A shell and tube heat exchanger functions as a heat transfer device utilized in various industries for exchanging heat between two fluids without any contact between the two. The exchanger comprises a cylindrical vessel called a shell, which encloses a bundle of tubes. The tube-side fluid is fluid, referred to as the fluid flowing through the tubes, while the shell-side fluid circulates around the tubes within the shell.
A shell and tube heat exchanger holds a significant position in petrochemical, oil and gas, power generation, and other industries by enabling efficient heat transfer between two fluids. Its primary function is to facilitate the exchange of thermal energy between a hot fluid and a cold fluid while maintaining their separation.
This allows industries to optimize their processes by controlling temperatures, recovering wasted heat, and ensuring the desired thermal conditions for equipment and products.
What Is Shell and Tube Heat Exchangers Training Course Overview?
With their versatility, high heat transfer rates, and capability to handle various fluids, shell and tube heat exchangers are indispensable in applications. Having fundamental knowledge and practical skill regarding this equipment should be paramount for engineers since shell and tube heat exchangers are widely used.
What Is Shell and Tube Heat Exchangers Training Course Objective?
The main objective of PetroSync’s Shell and Tube Heat Exchangers training course is to equip the attendees with a thorough understanding of shell and tube heat exchangers, including their design principles, operation, maintenance, and troubleshooting. Read on for the detailed objective of the training.
- Familiarize participants with the concepts and technical terms of the codes.
- Know the basic concepts of the codes and their design fundamentals.
- Understand salient features and differences between codes and standards.
- Know the design of pressure parts and major components.
- Understand the problems in exchangers in-service & corrosion-related issues.
- Learn the maintenance aspects of shell & tube exchangers.
- Get introduced to the repair techniques and considerations.
- Discover the fabrication requirements, assembly, and welding requirements.
- Understand NDE, inspection procedures, and pressure testing.
What Is Shell and Tube Heat Exchangers Training Course Outline?
The outline of PetroSync’s Shell and Tube Heat Exchangers training course is listed down below. For a more complete outline, you can refer to PetroSync’s Shell and Tube Heat Exchangers training course details.
Day 1
- Importance of Heat Transfer
- Categories of heat exchangers such as Plate Type/ Double Pipe/ Cooling Towers/ Air Cooled Exchangers
- Modes of heat transfer such as conduction/ convection/ radiation.
- Introduction to Fluid Flow, velocities, and Pressure Loss.
- Applicability of relevant codes under ASME/ TEMA/ API.
- Introduction and Considerations in Thermal Design
- Material selection criteria from ASME Section II.
Day 2
- Heat Exchanger Terminology as per TEMA/ ASME.
- Types such as Fixed/ Floating/ U tube sheet and applications.
- Shell-And-Tube Heat Exchanger parts and detailed function.
- Mechanical design & thickness calculations as per ASME-VIII (Internal/ External pressure) for shells/ bonnets/ tubes.
- Minimum thickness criteria from TEMA.
- Tube Layouts and Number of Tubes in specified Shell Diameter (for ease of maintenance)
- Exercise on (basic) thermal design of the exchanger
Day 3
- Thickness calculation for Tube sheet (Bending/ Shear) from TEMA.
- Minimum requirement criteria for baffles/ tie-rods/ tubes/ flanges/ impingement plates/ etc.
- Baffles clearance and spacing with consideration to flow-induced vibrations.
- Tube Layouts and Number of Tubes in specified Shell Diameter (for ease of maintenance)
- TEMA Standard References.
- General Introduction to API Standard for Petroleum and Natural Gas Industries
- Case study/ exercise on a mechanical design using TEMA/ ASME criteria
Day 4
- Inspection considerations (Radiography/ Ultrasonic/etc.)
- Heat Exchanger Hydrostatic test/ Pneumatic test.
- General reference from ASME Section-V and ASME Section-IX.
- Corrosion and Fouling in Heat Exchangers
- Maintenance and Cleaning Methods
- Preventive & Corrective Maintenance.
- Effects of tube failure/ bad design on the operation of the exchanger.
- Concept of MAWP.
Day 5
- Repair minimum requirement criteria from ASME PCC-2.
- Re-tubing/ tube pulling/ plugging (friction/ mechanical plugs) of tubes
- A case study from ASME PCC-2 philosophy.
- Final heat exchanger selection based on
- Type of Duty
- Operating Limitation
- Materials of Construction
- Safety and Reliability
- Design Methods
- Inspection of new Heat Exchangers during fabrication
- Dimensions and Weight
- Cost
- Delivery
- Review of a real-life typical fabrication assembly drawing/ calculations/ specification datasheet.
- Discussions and queries
- Final Exam (if required)
(Detailed Thermal Design and HTRI, are not part of this course)
(The main codes of discussion will be ASME VIII-1/ TEMA only. All other codes/ standards mentioned will be generally referred to, as required, to understand the concepts clearly.)
Who Should Attend Shell and Tube Heat Exchangers Training Course?
The course is tailored for engineers in various roles, such as mechanical design, operations, maintenance, and inspection professionals such as:
- Design Engineers/Managers
- Mechanical Engineers/Managers
- Maintenance Engineers/Managers
- QAQC Engineers/Managers
- Inspection Engineers/Managers, and
- Reliability Engineers/Managers.
While the course primarily focuses on equipment such as pressure vessels, heat exchangers, process columns, and more, it is not limited to these specific fields and welcomes participants from related areas as well. Joining Shell and Tube Heat Exchangers training course by PetroSync can help you understand how STHEs work while learning the principles behind heat transfer.
We complement our training with knowledge of efficient systems design, shell and tube heat exchangers performance optimization, and real case studies regarding issues and malfunction. Additionally, attending PetroSync’s training course can help you stay updated on industry advancements and new technologies. Enroll today and gain the knowledge and skills necessary to design, operate, and maintain effective heat exchanger systems with PetroSync!
Credit header image: adobestock.com
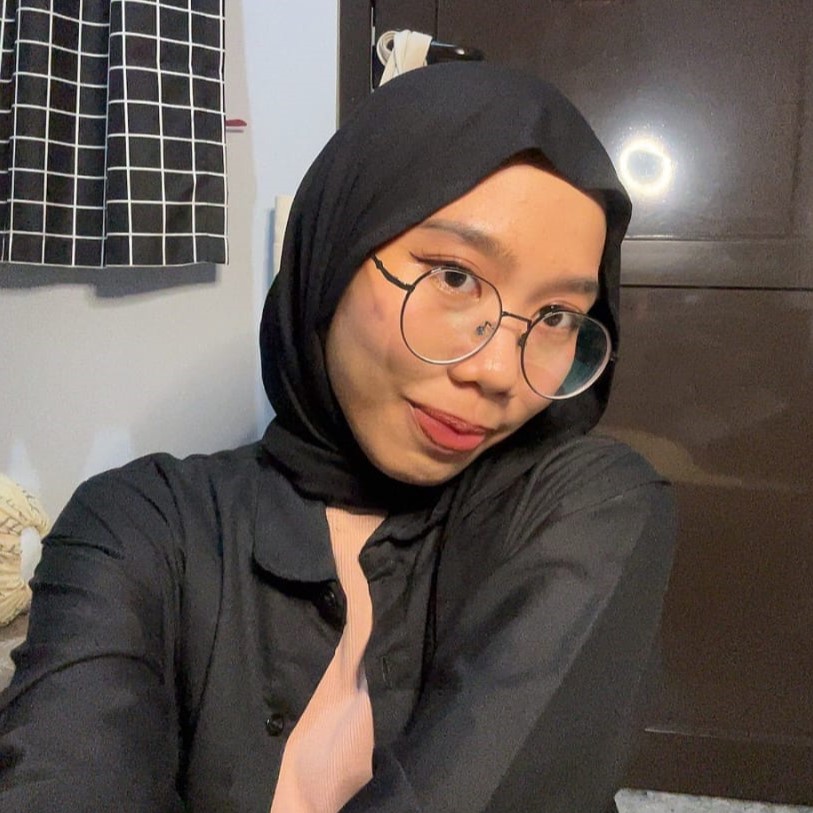
SEO specialist by day, fact-checker by night. An avid reader and content writer dedicated to delivering accurate and engaging articles through research and credible sources.