In the maintenance and reliability fields, knowing the metrics is essential for organizations seeking to optimize the performance and longevity of their products and services. These reliability metrics serve as critical indicators, offering insights into the effectiveness of systems and processes in terms of their reliability, ease of maintenance, and overall serviceability. In this article, we will delve into the significance of these metrics, examining how they contribute to informed decision-making and strategic planning.
What Is Reliability?
Reliability refers to the probability that a product, system, or process will consistently perform its intended functions without experiencing failures or breakdowns, emphasizing the likelihood of adequate performance for a specified period or operation in a defined environment without failure.
In simple terms, it is a measure of how dependable and trustworthy something is in carrying out its tasks over time. High reliability implies that the item or process is less prone to unexpected issues and can be counted on to work consistently according to its design and specifications.
What Is Maintainability?
Maintainability involves the ease with which a product or system can be maintained, repaired, or serviced and involves a system of continuous improvement – learning from the past to improve the ability to maintain systems. It measures how straightforward it is to perform necessary upkeep tasks, fix issues, or replace components when needed.
A high level of maintainability indicates that the product or system is designed in a way that facilitates efficient and cost-effective maintenance, reducing downtime and ensuring continued functionality over its lifecycle.
What Is Serviceability?
Serviceability is the measure of and the set of features that support the ease and speed at which corrective maintenance and preventive maintenance can be conducted on a system. It assesses how easily a product or system can be serviced or repaired when necessary, evaluating the convenience and efficiency with which maintenance tasks can be carried out to address issues, replace parts, or make adjustments.
A high level of serviceability means that the design of the product or system is user-friendly for maintenance purposes, allowing for swift and effective servicing to ensure uninterrupted functionality.
What Is The Difference Between Reliability and Serviceability?
Reliability measures the chance that a system will keep working at the next moment, considering it was working at the current moment. On the other hand, serviceability is about how easy it is to fix or maintain a system. While reliability looks at the likelihood of a product working consistently over time, serviceability considers how convenient it is to service or repair the product. Both are related ideas but focus on different aspects of a product or system.
Reliability is about how consistently and dependably a product performs its intended functions over time without failures. It gauges the likelihood of the product working well throughout its lifecycle. On the other hand, servicaability is about how easily and efficiently a product can be serviced, repaired, or maintained. It assesses the convenience with which maintenance tasks can be conducted to address issues or replace components. In essence, reliability emphasizes consistent performance, while serviceability emphasizes ease of maintenance and repair.
What Is The Difference Between Reliability and Maintainability?
Reliability characterizes how consistently a product or system performs its intended functions over time without failures, whereas maintainability describes the likelihood the same asset can be restored once a failure does occur.
These are distinct but interconnected concepts. Reliability focuses on how consistently a product or system performs its intended functions over time without failures. It measures the likelihood of uninterrupted operation.
On the other hand, maintainability is about how easily and efficiently a product or system can be maintained, repaired, or serviced when needed. It assesses the convenience with which maintenance tasks can be conducted to address issues or replace components.
What Is A Reliability Metric?
A reliability metric is a measurement used to assess how dependable and consistent a product or system is in performing its intended functions over time, providing operations management with valuable information about the performance of various aspects of an operation. These metrics are calculated from data generated by test programs, offering insights into the reliability of the product or system and aiding in the identification of potential issues for improvement. Reliability metrics play a crucial role in evaluating performance and guiding enhancements to ensure sustained and efficient operation.
What Are The Key Metrics of Reliability?
In the realm of reliability, various key metrics play a crucial role in assessing the performance and dependability of systems and components. These metrics offer valuable insights into different aspects of a product’s or system’s reliability.
1. Mean Time Between Failure (MTBF)
Mean Time Between Failure (MTBF) is a measure that tells us, on average, the average time between system breakdowns, and how much time passes between one failure of a product or system and the next.
In simpler terms, it provides an estimate of the average time a product or system can operate without encountering a failure. A higher MTBF value indicates a longer average time between failures, suggesting better reliability and a lower likelihood of unexpected issues during operation.
Apply the MTBF formula:
The result will be the average time between failures.
For example, if a system operates for 1,000 hours and experiences 5 failures during this time, the MTBF would be 1,000/5=200
It’s important to note that MTBF is an average value and is most meaningful when failures follow a consistent pattern over time. For systems with sporadic or irregular failures, other reliability metrics might be more appropriate.
2. Mean Time to Failure (MTTF)
Mean Time to Failure (MTTF) is an essential maintenance metric that estimates how long non-repairable assets can work before they falter, representing the average expected time until a non-repairable system or product is likely to experience its first failure.
In simpler terms, it gives an estimate of the average time a system can operate before the initial occurrence of a failure. A higher MTTF value indicates a longer average time before the first failure, suggesting better reliability and a more extended period of trouble-free operation.
3. Mean Time to Repair (MTTR)
Mean Time to Repair (MTTR) is the average time it takes to repair a system (usually technical or mechanical), telling us, on average, how much time it takes to fix or repair a system or product after it experiences a failure.
In simpler terms, MTTR provides an estimate of the average downtime, representing the time it typically takes to restore a system to its normal functioning state following a failure. A lower MTTR value is desirable as it indicates quicker and more efficient repair processes, minimizing disruptions and maximizing the availability of the system.
4. Mean Time Between Replacement (MTBR)
Mean Time Between Replacement (MTBR), usually used for non-repairable components or subsystems in a repairable system, is a measure that estimates, on average, the time that elapses between the replacements of a particular component or equipment.
In simpler terms, MTBR provides an average duration before a replacement is needed. A higher MTBR value indicates that the component or equipment tends to require replacement less frequently, suggesting better durability and a longer period of reliable performance before replacement becomes necessary.
5. Mean Time Between Unscheduled Maintenance Actions (MTBUMA)
Mean Time Between Replacement (MTBR), usually used for non-repairable components or subsystems in a repairable system, is a measure that estimates, on average, the time that elapses between the replacements of a particular component or equipment.
In simpler terms, MTBR provides an average duration before a replacement is needed. A higher MTBR value indicates that the component or equipment tends to require replacement less frequently, suggesting better durability and a longer period of reliable performance before replacement becomes necessary.
6. Mean Time Between Downing Event (MTBDE)
Mean Time Between Downing Event (MTBDE), which describes the expected time between two consecutive downing events for a repairable system, is a measure that calculates, on average, the time interval between occurrences of a system or equipment experiencing an event that causes it to be unavailable or “down.”
In simpler terms, MTBDE estimates the average time a system remains operational before an event leads to downtime. A higher MTBDE value signifies a longer average period of uninterrupted operation, indicating better reliability and a reduced frequency of events that result in system unavailability.
7. Failure In Time (FIT)
Failure In Time (FIT), another way of reporting MTBF, is a measure that quantifies the number of failures expected in a billion hours of operation for a particular component or system. In simpler terms, FIT represents the failure rate over a specific period, indicating how many failures can be anticipated for every billion hours of usage.
A lower FIT value suggests better reliability, as it indicates a lower likelihood of failures occurring within a given timeframe. FIT is commonly used in reliability engineering to assess and compare the expected failure rates of different components or systems.
In conclusion, delving into the realm of reliability metrics is vital for businesses and engineers. Reliability metrics and knowledge empower organizations to gauge the likelihood of failures, estimate repair times, and plan for replacements, ultimately contributing to improved product and system reliability.
PetroSync continues to offer Certified Reliability Engineer (CRE) training, providing you with a comprehensive and in-depth outline to prepare for CRE certification. Our CRE training program is designed to equip you with the knowledge and skills necessary to navigate the intricate landscape of reliability engineering.
By enrolling in our courses, you gain access to valuable insights, practical applications, and expert guidance that will not only bolster your understanding of reliability metrics but also enhance your overall proficiency in ensuring the dependability of systems and products.
Credit: Freepik
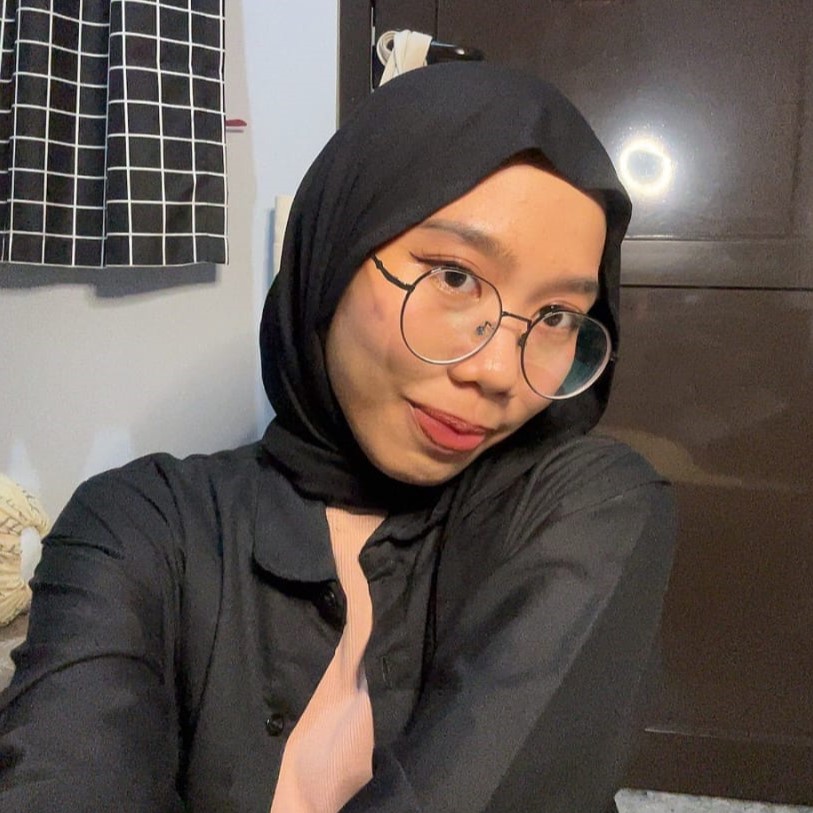
SEO specialist by day, fact-checker by night. An avid reader and content writer dedicated to delivering accurate and engaging articles through research and credible sources.