In high-stakes industries like oil and gas, manufacturing, and energy, the smallest undetected flaw can lead to catastrophic consequences. Ensuring asset integrity isn’t just about technology or regulations—it begins with one of the oldest and most fundamental inspection techniques: visual testing (VT).
Despite advancements in inspection technology, visual testing remains an irreplaceable first line of defense in identifying surface defects, preventing failures, and maintaining operational safety. Before we dive into the detailed methods, tools, and standards, it’s important to first understand what visual testing entails and why it continues to hold such a vital place in industrial operations today.
What is Visual Testing?
Visual testing (VT) is a non-destructive testing (NDT) method where inspectors use their eyes—sometimes aided by instruments like magnifying glasses, borescopes, or cameras—to detect surface anomalies. VT is typically the first and simplest step in any inspection protocol because it can quickly identify visible signs of damage such as cracks, corrosion, or misalignments.
The importance of visual examination dates back centuries, but in modern industries, it has evolved into a structured process supported by international standards like ASME Section V and ISO 17637. While it appears basic, effective visual testing demands significant expertise in lighting conditions, material behaviors, and flaw characterization.
Why is Visual Testing Important in Industrial Inspections?
Visual testing plays a critical role in early fault detection and preventive maintenance strategies. Several reasons underpin its enduring importance:
- Cost-Effective Prevention: Early detection of cracks, corrosion, or deformation avoids expensive repairs and potential system failures.
- Safety Assurance: In sectors such as oil and gas, a minor defect can escalate into an explosion or environmental disaster if undetected.
- Regulatory Compliance: International standards mandate visual inspections as a first step in quality assurance and risk management protocols.
- Efficiency and Speed: VT can quickly assess large surfaces without disrupting operations.
According to a report by the American Welding Society (AWS), effective visual inspection can detect up to 70% of weld defects without needing more invasive methods
Visual Testing Methods and Tools
Visual testing methods are generally categorized based on proximity and accessibility:
Direct Visual Testing (DVT)
- Performed with the naked eye, sometimes enhanced with magnifying glasses or portable lighting.
- Inspectors must be within a close range (usually within 600 mm) to ensure clear visibility.
Remote Visual Testing (RVT)
- Used when direct access is unsafe or impractical.
- Involves tools like borescopes, fiberscopes, videoscopes, or robotic systems to navigate confined spaces or hazardous environments.
Common Tools Include:
- Borescopes: Flexible or rigid tubes equipped with cameras for internal inspections.
- Mirrors and Flashlights: Basic tools to extend visual access.
- Drones: Increasingly used for inspecting tall structures like storage tanks or offshore platforms.
Mastering these methods ensures thorough inspections even in the most challenging environments.
Visual Testing Standards and Codes
To ensure consistency and reliability, several standards guide the application of visual testing:
- ASME Section V – Nondestructive Examination: Outlines procedures for visual inspections of boilers, pressure vessels, and nuclear components.
- AWS D1.1 Structural Welding Code: Sets requirements for visual inspection of welded structures.
- ISO 17637: Provides an international framework for visual examination of welds.
Following these standards is not merely about ticking compliance boxes; it’s about embedding best practices into every inspection process. Organizations adhering to international standards report an average of 30% fewer operational incidents compared to those with minimal compliance efforts.
Visual Testing Procedure: Step-by-Step
An effective visual inspection program typically follows these key steps:
Preparation:
- Review technical drawings, specifications, and previous inspection reports.
- Clean the surface to be inspected from debris, coatings, or rust.
Lighting Setup:
- Ensure adequate lighting (typically 1000 lux minimum) directed appropriately to reveal surface flaws.
Visual Examination:
- Conduct systematic scanning using naked eyes or tools.
- Note and characterize any discontinuities.
Measurement and Evaluation:
- If needed, use calibrated tools (e.g., weld gauges) to measure defect dimensions.
Reporting:
- Document findings clearly with photographs, defect maps, and recommendations for further testing or repairs.
By formalizing the process, companies significantly reduce oversight and improve inspection reliability.
Common Defects Detected Through Visual Testing
Some of the most frequently identified flaws include:
- Surface Cracks: Tiny fractures that can propagate under stress.
- Corrosion and Pitting: Localized material degradation compromising wall thickness.
- Weld Discontinuities: Porosity, undercuts, spatter, or incomplete fusion.
- Surface Deformation: Misalignments, dents, bulging due to overpressure or material fatigue.
Detecting these anomalies early is crucial to ensuring asset longevity and workplace safety.
Future Trends in Visual Testing
The field of visual inspection is rapidly advancing with technology:
- Drone and Robotic Inspections: Access hard-to-reach areas without human exposure to hazards.
- AI-Powered Defect Recognition: Software that analyzes images and identifies flaws faster and more consistently.
- Augmented Reality (AR): Overlay real-time inspection guidance on equipment surfaces.
- Predictive Maintenance Integration: Using visual data trends to forecast asset failure before it happens.
According to McKinsey & Company, leveraging AI and remote technologies in inspections can reduce inspection time by up to 30% and cut operational costs by 20%. These innovations are not replacing human expertise but enhancing it—freeing inspectors to focus on judgment and complex assessments.
Expand Your Expertise: Join PetroSync’s Professional Training
As industries evolve and new technologies redefine asset management, professional skills must advance alongside them. Developing a strong foundation in inspection techniques like visual testing is no longer optional; it’s a strategic necessity for career growth and operational excellence.
At PetroSync, we offer specialized professional training programs designed to equip engineers, technicians, and inspectors with practical, up-to-date knowledge aligned with international standards. Whether you aim to deepen your inspection expertise, strengthen your compliance skills, or prepare for leadership roles in asset integrity, our programs provide the essential tools to achieve your goals.
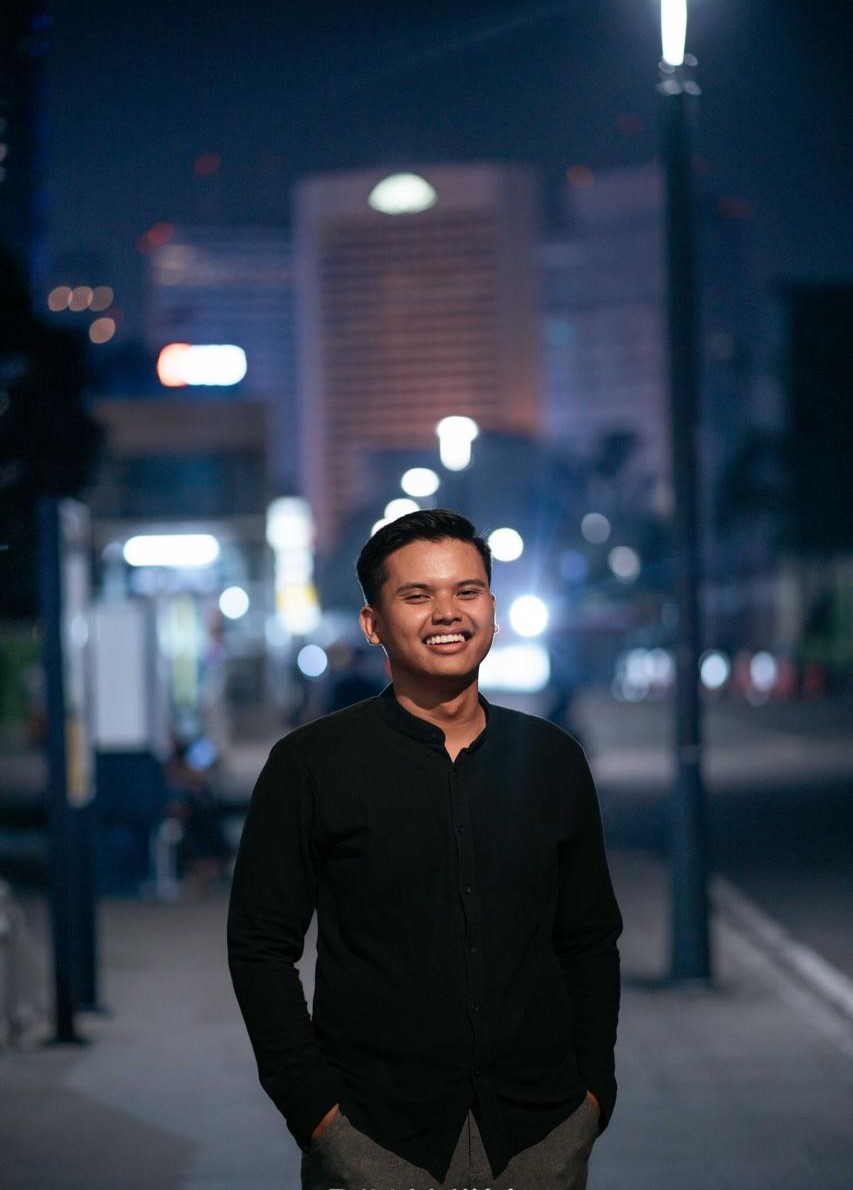
Results-oriented and thorough SEO specialist with extensive experience in conducting keyword research, developing and implementing digital website promotion strategies and plans, managing campaigns to develop company websites in the digital world, excellent knowledge of marketing techniques and principles, and attentive strong attention to detail.