API 936 provides essential standards for the proper installation, inspection, and testing of refractory materials in high-temperature industries. Sectors like oil and gas, petrochemical, and power generation rely heavily on refractory linings to protect critical equipment from extreme heat, chemical corrosion, and mechanical stress.
However, using refractory materials alone is not enough. Ensuring their quality and proper application requires compliance with industry-approved guidelines — and that’s where API 936 Certification comes in. This certification ensures refractory linings meet strict safety, durability, and performance standards.
So, what exactly is API 936? What does an inspector do? And how can you prepare to get certified? Let’s dive in.
What Is API 936?
API 936 is an American Petroleum Institute (API) standard that specifies standards for the installation and quality management of refractory linings. Refractories, which are materials that can survive high temperatures and severe environments, are critical in industries such as oil and gas, petrochemical, and energy.
These materials safeguard critical equipment, ensuring its safe and efficient functioning at extreme temperatures. The standard assures that they correctly install and inspect refractory materials to meet safety and performance standards This encompasses everything from material selection to installation practices and quality testing.
All of which contribute to lower downtime, fewer equipment failures, and higher operating efficiency. API 936 Certification is a recognized accreditation that recognizes individuals who can apply these requirements. This accreditation validates competence in managing refractory installations and conducting inspections, ensuring that all materials meet the highest quality standards.
This qualification shows how professionals can safeguard equipment integrity, eliminate risks, and assure long-term operational reliability, which sectors that use refractory materials highly value.
What is API 936 Refractory?
Refractory materials are essential in industries such as oil, gas, petrochemicals, and energy because they protect equipment that operates at high temperatures and under extreme conditions. These materials must survive severe temperatures, chemical exposure, and mechanical stress, therefore proper installation and inspection are vital.
Refractory refers to the American Petroleum Institute’s precise rules for selecting and using refractory materials that meet stringent safety and performance requirements. Refractories are designed to endure high temperatures, prevent corrosion, and maintain structural integrity in the harshest industrial settings.
From furnaces to reactors and kilns, these materials serve as protective barriers, insulating equipment from high temperatures and lowering the risk of failure. The standard assures that refractory materials are not only of excellent quality, but are also placed in accordance with best practices to maximize durability and performance.
Refractory Personnel Certification is an industry-accepted accreditation for inspectors that establishes a standard for those trained in refractory systems. This certification indicates that inspectors have a solid understanding of the API STD 936 refractory installation quality control guidelines.
Certified specialists are trusted to ensure that refractory materials meet high industry requirements, making this qualification extremely valuable in firms that rely on refractory systems to run safely and efficiently.
What Is API 936 Inspector?
An API 936 Inspector is a trained specialist in charge of supervising the installation and quality control of refractory materials in accordance with the requirements. They play an essential role in ensuring that they correctly install refractory linings and make them function effectively in challenging environments.
The inspectors possess a deep understanding of the technical aspects of refractory materials and thoroughly understand the specific requirements outlined by the API 936 standards. Inspectors are responsible for a variety of activities, including confirming material requirements, inspecting installation processes, and conducting tests to ensure the integrity of the refractory lining.
Their expertise helps guarantee that they identify and address any potential flaws early on, preventing costly repairs or downtime later. The industry highly values API 936 Inspector certification since it demonstrates a high degree of knowledge in quality assurance for refractory systems.
What Is API 936 Study Material?
API 936 inspectors are licensed specialists in charge of supervising the installation, quality control, and maintenance of fire-resistant coatings in industrial settings. These inspectors are critical in verifying that fireproof systems meet criteria and can endure the rigors of high-temperature conditions.
The primary responsibilities of API 936 inspectors are:
Ensure that the materials used in the fireproof installation meet API specifications.
Monitoring the installation process to ensure that correct procedures are followed.
Testing the installed fire-resistant layer to ensure its integrity and performance.
Identifying and documenting any flaws or concerns that may affect the effectiveness of the fire-resistant coating.
To become an API 936 inspector, professionals must first pass a certification exam that assesses their knowledge of refractory materials, installation techniques, and quality control procedures. This qualification assures that inspectors have the competence required to keep industrial processes safe and efficient.
What Are The Key Aspects of API 936?
To better understand API 936, let’s divide it down into its primary components:
1. Refractory Materials
API 936 digs into the world of refractory materials, offering engineers a thorough understanding of their properties, classifications, and uses.
2. Inspection and Testing
One of main objectives is to ensure the quality of refractory installations. This includes rigorous inspection and testing methods that meet the highest industry requirements.
3. Installation Guidelines
Learn about the best methods for installing refractory materials. Describes the methods and strategies that engineers must use to ensure a successful installation.
4. Repairs and Maintenance
Learn how to analyze and manage potential difficulties that may develop during the refractory materials’ lifecycle. Provides guidelines on repair and maintenance to help installations last longer.
How Are The Implementation of API 936 in The Industry?
API 936 provides essential guidelines for handling high-temperature materials in the oil and gas industry, ensuring safety and efficiency. The industry must follow API 936 norms and regulations to ensure the safe and efficient use of high-temperature materials. A true case study shows this:
Case Study: Refractory Lining in a Petrochemical Plant
In a petrochemical plant, there was a need to replace the refractory lining in a high-temperature furnace for safety and efficiency reasons. The company chose to apply API 936 standards to this project.
Implementation Steps:
1. Material Selection:
Following API 936 guidelines, the company carefully chose refractory materials that matched the furnace’s specific temperature and chemical requirements.
2. Inspection and Testing:
Certified inspectors rigorously examined the selected materials to ensure they met strict quality standards.
3. Installation Practices:
A team of API 936-certified professionals followed the best practices outlined in the standard to accurately install the refractory materials.
Results:
Through the implementation, the company successfully upgraded the furnace’s refractory lining with precision and safety. The advantages included:
Enhanced Safety:
The new lining compiled with API safety standards, reducing the risk of accidents and ensuring the protection of workers and assets.
Improved Efficiency:
The chosen materials and installation techniques optimized the furnace’s performance, enhancing operational efficiency.
Extended Lifespan:
Implementing API 936 guidelines extended refractory lining lifespan, reducing replacements and costs while improving safety and efficiency.
Get Certified in API 936: Become a Refractory Expert with PetroSync
PetroSync recognizes API 936’s value in the oil and gas industry. PetroSync provides a complete API 936 training program to assist professionals in taking advantage of the standard’s benefits. This training intends to provide engineers and industry workers with the information and skills they need to successfully implement.
By taking the PetroSync program, you will be able to improve your refractory installation skills and confidently utilize concepts in your job. This training is an excellent investment in your career growth in the oil and gas industry.
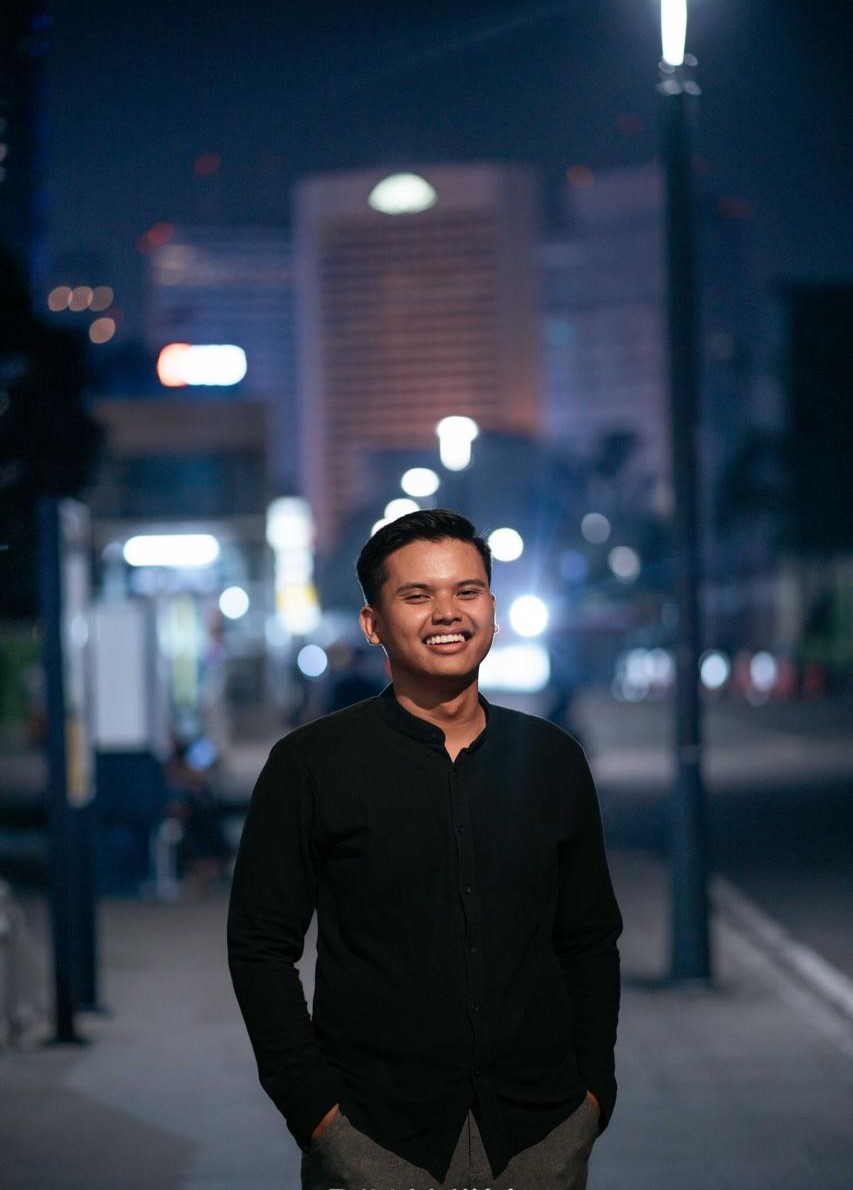
Results-oriented and thorough SEO specialist with extensive experience in conducting keyword research, developing and implementing digital website promotion strategies and plans, managing campaigns to develop company websites in the digital world, excellent knowledge of marketing techniques and principles, and attentive strong attention to detail.