Corrosion inspection is a vital process that helps identify and assess the damaging effects of corrosion. Employing specialized techniques, this inspection plays a crucial role in ensuring the safety and reliability of structures, equipment, and materials. In this article, we will explore the importance and methodologies of corrosion inspection, highlighting its benefits for various industries. Understanding the fundamentals of corrosion inspection is essential for protecting assets and prolonging infrastructure lifespan.
What Is Corrosion Inspection?
Corrosion inspection involves the assessment and evaluation of corrosion or deterioration in different structures, equipment, or materials. Its purpose is to visually examine and measure the extent of corrosion using specialized tools and techniques. By analyzing the collected data, the condition of the inspected object can be determined.
Corrosion can be caused by factors like moisture, chemicals, temperature changes, or environmental conditions. The inspection aims to identify areas affected by corrosion, gauge the severity of the damage, and develop effective strategies to prevent and mitigate corrosion.
What Is The Difference Between Corrosion Inspection and Monitoring?
Corrosion inspection and corrosion monitoring are two distinct processes that serve different purposes in managing corrosion-related issues. Corrosion inspection involves scheduled assessments to visually examine and evaluate the extent of corrosion on structures, equipment, or materials. Through techniques like:
- visual inspections
- non-destructive testing (NDT), or
- laboratory analysis
Inspectors identify existing corrosion damage, assess its severity, and determine maintenance or repair needs.
Corrosion monitoring, on the other hand, is an ongoing process that continuously collects and analyzes data to track and assess corrosion rates or behavior over an extended period. It employs:
- specialized sensors
- probes, or
- monitoring systems
to gather information on corrosion parameters, such as metal loss, corrosion rates, or environmental conditions. Corrosion monitoring enables the observation of corrosion trends, identification of potential risk areas, and assessment of the effectiveness of corrosion control measures.
Due to the frequency, inspection tools are typically utilized less frequently compared to corrosion monitoring devices, often on an annual basis or even less frequently. However, it is essential to determine the frequency of measurements through a risk-based analysis process in order to establish a program known as “risk-based inspection” (RBI).
What Is The Importance of Corrosion Inspection?
Corrosion inspection holds significant importance across various industries and sectors. Its value lies in several key factors:
1. Safety Assurance
Corrosion can compromise the structural integrity of assets, equipment, and infrastructure. Regular inspections help identify areas affected by corrosion, enabling timely repairs and maintenance. This ensures the safety of personnel, the public, and the environment by minimizing accidents, failures, and potential hazards.
2. Asset Protection and Longevity
Corrosion can lead to the gradual deterioration and degradation of equipment and structures. Through inspections, early signs of corrosion can be detected, allowing for timely interventions to protect assets from further damage. This extends the lifespan of assets, reducing the need for costly replacements and repairs.
3. Cost Savings
Corrosion-related failures and subsequent repairs can be financially burdensome. Regular inspections detect corrosion at an early stage when remediation is less expensive. By proactively addressing corrosion, companies can avoid costly emergency repairs, unplanned downtime, and production losses.
4. Regulatory Compliance
Many industries are subject to regulations and standards concerning corrosion prevention and control. Corrosion inspections ensure compliance with these requirements, mitigating potential legal and regulatory consequences.
5. Optimal Performance
Corrosion adversely affects equipment performance and efficiency, leading to reduced productivity and output. Inspections identify and address corrosion issues, thereby maintaining optimal performance levels and preventing operational disruptions.
6. Preventive Maintenance
Corrosion inspection serves as a valuable tool for proactive maintenance. By regularly assessing asset conditions, maintenance activities can be planned and executed in a timely manner, reducing the likelihood of unexpected breakdowns and prolonging equipment lifespan.
Overall, corrosion inspection plays a critical role in ensuring safety, safeguarding assets, minimizing costs, and optimizing equipment and structural performance. Early detection and remediation of corrosion contribute to operational efficiency, regulatory compliance, and effective maintenance strategies for long-term success.
What Are The Methods of Corrosion Inspection?
There are multiple corrosion inspection methods used to evaluate the severity and extent of corrosion on materials. These techniques aid in identifying corrosion damage, measuring corrosion rates, and determining material conditions. Some common corrosion inspection methods include:
1. Visual Inspection
This method involves visually examining the material’s surface for visible signs of corrosion, such as rust, discoloration, pits, or irregularities.
2. Non-Destructive Testing (NDT)
Non-Destructive Testing (NDT) techniques, like ultrasonic testing, radiographic testing, magnetic particle testing, and liquid penetrant testing, detect hidden or subsurface corrosion without causing harm to the material.
3. Corrosion Monitoring
This technique involves continuous or periodic measurement of corrosion parameters, including corrosion rate, corrosion potential, or electrochemical impedance, to monitor corrosion progression over time.
4. Microscopy
Microscopic examination, using optical or electron microscopy, provides detailed visualization of corrosion patterns and helps identify the underlying corrosion mechanisms.
5. Chemical Analysis
Chemical analysis techniques, such as spectroscopy, chromatography, or wet chemical analysis, determine the composition of corrosion products or the presence of corrosive elements in the environment.
6. Surface Roughness Measurement
Surface roughness measurements, using tools like profilometers or roughness testers, assess the extent of corrosion damage and surface irregularities caused by corrosion.
7. Corrosion Coupons
Corrosion coupons are small metal samples exposed to a corrosive environment for a specific duration. They are later analyzed to determine the extent of corrosion and corrosion rates.
8. Electrochemical Techniques
Electrochemical techniques, like linear polarization resistance, electrochemical impedance spectroscopy, or potentiodynamic polarization, assess corrosion behavior and rates by studying the material’s electrochemical responses.
These corrosion inspection methods are applied based on specific requirements, materials, and corrosion environments. They facilitate material condition evaluation, informed decision-making regarding maintenance and corrosion prevention strategies, and ensure the integrity of structures and equipment.
Corrosion inspection is crucial, especially if you are an aspiring piping inspector. It provides the necessary skills to identify and assess corrosion issues in piping systems, make informed maintenance decisions, and develop effective corrosion control strategies. By detecting and addressing corrosion early on, you can contribute to the longevity and reliability of piping infrastructure.
API 570 is a crucial standard for piping inspectors, highlighting the importance of proper inspection and monitoring. It provides guidelines for conducting inspections, identifying defects, and monitoring corrosion to ensure the safety and reliability of piping systems.
PetroSync offers API 570 course, providing you with essential knowledge and skills in accordance with the important standard for piping inspectors. This training emphasizes the significance of conducting proper inspections and monitoring to ensure the integrity and safety of piping systems.
By enrolling in PetroSync’s API 570 training, you will gain insights into inspection techniques, defect identification, and corrosion monitoring, enabling you to effectively uphold the standards outlined by API 570. Our comprehensive training equips you with the expertise needed to prevent failures, minimize downtime, and maintain the reliability of piping infrastructure.
Credit Header Image: Freepik
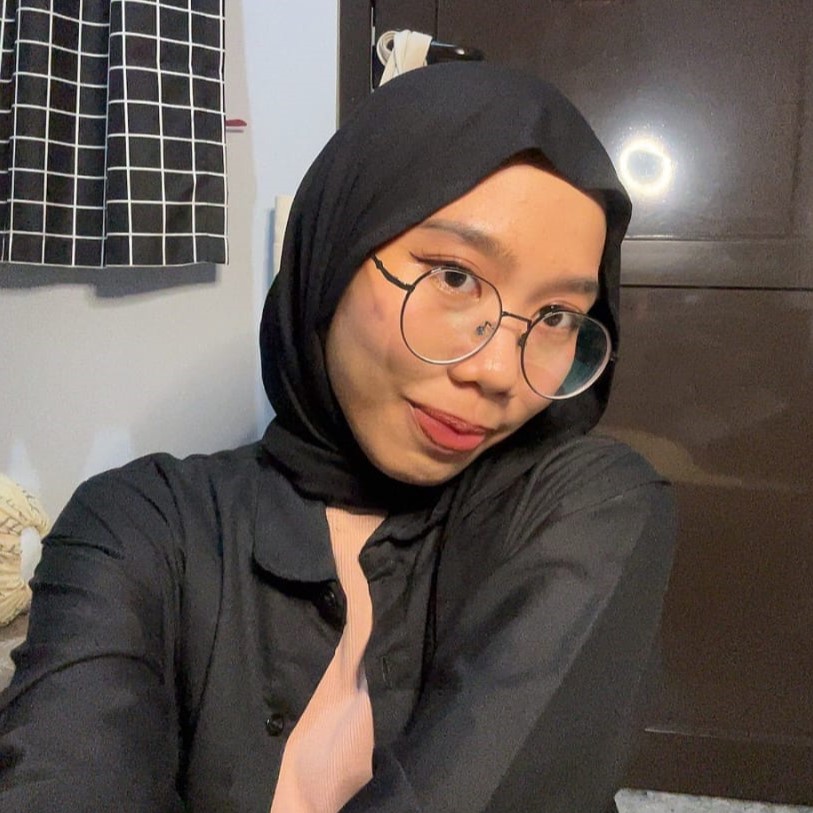
SEO specialist by day, fact-checker by night. An avid reader and content writer dedicated to delivering accurate and engaging articles through research and credible sources.