing aluminum scraps
- Melting
- Refining
By withstanding extreme heat, refractories ensure the structural integrity of these vessels, preventing damage and prolonging their lifespan. They also contribute to temperature control and energy efficiency, helping maintain the quality and consistency of aluminum products. In the Aluminum Industry, refractories are indispensable for enabling the safe and efficient production of aluminum materials.
3. Glass Industry
In the Glass Industry, refractories are essential components for creating glass products. They are used to line the interior of glass-melting furnaces, insulating and protecting the furnace structure from the extremely high temperatures required for glass production. This lining ensures the durability and longevity of the furnace and contributes to energy efficiency, resulting in cost savings. Refractories in the Glass Industry play a crucial role in enabling the efficient and consistent production of glass items while safeguarding the equipment’s integrity.
4. Power Generation
Refractories in power generation are crucial for lining the combustion chambers of boilers and furnaces where fuels like coal, natural gas, or biomass are burned to produce energy. These materials withstand extremely high temperatures and protect the chamber’s structural integrity.
By insulating against heat and maintaining efficient combustion, refractories enhance energy efficiency and contribute to the reliable and continuous production of electricity. In the power generation sector, refractories play a pivotal role in supporting the combustion processes necessary for electricity generation.
5. Cement Industry
Refractories are indispensable in the cement industry, where they line the interior of kilns and furnaces used for cement production. These materials endure exceptionally high temperatures, ensuring the structural integrity of the equipment while protecting against the harsh conditions of cement manufacturing.
By providing effective insulation and heat control, refractories contribute to energy efficiency and the production of high-quality cement. In the cement industry, refractories are essential for maintaining the durability of the equipment and ensuring the efficiency of the cement production process.
6. Refineries, Petrochemicals, and Chemicals
In refineries, petrochemicals, and chemical plants, refractories are integral for withstanding extreme temperatures and corrosive environments. They line the interior of equipment like reactors, boilers, and kilns, where chemical reactions and high-temperature processes occur.
Furthermore, it’s important to note that certain kinds of refractory solutions significantly help in lowering the rate at which the refractory linings are used up in the following equipment:
- Gasifiers
- Fired heaters
- Catalytic reactors
- Sulfur burners
In summary, refractories are incredibly important in many industries. These special materials act like protective shields against very high temperatures and harsh chemicals, often part of the manufacturing processes.
By lining the crucial equipment and keeping the heat in check, refractories ensure that the machines last a long time and can be used safely. They play a key role in keeping operations efficient and preventing damage to the equipment. As a result, these unsung heroes are vital for the ongoing success and reliability of these essential industries.
One of the remarkable types of refractory materials commonly used in the industry is monolithic refractories.” Monolithic refractories are a versatile group of materials that can be easily shaped and applied in various forms.
The materials used in monolithic refractories are particularly well-suited for repairs and maintenance of high-temperature equipment. Due to their adaptability and ease of use, monolithic refractories have become a preferred choice for quickly lining and repairing critical industrial equipment in the refineries, petrochemical, and chemical industries.
Building on the importance of refractories and specifically monolithic refractories, it’s worth noting that staying updated and well-trained in this field is essential for you working in the refineries, petrochemicals, and chemicals industry. Knowledge and expertise in the selection and application of refractories, including monolithic refractories, are critical for ensuring the continued efficiency and safety of operations.
PetroSync offers a specialized course known as API 936 training. This training equips industry professionals with the know-how to effectively work with monolithic refractories. You gain insights into the selection, installation, and maintenance of these materials, allowing you to make informed decisions and implement best practices.
In an industry where the correct use of refractories, including monolithic types, directly impacts safety, efficiency, and product quality, API 936 training can be an invaluable resource for you. Reserve your spot and ensure the smooth operation of your refractory facilities with PetroSync!
Credit: Seven Refractories
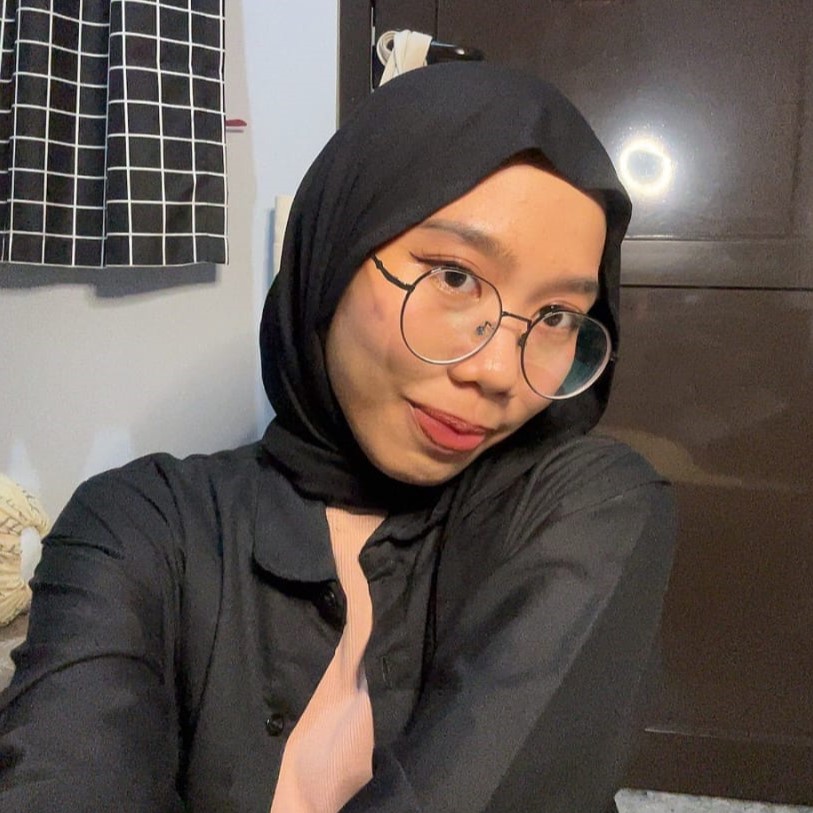
SEO specialist by day, fact-checker by night. An avid reader and content writer dedicated to delivering accurate and engaging articles through research and credible sources.