The API 570 inspector plays a critical role in preserving pipeline integrity for safety and efficiency in the oil and gas, petrochemical, and energy industries. The API 570 inspector establishes a plumbing system that meets predefined international requirements.
The standards are intended to decrease the risk of corrosion, erosion, and damage that could impair system function. As a result, it is critical to learn how to conduct proper pipe inspections according to API 570.
What Is an API 570?
API 570 is a standard developed by the American Petroleum Institute (API) that specifies the procedures for inspecting, repairing, changing, and rerating in-service pipe systems. This is especially important in industries like refining and chemical processing, where process pipe integrity is key to safety and efficiency.
The standard requires annual inspections of piping systems to prevent corrosion and material degradation, which can result in leaks, failures, or dangerous circumstances. Companies who adhere to API 570 can reduce costly downtime, preserve safety, and comply with regulatory obligations while safeguarding people and the environment.
What Does API Code 570 Mean?
API Code 570 specifies the methods and procedures for assessing operational pipe systems. It provides the inspection intervals, techniques, and corrective actions needed to ensure the safety and reliability of these systems. This code is crucial for keeping piping systems operational and safe, reducing the danger of leaks and catastrophic failure.
What Is an API 570 inspector?
API 570 inspector is critical for ensuring the safety and dependability of in-service pipe systems, notably in industries like oil, gas, and chemical processing. These inspectors are in charge of verifying piping integrity, recognizing dangers such as corrosion or material degradation, and discovering faults while keeping operations running smoothly.
Their knowledge of corrosion rates, material thickness, and probable faults aids in the prevention of costly breakdowns and shutdowns. Inspectors use the API 570 standard to help organizations extend the life of their pipe systems, manage maintenance schedules, and ensure regulatory compliance.
Finally, API 570 inspectors are essential for assuring safe, efficient, and risk-free operations that protect the environment and workers while minimizing financial losses.
What Is The Latest edition of API 570?
The API 570 standard describes how to inspect, repair, rerate, and alter metal and fiberglass-reinforced plastic (FRP) pipe systems. It also explains the pressure relief devices that are attached to these systems. The most recent amendment to this standard, known as the 5th Edition, was released in February 2024 to reflect current industry practices and safety norms.
Professionals and organizations can ensure that their pipe systems maintain the highest levels of integrity and functioning by adhering to the current criteria.
What Are The Types Of Inspections in API 570?
API 570 specifies many methods of inspections for determining the condition and safety of pipe systems. Each category is designed to ensure that any concerns are discovered and handled as soon as possible.
1. Internal Visual Inspection
This inspection entails a thorough study of the internal surfaces of piping systems. It is normally carried out during shutdowns, when the piping may be accessed securely. Inspectors look for evidence of corrosion, erosion, or other internal deterioration that could jeopardize the system’s integrity.
2. On-stream Inspection
An on-stream examination is carried out while the pipe system is still in operation. This form of examination is important for detecting surface problems like leaks or exterior corrosion without interrupting the process.
3. Thickness Measurement Inspection
This examination focuses on measuring the thickness of piping walls using non-destructive testing (NDT) techniques such as ultrasonic testing. Thickness measurement helps to determine corrosion rates and anticipate the remaining life of the piping system.
4. Various NDE Examinations
Non-Destructive Examinations (NDE) are a collection of procedures for detecting defects in piping systems without inflicting any damage. These procedures include radiography, ultrasonic testing, and magnetic particle inspection, all of which provide important information about the piping’s condition.
5. External Visual Inspection
External visual inspections are performed to determine the external condition of the piping system, including supports, insulation, and protective coatings. This inspection aids in the identification of problems such as exterior corrosion, misalignment, or mechanical damage.
6. Vibrating Piping Inspection
This inspection determines the impact of vibration on piping systems, which may lead to fatigue breakdowns over time. Inspectors monitor and evaluate vibration levels to determine whether mitigation procedures are required.
7. Supplemental Inspection
In some situations, you may need extra inspections, depending on the dangers connected with the piping system. These supplementary inspections may include more extensive NDE procedures or specialized techniques tailored to certain materials or situations.
How To Obtain API 570 Inspector Certification?
Candidates for API 570 inspector must go through a certification process administered by the American Petroleum Institute (API). This process include completing particular educational and experience criteria, passing a difficult exam, and proving understanding of the API 570 code and related inspection methodologies.
Inspectors must renew their certification every three years after they become certified to ensure they are up to date on the newest standards and procedures.
The Role of an API 570 Inspector with PetroSync
PetroSync offers high-quality training for API 570 inspectors, who are responsible for assuring the integrity of piping systems in industries such as oil, gas, and petrochemicals. PetroSync-trained API 570 inspectors are proficient at detecting corrosion and material degradation using a variety of inspection procedures, including non-destructive testing (NDT).
PetroSync’s courses ensure that inspectors not only receive actual experience inspecting piping systems, but also stay current on regulatory standards. This comprehensive training assists inspectors in reducing risks, preventing breakdowns, and maintaining the safety and efficiency of piping systems, resulting in long-term operating reliability.
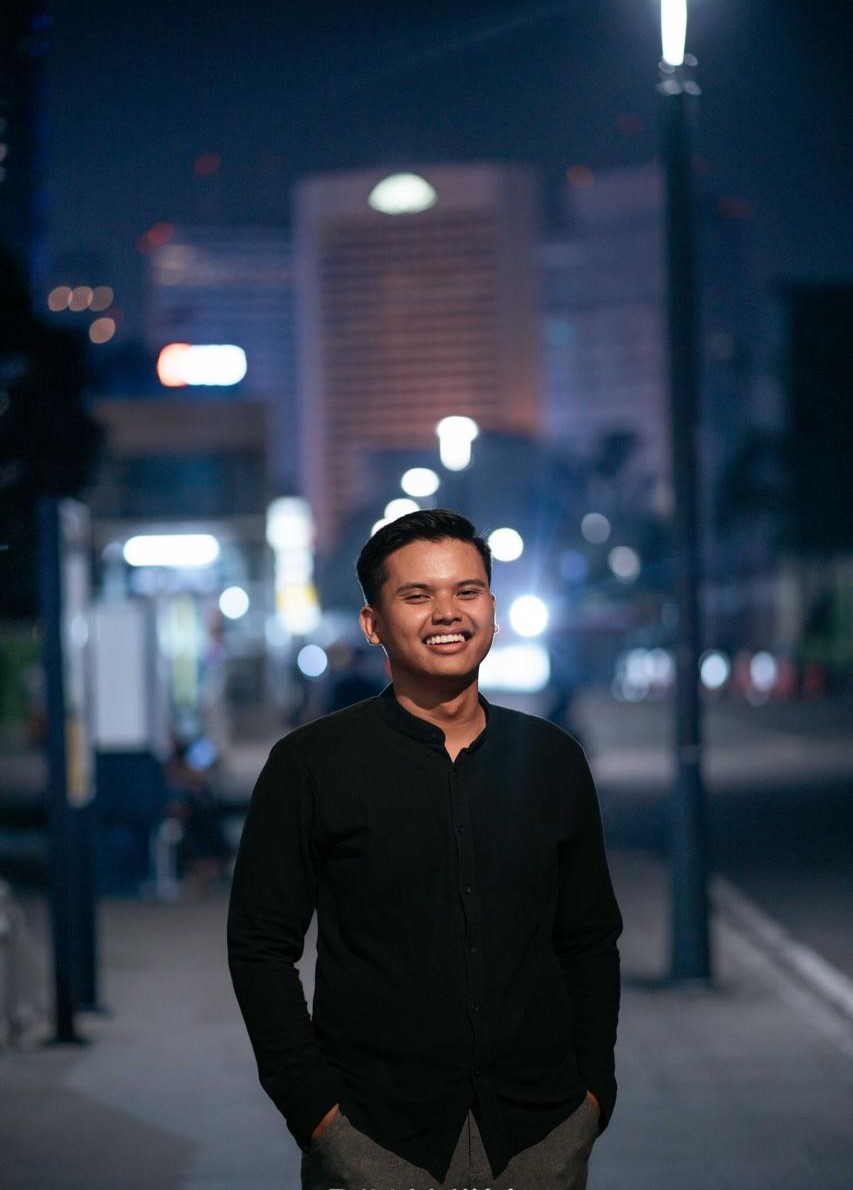
Results-oriented and thorough SEO specialist with extensive experience in conducting keyword research, developing and implementing digital website promotion strategies and plans, managing campaigns to develop company websites in the digital world, excellent knowledge of marketing techniques and principles, and attentive strong attention to detail.