Pressure testing is an important aspect across diverse industries, ensuring the safety, reliability, and performance of systems and components under operational conditions. This essential testing process involves subjecting objects to internal or external pressure to assess their capacity to withstand the intended pressures.
This article will provide a comprehensive exploration of pressure testing, delving into its significance, purpose, applications, types and requirements for achieving optimal testing outcomes.
What Is Pressure Testing?
Pressure testing is a method used to verify the strength and leak-resistance of a vessel, pipe, or system under pressure. It involves applying a specified amount of pressure, usually greater than the system’s normal operating pressure, to detect leaks or weaknesses. This method assures that the equipment can withstand the intended pressure without failing, preventing future dangers.
Pressure testing is common in the oil and gas industry to ensure that pipes, tanks, and other pressurized systems are safe to operate. Pressure tests are classified into several types, including hydrostatic and pneumatic testing, each with a specific use and material.
What Is The Purpose of Pressure Testing?
The purpose of pressure testing is to evaluate and confirm the strength, integrity, and safety of a system or component. Its objective is to ensure that the tested object can endure the intended operating conditions without experiencing any failures or compromises. By subjecting the system or component to different levels of pressure.
Pressure testing assists in identifying potential leaks, weaknesses, or defects. Additionally, it aims to verify adherence to design and safety standards, validate performance and reliability, and reduce the likelihood of accidents or malfunctions. Ultimately, pressure testing plays a vital role in ensuring the quality and safety of products and systems across various industries.
Why Is a Pressure Test Needed?
Pressure testing is essential for several reasons, all related to safety, performance, and regulation. Here are the main reasons why pressure tests are a necessity in the oil and gas, petrochemical, and energy industries:
-
Safety Assurance:
The most important reason for doing pressure testing is to protect personnel, the environment, and the equipment itself. Leaks or ruptures in pressurized systems can result in catastrophic failures, endangering human lives and the environment.
-
Compliance with Standards:
Regular pressure testing is required for equipment maintenance and compliance with industry standards such as ASME (American Society of Mechanical Engineers) and API (American Petroleum Institute). Meeting these criteria helps businesses avoid legal problems and assures they are following best practices.
-
Preventive Maintenance:
Regular pressure testing aids in recognizing potential issues before they become major concerns. Early detection of defects or leaks can help you avoid costly repairs, downtime, and accidents in the long run.
-
Operational Efficiency:
Pressure-tested equipment is more likely to perform efficiently and without unexpected failures. This guarantees that operations run smoothly, increasing productivity and lowering the danger of unexpected shutdowns.
Finally, pressure testing is critical for ensuring the integrity and safety of equipment in high-risk businesses. By following the right processes and adhering to industry standards, businesses may protect their operations, employees, and the environment from potential threats.
How To Do A Pressure Test?
A pressure test entails numerous critical stages to ensure accurate results and the safety of all concerned. A general summary of the technique is provided below :
-
Preparation:
Inspect the equipment thoroughly before beginning the test. Repair any obvious damage or faults, ensure all safety processes are in place, and isolate the system as needed.
-
Filling the System (for hydrostatic tests):
A hydrostatic test involves filling the system with water, which serves as the test medium. Perform pneumatic testing with air or gas, but take extra precautions due to the higher risk of energy release if a failure occurs.
-
Applying Pressure:
Gradually increase the pressure using specialized pumps after filling the system, until it reaches the specified test pressure, which is usually higher than the system’s operational pressure.
-
Monitoring:
Monitor the system while it is under pressure for a set period. Record any leaks or pressure decreases, then securely depressurize the system to resolve the problem.
-
Evaluation:
Check the equipment for apparent abnormalities or leaks after the test. If the system passes, consider it safe to operate. If not, repair or replacement may be required.
-
Documentation:
Document the pressure test data, including test pressures, timings, and observations, for future reference and to ensure conformity with regulatory standards.
What Are The Two Types of Pressure Testing?
There are two primary types of pressure testing: hydrostatic testing and pneumatic testing.
1. Hydrostatic Testing
Hydrostatic testing is the primary technique employed to evaluate the leak resistance and structural soundness of various pressurized equipment such as meter skids, compressed gas cylinders, boilers, tubing, pipelines, and other vessels.
This method involves filling the system or component with water or another liquid and applying pressure to it. The pressure is gradually increased to a predetermined level and maintained for a specified time. During the test, the system or component is inspected for any leaks, deformations, or failures.
Hydrostatic testing is commonly used for systems that handle liquids. It helps identify potential weaknesses or flaws in the system’s structure or sealing, ensuring its safety and integrity.
Advantages of Hydrostatic Testing |
Disadvantages of Hydrostatic Testing |
Hydrostatic testing allows for the accurate detection of leaks in pressurized systems or components. | Hydrostatic testing often requires a significant amount of time to fill, pressurize, and drain the system or component. |
This testing provides a thorough evaluation of the structural integrity and strength of the tested object. | The use of water as the testing medium in hydrostatic testing can potentially lead to corrosion issues. |
2. Pneumatic Testing
Pneumatic testing aims to ensure that a system can safely withstand its maximum operating pressure by subjecting it to pressures exceeding its design limit. This test employs air or inert gasses like nitrogen to pressurize the system up to 110% of its intended pressure threshold. In pneumatic testing, the system or component is pressurized with a gas, such as air or nitrogen, instead of a liquid.
Similar to hydrostatic testing, the pressure is gradually increased to a specific level and held for a set duration. This type of testing is typically employed for systems that handle gases or compressed air. Pneumatic testing helps assess the system’s ability to withstand pressure, detect leaks, and ensure overall reliability and performance.
Both hydrostatic and pneumatic testing involve careful pressure monitoring, visual inspections, and strict adherence to safety guidelines. The choice between the two methods depends on the specific characteristics and requirements of the system or component being tested.
Advantages of Pneumatic Testing |
Disadvantages of Pneumatic Testing |
Pneumatic testing is generally faster as it doesn’t require the time-consuming processes of filling, pressurizing, and draining with water. | The testing may not be as effective in detecting small leaks compared to hydrostatic testing. |
The use of air or inert gases as the testing medium in pneumatic testing eliminates the risk of corrosion. | It involves handling compressed gases, which can present safety hazards if not properly controlled and managed. |
Why Is Pneumatic Testing More Dangerous than Hydrotest?
Pneumatic testing poses a higher risk compared to hydrostatic testing due to the need for more energy to achieve the desired pressure with compressible gases. This stored energy can lead to explosive release in case of failure, making pneumatic testing significantly more hazardous than hydrostatic testing.
Working with compressed gases also introduces inherent hazards, including the potential for sudden releases, rapid decompression, or explosions. Detecting leaks during pneumatic testing is more challenging compared to hydrostatic testing, and the specialized equipment used can be prone to failures that result in uncontrolled pressure buildup.
Additionally, pneumatic testing at low temperatures raises concerns about brittle fracture and the subsequent release of energy. To mitigate these risks, it is crucial to implement strong safety measures, follow proper procedures, and closely monitor test conditions.
What Are The General Requirements of Pressure Testing?
The general requirements of pressure testing encompass several key aspects:
1. Stress Exceeding Yield Strength
When the stress on the material exceeds its yield strength, the test pressure should be reduced to a level that will not surpass the yield strength at the temperature of testing. This precaution is taken to avoid any permanent deformation or damage to the material.
2. Test Fluid Expansion
If the test pressure is to be maintained for a certain period and the fluid in the system is prone to thermal expansion, appropriate measures must be taken to prevent excessive pressure buildup. This is necessary to ensure the system remains within safe limits during the test.
3. Preliminary Pneumatic Test
Prior to conducting hydrostatic or pneumatic testing, it is recommended to perform a preliminary test using air at a pressure not exceeding 170 kPa (25 psi) gauge pressure. This preliminary test helps identify any major leaks in the system before the actual pressure testing is conducted.
4. Examination for Leaks
During the leak test, a minimum duration of 10 minutes should be maintained, and all joints and connections must be thoroughly inspected for any signs of leakage. This examination is crucial to identify and address any potential leaks in the system.
5. Heat Treatment
In cases where heat treatment is performed on the system, leak tests should be carried out after the completion of the heat treatment process. This helps ensure that the system remains leak-tight even after undergoing any heat-related treatments.
6. Low-Test Temperature
When conducting leak tests at low temperatures, especially near the ductile-brittle transition temperature of the metal, it is important to consider the possibility of brittle fracture. Suitable precautions should be taken to prevent any safety hazards that may arise due to brittle fractures during the testing process.
7. Personnel Protection
To ensure the safety of personnel in the vicinity of the tested piping system, proper precautions must be taken in the event of a rupture in the piping system. These precautions aim to minimize the risks and eliminate potential hazards to personnel during the testing procedure.
8. Repairs or Additions After Leak Testing
In cases where repairs or additions are made to the system after the initial leak test, the affected piping should be retested to ensure that the repairs or additions have not compromised the integrity of the system.
9. Test Records
During the testing process, detailed records should be maintained for each piping system. These records should include:
- The date of the test
- Identification of the piping system
- Test fluid used
- Test pressure was applied, and
- Certification of the results by the examiner.
Keeping accurate records is crucial for documentation, compliance, and reference purposes.
What Are The Preparation Steps for Pressure Testing
The preparation steps for pressure testing involve the following:
1. Examination of Design and Specifications
Thoroughly review the system or component’s design and specifications to understand the intended operating conditions, maximum allowable working pressure, and specific requirements for the pressure test.
2. Selection of Test Method
Choose the suitable pressure testing method based on the system or component’s characteristics, select either hydrostatic or pneumatic testing, and consider the nature of the fluid or gas to be handled.
3. Establishment of Test Boundaries
Define the boundaries of the system or component you will test, including entry and exit points, connections, valves, and any isolated sections that require separate testing.
4. Verification of System Readiness
Ensure that the system is ready for testing by confirming the proper installation and unobstructed status of all components, equipment, and instruments.
5. Evaluation of Safety Measures
Assess and implement appropriate safety measures, including the utilization of personal protective equipment (PPE), safety barriers, and emergency response protocols, to ensure the protection of personnel and equipment during the testing process.
6. Preparation of Test Equipment
Ensure the calibration, functionality, and suitability of test equipment such as pressure gauges, sensors, and control devices to meet the testing requirements.
7. Flushing and Cleaning
Thoroughly flush and clean the system to eliminate contaminants, debris, or foreign substances that may affect the accuracy of the pressure test or potentially damage the system.
8. Pre-Test Inspection
Conduct a visual inspection of the system or component to identify any visible defects, damages, or indications of leakage. Address and resolve any identified issues before proceeding with the pressure test.
9. Sealing and Isolation
Properly seal and isolate the test boundaries to prevent leaks or pressure loss during the test. Ensure the secure and tight connection of all joints, seals, and connections.
10. Communication with Personnel
Notify relevant personnel, including operators, supervisors, and technicians, regarding the impending pressure test, its schedule, and the necessary safety precautions they need to be aware of.
What Are The Standards of Practice Used for Pressure Testing?
Pressure testing relies on established guidelines and specifications to ensure the safe and precise examination of pressure systems. Several essential standards are commonly employed for pressure testing, including:
1. ASME B31.3
Pressure testing is a vital procedure in ASME B31.3 to guarantee the safety and integrity of process piping systems. ASME B31.3 provides guidelines for designing, constructing, inspecting, and testing these systems. Pressure testing involves subjecting the piping to a specified pressure, higher than the design pressure, to check for leaks, defects, or weaknesses.
2. ASME PCC-2
In ASME PCC-2, pressure testing is an essential procedure used to ensure the safety and reliability of pressure-containing components after repairs or modifications. Following the guidelines provided by ASME PCC-2, engineers and technicians subject the equipment to specific pressures to verify its ability to withstand operational conditions without any leaks or failures.
3. API 570
In API 570, pressure testing is an essential procedure used to examine and validate the performance of piping systems. This process involves subjecting the piping components to specific pressure levels to ensure their safety, integrity, and leak resistance. Pressure testing is carried out at different stages, such as during construction.
After repairs or modifications, and as part of regular inspections. By following these preparation steps, you will execute the pressure testing process smoothly, efficiently, and safely, resulting in accurate and reliable test outcomes. Mastering the art of pressure testing holds immense importance, particularly if you are a piping inspector.
A comprehensive understanding of pressure testing methodologies, safety protocols, and industry standards equips you with the knowledge and skills necessary to excel in your role.
Unlock Your Potential: Join Petrosync Training for Professional Growth
To further enhance your expertise in pressure testing and obtain a recognized certification, joining the API 570 Piping Inspector training course offered by PetroSync is highly recommended. Our specialized provides comprehensive training on pressure testing techniques, inspection methodologies, and compliance with API 570 standards.
By enrolling in API 570 training course, you can deepen your knowledge, refine your skills, and stay abreast of the latest industry practices. Ultimately, mastering pressure testing not only ensures the integrity of piping systems but also enhances the credibility and your competence in delivering high-quality inspection services.
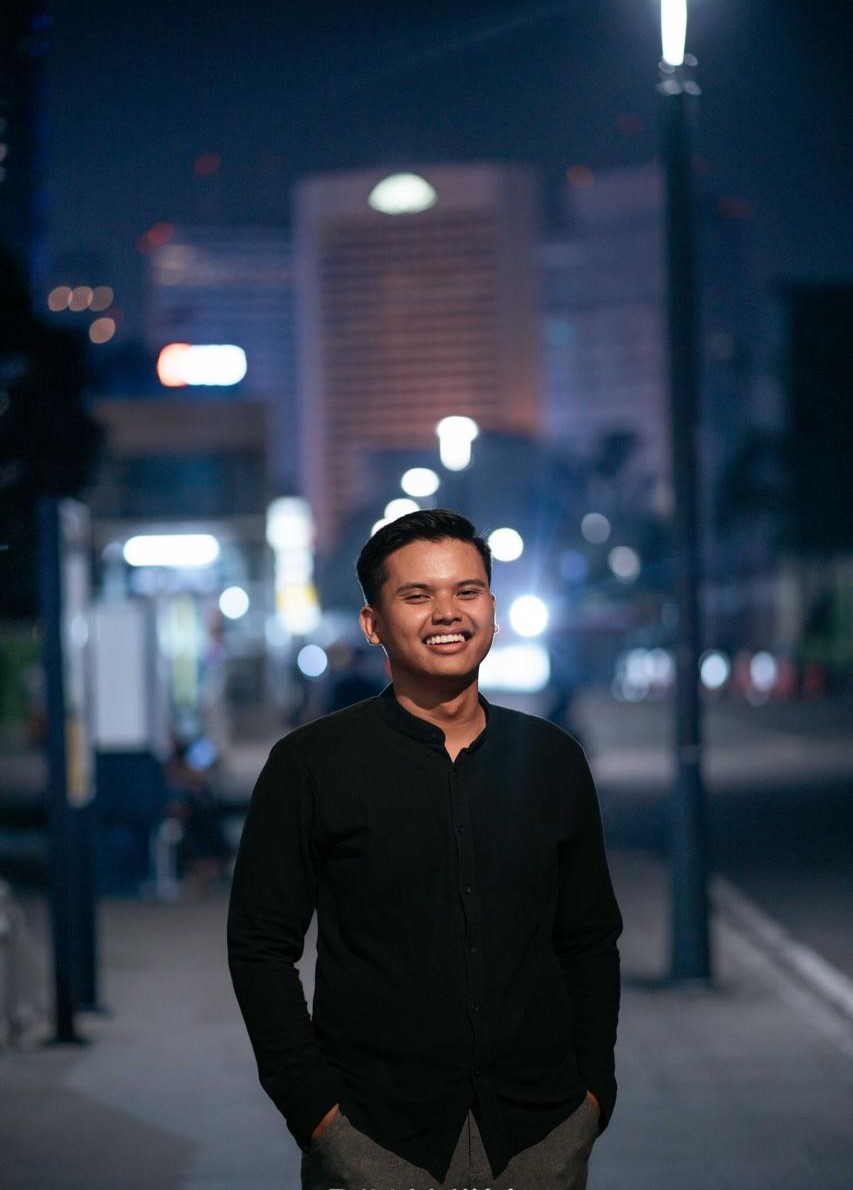
Results-oriented and thorough SEO specialist with extensive experience in conducting keyword research, developing and implementing digital website promotion strategies and plans, managing campaigns to develop company websites in the digital world, excellent knowledge of marketing techniques and principles, and attentive strong attention to detail.