In industries where high temperatures are commonplace, the integrity of refractory materials is paramount for safety and efficiency. Routine inspections of these materials are crucial to identify potential issues and prevent costly disruptions. In this article, we will explore five key practices for effective refractory inspection. These practices, when followed diligently, can prolong the lifespan of your equipment and ensure it functions optimally.
What Is Refractory Inspection?
Refractory inspection is the process of closely examining the heat-resistant lining in industrial equipment to ensure it is in good condition and functioning correctly. Thermography is a proven and accepted method for locating damaged and missing refractory material during this inspection.
The specialized linings examined in the inspection are like protective barriers wrapped around the equipment, ensuring it does not get harmed by extreme heat. They are designed to endure the intense temperatures that many industrial processes generate. Without these linings, the equipment could get damaged or even melt when exposed to such high levels of heat. So, they play a crucial role in maintaining the safety and efficiency of industrial operations.
Why Is Refractory Inspection Necessary?
What many people might not know is that fixing equipment lined with refractory material can be much more costly and troublesome than repairing rotating machinery or electrical failures. Here’s why:
1. Avoid Complete Shutdowns
When refractory-lined equipment needs repairs, it often leads to a complete shutdown of the entire plant. Unlike motors, pumps, or electrical breakers that can be easily switched to backups with minimal production loss, there are usually no backups available for this equipment.
2. Cost-effective
Repairing refractory-lined equipment tends to be expensive. It involves a lot of manual labor, heavy machinery, materials, and time to carry out the repairs effectively.
3. Prolong The Equipment’s Life
The primary reason for lining vessels or pipes with internal refractory material is to protect them from extreme heat that could damage the steel shell. The refractory material acts as insulation to prevent excessive heating of the external shell.
When Is The Right Time To Inspect The Refractory?
The ideal moments for checking the refractory are during different phases of the vessel’s start-up process:
1. Initial Start-Up
When the vessel is first started, and it changes in temperature and processes, use infrared inspection. This is when you might spot areas that are hotter, often due to cracks or gaps in the refractory. Keep a record of these spots because they are likely to cause problems.
2. Continuing Start-Up
As the start-up progresses with more temperature and process changes, the hot areas you observed earlier may become even hotter. Some areas may even approach critical temperatures and show signs of overheating on the outer shell. Keep track of these hot spots, especially the critical ones.
3. Full Operation
When the vessel is running at its full capacity and temperature, you may notice that many of the hot spots you saw earlier have become smaller and cooler. This happens because the refractory has expanded and sealed off the cracks and gaps.
4. Persistent Hot Spots
However, some hot spots may remain during full operation. These areas indicate ongoing issues with the refractory, like cracks, gaps, or damage. Document these problems because they are likely to be the primary hot spots during regular inspections in normal operation.
By examining the refractory during these different start-up stages, you can identify existing problems and areas that may lead to future issues. This approach establishes a baseline for predictive maintenance, allowing you to monitor and analyze data effectively, ensuring the longevity and performance of refractory-lined vessels.
What Are The 5 Best Practices in Refractory Inspection?
Adhering to the best practices of refractory inspection can help you ensure the longevity and efficiency of your refractories. You can find the best practices in doing refractory inspection as follows.
1. Understanding Refractory Materials
Before we delve into the best practices, it’s essential to grasp the basics of refractory materials. Refractories are specialized heat-resistant materials used to line equipment like furnaces, kilns, and reactors. They provide insulation and protect against extreme heat, ensuring industrial processes run smoothly.
2. Regular Visual Inspections
The first practice involves conducting regular visual inspections. Visual inspections entail a thorough examination of refractory linings to identify any visible signs of wear, erosion, or damage. Look for cracks, gaps, or areas with abnormal heat, as these could indicate refractory deterioration. Visual inspections should be scheduled and performed after any high-temperature operations.
3. Ultrasonic Thickness Testing
Ultrasonic thickness testing is a valuable tool in refractory inspection. This non-destructive testing method measures the thickness of refractory linings using ultrasonic waves. It helps pinpoint areas where the refractory lining may have thinned due to wear or erosion. Detecting these areas early allows for planned maintenance or repairs, reducing the risk of unexpected equipment failures.
4. Thermographic Imaging
Another advanced technique for refractory inspection is thermographic imaging. This method employs infrared cameras to capture temperature variations on the refractory surface. The presence of hot spots or cold areas can indicate issues with insulation or refractory integrity. Regular thermographic imaging can help address these issues proactively.
5. Sample Analysis
For a comprehensive assessment of refractory health, periodic sample analysis is recommended. This involves taking small samples of the refractory material and subjecting them to laboratory tests. These tests can reveal chemical changes, structural weaknesses, or contamination that may not be visible during visual inspections.
What Are Relevant Standards That Address Refractory Inspection?
In refractory inspection, some of the relevant standards that provide guidelines and procedures for assessing and maintaining refractory materials are:
1. ASTM C160
This standard from the American Society for Testing and Materials (ASTM) primarily focuses on the testing of refractory materials. It provides guidelines for conducting various tests to assess the physical and chemical properties of refractories.
2. ASTM C862
Another ASTM standard, ASTM C862, concentrates on the installation of monolithic refractories. It outlines procedures and recommendations for correctly installing these materials. Engineers use it to guarantee that refractories are installed in a way that maximizes their durability and effectiveness.
3. API STD 936
The American Petroleum Institute (API) developed this standard specifically for the petrochemical and refining industries. API STD 936 focuses on the installation and inspection of refractory linings in these industries.
API 936 standard provides detailed guidelines for the installation, inspection, and repair of refractory linings in various equipment, with a strong emphasis on safety and performance in high-temperature and high-pressure environments.
What Are The FAQs Related to Refractory Inspection?
1. How Often Should Refractory Inspections Be Conducted?
Refractory inspections should be carried out at regular intervals, ideally after each high-temperature operation. However, the frequency may vary depending on the specific industry and equipment.
2. Are There Any Safety Precautions for Refractory Inspections?
Yes, safety is paramount. Ensure equipment is shut down and cooled before inspections. Utilize appropriate personal protective equipment and adhere to safety protocols.
3. What Are Common Signs of Refractory Degradation?
Common signs include cracks, gaps, hot spots, or unusual temperature variations on the refractory surface.
4. Can Refractory Materials Be Repaired, or Is Replacement Necessary?
In many cases, minor damages can be repaired, but extensive damage may necessitate replacement to ensure safety and efficiency.
5. How Can I Find Qualified Professionals for Refractory Inspections?
Seek certified inspection companies with expertise in your industry. They should have experienced technicians and the necessary equipment.
It is worth remembering that refractory inspection is not just about maintenance, it’s an investment in the long life of your equipment and the success of your operations. So, being proactive and taking good care of your refractories will bring you long-lasting advantages.
If you are looking to enhance your ability to conduct accurate refractory inspections, consider enrolling in PetroSync’s API 936 training program. This specialized training equips you with the knowledge and skills needed to excel in refractory inspections.
With PetroSync‘s API 936 training, you will gain a deeper understanding of refractory materials, advanced inspection techniques, and best practices. Investing in this training can significantly boost your expertise and confidence in maintaining the integrity of industrial equipment through effective refractory inspections.
Credit header image: Pexels
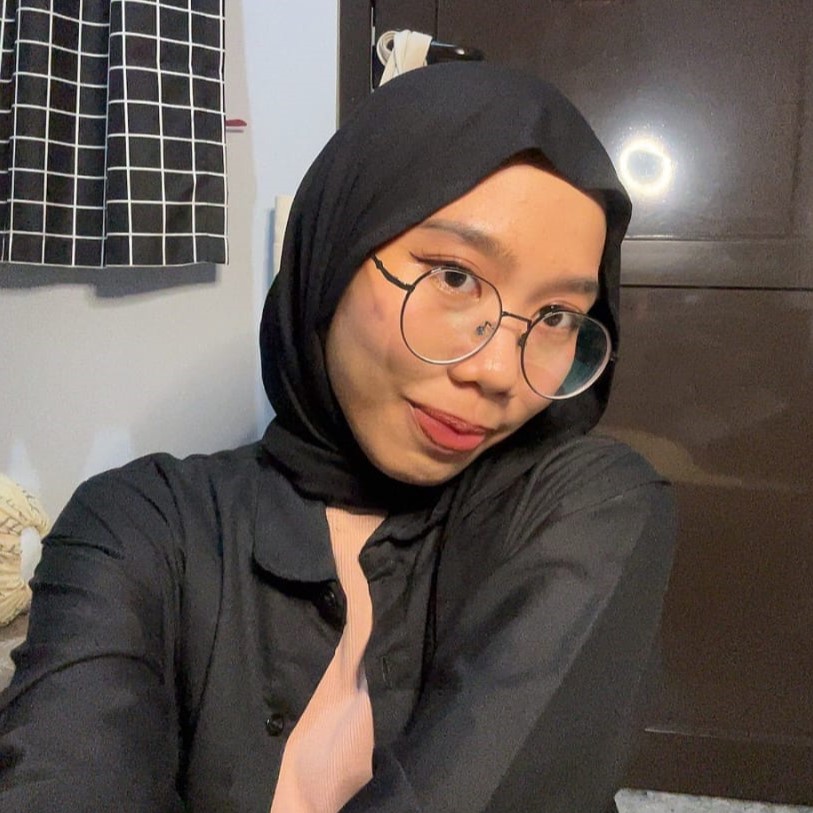
SEO specialist by day, fact-checker by night. An avid reader and content writer dedicated to delivering accurate and engaging articles through research and credible sources.