Hydrostatic testing is an important technique for ensuring the safety and reliability of pressurized systems such as pipelines, boilers, and storage tanks. This testing method reduces risks and maintains operational efficiency by finding any flaws or leaks before they occur. But what exactly is hydrostatic testing, and why is it important?
Hydrostatic testing is a rigorous method for determining a system’s structural integrity. The process comprises filling the equipment with a liquid, often water, and applying pressure to determine its strength. This test ensures that the system can withstand operating pressures safely, making it necessary in industries where safety and performance are critical.
Regular hydrostatic testing protects against catastrophic breakdowns and increases the life of equipment. It not only ensures compliance with industry rules, but it also increases confidence in the system’s reliability. Understanding hydrostatic testing is crucial for engineers, safety officials, and maintenance personnel responsible for complicated systems.
What Is Hydrostatic Testing?
Hydrostatic testing is a technique used to verify the durability and soundness of piping systems, boilers, gas cylinders, and pressure vessels by filling them with liquid and applying pressure to simulate the pressure they will experience during operation. Industries like oil and gas, chemical processing, and power generation commonly apply a hydrostatic testing approach for their piping systems.
Hydrostatic testing is performed after installing or modifying a piping system and periodically during its operation. Before conducting the test, the system is drained, cleaned, and inspected for defects or damage. Water is gradually introduced into the system during the test until the desired pressure is achieved.
Which is then held for a specified period of several hours to guarantee that the system can endure the pressure without leaking or failing. The system is inspected after the test to identify any damage or leaks, which are repaired before being back into operation. Hydrostatic testing is critical for maintaining the safety and dependability of piping systems.
How Does Hydrostatic Testing Work?
The hydrostatic testing of piping systems is guided by specific procedures detailed in the ASME B31.3 code, which outlines the following steps:
1. Preparation
Before testing, the piping system needs to be cleaned and drained to eliminate any residue that could affect the test results. Additionally, connections such as valves and flanges are inspected to ensure they are installed correctly and firmly.
2. Filling
The system is then filled with clean and contaminant-free test fluid such as water until it is completely full.
3. Pressurizing
The system is gradually pressurized and monitored using pressure gauges until it reaches a predetermined level. This pressure is maintained for a specific duration, typically 10 minutes.
4. Inspection
While the system is pressurized, it undergoes a visual inspection and other testing methods like ultrasonic testing to identify any leaks or failures. Any leaks or failures detected must be repaired before the system is put into service.
5. Depressurizing
Following the completion of the test, the system is depressurized slowly and drained of the test fluid. The system is then dried and prepared for operation.
What Are The Common Hydrostatic Testing Methods?
The common hydrostatic testing methods are used to assess the structural integrity and leak resistance of various pressurized equipment and systems. Some of the methods are:
1. The Water Jacket Method
The water jacket method involves immersing the item in a container filled with water and pressurizing it gradually until it reaches the intended pressure testing. As the water pressure increases, it is transmitted evenly to the test item through the water, leading to a uniform pressure distribution across its surface.
2. The Direct Expansion Method
The direct expansion method is a hydrostatic testing method that is utilized to assess the pressure integrity of vessels and pipelines. The test item is first filled with water, and the air is eliminated from the system.
Then, water is introduced into the system at a constant rate using a pump until the desired test pressure is reached. The pressure is held steady for a specific duration while the test item is scrutinized for any signs of damage or leakage.
3. The Proof Pressure Method
The proof pressure method fills the test item with water and pressurizes it 10%-50% above maximum operating pressure. The pressure is maintained for a set duration while the test item is checked for any leakage or damage. The aim of this method is to ensure that the test item can withstand higher pressure than what it will typically encounter during operation, providing an additional level of safety.
What Are The Benefits of Hydrostatic Testing?
Hydrostatic testing can ensure safety by detecting any weaknesses or defects in the equipment that could potentially lead to accidents. By detecting and repairing these issues, hydrostatic testing can prevent equipment failures which helps ensure the safety of the people and the environment. The test can also detect leaks as it is an effective way to detect leaks in piping systems.
By pressurizing the system with water, leaks can be easily identified and repaired before they cause significant damage or loss. Companies using hydrostatic testing on their piping systems directly demonstrate that they are following the required safety regulations and industry standards. They also take appropriate measures to ensure the safety of their equipment and the people working with it.
This can help prevent accidents, injuries, and property damage while equipment is functioning as intended. Hydrostatic testing improves reliability by identifying and addressing issues in pressure vessels, pipelines, and components. ASME B31.3 hydrostatic testing verifies piping strength, pressure capacity, and leak-tightness for safety and code compliance.
Is hydrotest pressure 1.3 or 1.5 times?
The pressure applied during hydrostatic testing is a frequently asked question. Depending on the system type and regulations, the test pressure is typically required to reach 1.3 or 1.5 times the design pressure. For example, the ASME Boiler and Pressure Vessel Code requires that hydrostatic test pressures be 1.3 times the design pressure.
This standard assures that the test is rigorous and safe for the system’s components. On the other hand, some businesses use a 1.5 times factor to accommodate for extra safety margins, especially in high-risk contexts. Understanding the logic underlying these standards is critical.
The relevance of hydrostatic testing is evident when you understand how varying test pressures assure system durability without putting undue stress on the materials. The appropriate pressure factor is determined by the specifications of your equipment and the applicable industry norms.
How long does hydrostatic testing take?
Hydrostatic testing duration depends on equipment size and system complexity, varying based on multiple factors. Typically, the testing process involves multiple stages, from preparation to evaluation. Hydrostatic testing for smaller systems may just take a few hours, whereas bigger systems or pipelines may take several days.
According to API 570 rules, the procedure is filling the equipment with a liquid, applying pressure to the prescribed level, and maintaining that pressure for a predetermined time, which commonly runs from 30 minutes to several hours. Each stage of the testing process is rigorously documented to ensure standard compliance and ease of tracking.
Hydrostatic testing is more than just the test itself; it also includes a dedication to thoroughness and safety. Understanding the timing requirements helps operators plan more effectively and avoid operational delays.
Join PetroSync’s ASME B31.3 Training to Boost Your Expertise
Join PetroSync’s ASME B31.3 training to master piping system design, construction, and maintenance expertise. These processes require specialized knowledge and skills to perform safely and accurately.
Master the principles, procedures, and techniques of hydrostatic testing, piping design, and performing tests safely following code requirements. With PetroSync’s ASME B31.3 – Process Piping Code Design Requirements training course, you will also learn how to interpret test results.
Identify potential issues and develop effective repair and maintenance strategies. Whether you are a piping engineer, quality control inspector, or maintenance technician, ASME B31.3 training can help you to enhance your career and professional development.
Investing in ASME B31.3 course by PetroSync should be the right choice if you are looking to expand your skills and knowledge in the field of piping systems and pressure vessels. Join us and master the safety and reliability of piping systems with PetroSync!
Credit header image: zerust.com
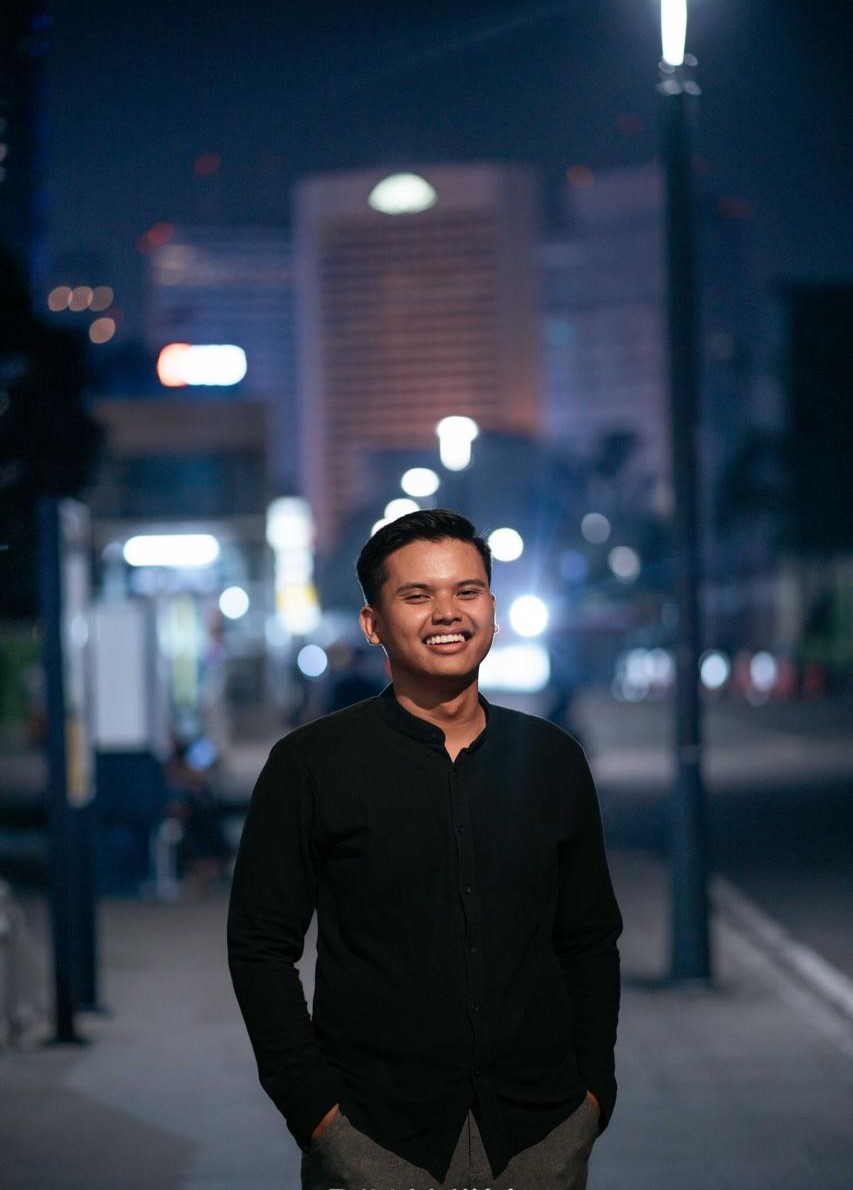
Results-oriented and thorough SEO specialist with extensive experience in conducting keyword research, developing and implementing digital website promotion strategies and plans, managing campaigns to develop company websites in the digital world, excellent knowledge of marketing techniques and principles, and attentive strong attention to detail.