Pipeline maintenance is a critical aspect of the industry, responsible for ensuring the safe and efficient transportation of valuable resources over long distances. By upholding the integrity and reliability of these vital conduits, pipeline maintenance plays a central role in safeguarding both the environment and local communities. In this article, the key principles and advanced technologies that underpin effective pipeline maintenance, empowering industry professionals to uphold operational excellence and commit to sustainability.
What is Pipeline Maintenance?
Pipeline maintenance is the essential process of preserving the reliability and effectiveness of a pipeline and its related parts. It involves ongoing efforts to ensure the pipeline’s longevity and prevent potential failures. Regular and proper maintenance significantly extends the lifespan of the pipes, safeguarding their functionality and integrity over time.
Maintenance like cleaning, testing, and replacing worn-out parts, operators can extend the lifespan of the pipeline and reduce risks. Pipeline failure is an undesirable outcome for any asset or property owner. It can result in significant damage to nearby infrastructure like roads, bridges, and buildings, undermining their integrity. To avoid shouldering these risks, pipeline maintenance is an absolute necessity.
What Are Some Common Pipeline Maintenance Challenges?
There are several common challenges associated with pipeline maintenance. These include:
1. Corrosion
Corrosion is a major concern for pipelines, as it can lead to structural damage and leaks. Preventing and managing corrosion requires regular inspections and the implementation of appropriate corrosion protection measures.
2. Environmental Factors
Pipelines are exposed to various environmental factors such as temperature changes, extreme weather conditions, and natural disasters. These factors can cause wear and tear, leading to potential failures. Mitigating the impact of environmental factors requires proactive monitoring and maintenance.
3. Access and Location
Some pipelines are located in remote or hard-to-reach areas, making access and maintenance challenging. The logistics involved in reaching these locations and ensuring proper maintenance can be complex and time-consuming.
4. Aging Infrastructure
Many pipelines are aging, which increases the likelihood of mechanical failures and structural deterioration. Regular assessments and upgrades are necessary to address aging infrastructure issues and maintain pipeline integrity.
5. Regulatory Compliance
Pipeline maintenance must adhere to strict regulatory standards and compliance requirements. Meeting these standards involves implementing robust inspection protocols, documenting maintenance activities, and ensuring adherence to safety regulations.
6. Cost and Resource Management
Pipeline maintenance can be costly, requiring significant financial resources for inspections, repairs, and upgrades. Efficient resource management is essential to optimize maintenance efforts while minimizing costs.
Addressing these challenges requires a comprehensive approach that includes proactive monitoring, regular inspections, timely repairs, adherence to regulations, and effective resource management.
7. Pipeline Length
The length of a pipeline can be a typical obstacle in pipeline maintenance. Lengthy pipelines demand extra resources and logistical arrangements to conduct inspections, maintenance, and repairs efficiently. The extensive distance covered by long pipelines can make it more time-consuming and expensive to reach specific sections for routine inspections or repairs.
8. Fluids Transported
Pipelines commonly contain flammable or hazardous substances. Even during maintenance shutdowns, there can be residual fuel remaining in the pipeline, which can complicate the repair and maintenance procedures. It is crucial to handle this situation with utmost caution to prevent any disruption or compromise to the pipeline contents during maintenance activities.
What Makes Pipeline Maintenance Important?
Pipeline maintenance is of utmost importance due to several compelling reasons. Firstly, it guarantees the continuous and secure operation of pipelines, preventing potential accidents and environmental risks. Regular maintenance aids in the early detection and resolution of issues or defects, mitigating the likelihood of costly repairs and downtime.
Any malfunction or defect in pipeline operations can result in significant disruptions throughout the entire value chain. Production processes may come to a standstill, and even worse, leakage can lead to damages that extend beyond mere production losses.
Moreover, well-maintained pipelines enhance operational efficiency and minimize energy wastage, leading to overall cost-effectiveness. Substantial harm to pipeline infrastructure invariably results in substantial financial losses. Companies are often held accountable for the damage to both property and human life that arises from faulty pipeline operations.
Additionally, pipeline maintenance extends the infrastructure’s lifespan, optimizing its long-term performance and dependability.
What Is The Standard Procedure for Pipeline Maintenance?
The standard procedure for pipeline maintenance ensures safe and efficient operation through systematic steps. Key components include:
1. Right-of-Way Clearing
Clearing the right-of-way is vital for efficient pipeline maintenance. It involves removing trees and roots to eliminate potential hazards. Additionally, maintaining a clear right-of-way ensures easy access for pipeline repairs during emergencies.
2. Hydrostatic Testing
Hydrostatic testing is recommended for pipeline pipes to ensure their strength and performance. It involves connecting the pipes and pressurizing them with water to evaluate their durability. This testing is conducted before installation and is also used to monitor the pipeline’s strength over time.
3. Corrosion Identification
Regularly inspecting for corrosion is essential to extend the lifespan of your pipeline. Prior to installation, use appropriate anti-corrosive coatings based on the pipe material. Keep in mind that complete protection against corrosion is not guaranteed due to environmental factors and unforeseen incidents. Leaks, emergencies, or natural disasters can cause significant damage, so monitoring their impact on your pipes is necessary.
4. Complete Records Maintenance
Maintaining accurate records is crucial for pipeline maintenance. These records provide a comprehensive history of your pipeline’s life cycle. It is important to maintain a database of site plans, pipeline product guides, and photographs. The photographs are particularly useful for documenting the pipe’s condition during installation and establishing a baseline for monitoring corrosion progression.
5. Regular Inspections Performance
Regular pipeline inspections are vital to identify maintenance issues promptly. Experienced crews can proactively address concerns based on their observations. Neglecting inspections increases the risk of emergencies, posing dangers and causing costly operational downtime.
What Are The Best Practices for Doing Pipeline Maintenance?
Effective pipeline maintenance prioritizes safety, reliability, and long-term performance. Some of the best practices for doing pipeline maintenance include:
1. Planning During The Pipeline Design Phase
Pipeline maintenance best practices are established techniques developed through years of pipeline operations. Some of these practices are specific to pipelines, while others are derived from standard asset maintenance approaches and a comprehensive understanding of the overall situation.
2. Inspection and Testing
Pipeline maintenance aims to conduct regular inspections and tests. A CMMS system aids in scheduling maintenance resources. Drones and robots inspect inaccessible areas, while manual inspections are performed for accessible pipelines.
Underground pipelines require a preventive maintenance dig before the inspection. Non-destructive tests like ultrasonic, eddy current and leak testing assess pipe integrity. Implementing these practices enhances efficiency, identifies maintenance needs, and ensures pipeline integrity.
3. Tracking Pipeline Condition
Continuous monitoring is essential to ensure the well-being of pipelines. A comprehensive log of data serves as valuable input for maintenance analytics and helps maintain an audit trail. Key parameters to be documented and tracked include:
- Fluid flow
- Pressure on pipeline walls
- Valve pressure
- Inspection records
- Testing records
- Maintenance records
- Changes in depth cover
- Environmental conditions at various pipeline locations
Depending on the type of fluid being transported, additional parameters may need monitoring. Given the vast amount of data involved, traditional methods of tracking can be challenging. Whenever possible, employing condition-monitoring sensors, non-destructive tests, and digital tools like CMMS is highly recommended to effectively manage these variables.
Access to such data and technology enables the implementation of condition-based and predictive maintenance strategies, optimizing maintenance resources and reducing long-term maintenance costs.
4. SOPs and Checklists
Standard operating procedures (SOPs) guide maintenance professionals in following best practices and ensuring compliance with health and safety recommendations. They provide clarity and consistency, improving efficiency in maintenance tasks.
5. Corrosion Prevention
Corrosion worldwide results in annual damages amounting to $2.5 trillion, a significant portion of which is preventable. It is crucial to actively employ corrosion prevention techniques to safeguard the health of your pipelines.
To ensure pipeline longevity, prioritize the use of suitable pipe materials, corrosion prevention coatings, drying agents, and effective protection against environmental factors in your maintenance efforts.
In summary, the significance of adhering to the best practices of pipeline maintenance cannot be overstated. By embracing proactive measures, conducting thorough inspections, and promptly addressing issues, pipeline operators can uphold the safety and reliability of this crucial equipment.
The significance of following best practices in pipeline maintenance is closely linked to API 570 and piping inspection. API 570 provides comprehensive guidelines for inspections, repairs, and alterations of piping systems, ensuring regulatory compliance and safety. Trained piping inspectors play a crucial role in conducting thorough assessments and making informed decisions for maintenance.
To excel in API 570 and advance your career in pipeline maintenance, enroll in PetroSync’s API 570 prep course. PetroSync offers comprehensive programs tailored for professionals in the oil and gas industry, covering API 570 body of knowledge, inspection techniques, and industry best practices.
With an experienced instructor holding API 570 certification, you can gain valuable insights to confidently conduct inspections, interpret results, and make informed decisions. Investing in PetroSync’s API 570 training will enhance your skills, keep you up-to-date with industry requirements, and contribute to the safety and reliability of pipeline systems. Reserve your spot and elevate your expertise and achieve excellence in API 570 and pipeline maintenance with PetroSync!
Credit header image: pexels.com
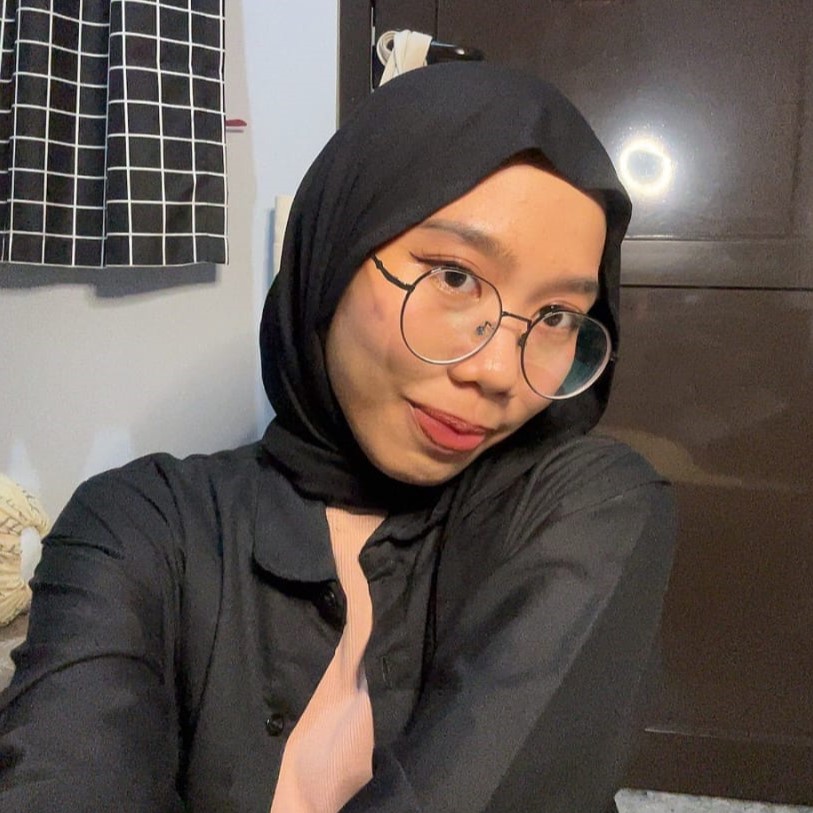
SEO specialist by day, fact-checker by night. An avid reader and content writer dedicated to delivering accurate and engaging articles through research and credible sources.