Stress corrosion cracking is a significant problem in the oil and gas industry. Exposure of metal structures to stress, corrosive environments, and chemical agents can cause cracks that can lead to catastrophic failure. Both upstream and downstream companies must understand and prevent this issue. In this article, we will discuss the causes, detection, prevention, and management of stress corrosion cracking in the industry.
What Is Stress Corrosion Cracking?
Stress corrosion cracking (SCC) is the development of crack formation of materials such as metal alloys and polymers when they are exposed to a corrosive environment. This corrosion type leads to the formation of fractures or cracks in the material, which can compromise its structural integrity and cause failure.
Various factors can cause stress corrosion cracking, such as exposure to chemicals, high temperatures, and mechanical stresses. It is a significant concern in industries like oil and gas, aerospace, and nuclear power, where the failure of critical components can result in severe consequences.
Preventive measures to avoid stress corrosion cracking involve the use of corrosion-resistant materials, applying protective coatings, and performing regular inspection and maintenance.
Example of Stress Corrosion in the Oil and Gas Industry
In the oil and gas industry, SCC can occur in pipelines, storage tanks, and other equipment that are exposed to harsh environments. One example of SCC in the oil and gas industry is piping systems used for transporting natural gas. The high-pressure gas can create tensile stresses in the pipeline, which, when combined with the presence of a corrosive environment, can lead to SCC. This can result in the formation of cracks that can grow over time and potentially lead to pipeline failures.
Another example is the storage of crude oil in tanks. The corrosive nature of the oil, combined with the tensile stresses on the tank walls, can lead to SCC. This can result in leaks or tank failures, leading to environmental damage and potential safety hazards.
Preventing SCC in the oil and gas industry requires careful material selection, design, and maintenance practices. Regular inspections and monitoring can help detect and address potential SCC issues before they result in equipment failures.
How Do I Know If Stress Corrosion Is Cracking?
Stress corrosion cracking occurs when materials that are under tensile stress and exposed to a corrosive environment develop cracks or fractures. Signs of this type of cracking include visible cracks on the material’s surface, sudden or unexpected failure of the material, and changes in the material’s color or texture.
It is vital to regularly inspect materials under tensile stress and in corrosive environments, especially in industries such as oil and gas, aerospace, and nuclear power. If stress corrosion cracking is suspected, immediate preventive measures must be taken to prevent further damage or failure of important components.
1. Material
The type of material used can cause stress corrosion cracking, as some materials are more susceptible to SCC than others. Selecting the wrong material can lead to stress corrosion cracking if the material is vulnerable to SCC in the corrosive environment it operates in.
2. Environment
Chemical species present in the operating environment can cause stress corrosion cracking in various materials. Therefore, selecting the appropriate material and environment is crucial to prevent stress corrosion cracking.
3. Tensile Stress
Tensile stress occurs when a material experiences stress or strain from residual stress or direct application of stress or pressure. Stress corrosion cracking is mainly caused by static stress, and for a crack to be considered stress corrosion cracking, factors related to the material and environment must also be present.
How Do I Prevent Stress Corrosion Cracking?
To avoid the catastrophic failure of materials caused by stress corrosion cracking (SCC), you can take the following measures:
- Choose a material that resists SCC to prevent it. Less susceptible materials, such as titanium and stainless steel, can be the first option possible.
- Reduce tensile stress on the material to avoid SCC. This can be done by reducing the weight or pressure on the material, or by modifying the design to distribute the stress more evenly.
- Control the environment to prevent SCC, as it can be caused by certain environmental factors. Protective coatings, controlling temperature and humidity levels, and avoiding chemicals that can cause SCC can be useful in this regard.
- Regularly inspect and maintain equipment to identify potential SCC problems early. This will help ensure timely repairs or replacements before any failure occurs.
By implementing these measures, you can prevent stress corrosion cracking and prolong the life of companies’ equipment. It is known that stress corrosion cracking (SCC) can pose significant safety and environmental hazards if it is not addressed and abandoned, SCC can cause cracks to propagate and weaken the material, which can result in sudden equipment failure, the release of hazardous materials, and devastating consequences for human health and the environment.
Engineers who are responsible in the fields of asset management, corrosion engineering, and materials science can highly benefit from attending API 580 and 581 training course crafted by PetroSync. Our training covers several RBI aspects, such as risk analysis, corrosion inspection planning, and implementing corrosion control measures. During the training, you will also learn to identify and manage stress corrosion cracking (SCC), which is a critical area of concern.
The core of PetroSync’s Risk-Based Inspection training is API 580 Risk-Based Inspection and API Publication 581 Base Resource Document. The training will uncover viable options and alternatives to achieve a successful RBI program without overcomplicating things.
The course adopts a clear and concise approach to explain the RBI framework and methodology, which aids in creating and executing a risk-based inspection program that aligns with the company’s goals. Reserve your RBI training and improve your company safety and accident prevention with PetroSync!
Credit header image: freepik.com
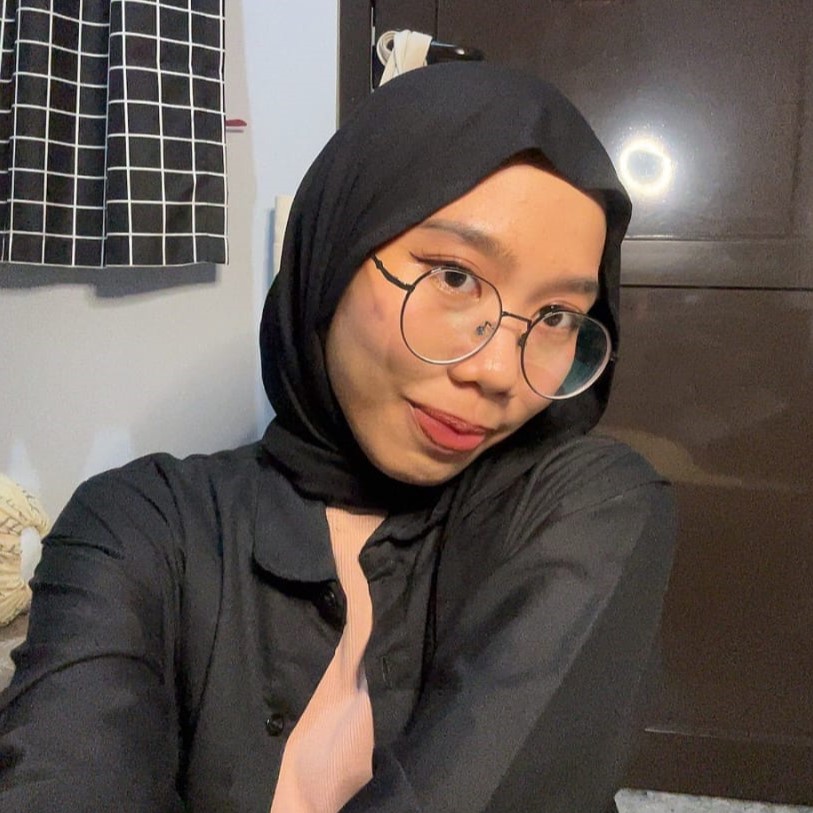
SEO specialist by day, fact-checker by night. An avid reader and content writer dedicated to delivering accurate and engaging articles through research and credible sources.