What Is API 936 Body of Knowledge?
The API 936 Body of Knowledge refers to the comprehensive set of information and principles that you can study for the API 936 exam. This body of knowledge encompasses the essential topics and concepts related to materials and equipment used in construction and inspection within the oil and gas industry.
API 936 serves as a guide for you outlining the areas you must be familiar with to pass the API 936 exam successfully. Mastery of the API 936 Body of Knowledge ensures that you have a solid foundation in the standards and best practices governing your field, enhancing your materials and inspection engineering capabilities within the specified sectors.
What Publications Are Mentioned in API 936 Body of Knowledge?
1. API Standard 936 Refractory Installation Quality Control Guidelines – Inspection and Testing Monolithic Refractory Linings and Materials
API Standard 936 provides comprehensive guidelines for quality control while installing monolithic refractory linings and materials. It focuses on inspection and testing processes, ensuring adherence to industry standards.
2. API TR 978 – Monolithic Refractories: Manufacture, Properties, and Selection
API Technical Report (TR) 978 delves into monolithic refractories’ manufacture, properties, and selection criteria. This report offers valuable insights for professionals involved in producing and applying these materials.
3. API TR 979 Applications of Refractory Lining Materials
API TR 979 focuses on the practical applications of refractory lining materials. It guides the effective use of these materials in various industrial settings, ensuring their optimal performance.
4. API TR 980 – Monolithic Refractories: Installation and Dryout
API TR 980 concentrates on the installation and dryout processes of monolithic refractories. This technical report outlines best practices for ensuring the proper and efficient installation of these materials.
5. ASTM Publications: C113-14 (2019) – Standard Test Method for Reheat Change of Refractory Brick
ASTM C113-14 establishes a standardized test method for assessing the reheat change of refractory brick. This method consistently evaluates the refractory brick’s performance under varying temperature conditions.
6. ASTM Publications: C133-97 (2021) – Standard Test Methods for Cold Crushing Strength and Modulus of Rupture of Refractories
ASTM C133-97 outlines standard test methods for determining the cold crushing strength and modulus of rupture of refractories. These methods provide essential metrics for assessing the mechanical properties of refractory materials.
7. ASTM Publication: C181-11 (2018) – Standard Test Method for Workability Index of Fireclay and High-Alumina Plastic Refractories
ASTM C181-11 offers a standard test method for determining the workability index of fireclay and high-alumina plastic refractories. This method aids in evaluating the ease with which these materials can be molded and shaped during installation.
8. ASTM Publication: C704-15 -Standard Test Method for Abrasion Resistance of Refractory Materials at Room Temperatures
ASTM C704-15 establishes a standard test method for evaluating the abrasion resistance of refractory materials at room temperatures. This method ensures consistent assessment of a refractory material’s ability to withstand wear under normal operating conditions.
What Topics Are Mentioned in API 936 Body of Knowledge?
The API 936 Body of Knowledge topics address various subjects associated with quality control in refractory installation.
1. Laboratory Testing Procedures
1. | Terms and definitions | |
2. | Test methods (e.g., C704, CCS, PLC, Density) and related calculations | |
3. | Material Qualification | |
4. | Testing equipment, sample preparation techniques, dimensional requirements for test specimens | |
5. | Various materials utilized (for example, plastic, ceramic fiber, anchor, metal fiber, corrosion coatings, etc. | |
6. | Curing and firing procedures | |
7. | Acceptance/rejection criteria | |
8. | Responsibilities of personnel and documentation requirements. |
2. Applicator and Material Qualification
1. | Installation methods (e.g., gunning, casting, ramming, and hand packing) | |
2. | Sampling and sample preparation procedures | |
3. | Terms and definitions | |
4. | Procedures for determining optimal water content and mixing | |
5. | Applicable formulation and manufacturing information | |
6. | Applicable knowledge of equipment and qualification process | |
7. | Applicable test panel/mockup requirements | |
8. | Applicable environmental controls | |
9. | Surface preparation requirements | |
10. | Responsibilities of personnel and documentation requirements |
3. Installation
1. | Terms and definitions | |
2. | Responsibilities of personnel and documentation requirements | |
3. | Knowledge of detailed execution plan including design details and quality standards | |
4. | Packaging and storage requirements | |
5. | Surface preparation and cleanliness requirements | |
6. | Anchor: welding, layouts, patterns, materials | |
7. | Frequency and methods of production sampling: gunning, casting, hand packing | |
8. | Water addition: quantity and temperature, mixing procedures | |
9. | Fiber addition: percentage, material, mixing | |
10. | Installation of environmental controls (minimum and maximum temperatures) | |
11. | Gunite procedures and equipment, including variables that affect gunite quality (i.e., air pressure, humidity, temperature, aging, water pressure, water purity, additives) | |
12. | Knowledge of flash set | |
13. | Casting procedures and equipment (e.g., air vibrator, vibrator frequency, vibrator sizing, forming, setup) | |
14. | Ramming / Hand-packed procedures and equipment |
4. Inspection
1. | Terminology, job specifications, application standards | |
2. | Inspection and data collection procedures | |
3. | Lining design and installation requirements | |
4. | Visual and nondestructive test methods and qualification testing methods | |
5. | Application/limitation for various inspection techniques (for example, hammer testing, sonic testing, radiography, core sampling, portable abrasion testing) | |
6. | Material verification and traceability | |
7. | Acceptance and rejection criteria | |
8. | Repair procedures | |
9. | Curing and dry out procedures | |
10. | Inspectors’ and contractors’ responsibilities | |
11. | Record-keeping systems and requirements |
5. Post-Installation
1. | Terms and definitions | |
2. | Responsibilities of personnel and documentation requirements | |
3. | Knowledge of dry out requirements | |
4. | Sealing requirements (for example, water mist, covering, membrane, curing) | |
5. | Application and time limits for applying membrane curing compounds | |
6. | Environmental conditions required for curing | |
7. | Heating equipment, methods, and procedures (e.g., gas-fired burner, stress relieving heating elements) | |
8. | Placement of temperature sensing probes | |
9. | Knowledge of manufacturer’s recommended heatup and cooldown schedules | |
10. | Applicable heating rates for various classes of refractories | |
11. | Lining integrity inspection techniques |
In summary, studying the API 936 Body of Knowledge is crucial if you are currently overseeing refractory installations. This detailed guide helps understand key concepts like inspection procedures and the characteristics of monolithic refractories. It serves as a strategic path for mastering this specialized field through certification.
It is widely known that success in the API 936 exam relies heavily on understanding this information, highlighting the importance of theoretical knowledge alongside practical experience. If you aspire to be a part of refractory engineers, you should recognize the pivotal role the API 936 Body of Knowledge for your certification.
If you feel overwhelmed with the amount of standards that you need to learn about, embarking on API 936 training by PetroSync is a wise and forward-looking decision. Our training program is designed to equip you with the latest standards and industry insights, ensuring that you are well prepared of this specialized field.
By choosing PetroSync training, you not only gain a deep understanding of essential concepts, including inspection procedures and refractory characteristics but also benefit from continuous updates that reflect the ever-evolving industry standards. Stay ahead in your career by enrolling in API 936 training by PetroSync– a commitment to ongoing learning and staying abreast of the most current practices in refractory engineering.
Credit header image: Freepik
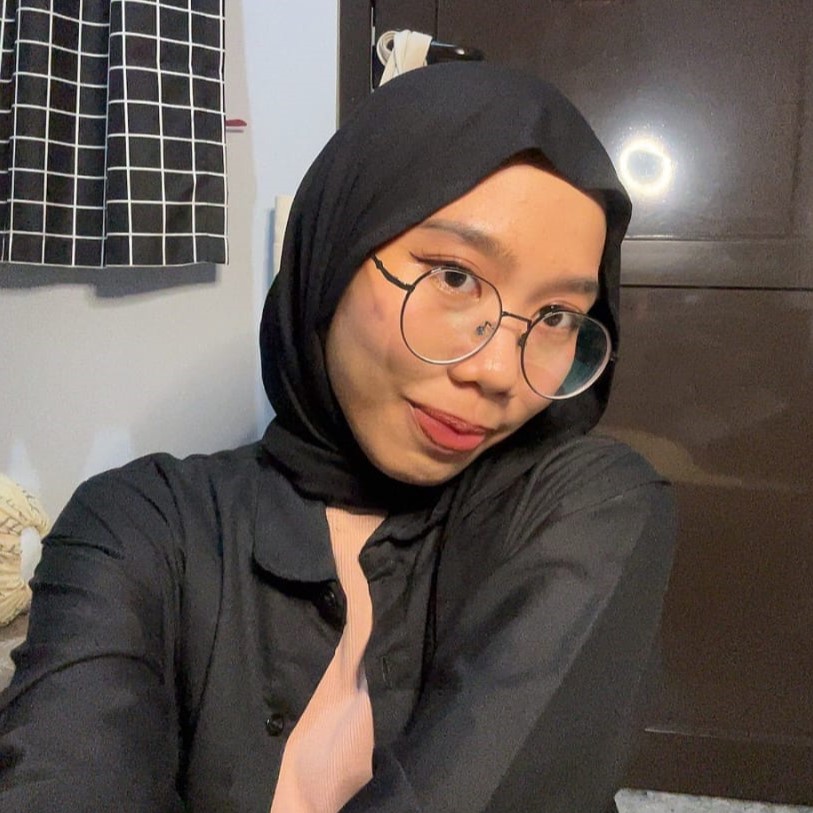
SEO specialist by day, fact-checker by night. An avid reader and content writer dedicated to delivering accurate and engaging articles through research and credible sources.