In the oil, gas, petrochemical, and energy industries, pressure vessel integrity is critical to ensuring safety and efficiency. Regular inspections, in accordance with industry standards such as API 510, are critical in maintaining this integrity. API 510 certification provides individuals with the specialized skills and in-depth knowledge needed to properly inspect, appraise, and repair pressure vessels.
This accreditation not only helps to decrease operational risks, but it also ensures that vessels adhere to strict regulatory and safety standards, protecting both assets and personnel.
What Is an API 510 Inspector?
An API 510 Inspector is a highly skilled and certified professional in charge of inspecting, repairing, and altering pressure vessels while they are in service, with comprehensive knowledge of these critical tasks. Certified API 510 inspectors are critical in ensuring that pressure vessels fulfill the strict standards established by the American Petroleum Institute (API), specifically the API 510 standard.
Their duties range from assessing the condition of pressure vessels to detecting early symptoms of wear, corrosion, or damage that could jeopardize safety and efficiency. These inspectors are responsible for proposing timely maintenance or repairs to avoid costly breakdowns and ensuring that boats comply with tight regulatory and industry standards.
To accomplish this, inspectors must pass the demanding API 510 exam, which is meant to assess their overall expertise of pressure vessel maintenance, inspection, repair, and change. API 510 pressure vessel inspections use their comprehensive knowledge to help extend the operating life of pressure vessels, improve safety standards, and maintain the reliability of equipment in some of the most challenging industrial situations.
Their work not only ensures operational efficiency but also reduces risks, making them important in businesses where safety and reliability are critical.
What Is a Pressure Vessel Inspection?
A pressure vessel inspection is a detailed process to check the structural integrity, safety, and reliability of the vessel. The goal is to find any signs of corrosion, cracks, or other damage that could weaken the vessel’s ability to handle internal pressure. These inspections can be performed visually or by non-destructive testing (NDT) techniques.
Which allow for a thorough examination without causing damage to the vessel. Regular inspections are critical for preventing accidents and reducing unplanned downtime, making them an important component of industrial safety measures.
What Is The API Standard For Pressure Vessel Inspection?
Professionals widely use the API 510 standard, also known as the ‘Pressure Vessel Inspection Code: In-Service Inspection, Rating, Repair, and Alteration,’ to inspect, repair, and maintain pressure vessels. This certification and standard guide inspectors to regularly examine and maintain pressure vessels, ensuring they remain in excellent working condition according to best industry practices.
It explains how to conduct inspections, including how frequently they should be performed, the procedures to be followed, and critical safety concerns to be made. Inspectors and maintenance teams may ensure that pressure vessels perform within their original design limits by complying to the API 510 standard, reducing the possibility of failure, which could result in safety hazards or costly downtime.
The standard highlights not only the vessel’s condition, but also the importance of regular maintenance and repair to keep the equipment functioning safely and efficiently for as long as possible. API 510 pressure vessel inspections is widely used in the oil and gas, petrochemical, and energy industries because it ensures a consistent level of safety and performance.
Facilities that follow this criterion are more likely to remain in regulatory compliance and prevent costly accidents or failures. In short, API 510 helps to build a reliable system for managing pressure vessels, which leads to safer operations, fewer failures, and more efficient processes overall.
How To Inspect a Pressure Vessel?
Pressure vessel inspection uses a variety of procedures to detect faults or weaknesses that could jeopardize their safety and performance. The following are the most typical methods used for pressure vessel inspections:
1. Visual Testing
Visual testing (VT) is the most basic yet essential form of inspection. It involves a thorough visual examination of the pressure vessel’s external and internal surfaces. Inspectors look for visible signs of wear, corrosion, cracks, or any other damage that may affect the vessel’s ability to withstand pressure.
This method is often the first step in the inspection process and can reveal obvious defects that need further evaluation. Visual testing is cost-effective and non-invasive, making it a standard procedure in regular inspections.
2. Ultrasonic Testing
Ultrasonic testing (UT) is a non-destructive testing (NDT) technique that employs high-frequency sound waves to find interior faults in a pressure vessel. An ultrasonic transducer is put on the vessel’s surface, causing sound waves to pass through the material.
If there are any cracks or voids within the vessel, the sound waves will reflect back, providing precise measurements of the defect’s size and location. Ultrasonic testing is particularly effective in detecting internal corrosion and fractures that would otherwise go undetected.
3. Radiographic Testing
Radiographic testing (RT) uses X-rays or gamma rays to inspect the internal structure of pressure vessels. This technique produces an image of the vessel’s interior, allowing inspectors to detect hidden flaws such as cracks, voids, or inclusions within the material. Radiographic testing is especially beneficial for inspecting welded connections, which are prone to flaws.
It provides a clear view of the inside condition while inflicting no damage to the vessel, making it an important instrument for guaranteeing structural integrity.
4. Magnetic Particle Testing
Magnetic particle testing (MT) is another non-destructive testing method used to detect surface and near-surface flaws in pressure vessels made from ferromagnetic materials. The procedure entails magnetizing the vessel and attaching magnetic particles to its surface.
If there is a crack or other fault, the magnetic field will induce particles to concentrate around it, allowing the inspector to see it. This approach is quite good in detecting surface flaws like cracks, seams, and laps.
5. Dye Penetrant Testing
Dye penetrant testing (DPT) is a common technique for finding surface fractures or defects in non-porous materials. The procedure entails adding liquid dye to the vessel’s surface. After allowing it to penetrate any defects, the technician removes the excess dye and applies a developer to highlight the flaws.
Inspectors use this technique to detect minor surface flaws that visual inspections might miss. They commonly apply it to nonferrous materials where magnetic particle testing doesn’t work.
What Are The Benefits Of API 510?
API 510 pressure vessel inspections provides tremendous benefits for both professionals and enterprises. For inspectors, it not only validates their expertise in pressure vessel inspection but also opens up more career opportunities.
The certification goes beyond just earning a credential—it enhances career prospects, promotes higher safety standards, ensures strict compliance with regulations, and encourages continuous professional development. Qualified API 510 inspectors help businesses examine pressure vessels to the highest standards, reducing the risk of accidents and costly repairs.
Furthermore, API 510 certification assists firms in remaining compliant with industry requirements, which improves both safety and operational efficiency.
Enhance Your Skills in API 510 Pressure Vessel Inspection with PetroSync
PetroSync‘s specialized API 510 training can help you improve your pressure vessel inspection skills. Our courses provide in-depth knowledge and practical experience, equipping you with the skills required to reach the highest industry requirements. Enroll in our API 510 program to become a certified inspector who will ensure the safety and dependability of your organization’s pressure vessels.
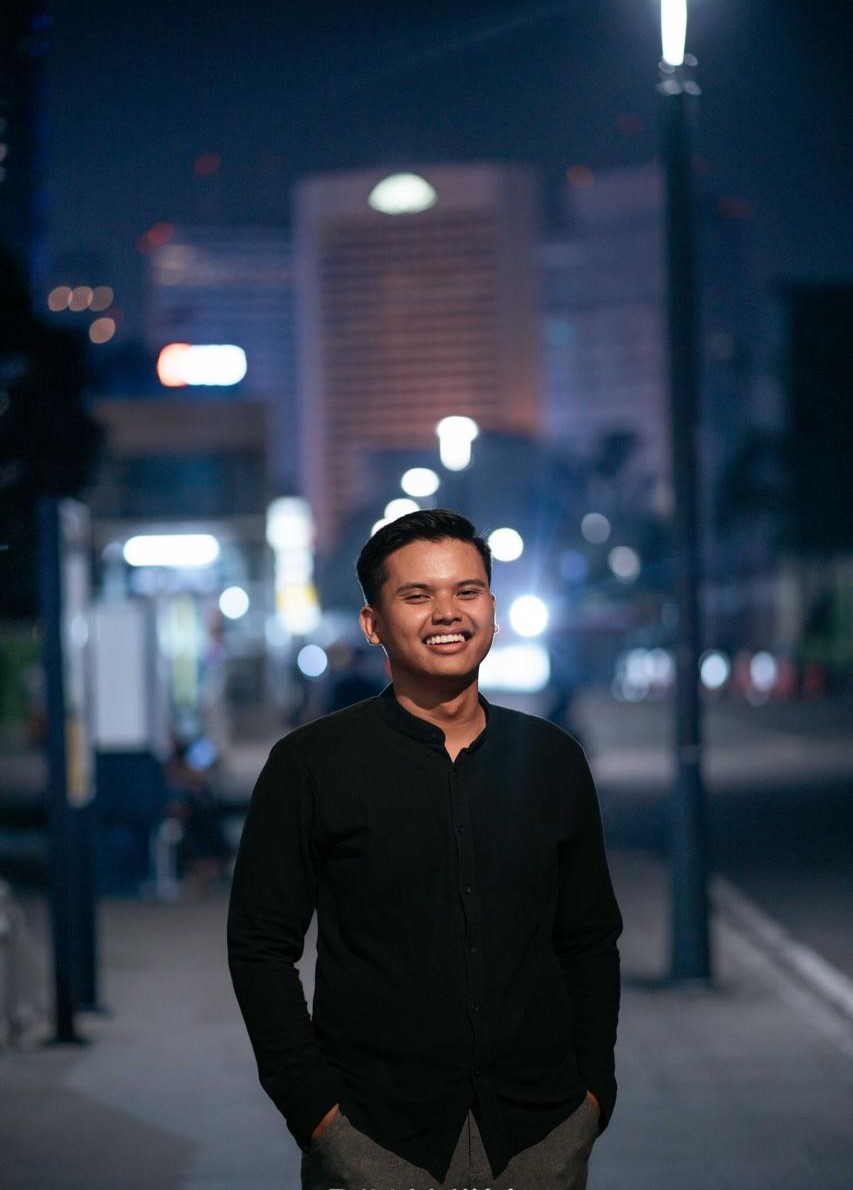
Results-oriented and thorough SEO specialist with extensive experience in conducting keyword research, developing and implementing digital website promotion strategies and plans, managing campaigns to develop company websites in the digital world, excellent knowledge of marketing techniques and principles, and attentive strong attention to detail.