Weld buildup is a crucial technique in welding and fabrication. Weld buildup, also known as weld overlay or hard facing, helps make the surface of equipment stronger and more durable. In this article, we will explore why weld buildup is important, where it is used, and how it is done along with the calculation formula.
What Is Weld Buildup?
Weld buildup is a process of adding weld metal to a base metal surface, the edge of a joint, or previously deposited weld metal to restore the component to the required dimensions. The added coating is applied via a fully or partially molten phase. When both the substrate and coating materials are melted, a metallurgical bond is formed in between.
Weld buildup is commonly employed in industries like manufacturing and construction to repair worn or damaged parts and reinforce critical areas. The key is to select the right welding materials and techniques to achieve the desired strength and durability.
What Is The Difference between Weld Build-up and Buttering?
Buttering and buildup are different in their purposes. Buttering is primarily used for metallurgical reasons, such as PWHT (Post Weld Heat Treatment) deduction, preventing lamellar tearing, avoiding reheat cracking, or dissimilar welding.
In contrast, the main objective of buildup is not dimensional control, but rather to strengthen and reinforce a joint or surface by adding extra material through welding.
Buttering is a variation of surface welding where weld metal is applied to one or multiple surfaces. Its purpose is to create a metallurgically compatible weld metal that can be used for the final welding process.
What Is Cladding in Weld Buildup?
Cladding is the application of one material onto the surface of a welded joint to create a protective skin or layer. Cladding is used to enhance the appearance of the joint and protect the underlying metal against corrosion.
What Is The Purpose of Weld Buildup?
The primary objective of weld buildup is to enhance the strength and durability of a joint or surface by adding extra material through welding. This technique is utilized not only to repair worn-out or damaged parts but also to improve dimensional control, fill gaps, or alter the shape of a component.
Moreover, weld buildup is employed for creating metallurgically compatible welds, preventing certain types of welding defects, and providing a reliable foundation for subsequent welding processes.
What Are The Applications of Weld Buildup?
Weld buildup finds application in various industries and scenarios. Some of the common areas where weld buildup is utilized include:
1. The Buildup of Worn Surfaces
When surfaces undergo wear or erosion, weld buildup is used to add material and rebuild them to their original specifications.
2. Dimensional Control
Weld buildup allows for precise control over component dimensions, filling gaps, creating specific shapes, and ensuring proper fitment between parts.
3. Metallurgical Compatibility
Weld buildup is employed to create welds between dissimilar materials that are metallurgically compatible, resulting in a strong and reliable bond.
4. Preventing Welding Defects
It helps prevent defects like cracking, tearing, or distortion during subsequent welding processes.
5. Strengthening Critical Areas
In specific applications, weld buildup reinforces critical component areas subjected to high stress or mechanical loads.
6. Extending Component Life
By repairing and strengthening components, weld buildup prolongs their useful life, reducing the need for replacements.
7. Repairing Castings
Weld buildup can fix defects in castings and molds, allowing them to be salvaged and reused.
8. Hardfacing
Weld buildup is also used for hard-facing, where a wear-resistant material is deposited on a surface to enhance its resistance to abrasion and erosion.
9. Repair and Maintenance
Weld buildup is commonly applied to fix worn-out or damaged machinery parts, equipment, and structures, restoring their original dimensions and functionality.
In the oil and gas, petrochemical, and power plants industries, weld buildup becomes one of the recommended repair methods for certain types of damage or defects. For example, if a pressure vessel or piping system has experienced erosion or wear in a critical area, weld buildup might be utilized to rebuild the affected surface and prevent further degradation.
How Is Weld Buildup for Pressure Vessel Performed?
According to ASME PCC-2, when performing weld buildup for a pressure vessel, the following steps are involved:
1. Inspection and Assessment
Before starting any repairs, a thorough inspection and assessment of the pressure vessel must be carried out. This helps identify the areas requiring weld buildup and assess the extent of the damage to determine the appropriate repair approach.
2. Repair Procedure Selection
ASME PCC-2 provides guidelines for choosing the right repair procedure, including weld buildup, based on the type and severity of the damage. The standard outlines various repair techniques, and weld buildup might be selected if deemed suitable for the specific situation.
3. Welding Procedure Specification (WPS)
Once weld buildup is chosen as the repair method, a Welding Procedure Specification (WPS) is prepared. The WPS outlines the specific welding parameters, such as welding method, filler material, preheating, and post-weld heat treatment (if required).
4. Surface Preparation
The surfaces to be welded are prepared by removing contaminants, coatings, or damaged material to ensure a proper bond during the weld buildup process.
5. Weld Buildup
The welding process is then performed to add extra material to the pressure vessel’s damaged or worn surfaces. Welders follow the approved WPS to achieve a strong and reliable weld with the desired properties.
6. Quality Control
Throughout the weld buildup process, strict quality control measures are applied to ensure the integrity and reliability of the repair. This includes non-destructive testing (NDT) techniques like ultrasonic testing, radiographic testing, or dye penetrant inspection to verify the weld’s quality.
7. Post-Weld Heat Treatment (PWHT)
Depending on the material and extent of the repair, post-weld heat treatment may be necessary to relieve residual stresses and improve the weld’s properties.
8. Inspection and Certification
After completing the weld buildup, a final inspection is conducted to ensure that the repair complies with all applicable codes and standards, including ASME PCC-2. Once the repair is deemed satisfactory, the pressure vessel is certified for safe operation.
It’s crucial to note that the specific steps of the weld buildup process may vary depending on the particular circumstances, materials involved, and the specific requirements outlined in ASME PCC-2.
Performing weld buildup in pressure vessels correctly and following the guidelines can bring numerous advantages. By adhering to the recommended procedures in ASME PCC-2, the repair process ensures the vessel’s integrity and safety.
Proper weld buildup helps restore damaged or worn surfaces, prolongs the vessel’s lifespan, and prevents further deterioration. Using approved welding parameters and quality control measures results in a strong and reliable weld with the desired properties.
Weld buildup finds a prominent place among the subjects covered within PetroSync’s ASME PCC-2 training. This specialized program delves into the intricacies of weld buildup techniques, ensuring you acquire a solid understanding of their significance in enhancing structural integrity and reliability across industries.
PetroSync’s dedication to excellence is evident in its ASME PCC-2 training, which comprehensively explores various weld buildup methods critical for effective maintenance and repair. This program equips you with essential knowledge to address structural challenges and maintain operational efficiency.
The training is thoughtfully designed to encompass a wide spectrum of crucial topics, ensuring you acquire the skills required to navigate complex scenarios and contribute significantly to successful weld buildup activities.
Elevate your expertise by enrolling in the ASME PCC-2 training with PetroSync. Gain practical insights into weld buildup techniques and enhance your ability to ensure structural soundness. Join us in learning the practicality of weld buildup and its application through PetroSync’s expert guidance!
Credit header image: Pexels
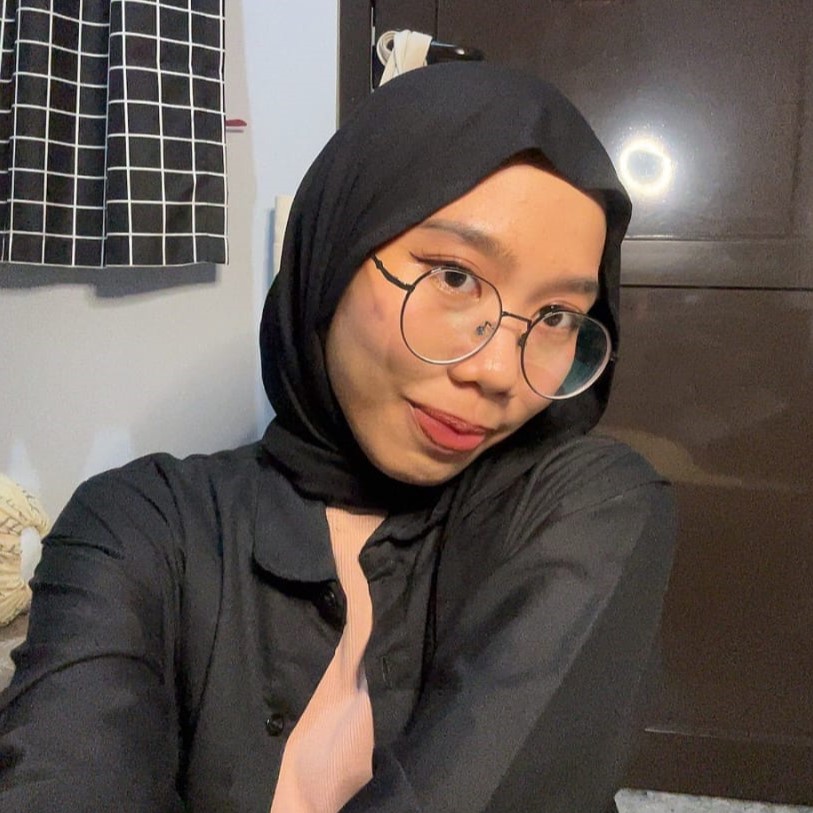
SEO specialist by day, fact-checker by night. An avid reader and content writer dedicated to delivering accurate and engaging articles through research and credible sources.