In industries that rely on high-temperature processes, the quality of refractory materials is crucial. Refractory materials are designed to withstand extreme heat and harsh conditions, and they play a vital role in processes like metal casting and cement production. This article explores the world of refractory quality control, explaining why it matters and how to maintain optimal performance.
What Is Quality Control in Refractory?
Refractory quality control is the careful process of making sure that the materials used in high-heat applications, such as furnaces and industrial equipment, meet specific standards and perform well.
Quality control is really important because it makes sure that refractories can handle extreme heat, chemical reactions, and physical wear and tear. This leads to better efficiency, long-lasting materials, safety, and being more environmentally responsible in different industries.
Who Is Responsible for The Refractory Quality Control Process?
The refractory life cycle involves a range of parties, such as owners, contractors, suppliers, and manufacturers. Each of these participants plays significant roles in the QA/QC process with important responsibilities.
1. Owner
Owners, as the title implies, are in charge of the equipment or parts that need refractory installation or repair. Their role involves creating detailed guidelines for the type of lining materials to be used, the materials to secure them in place, the curing and drying procedures, and other important specifications.
They also set standards for the quality of materials, the methods used for installation, how often inspections should be done, and the acceptable thickness of the lining. Additionally, owners are responsible for addressing any issues, substitutions, or deviations from the requirements, as well as resolving conflicts or problems noted by inspectors.
2. Contractor
Contractors have the task of putting the refractory in the owner’s equipment. To do this, they need to create, present, and carry out a thorough plan that aligns with API 936 and the standards provided by the owner. If there are any deviations, substitutions, or exceptions to this plan, the contractors must get the owner’s approval before proceeding.
Since the contractors are in charge of carrying out the installation work, they are responsible for providing all the necessary documents and records related to the process.
3. Inspector
Inspectors are individuals hired or appointed by owners, and they must oversee the testing of refractories and the installation work done by contractors and manufacturers.
4. Manufacturer
Manufacturers are tasked with creating refractory products at their manufacturing facilities. They must supply compliance datasheets, along with materials that meet the specifications mentioned in those datasheets. Additionally, manufacturers are responsible for providing any other documents that the owner might need.
Does API 936 Provide The Guidelines for Refractory Quality Control?
In API 936, there’s a table that gives a clear summary of the important quality control components, along with the actions and goals related to each component of the monolithic refractories. You can locate this table in Section 4 of the Standard for your reference.
API 936 Section 4 |
||
Elements |
Actions |
Objectives |
Documentation (see 5.1.1 and 5.2.1) | Owner specification and/or contractor execution plan. | Define job-specific work scope. |
Material qualification (see 8.2) | Testing at an independent or manufacturer’s laboratory. Inspector directs sampling, monitors specimen preparation and witnesses testing. | Confirm that materials manufactured for the job meet the specified physical property standards. |
Applicator qualification (see 8.3) | Contractor demonstration of capabilities in simulated installation which is witnessed and inspected by the inspector. | Confirm that equipment and personnel are capable of installing qualified materials to specified standards. |
Installation monitoring (see Section 9) | Inspector monitors contractor work and test sample preparation. | Confirm that specifications, good practice and installation procedures are followed. |
As-installed testing (see 8.4) | Inspector coordinates the sampling and testing of as-installed materials. | Confirm that installed materials meet specified physical property standards. |
Pre-dry out inspection (see 5.3f) | Inspector performs visual/hammer test inspection of applied linings. | Confirm that installed linings meet specification standards. |
Dryout monitoring (see Section 10) | For dry out prior to normal startup of equipment, the inspector monitors heating rates and hold times. | Confirm that agreed upon procedure is followed. |
Post dry out inspection (see 5.3f) | Inspector performs visual/hammer test inspection of applied linings. | Confirm that installed linings meet specification standards. |
NOTE: When an independent laboratory is utilized or the contractor assumes complete accountability for as-installed testing results, inspector participation may be waived or reduced by the owner. |
What Are The Key Aspects of Refractory Quality Control?
Refractory materials are essential for many industries as they become the protective barrier against high temperatures, chemical reactions, and wear and tear. However, to ensure they perform well, we need to focus on key aspects of quality control.
1. Material Composition
The first step in quality control is making sure the raw materials used to create refractories meet the required standards. Precise composition, from selected minerals to binders, is critical. Any variations can lead to reduced performance or even failure.
2. Consistency in Manufacturing
Producing refractory materials is a precise process. Consistency in shaping, firing, and cooling is necessary to achieve the desired properties. Even minor deviations can compromise the final product’s integrity.
3. Thorough Testing
Quality control doesn’t end in the production process. Rigorous testing, including checks for porosity, thermal conductivity, and resistance to chemical corrosion, is essential. These tests help identify defects or inconsistencies.
Refractory quality control is a collective effort even when it is mainly done by API 936 inspector. Owners set the standards, contractors implement them, inspectors ensure compliance, and manufacturers provide quality materials. API 936 offers a framework for clarity.
Key aspects include material precision, consistent manufacturing, and rigorous testing. This diligence guarantees refractories’ reliability in high-temperature environments, ensuring efficiency, safety, and environmental responsibility.
However, to become an expert in API 936 standards for refractories, PetroSync offers comprehensive API 936 training that covers all aspects of refractory management following these standards. This training is not just a valuable addition to your skill set; it’s a game-changer. It equips you with the knowledge and expertise to excel in the field of refractory quality control.
By taking API 936 training, you position yourself as an expert in the industry, enhancing your career prospects. Don’t miss out on the opportunity to elevate your skills and become a sought-after professional in the world of refractory inspection!
Credit Header Image: Freepik
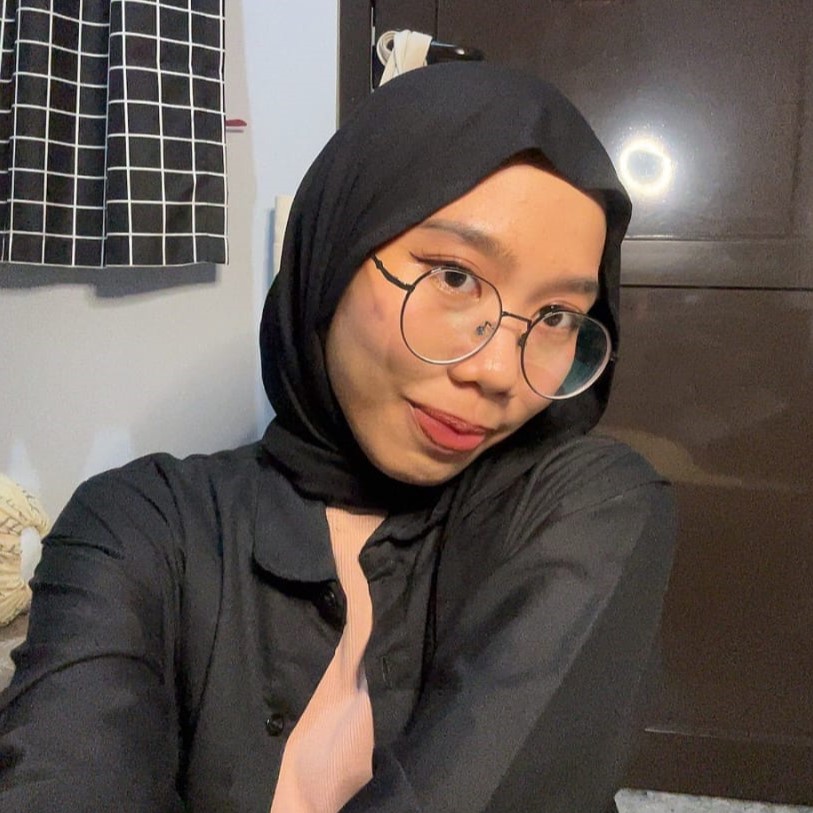
SEO specialist by day, fact-checker by night. An avid reader and content writer dedicated to delivering accurate and engaging articles through research and credible sources.