Flanged joint in a pipe plays a crucial role in various industries, providing a dependable and secure connection between pipes and components. These joints are specifically designed to handle high pressures, ensuring the smooth and safe flow of fluids and gases. Flanged joints offer a range of advantages, including their strength, resistance to leaks, ease of installation, and compatibility with different pipe sizes and materials.
What Is A Flanged Joint?
Credit: instrumentationtools.com
A flanged joint is a way to connect pipes, where the connecting pieces have flanges used to bolt the parts together. Although the word ‘flange’ generally refers to the actual raised rim or lip of fitting, many plumbing fittings with flanges are also called flanges themselves.
The flanges are carefully positioned and firmly fastened with bolts and nuts, creating a secure and leak-resistant connection. Flanged joints offer numerous benefits, notably easy assembly and disassembly, which prove convenient for maintenance, repairs, or alterations.
Flanged joints find extensive application across diverse industries, encompassing petrochemical, oil and gas, chemical, and power sectors. The selection of the appropriate flanged joint type is influenced by factors like pressure, temperature, and the size of the piping system.
Where Are Flanged Joints Used For?
Flanged pipes are commonly used for aboveground applications when a sturdy, secure connection is required for liquids like water, wastewater, air, and oil. They are extensively utilized in water treatment plants, wastewater treatment plants, industrial piping systems, and both indoor and outdoor applications such as bridges and elevated crossings.
Using flanged joints underground is generally not advisable due to the inflexible nature of the joint. This recommendation is supported by the appendices found in relevant ANSI/AWWA standards.
What Material Is Used For Flanged Joint?
Flanged joints can be made from various materials depending on the specific application and requirements.
- Carbon steel
- Alloy
- Stainless
The choice of material depends on factors like the conveyed fluid, temperature, pressure, corrosion resistance, and environmental conditions.
What Are The Most Commonly Used Flanged Types in The Petrochemical Industry?
In the petrochemical industry, several flanged types are commonly used for connecting pipes, valves, and equipment. Some of the most frequently utilized flanged types include:
1. Welding Neck Flange
A welding neck flange is a type of flange designed for welding to a pipe. It provides a smooth connection and adds strength. It is used in high-pressure applications and requires skilled welding for a reliable joint.
2. Slip On Flange
A slip-on flange is a type of flange that slides over a pipe and is then welded in place. It is used in low-pressure applications, easy to install, and provides a secure connection when properly welded.
3. Socket Weld Flange
A socket weld flange is a type of flange that is connected to a pipe using socket welding. It fits over the pipe end and is welded around the flange’s outer perimeter. It is used in small pipe sizes and low-pressure applications, providing a strong and leak-free connection when properly welded.
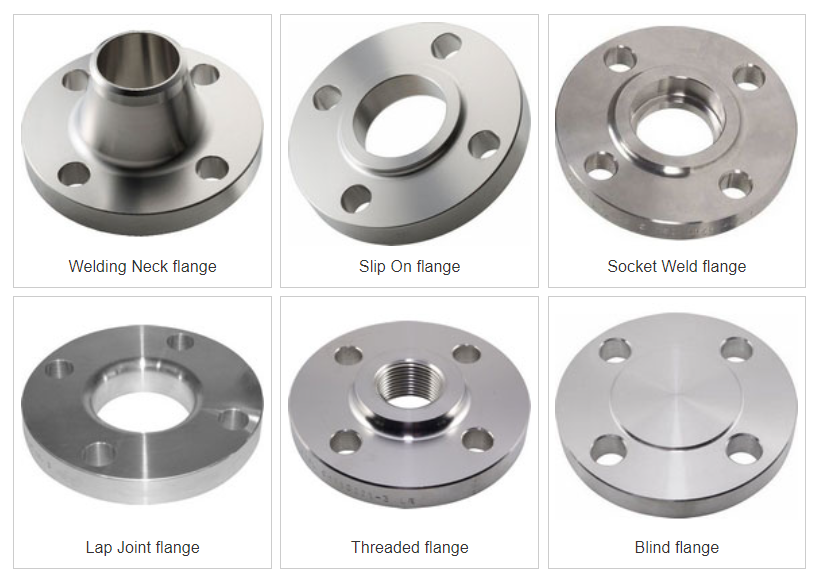
4. Lap Joint Flange
A lap joint flange consists of two parts: a flat disc with a raised inner ring and a collar. The collar is slipped over the pipe, and the flange rests on it. Bolts are used to secure the connection. Lap joint flanges allow for easy disassembly and are used when adjustments or changes to the pipe are needed. They are cost-effective but not suitable for high-pressure situations.
5. Threaded Flange
A threaded flange screws onto the pipe end for an easy and secure connection. It is commonly used in low-pressure applications but not recommended for high-pressure situations.
6. Blind Flange
A blind flange is a type of flange used to seal the end of a pipe or vessel. It blocks the flow of fluid or gas and provides a secure seal. It is commonly used for temporary or permanent closure during maintenance or inspections. Blind flanges are easy to install and can be removed when needed.
What Are The Advantages of Flanged Joints?
Flanged joints provide several advantages in various applications:
1. Strong and Secure Connection
Flanged joints offer a sturdy and dependable connection between pipes or components. The use of bolts and flanges ensures a robust joint that can withstand high pressure and stress.
2. Leak Resistance
The raised rims or lips of flanges create a tight seal when bolted together, minimizing the risk of leaks. This is especially important when dealing with fluids or gases under pressure, ensuring efficient and safe fluid transportation.
3. Easy Installation and Maintenance
Flanged joints allow for straightforward installation and disassembly, making maintenance, repairs, and component replacement easier. This convenience reduces downtime and improves overall operational efficiency.
4. Alignment Flexibility
Flanged joints provide flexibility in aligning pipes or equipment during installation. They can be adjusted or rotated to ensure precise alignment, even when dealing with misaligned or non-uniform components.
5. Compatibility and Standardization
Flanged joints adhere to standardized dimensions and designs, ensuring compatibility between pipes and components from different manufacturers. This interchangeability simplifies system integration and the replacement of parts.
6. Thermal Expansion Accommodation
Flanged joints can accommodate thermal expansion and contraction in piping systems. They allow for slight movements without compromising the integrity of the joint, reducing the risk of stress-related failures.
7. Versatility
Flanged joints are suitable for a wide range of applications and industries, including plumbing, oil and gas, and chemical processing. They can handle various fluids, pressures, and temperatures, making them highly versatile.
8. Longevity and Durability
Properly installed and maintained flanged joints offer long-lasting durability. They are designed to withstand challenging environmental conditions, corrosion, and wear, providing a reliable and extended service life.
It’s important to note that the specific benefits and suitability of flanged joints may vary depending on the application, system requirements, and adherence to industry standards. Following recommended procedures for installation and maintenance is crucial to maximize the advantages of flanged joints.
What Are The Disadvantages of Flanged Joints
While flanged joints offer various advantages, it’s important to be aware of their drawbacks:
1. Cost
Flanged joints can be more expensive than other types of connections due to the additional components required, such as flanges, bolts, and gaskets.
2. Stress Concentration
Flanged joints can create stress concentration points due to the bolt holes and the transition between the flange and the pipe, potentially increasing the risk of fatigue or corrosion cracking.
3. Limited Adaptability
Flanged joints are not as adaptable to changes or modifications compared to other types of connections. Altering or reconfiguring the system may require the removal and replacement of entire flanged sections.
4. Complex Installation
Proper installation of flanged joints requires skilled labor and knowledge of tightening procedures to ensure a leak-free connection, making the installation process more complex.
While the drawbacks of flanged joints can be mitigated through proper design, installation, and maintenance practices, assessing their suitability requires careful consideration of specific application requirements.
Piping inspectors, particularly those holding API 570 certification, play a crucial role in minimizing the disadvantages associated with flanged joints. Their expertise ensures correct installation, adherence to standards, and early identification of issues like incorrect tightening, alignment problems, or inadequate gasket selection. This proactive approach optimizes flanged joint performance, enhancing reliability and reducing drawbacks.
Petrosync, a leading provider of industry knowledge and training, offers comprehensive and in-depth materials on API 570. Our training delves into the intricacies of API 570, focusing on the inspection, repair, alteration, and rerating of in-service piping systems.
With a thorough understanding of API 570 standards, PetroSync is on a mission to provide you with the necessary expertise to effectively assess the integrity of piping systems and ensure compliance with industry regulations. Through our detailed materials, our API 570 training empowers you with the knowledge and skills required to perform critical tasks related to piping inspection and maintenance, contributing to the safe and reliable operation of industrial facilities.
Credit header image: Adobe Stocks
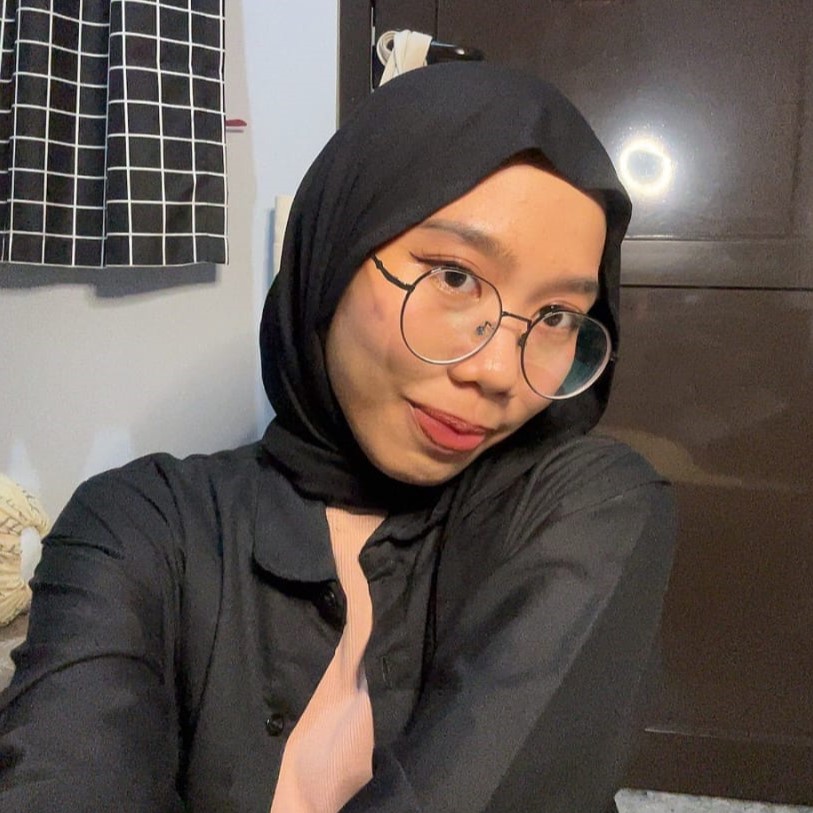
SEO specialist by day, fact-checker by night. An avid reader and content writer dedicated to delivering accurate and engaging articles through research and credible sources.